簡介
五十年代以來,由於
催化重整可以提供廉價的副產氫氣,餾分油的加氫精制得到了廣泛的套用和發展,逐漸取代了酸鹼用量大、廢渣難於處理的電化學精製。經過三四十年的發展,加氫精制技術已經相當成熟,目前,它可處理從輕石腦油到常壓渣油等各種原料,可用於產品精製;重整、催化裂化、延遲焦化等等裝置的原料預處理,因此國外普遍稱為加氫處理。
原料油可以是石油原油或其製品,如石腦油等。反應過程放熱,目前工業方法不用催化劑,操作溫度高於700℃。當使用原油時,可採用焦粒流化床加氫反應器,使床溫均勻;原料中不能蒸發的殘渣附著在焦粒上,定期排出。當使用石腦油時,可採用氣體循環加氫反應器,利用噴嘴射出反應物的動能帶動周圍氣體循環,達到與流化床相似的功能。
傳統柴油加氫精制
傳統的柴油加氫精制目的對含硫直餾瓦斯油主要是加氫脫硫,對二次加工瓦斯油主要是改質。
原料油與循環氫和補充氫混合後,經換熱器和加熱爐加熱至反應溫度,進入固定床反應器,在氫壓下發生加氫脫硫、脫氮、脫氧、烯烴飽和、多環芳烴環烷化、脫金屬、烴裂解等各種反應。總反應是放熱的。根據原料情況和加氫深度,催化劑可以是單層或分為幾個床層。對裂化或焦化柴油原料,為調節溫度,催化劑床層間需注入冷油或冷氫.出反應器的生成物經換熱器和冷卻器冷卻後,進高壓分離器閃蒸分出循環氫,經胺洗脫除H多後循環使用;高分液體則進汽提塔除去溶解的H:S和輕質烴後即為成品。
柴油加氫精制時的主要工藝條件為:液時空速1~5每小時,反應溫度32~38攝氏度,反應壓力4.0~6.0MPa,氣油比7.5~200。脫硫率一般在90%左右,產品收率達99.5%以上。反應過程中有少量焦碳沉積,降低了催化劑活性,可通過控制燃燒法再生,這樣催化劑壽命可達5~6年。
汽油加氫裝置的工藝路線
裂解汽油加氫裝置是乙烯裝置的一個配套裝置,該裝置的主要任務是將乙烯裝置的副產品“裂解汽油”進行再處理。裂解汽油中含有工業中重要的化工原料苯、甲苯、二甲苯,同時也含有大量的不飽和烴(雙烯烴、單烯烴)和其它含S, O,N等的烴類化合物。在抽提苯、甲苯、二甲苯時,這些不飽和烴和其它元素化合物的存在對裝置工藝操作有很大的影響。所以在提取三苯前必須對裂解汽油進行加工處理,將其中的不飽和烯烴進行加氫飽和,並將含有其它元素的烴類化合物進行加氫裂解淨化處理。但是裂解汽油中還含有C5及C9等烴類,所以在加氫前,先將裂解汽油中的C5及C9餾分分離,然後對裂解汽油的中心餾分C6-C8進行加氫處理。由於苯、甲苯、二甲苯也屬於不飽和烴,所以加氫反應中所採用的加氫催化劑是選擇性加氫催化劑。
國外汽油加氫技術
裂解汽油是乙烯生產過程中的副產物,其主要餾份為C5-205攝氏度烴類混合物,以各種芳烴居多,含量高達60%-80%。因此,裂解汽油經過加氫後,可進行芳烴抽提,提取其中的苯、甲苯、二甲苯,也可用作車用汽油的調和油。
從加氫處理的餾分來看,裂解汽油加氫可分為全餾分加氫和中心餾分加氫兩種工藝流程。全餾分加氫是對C5~C9的全部餾分進行加氫;中心餾分加氫是預先將裂解汽油中的C5和C9餾分分離出來,僅對C6~C8餾分進行加氫。
國外裂解汽油加氫的技術已十分成熟,廣泛採用的工藝技術有IFP、LUMMUS的DPG、HOUDRY的HPG、UOP、KELLOGG、三菱油化的MHC、BP和BAYER等工藝技術等等。一段加氫反應條件較為緩和,目前較多採用Pd催化劑,其反應溫度可低達50~150攝氏度之間,反應壓力4.1~5.9 MPa。二段加氫反應溫度較高,大多採用Co-Mo催化劑,其反應溫度達280~400攝氏度,反應壓力3.0~5.0 MPa。
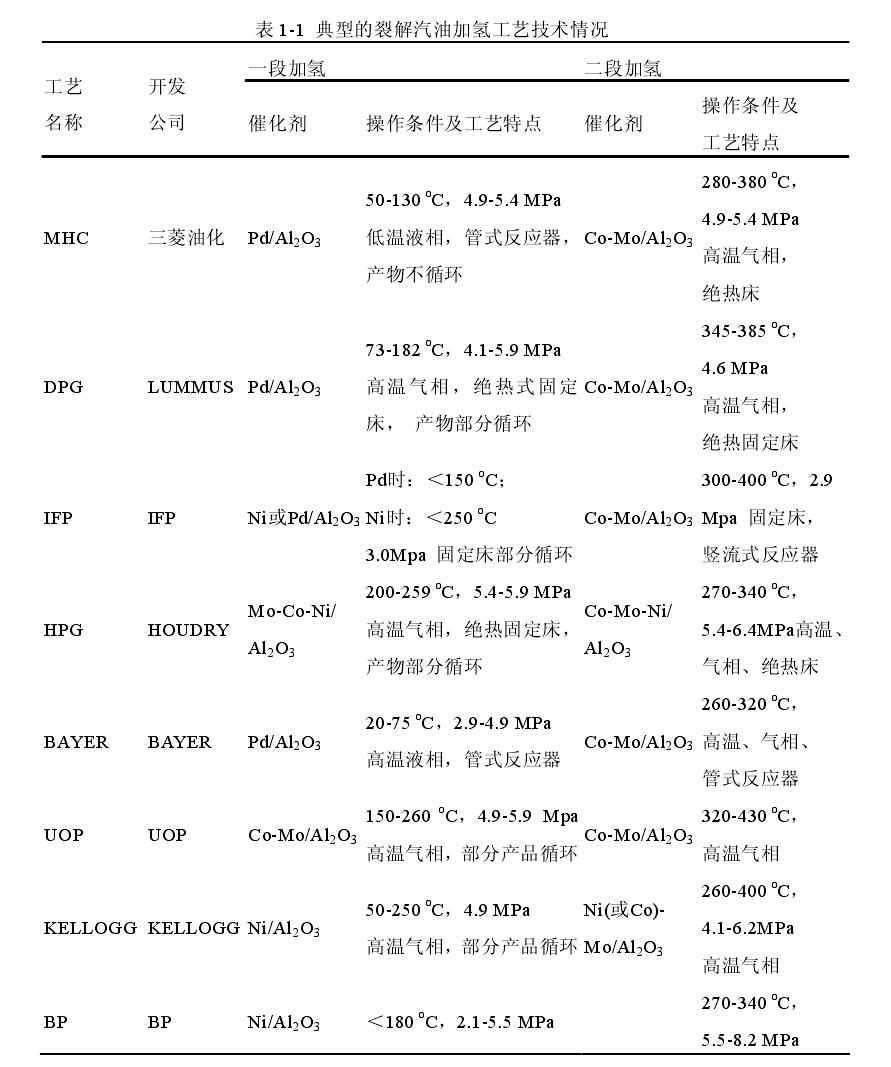
一段加氫反應可以採用
液相反應,也可採用氣相反應。有的採用管式反應器,有的採用絕熱式固定床反應器。二段反應均為高溫氣相反應,除BAYER公司採用管式反應器外(反應溫度相應較低),其餘均採用絕熱式固定床反應器。典型的國外裂解汽油加氫工藝技術的情況見圖。
國內的工藝技術現狀
我國齊魯石化公司、燕山石化公司、揚子石化公司等裝置採用中心餾分加氫,而撫順、新疆等地的工業裝置採用全餾分加氫工藝。中心餾分加氫工藝套用廣泛。該技術的主要內容:先採用普通精餾法脫除裂解汽油的C5、C9餾份,在脫C9前須先進行脫砷處理。分離後的中心餾分C6~C8進行二段加氫。一段低溫液相加氫除去高度不飽和鏈狀共軛烯烴、環狀共軛烯烴及苯乙烯等。二段高溫氣相反應除去含硫、氧、氮的有機雜質,並使單烯烴加氫飽和後用做芳烴抽提原料制出
苯、
甲苯、
二甲苯。部分國內裝置的技術方案見圖。不同工藝流程的分析
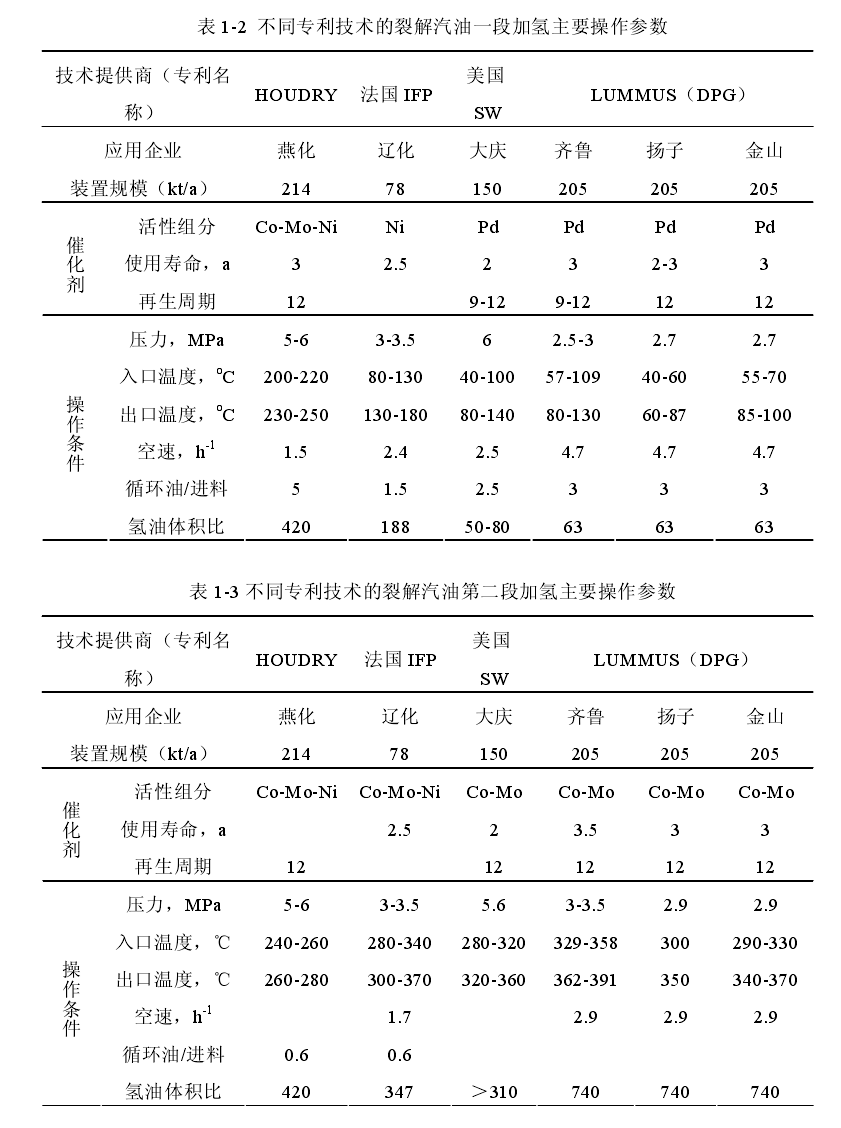
不同工藝技術的比較
目前國內外裂解汽油加氫裝置普遍都採用二段絕熱固定床反應器,第一段採用液相加氫法,第二段採用氣相加氫法。第一段加氫工藝條件比較緩和,主要是雙烯烴、炔烴以及烯基芳烴等高度不飽和烴進行加氫飽和,以穩定裂解汽油的穩定性。裂解汽油第一段加氫的特點是採用絕熱固定床液相加氫,利用循環油來控制反應器的溫升。不同點是當採用Co-Mo-Ni系催化劑時,反應條件較苛刻,反應溫度通常在200-250℃,反應壓力在3.0-3.6Mpa。當採用Pd催化劑時,反應條件緩和,反應溫度可低達30~150攝氏度之間,反應壓力2.7Mpa左右,空速大,能耗低,且操作平穩可靠。第二段加氫反應溫度較高,特點是採用絕熱固定床氣相加氫,採用Co-Mo催化劑,其反應溫度達280~400攝氏度,反應壓力3.0~5.0 MPa。
裂解汽油加氫裝置工藝流程可分為兩類,即中心餾分加氫和全餾分加氫流程。中心餾分加氫裝置從工藝流程上分三大部分:預分餾系統、反應系統及穩定系統。中心餾分加氫工藝流程為裂解汽油先進入脫戊烷塔,切除C5組分,然後進入BTX塔,脫出≥C9組分,得到C6—C8組分。C6—C8餾分再分別進入一段、二段反應器進行加氫精制,脫除雙烯烴、單烯烴給氧、硫、氮等雜質。最後進入穩定系統,在硫化氫汽提塔中脫除H2S氣體後,作為芳烴裝置的原料。
全餾分加氫工藝流程與中心餾分加氫工藝流程相似,主要區別在於,全餾分加氫工藝流程中裂解汽油先經過加氫精制,然後再分餾切割為C餾分、C6—C8中心餾分、C9以上餾分。加氫後的C5餾分可返回乙烯裝置循環裂解,C6—C8中心餾分則作為芳烴抽提原料,而C9以上餾分可作為裂解氣壓縮機沖洗油。
從生產情況看,在裝置運行周期、催化劑抑制結焦等方面,中心餾分加氫工藝好於全餾分加氫工藝。
裂解碳九加氫工藝
根據加氫目的的不同,裂解碳九加氫主要採用兩種絕熱固定床工藝:一種是兩段加氫工藝,類似於裂解汽油兩段加氫工藝;另一種是單段深度加氫工藝,除去易聚合雙烯及最大限度地飽和烯烴。
裂解碳九兩段加氫工藝包括原料預處理、一段加氫、二段加氫、餾程切割等過程。裂解C9-I~C9-III和閃蒸油均存在組分複雜、膠質含量高、毒物含量高或機械雜質多等問題。因此,原料預處理工藝是整個工藝的技術關鍵之一,脫除雜質及一些重組分後,切取一定的餾分來使用。
一段加氫將易生膠的二烯烴轉化為單烯,將鏈烯基芳烴轉為烷基芳烴。燕山石油化工公司採用中國科學院山西煤炭化學研究所鎳基催化劑技術。二段加氫將單烯烴飽和並脫除硫、氮、氧、氯和重金屬等化合物。催化劑採用Co-Mo、Ni-Mo、Ni-Co-Mo等金屬硫化物催化劑,類似於裂解汽油二段加氫精制催化劑。據報導,燕山石油化工公司採用石油化工科學研究院RN-10加氫催化劑或燕山石油化工研究院開發的BY-5加氫精制催化劑作為二段加氫催化劑。餾程切割是在一台填料精餾塔中採用多側線切割技術對加氫產品進行餾分切割。
裂解碳九單段深度加氫工藝[42—43,46—48]亦是採用絕熱固定床法,在較低的入口溫度、液體空速和較低的氫油體積比下,將物料中雙烯值降至0~0.1g I2/100 g,溴價降為12.0~16.0 g Br2/100 g。專利CN1948441A公開了一種裂解碳九鼓泡床加氫工藝。該工藝採用將壓力熱聚後的閃蒸油和連續負壓蒸餾後的精餾碳九相混合,得到一種混合碳九原料。加氫處理採用並流式絕熱鼓泡床反應器,可確保在較低空速下,處理高含量不飽和組分原料時,反應器內氣液分布合理,不產生溝流和局部過熱,抑制了反應過程中聚合生焦反應的發生。
裂解碳九一段選擇加氫工藝和單段深度加氫工藝適合各種碳九原料,均為氣液固三相反應,其中氣相主要是氫氣。提高反應壓力有利於增加液相溶解氫的能力,降低液相反應物向催化劑表面的擴散阻力,反應壓力一般控制在2.0~5.0 MPa。適當降低反應溫度可降低結焦,但催化劑活性也會降低。反應入口溫度主要取決於進口原料的不飽和度,以控制絕熱溫升80~140 ℃為宜。裂解碳九不飽和組分多,加氫難易程度不一,一般控制新鮮油空速在0.5~2.0 h-1。根據裂解碳九原料的不同,適當控制氫烴比、回流比和催化劑床層稀釋比等也是該工藝的重點。二段加氫精制催化劑及工藝與較為成熟的裂解汽油二段加氫精制催化劑及工藝類似。
催化劑的選擇
催化劑的選擇是裂解汽油加氫中核心問題,工業上用的催化劑一般需要滿足以下條件:催化活性高,選擇性好,活性穩定且耐毒,適當的載體和形狀,比表面積要大,表面酸性低,機械強度高,製造容易,價格便宜,易再生,使用壽命長等特點。
未來發展
在現代煉油工業中,加氫處理的工業套用(1950年)雖然起步較晚,但其工業套用的速度和規模都超過了其他煉油技術。由於油品需求結構向輕質化轉變、清潔燃料的推廣套用、含硫原油和重質原油比例的逐年增加、加氫技術的發展和工業套用增長速度越來越快。使得加氫技術的發展和套用進入一個新的階段。毫無疑問,今天的加氫技術已經成為煉油石化工業的支柱技術。