基本介紹
- 中文名:無間隙原子鋼
- 外文名:Interstitial-Free Steel
- 類別:鋼
- 別名:IF鋼
發展歷史,研究進展,國外,國內,工藝流程,成分控制,成分要求,碳含量,氮含量,氧含量,雜物影響,雜物種類,按來源分,按化學分,按變形能力分,按大小分,按形狀分,潔淨度,
發展歷史
IF鋼在1949年首次被研製成功,其基本原理是在鋼中加入一定比例的Ti,使鋼中固溶C和N的含量降到0.01%以下,使鐵素體得到深層次的淨化,從而得到良好的深沖性能。但由於受到當時冶煉技術的限制,鋼中原始的固溶C、N含量較高,所以需要加入的Ti含量也很高,達到了0.25-0.35%,Ti是一種價格非常昂貴的稀有合金元素,在當時更是如此,因而阻止了其當時的商業化進程。直到1967-1970,由於真空脫氣技術在冶金生產中的套用,大大減少了需要添加的Ti合金元素含量(大約為0.15%左右)才正式出現了商用的IF鋼,幾乎在同時,人們也發現了Nb具有和Ti幾乎相同的作用,但還是受到價格因素的制約,其套用也只限於少量特殊的零件。20世紀70年代在日本開始用連退線生產少量的IF鋼,70年代末,IF鋼成分大致為:0.005-0.01%C、0.003%N、0.15%Ti或Nb。到20世紀80年代,冶煉技術進一步發展,採用改進的RH處理可經濟的生產C≤0.002%的超低碳鋼,RH處理時間也縮短到10-20min。現代IF鋼的成分大致為:C≤0.005%、N≤0.003%,Ti或Nb一般約0.05%。到1994年全世界IF鋼的產量超過了1000萬噸。歸根到底,IF鋼的迅速發展來自於市場需求的急劇增加和生產成本的降低。
研究進展
國外
汽車工業的飛速發展帶動了IF鋼(Interstitial Free Steel,無間隙原子鋼)的生產。世界許多先進鋼鐵廠都非常重視IF鋼的生產,安賽樂米塔爾、新日鐵、JFE、蒂森克虜伯、美鋼聯、浦項等先進鋼廠的IF鋼年產量均在200萬噸以上。20世紀末,日本IF鋼年產量已超過1000萬噸,並呈逐年上升趨勢。許多大型鋼鐵公司均積極發展IF鋼生產,如日本的川崎制鋼公司、新日鐵公司,德國的Thyssen鋼鐵公司、Hoesch鋼鐵公司,美國的Armco鋼鐵公司、Inland鋼鐵公司,韓國的浦項鋼鐵公司等,其IF鋼年產量均在100萬噸以上。近年來,為適應汽車減重、降低材料消耗和節約燃油的需要,對汽車用鋼板強度的要求越來越高。“超低碳”鋼是高端產品,新日鐵、JFE、蒂森克虜伯等鋼廠在鋼的化學成分、夾雜物含量以及每道工序的控制等方面均有成熟的經驗。
國內
從2000年以來,由於IF鋼具有優良的深沖性和無時效性,已逐漸成為繼沸騰鋼和鋁鎮靜鋼之後的新一代衝壓用鋼,是一個國家汽車用鋼板生產水平的標誌。
我國研製IF鋼始於1989年,寶鋼集團公司、鞍鋼集團公司、武鋼集團公司、攀鋼集團公司、本鋼集團公司等先後開展IF鋼的研究開發工作,並大力發展IF鋼生產。到2009年,我國的IF鋼生產已具有一定規模,但仍處於初級發展階段。以汽車板用IF鋼為例,國產的IF鋼僅可以滿足中低檔轎車和卡車用鋼板的質量要求,中高檔轎車用高品質鋼板仍然需要大量進口,尤其是對於表面質量要求非常嚴格的汽車面板,與國外同類型IF鋼產品的質量差距更大。
到2010年,我國的汽車產量達800萬輛,其中轎車600萬輛。可見我國對汽車板的需求量之大。2009年我國寶鋼生產的IF鋼的成分已能控制在[C] 0.002%、[N] 0.002%、[S] 0.001%、T[O] 0.002%的水平。本鋼生產的IF鋼的成分控制在[C] 0.003%、[N] 0.004%、[S] 0.005%的水平。我國武鋼、鞍鋼也已批量生產IF鋼。中鋼公司(中國鋼鐵集團公司)採用BOF+RH 真空脫氣工藝,並改造了關鍵設備,開發出優質IF鋼。
工藝流程
IF鋼對鋼水純淨度有著較為苛刻的要求,生產工藝流程的選取直接影響到IF鋼的品質和生產的順行。當前IF鋼的生產有三種典型的工藝流程,必須根據企業現有的裝備條件來選擇合適的流程。
工藝路線A:
工藝路線B:
工藝路線C:
高爐→鐵水脫硫→轉爐冶煉→氬氣攪拌→LF精煉→RH真空處理→連鑄
工藝A是目前國內外生產IF鋼最常用的方法,適用於傳統厚板坯連鑄機,由於其不需要經過LF精煉處理,生產成本最低,工藝設備基本上能滿足IF鋼的生產需要。工藝B和工藝C由於採用了LF精煉,能使大包渣得到很好改性,有利於渣吸收夾雜物,淨化鋼液。目前馬鋼、本鋼採用LF-RH雙聯法在薄板坯連鑄機上成功實現IF鋼的批量生產,但是這兩種工藝路線相對複雜,成本相對較高。
每一個工序均在不同程度上影響IF鋼的最終產品性能。為保證IF鋼的最終產品性能,國內外IF鋼生產工藝的技術要點總結如表1所示。
表1 國內外IF鋼生產工藝的技術要點
工序 | 技術要點 |
熱軋 | |
冷軋 | 儘可能大的冷軋壓下率。 |
退火 |
成分控制
成分要求
間隙原子C、N對IF鋼的織構、r值與時效特性有著十分重要的影響。固溶的C、N原子不利於{111}織構的形成,r值急劇降低。此外,C、N含量高還將會明顯增大IF鋼的時效硬化傾向。Nb、Ti等元素可以將C、N間隙原子從基體中清除出來,從而獲得較純淨的鐵素體鋼,有利於{111}織構的發展和r值增大,並且保證了IF鋼的非時效性。因此IF鋼必須具有超低碳氮、鈮鈦微合金化等特點。
IF鋼的成分特點是:①為了獲得良好的深沖性能,鋼中的[C]、[N]、[Si]很低;②為Al脫氧鋼。除了脫氧作用以外,Al對冷軋鋼板的織構控制有重要作用;③對[S]和[P]控制要求相對寬鬆;④為了保證良好的表面質量,對鋼中的非金屬夾雜物要求嚴格。日本企業提出IF鋼冷軋板中非金屬夾雜物的尺寸必須小於100μm。
從IF鋼的性質可知,鋼中最有害的元素是間隙原子C、N,為保證鋼的深沖性能、表面質量、鍍鋅性能以及生產順行,對鋼中其他元素和夾雜物也有一定要求。根據對鋼的有害程度,對鋼中有害雜質排序如圖1:C:嚴重影響鋼的深沖性能,必須儘可能去除,對於鋼中殘餘的C,採用加Ti的方式加以固定。
圖1:有害夾雜物在鋼中的有害程度
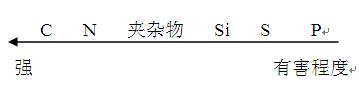
N:對鋼的有害作用與C類似,但因煉鋼一般能將N控制在40ppm以下,而脫氧殘留的Al能與N生產穩定的AlN, 能將N完全固定,因此,N對IF鋼的有害作用基本上得到控制。
夾雜物:對鋼的表面質量和深沖性能有一定影響,應使鋼中夾雜物儘可能少,尺寸儘可能小。
Si:一方面增加鋼的強度,減少鋼的延性,對鋼的深沖性能有害;另一方面影響鋼的鍍鋅性能。應儘可能減少鋼中的Si含量。
S:在一定程度上(約0.005~0.006%)有利於C的析出,對提高鋼的深沖性能有利。但是S過高則對鋼有害。
P:對IF鋼的延性、低溫塑性有很大影響,要求IF鋼中磷含量越低越好。在某些高強IF鋼中作為強化元素提高鋼的強度。
碳含量
IF鋼生產中,碳的控制是十分關鍵的內容。鋼中的碳對IF鋼的性能有極大的影響,IF鋼中不允許有固溶的碳,鋼中的碳必須採用加入鈦合金的方式加以固定。鋼中的碳含量一要儘可能的低從而減少合金的加入量;二要穩定從而確定鈦鐵的加入量。這兩點都要得到保證,IF鋼才能大規模生產。
目前IF鋼轉爐冶煉終點的碳含量一般控制在(200~400)×10-4%,要使鋼中的碳含量小於50×10-4%,甚至低於20×10-4%,必須通過RH真空精煉來完成。
RH真空精煉是生產超低碳IF鋼的關鍵技術,通過吹氧強制脫碳和後序工藝防止增碳來實現對碳的控制。
提高鋼水脫碳速度的工藝措施有:
(1)進一步提高真空系統的抽氣能力。
真空泵的抽氣能力是通過真空室的真空度來影響脫碳速度的。真空度的高低,決定了RH真空脫碳的速度。較大的抽氣能力可以使真空度在短時間內獲得較高的真空度,即快速降低真空室的壓力,可以增加CO氣泡的發生率,使鋼中碳含量迅速下降,能夠達到的最終碳含量頁越低。武鋼二煉鋼廠1、2 號RH 真空度的變化曲線和碳含量變化的對應關係說明了這一點,如圖2所示。
圖2 RH真空脫碳情況比較
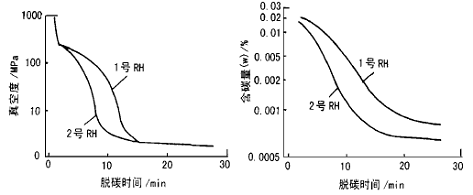
(2)增加驅動氣體流量。
驅動氣體是RH的鋼液循環的動力源,驅動氣體量的大小直接影響鋼液循環狀態和脫碳等冶金反應。驅動氣體流量控制不當會產生強烈噴濺。脫碳過程中生成CO氣體,加劇噴濺程度,在脫碳前期,驅動氣體量應調小,隨著C-O反應的減弱而適當增大,直到脫碳結束達到RH循環所需驅動氣體量,可以加強後期鋼液的攪拌,抑制傳質係數的降低,從而抑制了後期脫碳速率的降低。
(3)脫碳前期吹氧強制脫碳
在真空脫碳反應中,當鋼水中碳含量高([C]/[O]>0.66)時,即脫碳反應前期,氧的傳質決定脫碳速度。這時頂吹氧槍吹氧可以有效提高表觀脫碳常數,縮短處理時間。另外,高速氧氣流衝擊鋼水表面,鋼水飛散成為大量小液滴,更增加了脫氣表面積,加快了脫碳速度。但是,吹氧一般會使得脫碳結束鋼水中的溶解氧含量增加,從而惡化鋼水的潔淨度。應該掌握好吹氧時機和吹入的氧氣量。
(4)增加插入管截面積。
在增大鋼水循環流量的措施中,如果單純增大驅動氣體流量會使得環流管內鋼水線速度上升,容易造成真空室內噴濺粘鋼。解決辦法就是擴大環流管內徑。增大插入管內徑,即增大了插入管的截面積,增大了循環流量。即使在同樣的驅動氣體流量的情況下,由於CO氣體向氣泡中的擴散作用,可以容納和產生更多的氣泡,增大了循環管上升區的相界面,同時也使噴濺到真空室的鋼液量增加,增大了鋼液乳化區的相界面,使脫碳速度加快。另一方面由於循環流量增加,鋼液在真空室底部的線速度增加,使鋼流的邊界層減薄,碳氧向鋼液面擴散速度增加。插入管的內徑越大,脫碳速度越快。在條件允許的情況下應儘可能地增大插入管內徑,增加循環流量,促進脫碳反應。圖3展示了新日鐵八幡廠增大插入管內徑後鋼水環流量的變化,可以看出增大插入管內徑對於增大鋼水環流量效果明顯。
圖3:增大插入管內徑後鋼水環流量的變化
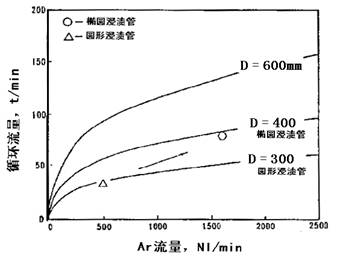
氮含量
鞍鋼開發了低氮IF鋼的生產工藝,包括轉爐冶煉工序提高鐵水比、冶煉過程控制返乾、冶煉終點減少補吹次數和時間,採用鐵礦石(燒結礦)造渣,能夠控制冶煉終點氮的質量分數小於12×10;RH-TB精煉工序處理前期提高脫碳速度,處理中期快速提高真空度、提升氬氣流量和鋼水循環量,處理後期控制鋼水中的氧含量,同時必須保證鋼水極低的硫含量。目前鞍鋼可以批量穩定生產氮含量小於20×10的IF鋼。 馬鋼CSP在生產SPHC鋼種時轉爐採用全程底吹氬模式,在轉爐自動化系統中增加氮氣閥門的控制手段,徹底杜絕吹煉過程中的氮氣泄露,加強出鋼口的維護,出鋼氮含量從47.4×10降至30×10。劉光穆等人考察了漣鋼100t轉爐不同氮氬切換模式對終點氮含量的影響,儘管全程底吹氬氣有利於鋼中[N]的降低,但是在考慮綜合成本的情況下,將轉爐冶煉供薄板鋼水底吹定為前10min吹氮後吹氬工藝。此外吹氬強度合理時,可以避免鋼水在吹氬站增氮。
武鋼三煉鋼廠通過轉爐終點、脫氧制度和連鑄三個環節來系統控制鋼中的氮含量,並把保護澆注視作控氮關鍵環節,為此提高鋼包開澆自開率,在長水口和鋼包下水口之間採用特殊密封材料和氬封方式,中間包採用高鹼度覆蓋劑並控制吹氬流量確保液面不暴露。目前該廠鋼包到中間包鋼水增氮已經控制在2×10以內,中間包鋼水平均氮含量為22.8×10。
內陸鋼公司通過轉爐副槍終點控制降低補吹率、終點添加石灰石造泡沫渣、以CO2作為底吹氣體,終點氮含量小於13×10,沸騰出鋼避免吸氮,出鋼過程平均增氮7×10。RH精煉改進浸漬管的法蘭密封同時採用低氮合金和廢鋼,RH平均氮含量為18.3×10。保護澆注增氮量為1×10。
綜上所述,IF鋼氮含量控制的要點是:
轉爐工序提高鐵水比,提高氧氣純度;吹煉過程中增加礦石的投入量,添加石灰石造泡沫渣,控制轉爐爐內為正壓;吹煉後期,採用低槍位操作,增加攪拌強度,強化終點命中率;採用沸騰出鋼。RH工序加強真空室密封,減少合金和廢鋼帶入的氮,避免RH吸氮。連鑄工序提高鋼包開澆自開率,改進長水口機構、操作、密封材料、氬封方式並控制合理的吹氬量,中間包採用高鹼度覆蓋劑,確保液面不暴露。
氧含量
(1)轉爐工序氧含量的控制
冶煉IF鋼一般採用頂底復吹轉爐,在冶煉後期增大底部惰性氣體流量、加強溶池攪拌,以降低轉爐冶煉終點鋼中氧含量;實現轉爐冶煉動態模型控制,將IF鋼轉爐冶煉終點碳含量由0.02%~0.03%提高到0.03%~0.04%以提高冶煉終點鋼液碳含量和溫度的雙命中率,減少補吹率;採用擋渣出鋼、鋼包下渣自動檢測技術及鋼包渣改質措施以減少鋼包渣對鋼液的污染。
IF鋼轉爐冶煉終點爐渣的全鐵含量一般為15%~25%,通過出鋼擋渣技術使鋼包內爐渣的厚度控制在50mm以下、防止出鋼過程中下渣量過大造成鋼液二次氧化嚴重。出鋼後立即向鋼包內加入改質劑,爐渣改質劑由CaCO3和金屬鋁組成,可將渣中的全鐵含量降低到4%左右,甚至2%以下。
(2)連鑄工序氧含量的控制
雜物影響
研究發現,鋼中的成分和夾雜物對於IF鋼的性能影響顯著。非金屬夾雜物的性質、形態、分布、尺寸及含量不同,對鋼性能的影響也不同,如若生產表面無缺陷的汽車面板(05板),必須嚴格控制IF鋼中夾雜物的數量、類型、形態及其分布狀況。因此,針對IF鋼存在的表面質量問題,開展IF鋼成分及夾雜物的過程控制研究成為當務之急,其研究成果對於我國IF鋼生產的進一步發展具有重要的理論價值和現實意義;非金屬夾雜物作為獨立相存在於鋼中,破壞了鋼基體的連續性,加大了鋼中組織的不均勻性,嚴重影響了鋼的各種性能,如非金屬夾雜物導致應力集中,引起疲勞斷裂,數量多且分布不均勻的夾雜物會明顯降低鋼的塑性、韌性、焊接性以及耐腐蝕性,鋼中呈網狀存在的硫化物會造成熱脆性。因此,夾雜物的數量和分布被認定是評定鋼材質量的一個重要指標,並且被列為優質鋼和高級優質鋼出廠的常規檢測項目之一。
雜物種類
按來源分
(1)內生夾雜物
鋼在冶煉過程中,脫氧反應會產生氧化物和矽酸鹽等產物,若在鋼液凝固前未浮出,將留在鋼中。溶解在鋼液中的氧、硫、氮等雜質元素在降溫和凝固時,由於溶解度的降低,與其他元素結合以化合物形式從液相或固溶體中析出,最後留在鋼錠中,它是金屬在熔煉過程中,各種物理化學反應形成的夾雜物 。內生夾雜物分布比較均勻,顆粒也較小,正確的操作和合理的工藝措施可以減少其數量和改變其成分、大小和分布情況,但一般來說是不可避免的。
(2)外來夾雜物
鋼在冶煉和澆注過程中懸浮在鋼液表面的爐渣、或由煉鋼爐、出鋼槽和鋼包等內壁剝落的耐火材料或其他夾雜物在鋼液凝固前未及時清除而留於鋼中。它是金屬在熔煉過程中與外界物質接觸發生作用產生的夾雜物。如爐料表面的砂土和爐襯等與金屬液作用,形成熔渣而滯留在金屬中,其中也包括加入的熔劑。這類夾雜物一般的特徵是外形不規則,尺寸比較大,分布也沒有規律,又稱為粗夾雜。這類夾雜物通過正確的操作是可以避免的。
按化學分
(1)氧化物系夾雜
簡單氧化物有FeO、Fe2O3、MnO、SiO2、Al2O3、MgO和Cu2O等。在鑄鋼中,當用矽鐵或鋁進行脫氧時,SiO2和Al2O3夾雜比較常見。Al2O3 在鋼中常常以球形聚集呈顆粒狀成串分布(圖4)。複雜氧化物包括尖晶石類夾雜物和各種鈣的鋁酸鹽等以及鈣的鋁酸鹽。矽酸鹽夾雜也屬於複雜氧化物夾雜,這類夾雜物 有2FeO·SiO2 (鐵矽酸鹽)、2MnO·SiO2(錳矽酸鹽)和CaO·SiO2 (鈣矽酸鹽)等。這類夾雜物在鋼的凝固過程中,由於冷卻速度較快,某些液態的矽酸鹽來不及結晶,其全部或部分以玻璃態的形式保存於鋼中。
圖4: 掃描電鏡下的Al2O3夾雜
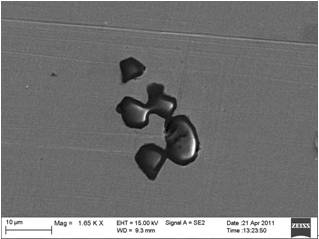
(2)硫化物系夾雜
主要是FeS 、MnS和CaS等。由於低熔點的FeS易形成熱脆,所以一般均要求鋼中要含有一定量的錳,使硫與錳形成熔點較高的MnS而消除FeS的危害。因此鋼中硫化物夾雜主要是MnS。鑄態鋼中硫化物夾雜的形態通常分為三類:①形態為球形,這種夾雜物通常出現在用矽鐵脫氧或脫氧不完全的鋼中;②在光學顯微鏡下觀察呈鏈狀的極細的針狀夾雜;③呈塊狀,外形不規則,在過量鋁脫氧時出現。
(3)氮化物夾雜
當鋼中加入與氮親和力較大的元素時形成AlN、TiN(圖5)、TiN-Al2O3(圖6)、ZrN和VN等氮化物。在出鋼和澆鑄過程中鋼液與空氣接觸,氮化物的數量顯著增加。
圖5:掃描電鏡下TiN夾雜
圖6:掃描電鏡下TiN-Al2O3夾雜
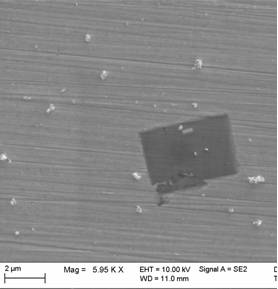
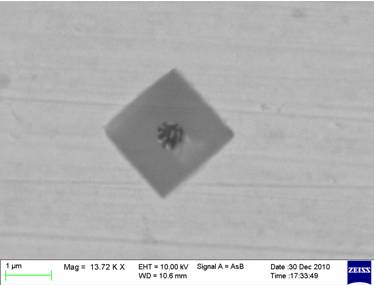
按變形能力分
(1)塑性夾雜物
塑性夾雜物在軋制時沿軋制方向伸長,如MnS、FeS、MnO·SiO2、SiO2含量低的矽酸鹽等。
(2)半塑性夾雜物
半塑性夾雜物在軋制時呈不連續延伸成鏈狀分布,如簇群狀Al2O3,複合鋁矽酸鹽等。
(3)脆性夾雜物
脆性夾雜物在軋制時不發生塑性變形而成不規則分布,如Al2O3、Cr2O3、ZrO2、TiN、Ti(C,N)、SiO2、FeO·Al2O3、MgO·Al2O3、CaO·6Al2O3、SiO2含量高的矽酸鹽、球狀鋁酸鈣等。
按大小分
按夾雜物的大小可分為兩類:
(1)巨觀夾雜物
這類夾雜物是在鋼的冶煉或澆注過程中由於耐火材料的混入而造成的,其特點是大而無固定形狀。
(2)微觀夾雜物
按形狀分
按夾雜物的形狀可分為六類:(1)球狀夾雜物;(2)多面體夾雜物;(3)盤形夾雜物;(4)樹枝狀夾雜物;(5)團絮狀夾雜物;(6)聚合體狀夾雜物。
潔淨度
鋼的潔淨度是指鋼中夾雜物的含量、形態與分布。用於製造汽車外面板的冷軋薄板除要求成型性外,對表面質量要求也非常高。生產IF鋼時,鋼水的潔淨度對最終冷軋薄板產品質量和使用性能會產生重大影響,是反映IF鋼總體質量水平的標誌。