烴轉化制氫是指利用蒸汽轉化工藝將輕油轉換為氫類,從而達到降低制氫成本的目的。
基本介紹
- 中文名:烴轉化制氫
- 外文名:Hydrogen production by hydrocarbon conversion
- 學科:石油煉製工程
- 技術水平:國際先進水平
- 背景:環保法規日益嚴格
- 方法:PSA淨化技術、城市煤氣製造
背景,研究內容,烴類蒸汽轉化工藝,影響因素,
背景
隨著環保法規的日益嚴格以及對油品質量要求的不斷提高和含硫原油、重質原油數量的不斷增加,使得加氫精制、加氫裂化等深加工技術成為各煉廠重要的加工工藝, 進而促使對氫氣的需求量迅速增長, 新建和擬建的制氫裝置的能力大大超過以往任何一個時期。就大多數煉廠來說, 所需氫氣絕大部分靠制氫裝置提供, 而在制氫裝置中原料費用占了氫氣成本的65%~ 85 %左右。由於大多數煉廠均採用輕油作為制氫原料(即採用輕烴水蒸汽轉化工藝), 每年消耗大量寶貴的輕質油品, 這使得氫氣生產成本居高不下, 成為限制加氫工藝發展的重要因素。因此, 如何顯著有效地降低制氫成本, 已成為石油化工領域迫切需要解決的問題。
現階段, 國內外製氫裝置仍以烴類蒸汽轉化法制氫占主導地位, 無論在催化劑方面、工藝技術方面以及裝置的可靠性方面均達到較高水平, 已為石油煉製、石油化工、精細化工的迅速發展做出了較大的貢獻。國內所採用的制氫催化劑已全部實現國產化, 其中, 烴類蒸汽轉化、變換、脫毒、甲烷化等催化劑均達到國際先進水平。
研究內容
為了有效地降低制氫成本, 國內外的研究人員主要針對下列有關制氫技術的三個方面進行了大量的研究和開發工作。
(1)原料。
目的在於拓寬制氫原料, 由輕油轉換為價格低廉且供應充足的煉廠乾氣, 如焦化富氣等,從而達到降低制氫成本的目的。
烴類蒸汽轉化制氫可採用的原料有天然氣、油田氣、石腦油、液化石油氣和煉廠各種尾氣等。在國內制氫裝置中, 絕大部分採用輕油為原料, 包括石腦油、抽余油、飽和液化氣等。近年來, 由於輕烴作為寶貴的化工原料和市場緊缺的商品燃料, 價格不斷上漲, 使以石腦油等輕烴為原料的制氫成本增高。
由於煉廠氣具有價格低廉且產氫率高等優點, 在制氫裝置上的用量日益擴大, 品種也在不斷拓寬。因此, 國內外化工行業近期都特別重視煉油廠副產的富烴氣體作為制氫(或制氨)原料的利用。然而, 由於煉廠氣中的烯烴及硫的含量較高, 必須經過脫硫、烯烴飽和等處理, 才能滿足蒸汽轉化催化劑對此類原料的各種要求。因此, 如何改進劣質原料的脫毒及精製方法, 最佳化烴類蒸汽轉化制氫的工藝流程, 為制氫裝置開闢多種廉價的原料來源, 以彌補制氫原料的短缺並最終降低氫氣的生產成本, 已成為開發研究的重要課題。
(2)工藝。
以節能、擴產、縮小裝置尺寸、降低投資費用和延長開工周期為目標進行工藝改進, 包括預轉化工藝(低溫蒸汽轉化)、自熱轉化工藝(部分氧化和絕熱蒸汽轉化)以及先進的可用於淨化煉廠氣使之滿足於蒸汽轉化催化劑要求的氣體淨化工藝等, 達到最終降低制氫成本的目的。
(3)催化劑。
圍繞著不同原料、不同工藝而開發的配套的系列化催化劑, 具體包括催化劑載體、助劑及活性組分的選擇、含量等, 以提高催化劑活性、選擇性、抗積炭性和抗硫中毒性為目標, 在此基礎上,儘可能降低催化劑製備成本。另外, 載體材料的新途徑、催化劑的異型化也是關注的內容之一。
多年來, 蒸汽轉化催化劑在合成氨、制氫、甲醇及城市煤氣工業上一直占據著重要的地位。世界上各個催化劑供應商都在對其催化劑進行不斷的改進, 使其能夠更好地適應於多變的工況、惡劣的原料等情況。現階段, 以鎳作為活性組分的蒸汽轉化催化劑在制氫工業上被廣泛採用, 其優勢在於催化劑活性高, 能夠較好地滿足轉化工藝的要求, 而且製備成本較低。不利因素是, 對於高碳烴的轉化, 易於發生積炭, 造成催化劑失活。為了克服積炭, 在催化劑中加入鹼性助劑(例如鉀鹼), 明顯地改善了催化劑的抗積炭性能。但隨著原料烴類的日益惡化以及重質化, 催化劑上的積炭也就日趨嚴重, 為此, 迫使工業上採用高汽/碳進行轉化, 這就增加了單位產品的能耗。
烴類蒸汽轉化工藝
1、城市煤氣製造工藝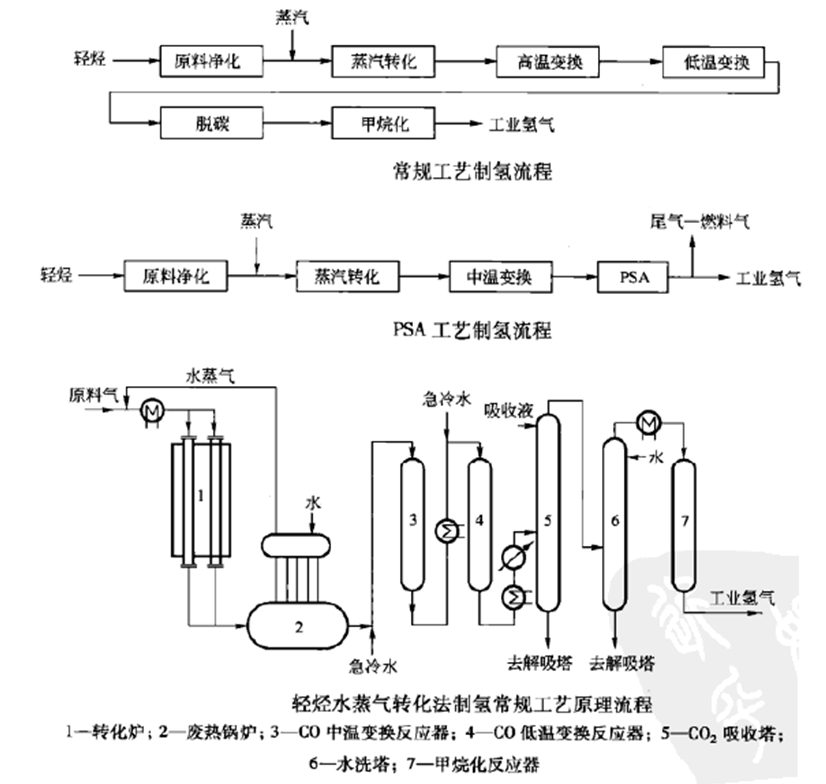
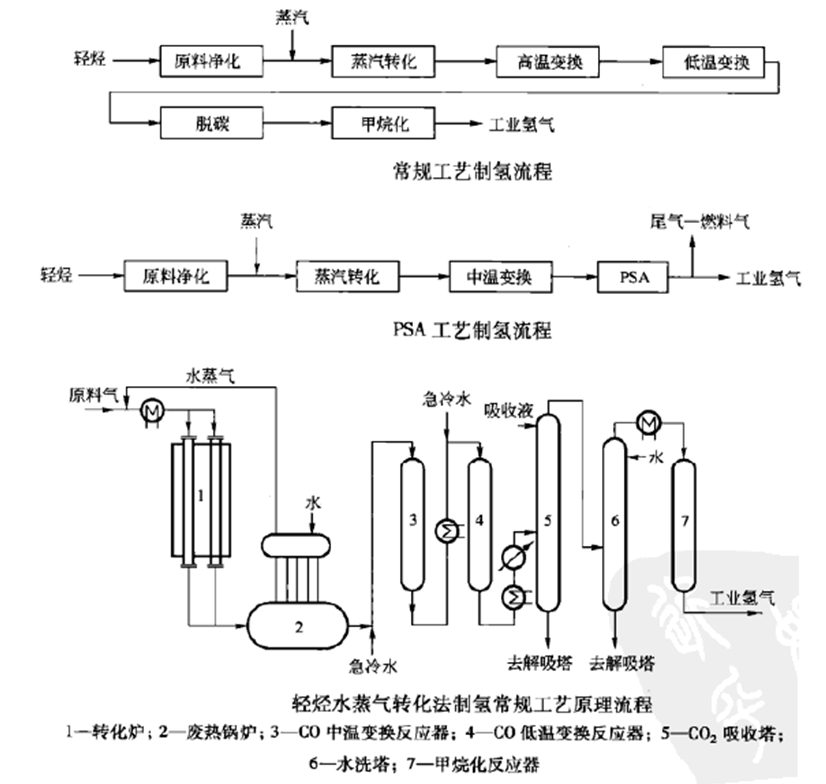
日本專利公開了一種由脫硫後的石油基烴類原料蒸汽轉化製備城市煤氣的工藝方法。該方法包括:對脫硫後的石油基烴類進行低溫蒸汽轉化, 得到含有CH4 、CO2 、H2 等氣體的低溫轉化氣, 將其導入膜分離裝置, 在膜的非滲透側得到富甲烷氣體, 然後把來自PSA 裝置的H2與之混合, 再將該混合氣進行甲烷化反應, 使CO2 轉變為CH4 , 由此得到高熱值城市煤氣的原料氣。把低溫蒸汽轉化後的氣體分出一部分使之進行高溫蒸汽轉化, 然後接著進行變換反應, 把變換後的富含H2 的氣體分成兩路, 一路作為低熱值城市煤氣的原料氣, 一路作為PSA 氣體淨化裝置的原料氣。該方法的優點在於可以同時製備高熱值及低熱值的城市煤氣。
2、採用PSA 淨化技術的制氫工藝
日本公開了一種烴類蒸汽轉化製備高純氫的方法, 原料為液化氣和石腦油。該方法採用加熱爐對蒸汽轉化反應器中的烴類原料加熱, 將反應所得氣體混合物導入變壓吸附氣體淨化裝置, 得到高純氫氣。利用變壓吸附氣體淨化裝置產生的廢氣導入反應器的加熱爐作為燃料使用, 同時回收輻射段煙氣熱量對燃燒用空氣進行預熱。制氫裝置包括預熱爐、PSA 氣體淨化裝置、熱輻射段、蒸汽轉化反應器以及加熱爐等。該方法的優點在於, 轉化爐輻射段熱效率得到提高, 達70 %以上, 而且不需要在外部供應燃料, 可減少過量水蒸汽的生成, 省略了大型的燃料氣廢熱回收裝置, 因此可減少裝置投資費用。
美國公開了一種能夠提高氫回收率的變壓吸附的工藝方法, 利用該方法制氫, 可以減小甲烷蒸汽轉化爐及變壓吸附裝置的尺寸。通常, PSA裝置的解吸氣均作為廢氣在轉化爐中被燃燒掉, 解吸氣中含有大量的氫氣, 將其回收並打入PSA 系統進行循環, 可以提高高純氫的產量。該方法通過吸附膜分離裝置將解吸氣中氣體進行選擇性的吸附,從而分離出高濃度的氫氣, 而低濃度氫氣的剩餘解吸氣部分將作為轉化爐中的燃料被利用。
3、採用甲醇和氫氣聯產技術的制氫工藝
世界專利公開了一種甲醇和氫的聯產工藝。該工藝包括:
(a)在高溫和高壓下進行烴類原料的蒸汽轉化, 得到含有氫氣、碳氧化物、甲烷及未反應的蒸汽等氣體的混合氣;
(b)將所得的轉化氣冷卻, 並將冷凝水分離掉;
(c)將脫水後的轉化氣不經壓縮直接進行甲醇合成, 將合成的甲醇從產品中分離出來,剩下未反應的氣體物流;
(d)從未反應的氣體物流中分離出氫氣。該集成工藝在製備氫氣和甲醇時, 產品收率得到提高, 具有明顯的經濟性。利用這一方法, 可以製得大量的甲醇, 能夠滿足煉油廠對MTBE 和TAME 原料的需求。該工藝可利用現有制氫裝置稍做改動後就可聯合生產氫氣和甲醇。
4、採用預轉化技術的制氫工藝
托普索公司申請的專利公開了一種烴類蒸汽轉化製備富含CO 和氫氣的方法, 包括下列步驟:
(a)讓預轉化的烴原料氣體任意地通過在反應器壁上載有蒸汽轉化催化劑薄膜的第一管式反應器, 該反應器能與來自後置的第二管式蒸汽轉化反應器的熱煙氣進行熱交換;
(b)讓第一管式反應器的流出物流入具有蒸汽轉化催化劑薄膜並被燃料燃燒加熱的第二管式反應器, 由此獲得部分蒸汽轉化氣流和熱煙氣;
(c)讓第二反應器的流出物通過固定床蒸汽轉化催化劑;
(d)從固定床排出富CO 和H2 的產品氣。其中, 固定床蒸汽轉化催化劑可以在絕熱條件下進行操作, 所採用的催化劑是鎳系和/或釕系催化劑。利用該方法製備合成氣, 使轉化器的傳熱效率提高約49 %, 同時, 降低了催化劑消耗、轉化器中的管材消耗(24 %)以及燃料消耗(7 .4 %)。世界專利WO98/28071 公開的一種烴類原料蒸汽轉化製備碳氧化物和氫氣的工藝方法及設備,包括:將烴類原料和轉化劑(水蒸汽)輸入蒸汽轉化段, 其中包括裝有轉化催化劑的多個轉化室;在轉化反應條件下使烴類物質和蒸汽進行轉化反應, 製得合成氣混合物。可利用燃燒燃料和空氣對轉化段進行熱量供給, 先對含有可燃燒氧的氣態物流(指空氣)進行增濕, 使增濕後的空氣在進入轉化器之前與流出轉化段的合成氣混合物之間進行熱交換, 然後收集利用冷卻後的合成氣混合物, 同時也回收燃料燃燒後的產物及未燃燒物。該工藝的優點是開停車比較方便快捷, 而且能夠使轉化爐的熱量供給達到較好的平衡。
5、採用部分氧化和蒸汽轉化相結合的制氫工藝
日本專利公開了一種烴類蒸汽轉化製備富氫氣體的工藝及其製備, 該工藝方法包括:將烴類原料和氧氣/或空氣輸入第一反應室, 即部分氧化室,製得含有H2 和CO 的合成氣;將烴類原料和蒸汽輸入第二反應室, 即蒸汽轉化室, 製得合成氣, 轉化室所需熱量由部分氧化室產生的熱量來提供, 最後將兩個反應室的氣體產品混合得到合成氣, 通過水煤氣變換反應後可進一步提高氫氣濃度。工藝的專用設備也同時要求保護。該工藝使部分氧化和蒸汽轉化反應操作條件得到最佳化, 可有效地製備H2和CO。
影響因素
1、溫度的影響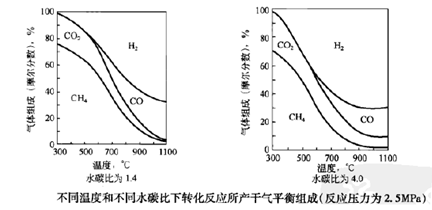
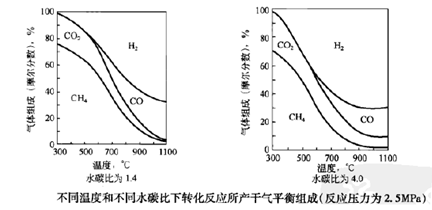
轉化爐出口溫度是影響輕烴水蒸氣轉化反應的最重要參數。烴類的水蒸氣轉化是一個強吸熱反應,其反應平衡常數隨溫度的升高而增大,如表所示,所以高溫對反應有利。這一點從右圖中也可以清楚地看出。一般情況下,轉化爐出口溫度提高10℃左右,爐出口殘餘甲烷含量約降低1%。但是,溫度越高,原料在轉化爐內的結焦傾向越大。此外,爐管的使用壽命也隨溫度的升高而降低,提高溫度受到反應爐管材質最高允許使用溫度的限制。工業上一般控制在800℃左右,但有逐漸升高的趨勢。
溫度,℃ | CH4+H2O=CO+3H2 | CO+H2O=CO2+H2 |
500 | 0.00586 | 126 |
600 | 0.38 | 27.08 |
700 | 7.4 | 9.017 |
900 | 0.001307 | 2.204 |
2、水碳比的影響
所謂水碳比(H2O/C)是水蒸氣分子數與制氫原料中碳原子數之比,它是輕烴水蒸氣轉化制氫過程的一個重要的操作參數。從上圖可以看出水碳比對產氣組成的影響。增加水碳比有利於原料的充分利用,降低制氫成本,同時可以防止催化劑積炭,所以實際採用的水碳比較按化學反應平衡計算的理論值(稱為最小水碳比)要大得多。但是,水碳比過高會一導致蒸汽消耗過多,反應管內的壓降太大,能耗也過高。目前工業上採用的水碳比一般為3-5,常規制氫裝置採用4-4.5, PSA制氫裝置採用3.5-4。對於以甲烷為主的原料可以用較小的水碳比,而對於相對分子質量較大的輕烴則需用較大的水碳比。
3、壓力的影響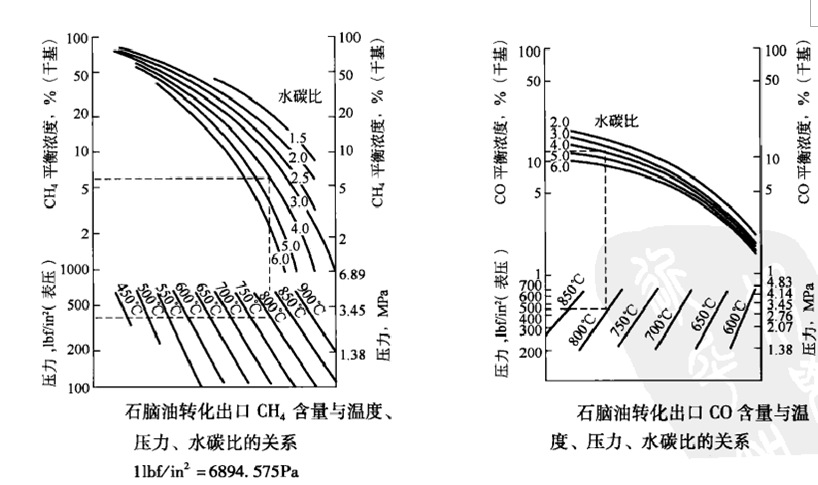
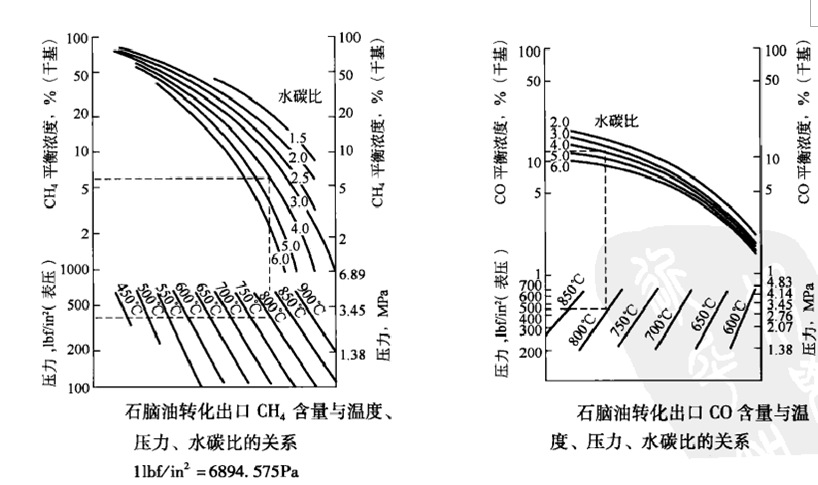
輕烴水蒸氣轉化反應產物的分子數是大於其原料的,是體積增大的反應,由此可以判定低壓對反應有利。但是在工業上仍採用在加壓下進行反應,這是由於所產氫氣都將在有壓力的情況下利用,所以總的來著在加壓下制氫經濟性更好。對於因加壓導致對轉化反應的不利影響,可以用提高反應溫度及水碳比來加以彌補,但所用的壓力一般不超過2.8MPa。
下表所列為輕烴水蒸氣轉化所產乾氣的典型組成。由此可見,其中還含有相當量的CO及CO2,以及少量甲烷,這些都需要進一步加以轉化和脫除。
組分 | 含量(摩爾分數),% | 組分 | 含量(摩爾分數),% |
CH4 | 2.0 | CO2 | 12.0 |
CO | 14.5 | H2 | 71.5 |
實際上,溫度、壓力和水碳比三者對輕烴水蒸氣轉化過程的轉化率(出口CH4含量)、CO和H2含量的影響相互藕合,具體制氫裝置必須根據原料、催化劑特性和氫氣的純度、壓力等具體要求合理地選擇操作條件,右圖的結果即是一個很好的例證。