隧道窯直接還原法是一種重要的煤基直接還原煉鐵法。這種方法是瑞典人E.Sieurin於1911年發明的。此法在瑞典已有多年的生產歷史,50年代經過技術改造後實現了機械化的生產。
基本介紹
- 中文名:隧道窯直接還原法
- 外文名:tunnel kiln direct reduction
- 類別:還原煉鐵法
- 學科:冶金工程
- 發明人:E.Sieurin
- 發明時間:1911年
介紹
發展展望
套用
工藝特點
工藝原理
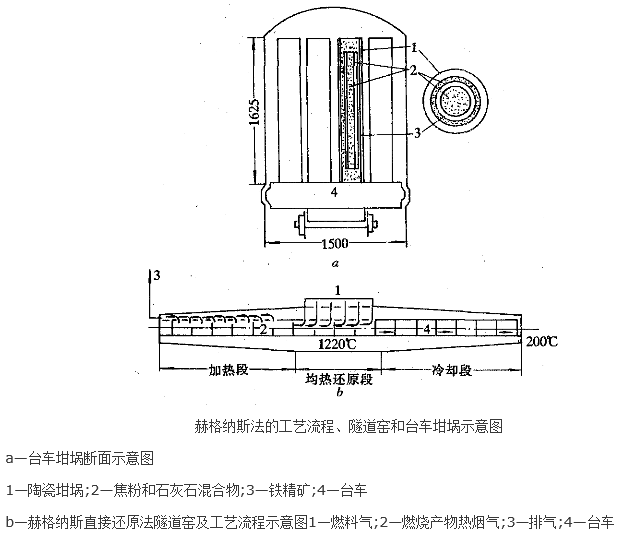
隧道窯直接還原法是一種重要的煤基直接還原煉鐵法。這種方法是瑞典人E.Sieurin於1911年發明的。此法在瑞典已有多年的生產歷史,50年代經過技術改造後實現了機械化的生產。
隧道窯直接還原法是一種重要的煤基直接還原煉鐵法。這種方法是瑞典人E.Sieurin於1911年發明的。此法在瑞典已有多年的生產歷史,50年代經過技術改造後實現了機械化...
直接還原鐵生產工藝 編輯 在工業上套用較多的有鐵磷還原法,鐵精礦粉還原法等,...氧化鐵在隧道窯中加熱被固體碳還原的過程是比較複雜的過程。爐料以預熱到還原、...
根據還原劑類型有使用氣體還原劑的氣基直接還原煉鐵法和使用固體還原劑的煤基...以高品位鐵礦為原料,粉焦作還原劑,採用隧道窯直接還原(罐式)法生產高金屬化...
隧道窯直接還原法(Hoganas法)是鐵精粉與還原劑在圓筒形反應罐內進行還原.反應罐裝在有燃燒室和小車可以從中通過的隧道窯內加熱,反應罐冷卻後出窯倒罐取出直接還原...
直接還原技術經濟指標是指直接還原鐵生產工藝中各項主要經濟技術指標。世界上有...法,按還原設備分為豎爐法、迴轉窯法、轉底爐法、反應罐(隧道窯、倒焰窯)法等...
一次還原鐵粉,即利用直接還原法生產生鐵。直接還原法是指在低於熔化溫度之下將鐵礦石還原成海綿鐵的煉鐵生產過程,其產品為直接還原鐵(DRI),也稱海綿鐵。...
較少的直接還原工藝發展較快,最近相繼在建和建成了數十條鐵礦石直接還原生產線,其中大部分是以轉底爐為主體還原設備的Fastmet工藝和以隧道窯為主體還原設備的H g ...
非高爐煉鐵是指高爐煉鐵之外的煉鐵方法。包括直接還原煉鐵,熔融還原煉鐵,粒鐵法,生鐵水泥法和電爐煉鐵等方法。非高爐煉鐵按工藝特徵、產品類型及用途可分為直接還原和...
13.貴州省高磷鮞狀赤鐵礦直接還原工藝中試基地建設,2011年 [1] 14.內蒙古朱日和鐵礦直接還原工藝研究,2010年 [1] 15.隧道窯盒裝直接還原鐵礦石研究與設計,2009...
重點介紹了釩鈦磁鐵礦直接還原基本原理及其還原特點,轉底爐、車底爐、隧道窯、豎爐及迴轉窯還原釩鈦磁鐵礦工藝研究情況。另外,還展望了釩鈦磁鐵礦非高爐還原工藝的發展...
近年來湧現出幾種具有代表性的直接還原工藝,如氣基豎爐、流化床裝置、煤基轉底爐、迴轉窯、隧道窯工藝,流化床工藝,可省去焦炭,直接利用粉礦,傳質和傳熱的效率高,...