微燃燒室(別稱微尺度燃燒室)是指進行微尺度燃燒的裝置,其容積通常低於1立方厘米。微尺度燃燒是隨著MEMS(微機電系統)技術的發展而提出的,它是相對於傳統燃燒發生在較大的尺度範圍而言的。微燃燒室是微動力系統的重要組成部分,其作用是通過燃料在微燃燒室內發生燃燒反應產生熱能,為微動力系統的能量輸出服務。詳細介紹了其國內外研究現狀、物理模型和數學模型、計算機仿真以及虛擬裝配原則與套用等。
基本介紹
- 中文名:微燃燒室
- 外文名:Micro combustor
- 別名:微尺度燃燒室
- 作用:微尺度燃燒、節能
- 領域:能源
- 學科:熱力學
簡介,研究現狀,國外研究現狀,國內研究現狀,物理模型和數學模型,物理模型,數學模型,微燃燒室的計算機仿真,微燃燒室虛擬裝配原則及套用,
簡介
隨著各種微型化機械裝置系統的出現,研製作為微系統能量供給的微能源系統(PowerMEMS System)一直受到世界各國的普遍重視。1997年美國麻省理工學院(MIT)首次提出了研製矽基燃燒/透平發動機的構想,希望開發出一種能量密度遠高於銼電池數十倍,亞立方厘米體積的微燃燒/透平發動機。由於該發動機與其它微能源相比,具有能量密度高、供電時間長、體積小、無污染等優點,有望在未來得到廣泛的套用,所以其相關技術的研究受到了各國專家的普遍關注。
微尺度燃燒室是微燃燒/透平發動機的關鍵部件,對其燃燒性能的研究具有非常重要的意義。
研究現狀
自 20 世紀 80 年代以來,微機電系統(MEMS:micro-electro-mechanical systems)迅速發展,在航空、航天、汽車、軍事等領域的套用越來越多。微動力系統重量輕,比能高,壽命長,可以滿足 MEMS 的能源供給需求,引起了各國學者的廣泛關注。
國外研究現狀
微燃燒器是微動力系統的重要組成部分,其作用是通過燃料在微燃燒室內發生燃燒反應產生熱能,為微動力系統的能量輸出服務。為了在微燃燒室內實現穩定高效的燃燒,國外學者進行了多種嘗試。如 LarsSitzki 等對螺旋形微尺度逆流回熱型“Swiss Roll”燃燒器內的燃燒過程進行了實驗研究,現通過採用回熱加熱可燃混合氣、催化助燃和努力減少熱損失等措施就能在微燃燒器內實現燃料的穩定燃燒。麻省理工學院製造了三晶片的接觸反應燃燒器,實驗表明,在該燃燒器內採用乙烯/空氣和丙烷/空氣為燃料的燃燒效率超過 40%。George A. Boyarko 等實驗研究了內徑分別為 0.4 mm 和 0.8 mm 的金屬鉑製成的微管內過量氫氣和氧氣的燃燒過程,確定了兩種直徑微管內的最低催化預熱溫度,在實驗條件下該溫度介於 350 ~400 K 之間。Shan 等製造的微燃燒器由矽晶片構成,有七層微結構,帶有一條燃料空氣循環通道,實驗測得的排氣出口處的最高溫度達 1 700 K。
國內研究現狀
在國內,李軍偉等在微小型 Swiss-roll 燃燒室內進行了甲烷/空氣預混氣的燃燒實驗,獲得了燃燒器的可燃極限,並研究了回熱對燃燒器可燃極限的影響。朱林等採用二維計算流體動力學(CFD)數值分析方法,研究了在微尺度燃燒器入口處混合氣體流量不變的情況下,改變氫氣/空氣當量比對微尺度燃燒器燃燒特性的影響。鐘
北京等設計了一個通道截面為 7mm×0.6mm的等速螺線過量焓微燃燒器,並在其中完成了甲烷/空氣預混氣的燃燒實驗。通過數據採集系統得到了微燃燒器端面的溫度分布,並使用氣相色譜法分析了煙氣成分。蔣利橋等對靜止空氣中自由射流微噴管甲烷/空氣預混合火焰的燃燒特性進行了實驗研究,考察了火焰高度特徵及其相關影響因素,並詳細探討了尺度變化對微火焰熄火極限的影響。潘劍鋒等在碳化矽材料的亞毫米尺度微燃燒室內,針對甲烷和氫氣兩種不同燃料進行了燃料與氧氣預混合燃燒的實驗。利用熱電偶測出燃燒室壁面溫度並進行了分析。在微尺度燃燒中,由於燃燒器的尺寸很小,燃燒過程與常規燃燒過程不同,而相關實驗設備的開發滯後,造
成對微燃燒機理的認識不足。
北京等設計了一個通道截面為 7mm×0.6mm的等速螺線過量焓微燃燒器,並在其中完成了甲烷/空氣預混氣的燃燒實驗。通過數據採集系統得到了微燃燒器端面的溫度分布,並使用氣相色譜法分析了煙氣成分。蔣利橋等對靜止空氣中自由射流微噴管甲烷/空氣預混合火焰的燃燒特性進行了實驗研究,考察了火焰高度特徵及其相關影響因素,並詳細探討了尺度變化對微火焰熄火極限的影響。潘劍鋒等在碳化矽材料的亞毫米尺度微燃燒室內,針對甲烷和氫氣兩種不同燃料進行了燃料與氧氣預混合燃燒的實驗。利用熱電偶測出燃燒室壁面溫度並進行了分析。在微尺度燃燒中,由於燃燒器的尺寸很小,燃燒過程與常規燃燒過程不同,而相關實驗設備的開發滯後,造
成對微燃燒機理的認識不足。
物理模型和數學模型
物理模型
此處介紹的物理模型是矩形微通道。微燃燒室示意圖如圖所示.燃燒室材料為不鏽鋼,採用3維模擬方法,通道外部尺寸為10 mm x 7 mm x 1. 6mm,內部尺寸為10 mm x 6 mm x 0. 6 mm.由於燃燒室結構規則,採用結構化格線進行計算.不鏽鋼的物性參數:密度為8 030 kg·m-3,比熱為502. 48)·(kg·K)-1 導熱係數為16.27 W·(m·K) -1。
示意圖
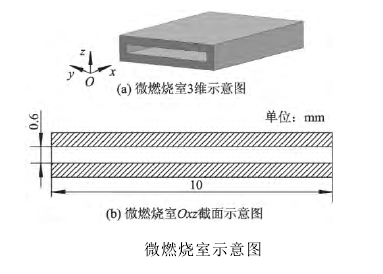
數學模型
數學模型包括以下基本控制方程:連續性方程、組分守恆方程、動量守恆方程和能量守恆方程.通道外壁面採用綜合換熱邊界條件.假設忽略體積力、流動耗散和內部氣體輻射效應,忽略燃燒過程中湍流脈動現象,採用層流有限速率燃燒模型.
微燃燒室的計算機仿真
由於微燃燒室尺寸過小,以及相關實驗設備功能的限制,目前大都採用計算機仿真的方法來研究微燃燒室的燃燒特性,如基於CFD軟體Fluent平台,模擬燃燒室在各種條件下的燃燒狀況,以獲得一定的燃燒特性參數。但想要得到滿意的數值模擬結果,建立精確的幾何模型是非常必要的。目前,導入Fluent進行流體動力學研究的幾何模型一般採用線框建模的方法,利用Fluent前置模組Gambit來構建;
研究發現,上述建模方法能保證進行流體動力學計算所需要的精度,但依據MEMS器件設計理念,從機械結構設計角度來看,顯然還是不夠的,具體表現在:
(1)從建模方法看,由於線上框模型中沒有面和體的概念,因此無法區別物體的內部和外部,無法採用連線許多簡單幾何對象的方式來構造複雜的結構,進而無法檢驗所構建的幾何形體的正確;
(2)從機械結構設計角度看,該方法無法進行參數化建模,但作為微燃燒系統的器件一燃燒室,如藉助高柔性、封裝後的參數化模型來實現,可減少設計的反覆次數,簡化整個燃燒系統設計的難度和煩瑣程度,對於提高設計質量和效率至關重要;
研究發現,上述建模方法能保證進行流體動力學計算所需要的精度,但依據MEMS器件設計理念,從機械結構設計角度來看,顯然還是不夠的,具體表現在:
(1)從建模方法看,由於線上框模型中沒有面和體的概念,因此無法區別物體的內部和外部,無法採用連線許多簡單幾何對象的方式來構造複雜的結構,進而無法檢驗所構建的幾何形體的正確;
(2)從機械結構設計角度看,該方法無法進行參數化建模,但作為微燃燒系統的器件一燃燒室,如藉助高柔性、封裝後的參數化模型來實現,可減少設計的反覆次數,簡化整個燃燒系統設計的難度和煩瑣程度,對於提高設計質量和效率至關重要;
(3)從MEMS器件設計角度看,該微燃燒室主要是通過燃料/空氣混合燃燒將化學能轉化為熱能,進而轉化成機械能推動後續器件一渦輪進行工作,但由於該燃燒室尺寸微小,可能因為整個燃燒室結構溫度過高,導致其疲勞破壞,因此,對其進行藕合場分析、瞬態分析、應力應變分析非常必要。
微燃燒室虛擬裝配原則及套用
通常虛擬裝配有自頂向下(Top -Down)和自底向上(Down -Top)兩種裝配形式。自頂向下裝配形式的主要優點在於:所有設計的零件都是根據最終產品的要求在裝配環境下完成的,因而能確保每個零件的設計從產品設計開始就被有效地控制在最終產品可裝配的範圍內,真實反映了設計過程,節省了不必要的重複設計,提高了設計效率,尤其適合全新產品的研發;自底向上的裝配方法特點在於:設計者從最簡單的零件每個單獨設計,並利用裝配約束將
其組合成裝配體,然後對整個裝配過程進行分析,如發現不符合要求的零件,需重新設計、重新裝配,直至零件滿足要求。該方法充分利用了現有的設計資料,有效地避免了重複設計,因而非常適合產品的更新和系列化開發。
SolidWorks平台是通過Layout(布局)來完成從上到下的功能設計的。Layout實質上是一個傳統粗總裝二維圖。它可以使用戶在其上定義一個部件的基本功能要求、基本結構和全局參數之間的順序依賴關係。藉助這個草圖和
SolidWorks的形狀置換功能可有效地完成自頂向下的設計過程,但自頂向下及子功能的聯繫還不能完全實現,從草圖到零件造型過程中產品功能信息的流程設計仍然依靠設計者掌握。
基於以上的分析和討論,在實際的微燃燒室結構設計過程中,採用了自頂向下和自底向上並用的方法。具體地說,先考慮產品的功能及裝配的問題,然後對組成裝配體的零部件進行詳細設計。在這一過程考慮零部件在裝配、功能及製造等方面的設計,即後期零部件的設計依賴於前期的功能及裝配設計;後期為前期規定了行為準則和性能要求,這一過程是一種自頂向下的設計過程。但是,在這個過程中存在著後期和前期相互反覆的過程,所以,實際的設計並不是嚴格的自頂向下,而只能說在整體上是自頂向下,在局部上仍屬於自底向上的設計方式。通過這種方法,所設計器件(這裡是微燃燒室)的主模型在所屬的裝配配合中被描述,允許設計人員的工作與整個產品的進展過程相關聯,部件模型的變化將自動反映到相應的裝配部件中,從而保證了模型數據的集成性,避免了設計工作的重複。
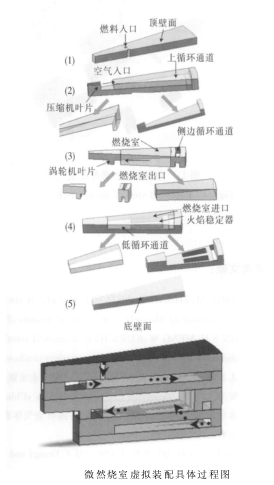
微燃燒室各晶片的具體虛擬裝配過程如圖。