基本介紹
- 中文名:控制分級
- 外文名:Control classification
- 釋義:礦物與脈石分離裝置
- 工作:自動檢測儀表和控制裝置
- 學科:採礦
概念
介紹
組成
水力旋流器在銅鉛鋅礦控制分級中的套用
研究背景

控制分級工藝的確定
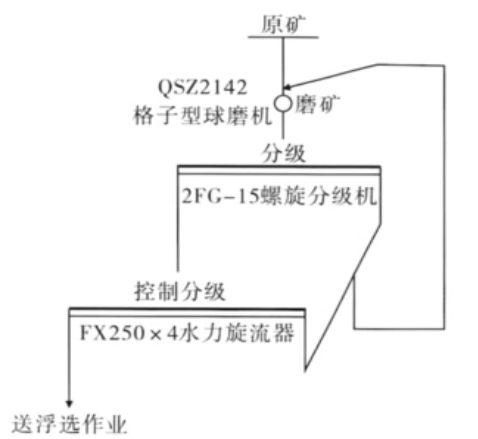
分級控制又稱等級控制或分層控制,是指將系統的控制中心分解成多層次、分等級的制體系,一般呈寶塔型,同系統的管理層次相呼應。分級控制的特點是綜合了集中控制和分散...
控制分級是有用礦物與脈石的充分的單體分離,所屬選礦作業過程控制內容之一。...... 控制分級是有用礦物與脈石的充分的單體分離,所屬選礦作業過程控制內容之一。...
分級調節是一種分層控制的方式,比如下丘腦能夠控制垂體,再由垂體控制相關腺體,例如甲狀腺。...
一個交通控制系統中使用多台計算機,每台計算機承擔系統一部分功能的交通控制系統。一般用於較大區域的實時交通自適應控制系統。同步協調控制的交通信號。即聯動信號控制...
分級遞階智慧型控制(Hierarchical Intelligent Control) 是在自適應控制和自組織控制基礎上,由美國普渡大學Saridis 提出的智慧型控制理論。分級遞階智慧型控制主要由三個控制級...
等級的行為控制系統(hierarchical behavior controt system)協調有機體動作所必需的神經結構。在有機體等級系統中,上級中樞通過選擇性的興奮和抑制來控制下級中樞。高度...
控制測量是指在測區內,按測量任務所要求的精度,測定一系列控制點的平面位置和高程,建立起測量控制網,作為各種測量的基礎。控制網具有控制全局,限制測量誤差累積的...
標準的分級是指我國的標準按《中華人民共和國標準化法》分為四級:國家標準、行業標準、地方標準和企業標準。...
分級存貨控制制度,按存貨的價值和對生產經營活動的重要程度,將存貨劃分為A,B,C 三類進行分別管理。...
頻率:指在一個周期內的重複次數,或每秒的周波數。分級:根據固體顆粒因粒度不同在介質中具有不同沉降速度的原理,將顆粒群分為兩種或多種粒度級別的過程。...
系統分級Windows新系統中的電腦性能檢測工具,測量計算機硬體和軟體配置的功能,並將此測量結果表示為稱作基礎分數的一個數字。...
IE分級審查是用分級系統來幫助用戶控制在該計算機上看到的Internet內容,它可以過濾掉一部分不健康的東西,即根據用戶的要求,由系統自動對那些包含暴力、性、裸體、語言...
旋迴分級對比是指“ 旋迴對比、分級控制” 的地層對比技術方法。即在標準層控制下的單層對比方法。...
分級網路是在政府、企業集團等大型網路中,IT基礎結構複雜、設備眾多,數據類型繁雜,數據量越龐大,且存在較多樹形或星形拓撲的分支機構。而各分支結構也已基本完成了...
危險源分級實質上是對危險源的評價。危險源分級一般按危險源在觸發因素作用下轉化為事故的可能性大小與危險源引起事故後果的嚴重程度來劃分。...
目前的物料分級方法主要有4大類,即水力分級、氣流分級、篩分分級和複合力場分級等。根據作用力的不同,又分為重力分級和離心力分級兩種。重力分級是根據物料密度、...
網路層還可以實現擁塞控制、網際互連等功能。分級層次結構傳輸層(Transport layer) 第4層的數據單元也稱作處理信息的傳輸層(Transport layer)。但是,當你談論TCP等...
根據美國道路通行能力手冊(HCM 2000)定義,控制延誤是指用戶由於控制器的原因而經歷的多餘的旅行時間,包括信號分配的通信權,將通行權以安全的方式過渡所花費的時間,...
等級的行為控制系統,是指協調有機體動作所必需的神經結構。在有機體等級系統中,上級中樞通過選擇性的興奮和抑制來控制制下級中樞。高度興奮的中樞有使有機體活動的...
IE分級審查是用分級系統來幫助用戶控制在該計算機上看到的Internet內容,它可以過濾掉一部分不健康的東西,即根據用戶的要求,由系統自動對那些包含暴力、性、裸體、語言...
《控制》是由安東·寇班執導,薩姆·賴利、薩曼莎·莫頓主演的黑白傳記電影,於2007年10月10日在美國上映。該片講述了20世紀70年代搖滾樂巔峰時期,朋克音樂的領軍...
(衛生部84號令〔2012〕)精神,抗菌藥物臨床套用實行分級管理,根據安全性、療效、...(三)嚴格控制特殊使用級抗菌藥物使用。特殊使用級抗菌藥物不得在門診使用,住院...
2015年9月8日,國務院辦公廳以國辦發〔2015〕70號印發《關於推進分級診療制度建設的指導意見》。該《意見》分總體要求、以強基層為重點完善分級診療服務體系、建立...
燃料分級燃燒技術又稱為再燃燒技術或三級燃燒技術,其特點是將燃燒分成3個區域:一次燃燒區(即主燃燒區)是氧化性或弱還原性氣氛;在第二燃燒區,將二次燃料送入爐...
中文名 等級制組織 1.垂直指揮鏈最簡單又最常見的組織形式是等級制。等級制的優點:(1)易於理解,運營簡單(2)組織中存在清晰且直接的控制鏈使得組織的決策制定迅速...
分級分散式系統是指按計算機開放系統互連(ISO/OSI)參考模型組織的一種分散式系統結構。該系統的所有組成部分均作為單元、屬於某個邏輯控制層(級),每個單元受較高一...