基本介紹
- 中文名:高爐煤氣
- 外文名:blastfurnace gas
- 設備名稱:高壓鼓風機/羅茨風機
- 含有:二氧化碳、一氧化碳、氫、氮氣等
- 作用:加熱熱軋的鋼錠、預熱鋼水包
- 俗稱:鼓風爐煤氣
產品信息
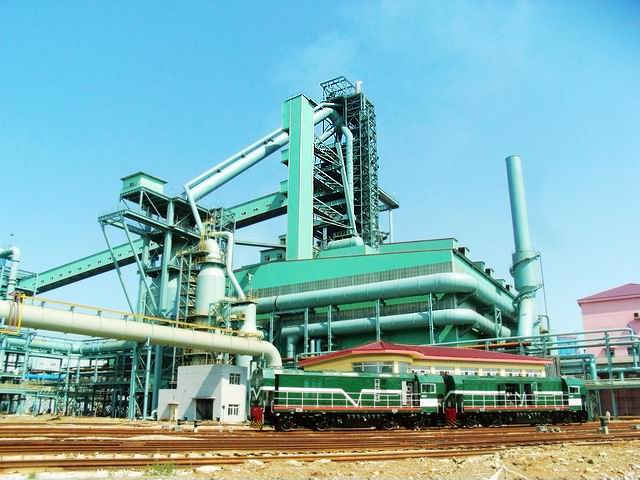
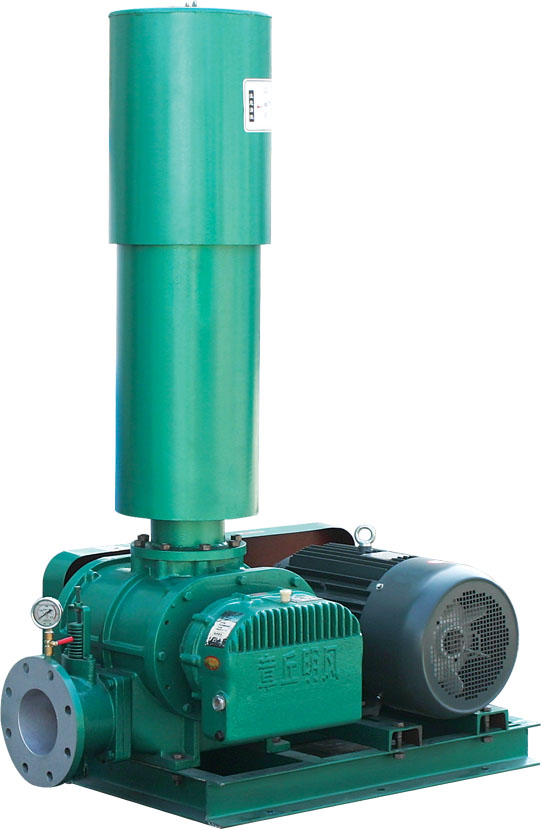
套用
特性
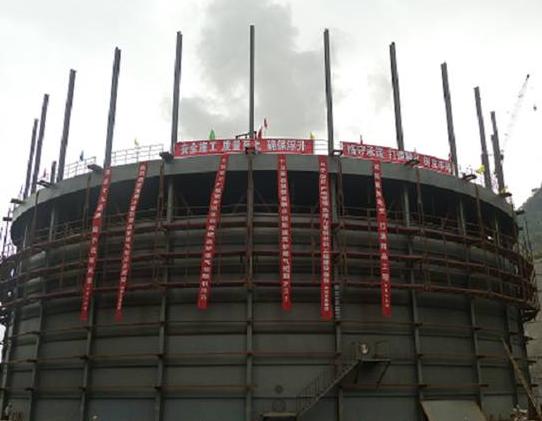
高爐煤氣是高爐煉鐵生產過程中副產的可燃氣體。它的大致成分為二氧化碳6-12%、一氧化碳28-33%、氫氣1-4%、氮氣55-60%、烴類0.2-0.5%及少量的二氧化硫。它...
煤氣是以煤為原料加工製得的含有可燃組分的氣體。根據加工方法、煤氣性質和用途分為:煤氣化得到的是水煤氣、半水煤氣、空氣煤氣 (或稱發生爐煤氣) .這些煤氣的...
高爐煤氣運動是指高爐煉鐵過程中在風口燃燒帶產生的熾熱煤氣穿過料柱上升到爐頂的過程。研究高爐煤氣運動主要是研究高爐內的壓力場和煤氣流量的分布,煤氣運動過程中...
高爐煤氣除塵系統是指從高爐爐頂出來的煤氣含有大量灰.塵,經除塵系統除去灰塵後才能輸送給用戶。...
TRT——(Blast Furnace Top Gas Recovery Turbine Unit,以下簡稱TRT) 高爐煤氣余壓透平發電裝置(即TRT)是利用高爐冶煉的副產品——高爐爐頂煤氣具有的壓力能及熱能...
煤氣含量,城市居民生活所用的燃氣,主要有人工煤氣、天然氣和液化石油氣。這些氣體都具有易燃、易爆的特點,一旦泄漏容易引發閃爆事故,而且人工煤氣含有毒的一氧化碳...
轉爐煤氣是鋼鐵企業內部中等熱值的氣體燃料。可以單獨作為工業窯爐的燃料使用,也可和焦爐煤氣、高爐煤氣、發生爐煤氣配合成各種不同熱值的混合煤氣使用。轉爐煤氣含有...
高爐煤氣余壓透平發電裝置(Blast Furnace Top Gas Recovery Turbine Unit,以下簡稱TRT),TRT是利用高爐冶煉的副產品——高爐爐頂煤氣具有的壓力能及熱能,使煤氣通過...
高爐煤氣是鋼鐵企業煉鐵時的副產氣,主要成分是一氧化碳和氮氣,低熱值約為4MJ/m。高爐煤氣可用作煉焦爐的加熱煤氣,以使更多的焦爐煤氣供應城鎮。高爐煤氣也常用作...
一種專門製作的氣體燃料,因用煤氣發生爐生產而得名。在充滿固體燃料的豎式煤氣發生爐的下部,通入空氣和水汽的混合物,使之穿過灼熱的固體燃料層而製得。熱值低、...
高爐爐頂煤氣成份是直接反映冶煉過程的狀態參數,是高爐操作調節負荷的主要依據,同時反映冶煉過程煤氣利用情況,對高爐負荷平衡致關重要。...
冶金煤氣是在煉鋼、煉鐵、煉焦、發生爐、鐵合金生產過程中產生的含有大量CO的可燃性混合氣體。煤氣的成分一般受制氣原料和煤氣的生產、回收工藝方法的不同,其組成和...
內容介紹《中等職業學校教材·煤氣基礎知識》主要對煤氣的基本性質、燃燒特性,各種煤氣(高爐煤氣、焦爐煤氣、冶金煤氣和發生爐煤氣)的發生原理及影響煤氣組成的因素,...
煤氣因來源不同,有不同的名稱...... 煉鐵高爐排出的氣體中還有相當多的可燃成分,叫高爐煤氣。 發生爐煤氣和高爐煤氣主要是一氧化碳;焦爐煤氣則富含氫氣、甲烷,還有...
高爐是用鋼板作爐殼,殼內砌耐火磚內襯。高爐本體自上而下分為爐喉、爐身、爐腰、爐腹 、爐缸5部分。由於高爐煉鐵技術經濟指標良好,工藝簡單,生產量大,勞動生產...
高爐煤氣是高爐煉鐵過程中所產生的一種副產品。高爐煤氣含有大量的CO,在使用時應特別注意,防止煤氣中毒。另外,高爐煤氣還易燃、易爆,因此,在使用時,應充分予以注意...
煤氣曲線是用爐頂十字測溫裝置測得的爐頂徑向上五點煤氣溫度而繪製的溫度曲線。一般爐頂十字測溫裝置安裝在爐喉上方、離料面0.5~1.0m處,也有安裝在料面以下的。...
高爐熱風爐是煉鐵廠高爐主要配套的設備之一,一般一座高爐配3~4座熱風爐,熱風爐的作用是為高爐持續不斷的提供1000度以上的高溫熱風。目前先進的現代熱風爐風溫可以...