催化裂化提升管反應器,提升管反應器的直徑由進料量確定。
基本介紹
- 中文名:催化裂化提升管反應器
- 特色技術:終止反應技術
- 套用範圍:重油催化裂化
- 性質:反應器
提升管反應器
提升管反應器的作用
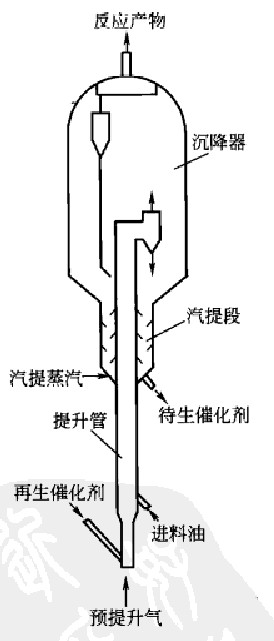
提升管反應過程
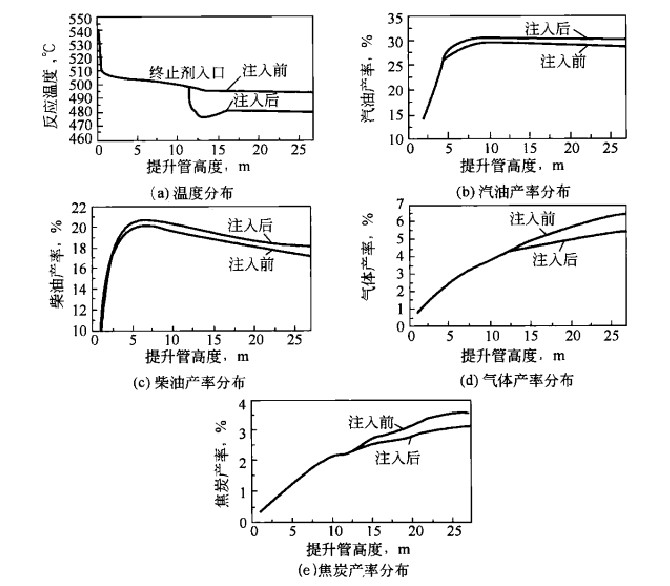
汽提段的作用
提升管反應器的發展
兩段提升管催化裂化技術(TSRFCC)
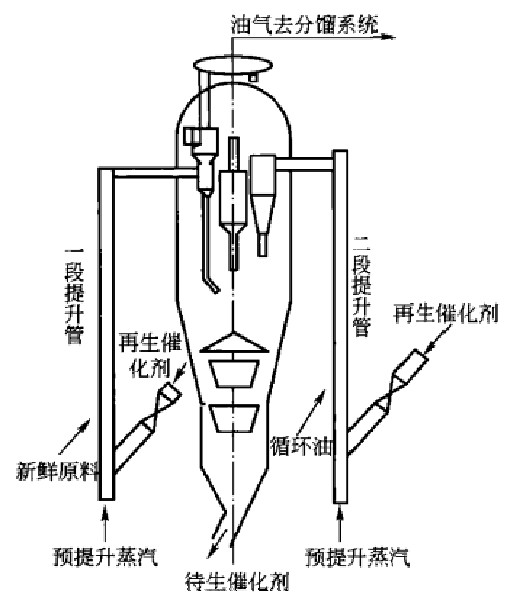
多產異構烷烴催化裂化技術(MIP)
催化裂化汽油輔助反應器改質技術
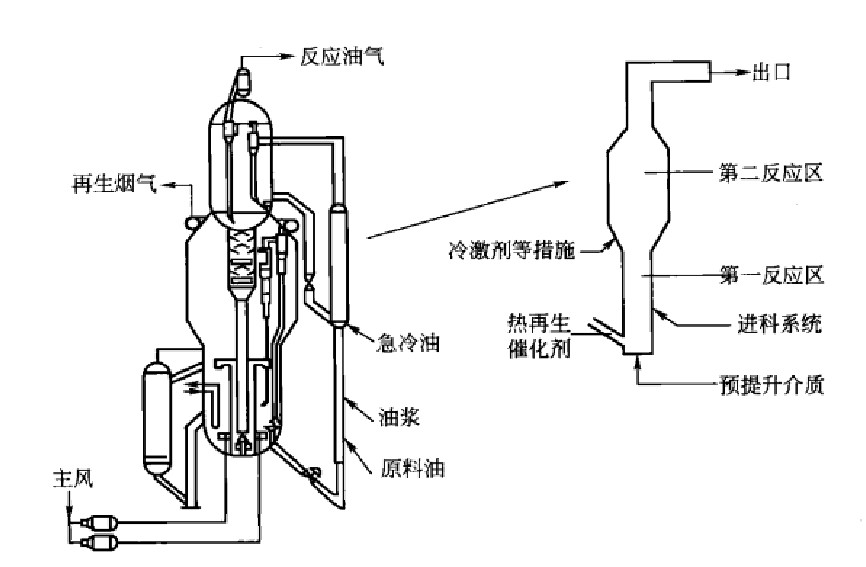
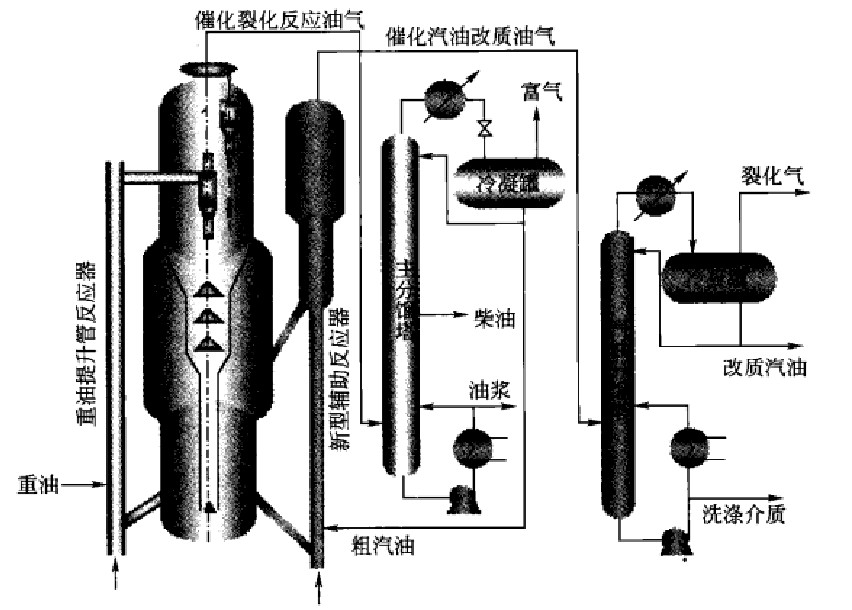
催化裂化提升管反應器,提升管反應器的直徑由進料量確定。
催化裂化提升管反應器,提升管反應器的直徑由進料量確定。...... 催化裂化提升管反應器,提升管反應器的直徑由進料量確定。中文名 催化裂化提升管反應器 特色技術...
主要定義 提升管催化裂化riser 應器的流化催化裂化過程二 catalytic cracking指有提)f-竹反 一般流化催化裂化裝置兩器的排 列位置有兩種:一種是反應器與再生器等...
兩段提升管催化裂化(TSRFCC)新技術是在中石油公司的大力支持下、煉油與銷售分公司的直接領導和組織下與中國石油大學共同開發,經過整個“九五”和“十五”前期,歷時...
催化裂化是石油煉製過程之一,是在熱和催化劑的作用下使重質油發生裂化反應,轉變為裂化氣、汽油和柴油等的過程。...
催化裂化設備 CAt&以st Cracke;石油催化裂化設備指其反應一再生系統。其類型有:床層反應式、提升管式、高低並列式及同軸式等。如提升管反應器,原料油是與霧化...
噴嘴環管反應器是針對催化裂化提升管反應器噴嘴進料混合段催化劑顆粒不均勻分布的現象,提出了一種新型結構的進料混合段,並在內徑為186mm,高14m的大型提升管冷模...
催化裂化工藝過程,一般由三個部分組成,即反應一再生系統、分餾系統、吸收—穩定系統。對處理量較大、反應壓力較高(例如>0.2MPa)的裝置,常常還有再生煙氣的能量...
該工藝是中國石化石油化工科學研究院開發的製取乙烯和丙烯的專利技術,在傳統的催化裂化技術的基礎上,以蠟油、蠟油摻渣油或常壓渣油等重油為原料,採用提升管反應器和...
提升管 riser 在流化催化裂化裝置中,藉助氣體介質(空氣、蒸汽或油氣)的提升力將催化劑提升至高處所用的管子,由下而上依次為預提升段、進料段和裂化反應區,出口...
MIP工藝採用串聯提升管反應器型式的新型反應系統及相應的工藝條件,突破了現有的催化裂化工藝對某些反應的限制,實現了可控制和選擇性進行某些反應,具有如下特點:⑴...
《催化裂化事故分析與預防》是2007年中國石化出版社出版的圖書,作者是中國石化...十九、MIP工藝提升管反應器噎塞故障第二部分 分離系統一、鹼罐爆炸...
催化熱裂解(CPP) 是在傳統催化裂化技術的基礎上,以蠟油、蠟油摻渣油或常壓重油等重油為原料,採用專有催化劑,在提升管反應器以連續反應-再生循環操作方法式,在比...
FCC裝置採用兩段提升管技術及擴能的改造設計重油催化裂化進料霧化噴嘴研究催化裂化裝置旋風分離器設計的有關問題催化裂化裝置反應系統磨損問題及對策...
石油催化裂化發展初期,曾採用移動床反應器,但現已被流化床反應器和提升管反應器所取代。目前,套用移動床反應器的重要化工生產過程有連續重整、二甲苯異構化等催化...
該工藝借鑑流化催化裂化技術,採用催化劑的流化、連續反應和再生技術,已經實現了...DCC-Ⅰ選用較為苛刻的操作條件,在提升管加密相流化床反應器內進行反應,最大量...
目前承擔有國家自然科學基金重大項目子課題“催化裂化提升管反應器的時空多尺度結構研究”、973項目子課題“重油臨氫與非臨氫轉化技術集成過程的化學”,山東省重點科研...
為生產能力提高50%的擴容改造創造了前提條件,2002年獲國家科技進步二等獎;發明了“催化裂化提升管反應器出口三快組合技術”,在煉油企業廣泛推廣套用,分別獲兩項中國...
ARGG:內提升管反應器、反應再生並列式催化裂化裝置。...... ARGG:內提升管反應器、反應再生並列式催化裂化裝置。中文名 ARGG 設計 中國石化工程建設公司 生產 富...
五、重油催化裂化六、中國的重油催化裂化技術第七節 催化裂化主要設備一、提升管反應器二、再生器三、專用設備和特殊閥門四、旋風分離器第八節 反應一再生系統工藝...
第六節 催化裂化工藝流程一、反應?再生系統二、分餾系統三、吸收?穩定系統四、煙氣能量回收系統第七節 催化裂化主要設備一、提升管反應器及沉降器二、再生器...
①採用串聯提升管反應器形式的反應系統,最佳化催化裂化的一次反應和二次反應,從而減少乾氣和焦炭產率,有利於產物分布的改善;②設計兩個反應區,第一反應區以裂化反應...
因此,由中國石化工程建設公司設計的國內第一套年處理蠟油60萬噸的提升管反應、兩器高低並列式的流化催化裂化置於1978年初,在武漢石化廠建成投產。鑒於分子篩催化劑...
許友好,男,現任石油化工科學研究院催化裂化工藝研究室主任工程師。[1] ...成功地設計具有兩個反應區的串聯提升管新型反應器,在國際上首創了全新反應系統的...