基本介紹
- 中文名:東風商用車車身廠
- 產量目標的:167.94%
- 駕駛室:158597台
- 時間:2010年
產銷實力,駕駛室品質,質量標準化,經營亮點,混流生產,高產,產量目標,
產銷實力
東風商用車車身廠最新生產經營數據顯示,2010年11月份該廠生產駕駛室18233台,單月產量達到合資以來最高點,其中D310、D530產量分別為11015台和3979台,這兩種產品單月產量均創上市以來歷史新高。
據了解,2010年1-11月份,車身廠累計生產駕駛室158597台,已完成全年預算產量目標的167.94%。在產品結構方面,1-11月份D310、D530產量分別為92823台和31517台,占該廠駕駛室總產量的80%左右。根據12月份生產計畫,D310全年產量有望突破10萬台,預計2010年車身廠駕駛室總產量將達到17.5萬台。當前,D310、D530日產量雖然處於歷史高點,並且隨著D530塗裝新車間建成投產,D310、D530駕駛室實現混流生產,車身廠生產能力也將進一步提升,但車身廠面對高產從容應對,生產現場秩序井然,員工加班連點時間較上半年也有所減少。
2010年1-9月車身廠累計生產駕駛室127347台,根據第四季度排產安排,該廠將抓住東風商用車高產旺銷勢頭,實現全年16萬台駕駛室生產目標。
據介紹,前三季度,東風商用車車身廠主要產品為東風天龍、東風天錦、EQ153系列以及長頭車系列,其中天龍和天錦駕駛室產量總和達10萬台,占該廠駕駛室總產量的78%左右。第四季度將採取四項措施力保全年產量目標:一是進一步提高天龍、天錦焊接混流線和塗裝新車間的生產能力,增加天龍標準型駕駛室在山下車間的生產數量;二是通過檢修和設備日常維護,為挑戰全年產量目標提供可靠的裝備保障;三是最佳化生產組織,在生產計畫編制上,將同種漆色的產品放在一個批次,實行合序生產,降低換漆頻次,提高生產效率;四是調整產品結構,改變焊接車間作業方式,在長頭車和平頭車等老產品生產線上採取一人多崗輪流作業,將更多的人力集中到新產品生產線,提高全員勞動效率,提升整體生產水平。
駕駛室品質
東風商用車基層生產單位真正把產品品質做到讓用戶放心,在東風商用車車身廠質量部、裝焊作業三部調研東風天龍駕駛室D310焊接質量時發現,車身焊裝穩定控制在管理目標值之內的三項關鍵指標,給了D310車身用戶一個肯定的答案。三項關鍵指標是: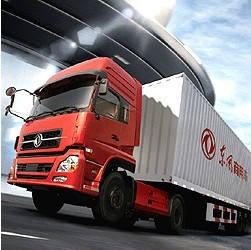
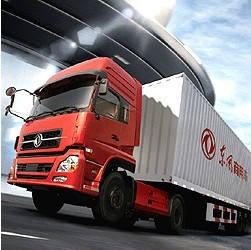
OK-VES質量抽查缺陷點控制在0.49-0.41個點(目標值為0.5個點)。
一次交檢合格率穩定控制在96.1%-96.8%之間;
作業部當月廢品損失小於目標值的5倍多。
好的指標達成源於好的管理。據了解,車身廠以裝焊作業三部為首的四項品質保證措施,為D310車身質量達標起了關鍵作用。
保證質量管理體系在運行中發揮作用。推行 “QCC” (即Quality Control Circle“品質管理圈”)和“自工程全數品質保證”(即對自己的產品品質作出承諾和保證的一種系統的質量管理模式)活動,以作業部各生產班組為單位,按照“一元化”管理的方式,每天召開QCC分析會,再根據解析的問題快速整改。
注重全員全數品質保證的學習與培訓。該部先後組織員工進行D310車身焊接標準作業培訓、焊接工藝及基礎知識培訓、班組長GK診斷綜合培訓和裝備自主保全專題培訓等,並以班組為單位開展了ILU技能培訓和OPL培訓(指一個重點的訓練),對作業部9個生產班組156名員工進行了100%技能升級培訓,達標率100%。其中,經培訓達到U級水平員工9人,L級水平員工137人,I級水平員工17人。並針對D310地板線一工位、總裝線三工位、分裝班側圍、車門工位和KUKA線地板一工位、總裝十二工位、分裝高頂雙臥後圍、頂蓋工位等重點難點工位作了OPL訓練;通過不斷地學習和培訓提高員工的綜合技能,引導員工樹立正確的質量觀,積極參與現場改善,形成重視質量進步、崇尚自主創新的良好氛圍。通過開展“自工程全數品質保證”活動,D310車身在OK-VES評審中因管理問題造成的焊接質量缺陷同比下降了20%,焊接打點數提升至目前的98%。
“過程控制零缺陷”的質量競賽顯現活力。作業部強化過程質量控制,嚴格要求各工序認真貫徹落實“三不”(不接受不良品,不放過不良品,不製造不良品)原則,並加大了過手質量考核和現場稽查力度,使工序自控水平保持穩中有升。針對現場存在的質量問題,作業部質量稽查小組以一次交檢合格率、OK-VES缺陷點和不合格品率為主要依據,定期開展質量稽查。在開展“過程控制零缺陷”的質量競賽中,作業部各班組各出妙招抓自控:KUKA線總裝班針對駕駛室外表面易劃傷、坑包等特點,推行“質量聯保”,即從三工位側圍上線到十二工位下線,相關工位員工逐一進行確認並標識,發現問題及時處理並記錄。據一次交檢統計,“質量聯保”措施實施以來,該班側圍、車門的劃傷、坑包等情況,均得到有效控制。
“三現”改善促進品質提升。“三現”即現場、現物、現策。如果你問這個部的員工“出現質量問題怎么辦”,員工會說——走,到現場去,觀察現物,提出現實對策。今年6月,內飾質量信息反饋:側圍右輪罩與地板翻邊搭接間隙過大,不便裝配。作業部聞訊迅速立項改善,使問題一出現就得以快速整改。分裝班通過對D310駕駛室側圍門框導電板進行的改善、對高頂雙臥駕駛室後圍外板焊接定位樣板進行的改善、對高頂駕駛室後下頂蓋夾具加裝定位導向的改善等,使作業部實物質量穩步提升,一次下線合格率穩定在96%以上。維修班改善KUKA線機器人水芯,不僅使機器人的焊接質量得到鞏固,還實現了備件的國產化,一年可節約機輔具費用近10萬元。
質量標準化
日前,國家安全生產監督管理總局授予東風商用車車身廠“一級安全質量標準化企業”稱號,這標誌著車身廠持之以恆開展的安全質量標準化工作,得到國家權威機構的認可。
車身廠廠長毛長林告訴記者,工廠深入持久的“安全質量標準化”活動,使工廠環境/職業健康安全一體化管理體系發揮效應,生產過程中物的不安全狀態和人不安全行為得到有效控制,從基礎上規範了企業安全生產行為,保障了企業的安全生產。
據了解,車身廠在近年來的安全質量標準化工作中,高起點規劃,高水平管理,始終把企業的安全管理放在首位,認真貫徹執行“安全第一,預防為主”的方針,以體系建設為保障,以制度建設為規範,以全員參與為基礎,以加強預防為核心,以《安全生產法》等安全法律法規為準則,採取系列行之有效的措施,全面推進安全生產管理規範化和標準化。
首先是成立創建安全質量標準化企業領導小組、工作小組和專項工作推進辦公室,組成基礎管理、機械、電氣、易燃易爆和熱工、作業環境等5個專業組。二是邀請專家現場諮詢,選派人員參加考評標準培訓,通過廠內區域網路公布《安全質量標準化工作指南》,組織全員學習培訓。三是制定、完善各項管理制度。據統計,車身廠依據安全質量標準化業務流程,先後制定出覆蓋全廠的42項管理制度。四是通過設備設施普查,做到設備設施管理和運行安全受控。
據悉,為進一步鞏固和擴大安全質量標準化工作成果,目前,車身廠正結合安全生產新形勢、新要求,有序推進安全生產工作創新。
經營亮點
2010年12月16日,東風商用車車身廠召開2010年終經營分析會,總結2010年生產經營工作,謀劃和分析2011年工作思路。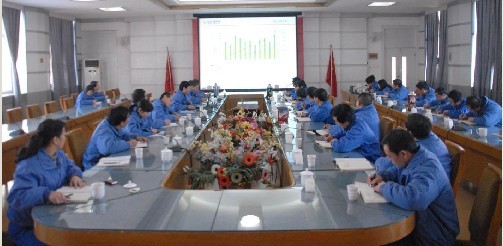
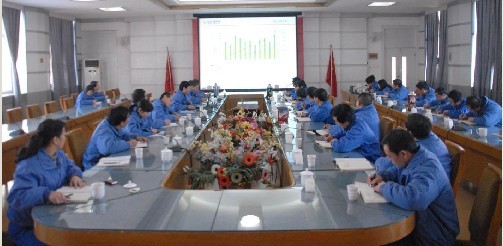
據了解,2010年車身廠生產經營亮點主要體現在以下方面:2010年1-11月份車身廠累計生產駕駛室158597台,完成年度預算產量的153.2%,成本、質量等各項KPI指標全面達成挑戰目標;品種結構進一步最佳化,D530、D310已替代EQ153系列產品成為工廠主打產品;面對高產挑戰,工廠上下積極挖掘改善課題,有力支撐了各項KPI指標的實現;職能部門積極作為、服務現場,提高設備綜合效率和產品質量,保證高產順利進行;D530面漆生產線順利投產,D530、D310焊接線實現混流生產,綜合產能進一步提升。
針對2011年生產經營工作,由於2011年我國汽車產業環境更加複雜,東風商用車車身廠面臨的指標壓力更大,各單位要提前做好工作規劃和管理預控工作,規避潛在的生產經營風險。在工廠管理方面要以效率為中心,通過提升全員勞動效率和人事效率,進一步改善經營質量,保證員工收入穩定增長。
混流生產
2010年9月份,東風商用車車身廠D310駕駛室排產突破10000台,D530排產達3500多台,單月排產均創歷史新高。

10月份車身廠D310駕駛室日均產量345台,已達到產能極限,為緩解生產壓力,決定在本月初實現D310、D530混流生產的基礎上,著力提高D310、D530混流生產線節拍和柔性化技術水平,對焊接夾具和機器人程式進行適應性改造,減少設備磨合時間,逐步提升D310生產小時均衡。與此同時,車身廠多部門聯手,對混流生產中物流運轉方式,工位器具等進行一系列的改善,使D310、D530混流生產線D310日產量提升到80台左右,駕駛室骨骼精度穩定達標,實現了D310產能和質量雙提升。
至2010年9月26日,車身廠在山下車間混流生產D310標準車超過1000台,約占D310車型總產量20%。
高產
目前商用車車身廠一方面搶抓市場機遇,開足馬力戰高產;一方面從產能提升、成本控制、提高全員勞動效率三個方面落實“863振興計畫”。在產能提升方面,車身廠在推進東風天錦金屬漆能力項目建設的同時,通過工廠內部的技術改造和管理改善,提升東風天龍瓶頸工序的生產能力。在成本控制方面,車身廠以過程控制為重點,強化細節管理,分析成本管理數據背後的癥結和變動因素,進一步提高工廠低成本運營的能力。在提高全員勞動效率方面,車身廠採取靈活動態的用工機制,根據車間每月產量和用工情況實行餘缺調劑,最大限度地盤活現有人力資源。
產量目標
2月16日,東風商用車公司車身廠召開了第十二屆五次員工代表大會暨2012年工作會,確立了新一年的“三大”工作目標:全面、高質量地完成公司下達的生產任務和KPI指標,2012年駕駛室預算產量目標為15.2萬台;鞏固車身廠現有的管理水平和成果,力爭有所突破和上升;持續推進和諧工廠建設,提升員工滿意度和幸福感。
2012年車身廠面臨三個方面的挑戰和壓力:一是預算產量穩中有降,起伏較大,多餘產能和不平衡的產量對成本的影響十分突出;二是改善壓力增大,實現東風商用車公司下達的DSTR(標準設計時間倍率)、庫存資金和製造周期“三年減半目標”進入了攻堅期,實現2012年的目標難度非常大;三是完成指標的難度增大,質量指標管控更加嚴格,後工程不良要由去年的12%降到今年的2%,CS-VES(客戶滿意質量評審系統)要由去年的1.85降到今年的1.1。成本管理方面,東風商用車公司將實行全成本CPU(輛份成本)管理模式,這對工廠成本管理提出新挑戰。
基於對形勢的分析判斷,2012年車身廠工作的總體思路是:以科學發展觀為指導,認真貫徹落實公司工作會精神,繼續實踐“構建和諧工廠、創建節約型企業”願景和“以人為本、強化溝通、細化數據、用戶滿意”管理方針,緊緊圍繞工廠年度目標,以“改變思維模式、推動管理創新”和“強化自主意識、推動技術創新”為基礎,在新方法套用、製造效率提升和人才培養等方面開展紮實工作,不斷推動車身事業新發展,提升工廠對公司事業計畫的貢獻度。
根據2012年車身廠工作總體思路和生產經營目標,車身廠著重從新方法套用的深化和細化、提升技術創新的貢獻度、持續提升製造效率、改變思維模式創新管理、培養造就各方面專門人才等五個方面開展工作。