產品概述
1、濾塵機制
含塵氣流從下部進入圓筒形
濾袋,在通過濾料的孔隙時,粉塵被濾料阻留下來,透過濾料的清潔氣流由排出口排出。沉積於濾料上的粉塵層,在機械振動的作用下從濾料表面脫落下來,落入灰斗中。
袋式除塵器的濾塵機制包括篩分、慣性碰撞、攔截、擴散、靜電及重力作用等。篩分作用是袋式除塵器的主要濾塵機制之一。當粉塵粒徑大於濾料中纖維間孔隙或濾料上沉積的粉塵間的孔隙時,粉塵即被篩濾下來。通常的織物
濾布,由於纖維間的孔隙遠大於粉塵粒徑,所以剛開始過濾時,篩分作用很小,主要是纖維濾塵機制——慣性碰撞、攔截、擴散和
靜電作用。但是當濾布上逐漸形成了一層粉塵
粘附層後,則碰撞、擴散等作用變得很小,而是主要靠篩分作用。
一般粉塵或濾料可能帶有電荷,當兩者帶有異性電荷時,則靜電吸引作用顯現出來,使濾塵效率提高,但卻使清灰變得困難。不斷有人試驗使濾布或粉塵帶電的方法,強化靜電作用,以便提高對微粒的濾塵效率。重力作用只是對相當大的粒子才起作用。慣性碰撞、攔截及
擴散作用,應隨纖維直徑和濾料的孔隙減小而增大,所以濾料的纖維愈細、愈密實,濾塵效果愈好。
2、濾塵效率
在各種
除塵裝置中,
袋式除塵器是濾塵效率很高的一種,幾乎在各種情況下,濾塵效率都可以達到99%以上。如設計、製造、安裝運行得當,特別是維護管理適當,則不難使其除塵效率達到99.9%。在許多情況下,袋式除塵器的
排塵濃度可以達到每立方米數十毫克,甚至0.1mg/m3以下。因此,有時可以將袋式除塵器排氣送回車間內部循環使用,節省了為補給空氣加熱或冷卻的能耗和費用。當然,在設計、選用不當或操作管理不善的情況下,袋式除塵器的排塵濃度也會達到很高數值。
影響濾塵因素
濾料的結構及粉塵層厚度
袋式除塵器採用的濾料可以是織物(素布或起絨的絨布),也可以是輥壓或針刺的氈子。不同結構的濾料,濾塵過程不同,對濾塵效率的影響也不同。素布中的孔隙存在於經、緯線以及纖維之間,後者占全部孔隙的30%~50%。開始濾塵時,大部分氣流從線間網孔通過,只有少部分穿過纖維間的孔隙。其後,由於粗塵粒嵌進線間的網孔,強制通過纖維間的氣流逐漸增多,使慣性碰撞和攔截作用逐步增強。由於
粘附力的作用,在經、緯線的網孔之間產生了粉塵
架橋現象,很快在
濾料表面形成了一層所謂粉塵初次
粘附層(簡稱粉塵初層)。由於粉塵粒徑一般都比纖維直徑小,所以在粉塵初層表面的篩分作用也強烈增強。這樣一來,由於
濾布表麵粉塵初層及隨後在其上逐漸沉積的粉塵層的濾塵作用,使濾布成為對粗、細粉塵皆是有效的過濾材料,濾塵效率顯著提高。
絨布是素布通過起絨機拉刮成具有絨毛的織物。開始濾塵時,塵粒首先被多孔的絨毛層所捕獲,經、緯線大都起一種受力的支撐作用。隨後,很快在絨毛層上形成一層強度較高且較厚的多孔粉塵層。由於絨布的容塵量比素布大,所以濾塵效率比素布高。氈子是由單纖維雜亂堆積的、較厚實的多孔性濾料,在一定程度上具有內部式過濾器的特點。不但氈本身具有一定的濾塵能力,而且
容塵量大,所以即使其表面不形成粉塵層,也能保證有較高的濾塵效率。
可見,
袋式除塵器的濾塵效率高,主要是靠濾料上形成的粉塵層的作用,
濾布則主要起著形成粉塵層和支撐它的骨架的作用。正是由於袋式除塵器是把沉積在濾料表面上的粉塵層作為
過濾層的一種過濾式
除塵裝置,所以為控制一定的
壓力損失而進行清灰時,應保留住粉塵初層,而不應清灰過度,乃至引起效率顯著下降,
濾料損傷加快。
過濾速度
過濾速度V(或比負荷qf)是代表袋式除塵器處理氣體能力的重要
技術經濟指標。過濾速度的選擇要考慮經濟性和對濾塵效率的要求等各方面因素。從經濟方面考慮,選用的過濾速度高時,處理相同流量的含塵氣體所需的濾料面積小,則
除塵器的體積、占地面積、耗鋼量亦小,因而投資小,但除塵器的
壓力損失、耗電量、濾料損傷增加,因而運行費用高。從
濾塵效率方面看,過濾速度大小的影響是很顯著的。一些實驗表明,過濾速度增大1倍,粉塵通過率可能增大2倍甚至4倍以上。所以通常總是希望過濾速度選得低一些。實用中織物
濾布的過濾速度為0.5~2m/min,毛氈濾料為1~5m/min。從經濟性和高效率兩方面看,這一
濾速範圍是最適宜的。當
過濾速度提高時,將加劇塵粒以三條途徑對濾料的穿透,即直通、壓出和氣孔,因而降低除塵效率。
上面所述的濾塵效率隨過濾速度增大而顯著降低的特性,是不能用纖維過濾理論來解釋的。從纖維過濾理論來看,當以慣性碰撞為主要捕集機制時,捕集效率應隨過濾速度增大而提高;只有在以擴散為主要捕集機制時,捕集效率才會隨速度減小而提高,但
擴散作用對粒徑為0.2μm左右以上的粒子是不重要的,而實際要捕獲的粒徑要比這大得
粉塵特性
在粉塵特性中,影響
袋式除塵器除塵效率的主要是粉塵顆粒。對於0.1μm的塵粒,其分級除塵效率可達95%。對鍋爐飛灰的分級除塵效率。對於大於1μm的塵粒,可以穩定地獲得99%以上的除塵效率。在大小不等的塵粒中,以粒徑0.2~0.4μm塵粒的分級效率最低,無論清潔濾料或積塵後的濾料皆大致相同。這是由於這一粒徑範圍的塵粒處於幾種除塵效率低值的區域所致。
塵粒攜帶的
靜電荷也影響
除塵效率,粉塵
荷電越多,除塵效率就越高。現已利用這一特性,在濾料上游使塵粒荷電,從而對1.6μm塵粒的捕集效率達至99.99%。
清灰方式
袋式除塵器濾料的清灰方式也是影響其濾塵效率的重要因素。如前所述,濾料剛清灰後的濾塵效率是最低的,隨著過濾時間(即粉塵層厚度)的增長,效率迅速上升。當粉塵層厚度進一步增加時,效率保持在幾乎恆定的高水平上。清灰方式不同,清灰時逸散粉塵量不同,清灰後殘留粉塵量也不同,因而
除塵器排塵濃度不同。例如,機械振動清灰後的排塵濃度,要比脈衝噴吹清灰後的低一些;以直接脈衝(壓縮空氣直接向
濾袋噴吹)和阻尼脈衝(在清灰系統中有一裝置,當電磁閥關閉後可使濾袋內的壓力逐漸降低)相比較(兩者的壓力上升率和最大逆壓均相同),前者的排塵濃度約為後者的幾倍。這是因為在直接脈衝的情況下,噴吹後濾袋急劇地收縮,過濾氣流和濾袋的加速一起作用,使噴吹後振鬆了的粉塵穿透增多。阻尼脈衝噴吹後
濾料上殘留粉塵較多,因而其
濾層阻力比直接脈衝高。此外,對於同一清灰方式,如機械振動清灰方式,在
振動頻率不變時,振幅增大將使排塵濃度顯著增大;但改變頻率、振幅不變時,排塵濃度卻基本不變。實際套用的
袋式除塵器的排塵濃度取決於同時清灰的
濾袋占濾袋總數的比例,氣流在全部濾袋中的分配以及清灰參數等的影響。
袋式除塵器的壓力損失(設備阻力)不但決定著它的能耗,還決定著除塵效率和清灰的時間間隔。袋式除塵器的壓力損失與它的結構形式、濾料特性、
過濾速度、
粉塵濃度、清灰方式、氣體溫度及氣體黏度等因素有關。
△p0——清潔濾料的阻力,Pa;
△Pd——濾料上附著粉塵的阻力,Pa。
(1)除塵器結構阻力 是指氣體通過入口、出口以及除塵器內部的擋板、
引射器等產生的阻力。正常情況下,這部分阻力一般為200~500Pa(20~50mmH2O);
(2)清潔濾料的阻力(△p0) 是指濾料未附著粉塵時的阻力。該項阻力較小.
(1)袋式除塵器的壓力損失在很大程度上取決於選定的過濾風速。
除塵器結構阻力、清潔濾料的阻力及濾料上附著粉塵層的阻力都隨過濾風速的提高而增加。
(2)粉塵堆積負荷(m)對積塵濾料的阻力有決定性的影響。除直接關係著△Pd的大小外。
(3)濾料的特性。不同結構濾料的阻力通常有如下關係:長
纖維濾料高於短纖維濾料;不起絨濾料高於起絨濾料;紡織濾料高於氈類濾料;布料較重的濾料高於較輕的濾料。
(4)過濾時間。工作過程中
袋式除塵器的阻力不是定值,而是隨時間變化的。
隨著過濾的進行,濾料上附著的粉塵層逐漸增厚,透光性降低,阻力便相應增加。這將使風機工作風量減小,粉塵穿透量增大,並可能抽去濾料縫隙間的沉積粉塵,使除塵效率降低。此時便需清灰,以便將阻力控制在一定範圍之內。因而,設備阻力的變化實際如圖6—26所示。對於分室的袋式除塵器,常用逐室中斷過濾進行清灰的方法。此時,總抽風量稍有下降,設備阻力亦略有增加。當清灰結束重新恢復濾塵時,由於清灰濾室的阻力已下降,所以袋式除塵器總風量將增加,設備阻力將下降。
實際上,濾料清灰後其阻力只能降低到清灰前的20%~80%,而不能恢復到新濾料狀態,這是因為濾料上含殘存初次粉塵層。而且殘存初次粉塵層的量會隨使用時間推移而增加。一般情況是,
袋式除塵器的
壓力損失在剛使用時增加較快,但經1~2個月便趨穩定,以後雖有增加但比較緩慢,多數趨於定值。
(5)清灰方式。在同樣條件下,採用高能量清灰方式(如脈衝噴吹、氣環反吹等)的設備阻力較低,而採用低能量清灰方式(如機械振動、逆氣流等)的設備阻力較高,這是由於清灰後濾料與剩餘粉塵量不同所致。
選型因素
1.處理風量
袋式除塵器的處理風量必須滿足系統設計風量的要求,並考慮管道
漏風係數。系統風量波動時,應按最高風量選用袋式除塵器。
高溫煙氣中應按
煙氣溫度折算到工況風量來選用袋式除塵器。
2.使用溫度
袋式除塵器的使用溫度受以下兩個條件的制約。
(1)濾料材質所允許的長期使用溫度和短期最高使用溫度,一般應按長期使用溫度採取。
(2)為防止
結露,煙氣溫度所允許的最低限度,一般應保持
除塵器內的煙氣溫度高於露點15~20℃。
對於高溫塵源,必須將含塵
氣體冷卻至濾料能承受的溫度以下。在高溫煙氣中往往含有大量水分子和SOx,鑒於SOx的
酸露點較高,這時確定
袋式除塵器的使用溫度時,應予特別的注意。
在淨化溫度接近露點的高溫氣體時,應以間接加熱或混入高溫氣體等方法降低氣體的相對濕度,以防結露,影響袋式除塵器的使用。
3.氣體的組成
在考慮被處理氣體中含有可燃性、腐蝕性以及有
毒性氣體時,必須掌握氣體的化學成分。而一般情況下,則可按照處理空氣來選用袋式除塵器。
對於腐蝕性氣體,如氧化硫、氯及
氯化氫、氟及
氟化氫、磷酸氣體等,需根據腐蝕氣體的種類選擇濾料、殼體材質及防腐方法等。
4.煙氣含塵濃度
煙氣的入口含塵濃度對袋式除塵器的
壓力損失和清灰周期、濾料和箱體的磨損及排灰裝置的能力等均有較大影響,濃度過大時應設預除塵。
5.粉塵特性
(1)附著性和凝聚性 這一屬性對袋式除塵器的清灰效果和除塵效果有較大影響。
(2)
粒徑分布 粉塵中的細微部分對於
袋式除塵器的除塵效果和壓力損失影響較突出;而在入口含塵濃度高和粉塵硬度大時,粗顆粒粉塵對濾料和殼體等的磨損影響較顯著。
(3)粒子形狀 通常在過濾特殊形狀的粉塵時,才考慮此因素。例如纖維性粉塵,因容易凝聚成絮狀物而難以被清離
濾袋,因而袋式除塵器應採用外濾式,適當降低過濾風速,並採用特殊清灰措施。
(4)粒子的密度 粉塵假密度越小,清灰便越困難,因而必須適當降低過濾風速。此外,假密度直接影響卸灰裝置的能力。
(5)
吸濕性和
潮解性 具有較強吸濕性和潮解性的粉塵,極易在濾袋錶面吸濕而固化或潮解成稠狀物,致使
袋式除塵器壓力損失增大而不能工作。在過濾這些粉塵時,必須採取包括加熱保溫在內的措施。
(6)磨啄性 磨啄性強的粉塵系指硬度高且粒度粗的粉塵,它們容易磨損濾袋和殼體等,應設法防止或減輕其危害。
(7)帶電性 容易帶電的粉塵常使清灰困難,因而選擇過濾風速必須適當。若粉塵可能因靜電發生的火花而引起爆炸,則應採取防靜電措施。
(8)爆炸性、可燃性 爆炸性粉塵應採取防爆防火措施。
6.設備阻力
每一類袋式除塵器都有其一定的阻力範圍。但選用時可能需根據風機能力等因素做適當的變動。此時應對過濾風速、清灰周期做相應的調整。
7.工作壓力
一般情況下,要求
袋式除塵器的耐壓度為3000~5000Pa(約300~500mmH2O),當採用
羅茨鼓風機為動力時,要求耐壓度為15000~50000Pa(約1500~5000mmH2O),在少數場合(例如
高爐煤氣淨化),要求的耐壓度超過105Pa。
8.工作環境
室外安裝袋式除塵器時,應考慮相應的電氣系統及採取防雨措施。
袋式除塵器設在有腐蝕性的氣體或粉塵的環境中,或者在海岸近旁或船上,則應仔細選擇
除塵器的結構材質和
防腐塗層。
袋式除塵器用於寒冷地帶,若以
壓縮空氣清灰或採用
氣缸驅動的
切換閥時,必須防止壓縮空氣中的水分凍結,以免運轉失靈。
濾料是袋式除塵器的主要組成部分之一,袋式除塵器的性能在很大程度上取決於
濾料的性能。濾料的性能,主要指
過濾效率、
透氣性和強度等,這些都與濾料材質和結構有關。根據袋式除塵器的除塵原理和粉塵特性,對濾料提出如下要求。
(1)
容塵量大,清灰後能保留一定的永久性容塵,以保持較高的過濾效率;
(3)抗皺摺、耐磨、耐溫和耐腐蝕性好,機械強度高;
(5)使用壽命長,成本低。
這些要求,有些取決於纖維的理化性質,有些取決於濾料的結構。一般濾料很難同時滿足所有要求,要根據具體使用條件來選擇合適的濾料。
袋式除塵器採用的濾料種類較多,按濾料的材質分,有
天然纖維、無機纖維和合成纖維等。隨著合成纖維工業的發展,不斷出現一些價廉、耐用的新型濾料。就纖維而言,有長纖維和短纖維兩種。長纖維織物的表面絨毛少,粉塵層壓力損失高,但容易清灰;一般短纖維織物表面有絨毛,濾塵性能好,壓力損失低,但清灰時稍為困難。按濾料的結構分,有
濾布(素布和絨布)和
毛氈兩類。按濾布的織法分,有
平紋布、
斜紋布和
緞紋布三種。其中斜紋布的綜合性能較好,
過濾效率和清灰效果都能滿足要求,柔軟性好,
透氣性比平紋布好,但強度比平紋布稍差。
(1)棉布 是價格最低的一種,通常只能用於80℃以下,溫度高時強度急劇降低,耐酸差,對小於10μm粉塵的過濾效率低,一般較少採用。
(2)毛織
濾布(呢料) 通常用羊毛織成
絨布,比
棉布厚,纖維比
棉纖維細。它的透氣性好,阻力小,
容塵量大,過濾效率高,易於清灰,耐酸、鹼性好,但只能用於90℃以下,價格比棉布或合成纖維濾布高得多。
(3)
柞蠶絲布(平綢) 表面平滑,易清灰,透氣性好,但容塵量小,
濾速大時效率低。
主要指玻璃纖維濾布,具有過濾性能好,阻力小,
化學穩定性好,耐高溫,不吸濕和價格便宜等優點。
中鹼玻璃纖維圓筒形濾布,廣泛地用於水泥、冶煉、炭黑和農藥等工業的氣體淨化中。玻璃纖維濾布的過濾效率低於天然、合成纖維濾料。玻璃纖維不耐磨,不抗折,易斷裂。為改善其性能,可用芳香基
有機矽、
聚四氟乙烯、
石墨等方法處理。處理後能提高耐磨、疏水、抗酸和柔軟性,表面光滑易於清灰,延長使用壽命。
合成纖維濾料發展很快,並有可能取代
天然纖維濾料。當前使用較多的有聚醯胺(
尼龍、錦綸)、聚酯(
滌綸)、
聚丙烯腈(腈綸、奧綸)、聚氯乙烯(
維尼綸)、聚四氟乙烯等。我國生產的“208”工業滌綸絨布,具有過濾能力大、效率高、阻力小、強度高等優點,可耐溫130℃,大量用於各種
袋式除塵器中。合成纖維還可以與棉、
毛纖維混合織布,例如我國生產的“尼毛特2號”及“尼棉特4號”,經線用維尼綸線,耐磨性好,緯線用毛線或
棉線,直接織成無縫的圓筒形
斜紋布,過濾性能和
透氣性好。
有
滾壓的毛氈,混以合成纖維後製成的過濾細毛氈及針刺氈等。毛氈濾料的濾塵效率高,可以採用高速過濾。在空隙率相同的條件下,其平均濾速比其他織物大2~3倍。但耐磨、彎折性差。毛氈的表面結構鬆散,粉塵可深入到內部,故難於清灰,僅適用於採用強力清灰方式的除塵器中。為此,可對毛氈進行各種表面加工處理,如熔合、樹脂化或受控熱處理(加熱壓縮),以改善毛氈的捕集性能和清灰性能。毛氈的價格比織物高,因而適宜於大型裝置使用,而織物則適宜於小型裝置使用。
結構形式
除塵器的進氣口布置有上進氣和下進氣兩種方式(見圖6—29)。用得較多的是下進氣方式,它具有氣流穩定、
濾袋安裝調節容易等優點,但氣流方向與粉塵下落方向相反,清灰後會使細粉塵重新積附於濾袋上,清灰效果變差,
壓力損失增大。上進氣形式可以避免上述缺點,但由於增設了上花板和上部進氣分配室,使除塵器高度增大,濾袋安裝調節較複雜,上花板易積灰。
按除塵器內氣體壓力分,有正壓式和負壓式兩類。正壓式(又稱壓入式)除塵器內部氣體壓力高於大氣壓力,一般設在通風機出風段;反之為吸入式。正壓式
袋式除塵器的特點是外殼結構簡單、輕便,嚴密性要求不高,甚至在處理常溫無毒氣體時可以完全敞開,只需保護
濾袋不受風吹雨淋即可,且布置緊湊,維修方便,但風機易受磨損。負壓式袋式除塵器的突出優點是可使風機免受粉塵的磨損,但對外殼的結構強度和嚴密性要求高。
袋式除塵器的形式多種多樣。從濾袋斷面形狀上分,有圓筒形和扁平形濾袋兩種。圓袋套用較廣,直徑一般為120~300mm,最大不超過600mm,濾袋長度一般為2~6m,有的長達12m以上。徑長比一般為16—40,其取值與清灰方式有關。對於大中型
袋式除塵器,一般都分成若干室,每室袋數少則8~15隻,多達200隻,每台
除塵器的室數,少則3~4室,多達16室以上。
按含塵氣流通過濾袋的方向分,有內濾式和外濾式兩類。內濾式系指含塵氣流先進入
濾袋內部,粉塵被阻留在袋內側,淨氣透過
濾料逸到袋外側排出;反之,為外濾式。外濾式的濾袋內部通常設有支撐骨架(袋籠),濾袋易磨損,維修困難。
袋式除塵器的效率、
壓力損失、
濾速及濾袋壽命等皆與清灰方式有關,故實際中多數按清灰方式對袋式除塵器進行分類和命名。
(1)簡易清灰式;
(3)逆氣流清灰式;
(4)逆氣流機械振動並用式;
(5)氣環反吹風式;
(6)脈衝噴吹式。
機械振動式、逆氣流清灰式和逆氣流機械振動式,皆屬於間歇清灰方式,即除塵器被分隔成若干個室,清灰時逐室切斷氣路,順次對各室進行清灰。這種間歇清灰方式沒有伴隨清灰而產生的粉塵外逸現象,可獲得較高的除塵效率。
氣環反吹式和脈衝噴吹式,是連續清灰方式,清灰時不切斷氣路,連續不斷地對
濾袋的一部分進行清灰。這種連續清灰方式,由於其
壓力損失穩定,適於處理含塵濃度高的氣體。
袋式除塵器的結構
根據上述按清灰方式進行分類和命名的方法,介紹幾種常用的
袋式除塵器的結構形式和性能。氣環反吹袋式除塵器雖具有過濾風速高、清灰能力強的特點,適於淨化含塵濃度高和較潮濕的氣體,但由於對
濾袋磨損快,氣環箱及其傳動構件易發生故障,較少採用,所以此處不予介紹。
(一)簡易清灰袋式除塵器
簡易清灰袋式除塵器包括各種的簡易清灰方法,有靠濾料表面沉積粉塵層自重自行脫落的,有人工拍打的,有設手工搖動機構的,也有利用空氣振動的。圖6—31所示為簡易袋式除塵器的兩種形式,其中(a)為上進氣的,(b)為下進氣的,皆為正壓、內濾式結構,淨氣由百葉窗或風帽排出,清灰靠粉塵層自重脫落及人工定期拍
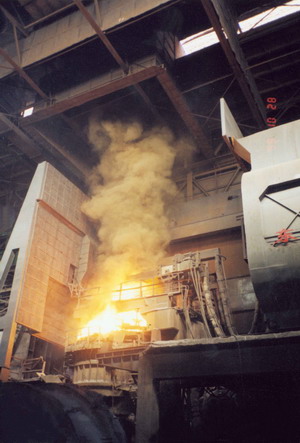
簡易清灰
袋式除塵器的過濾風速,比其他形式都低,一般採用0.15~0.6m/min,當用棉布,絨布濾料時取0.15~0.3m/min,採用毛呢
濾布時取0.3~0.6m/min。壓力損失控制在600~1000Pa以下,設計、使用得好時,除塵效率可達99%。
濾袋直徑一般取100~400mm,長度取2~6m,濾袋間距取40~80mm,各濾袋組之間留有寬度不小於800mm的檢修通道。
簡易清灰袋式除塵器的特點是結構簡單、安裝操作方便、投資省、對
濾料要求不高、維修量小、濾袋壽命長。主要缺點是由於過濾風速小,使得
除塵器體積龐大,占地面積大,正壓下運行時,人工清灰的工作環境差。
這種除塵器是利用
機械傳動使
濾袋振動,致使沉積在濾袋上的粉塵層落入灰斗中。圖6—32示出三種不同的振動方式,其中圖6—32(a)是濾袋沿垂直方向振動的方式,既可採用定期提升濾袋的吊掛框架的辦法,也可利用
偏心輪振打框架的方式;圖6—32(b)是濾袋沿水平方向振動的方式,可分為上部擺動和腰部擺動兩種,圖6—32(c)是扭轉一定角度,使袋上的粉塵層破碎而落入灰斗中。
利用偏心輪垂直振動清灰的袋式除塵器(見圖6—18)具有構造簡單、清灰效果好、清灰耗電小等特點,它適用於含塵濃度不大、間歇性塵源的除塵。當採用多室結構,設閥門控制氣路開閉時,也可用於連續性塵源的除塵。
機械振動清灰
袋式除塵器的過濾風速一般取0.6~1.6m/min,
壓力損失約為800~1200Pa。
(三)逆氣流清灰袋式除塵器
逆氣流清灰系指清灰時的氣流方向與正常過濾時相反,其形式有反吹風和反吸風兩種。實質上氣環反吹風式和脈衝噴吹式也屬於逆氣流清灰類型。
現以反吸風清灰方式為例來說明逆氣流清灰的原理。如圖6—33所示,逆氣流清灰袋式除塵器通常被分隔成若干個室,每個室都有單獨的灰斗及含塵氣體進口管、清潔氣體出口管和反吸風管,並分別與進氣總管、淨氣總管和反吸風總管相連。淨氣管中設有
切換閥(
一次閥)、反吸風管中設有逆氣流閥(二次閥)。圖6—33(a)為正常過濾狀態,一次閥開啟,二次閥關閉。根據預定的周期(定時控制)或
除塵器壓力損失達到預定值(定壓控制)需要清灰時,控制儀發出指令,清灰機構開始動作,一次閥閉,二次閥開[見圖6—33(b)]。由於除塵器內是負壓狀態,所以空氣從反吸風管吸入,從
濾袋外側透過濾袋進入內側,使濾袋變形(呈星形),沉積在濾袋內表面的粉塵層破壞、脫落。清灰結束後,兩閥皆關閉[見圖6—33(c)],處於無風狀態,使濾袋內懸浮的粉塵自然沉降。一定時間後重新恢復過濾狀態[見圖6—33(a)],再轉為下一個過濾室清灰。一般將這種具有圖6—33(a)、圖6—33(b)、圖6—33(c)三個動作的清灰方式稱為“三狀態”方式,將只有圖6—33(a)、圖6—33(b)兩個動作[無圖6—33(c)的動作]的稱為“二狀態”方式。“三狀態”方式可以避免逆氣流清灰後粉塵即刻又被吸附到濾袋上,使清灰效果變差。
為了加強清灰的效果,可以將兩種清灰方式同時採用。例如機械振打加反吹風,它的結構如圖6—34所示。
濾袋皆是掛在支撐吊架5上,振打機構可以使支撐吊架提升起來上下振動。在正常過濾時,含塵氣體由進氣管1進入
除塵器,經分配管2分配到各組濾袋9內,淨氣通過一次閥門7由總管8排出。清灰是逐室進行的,當某室的一組濾袋需要清灰時,啟動該室上部提升振打機構,同時關閉
一次閥7,打開反吹風閥6,在機械振打和反吹風的同時作用下,實現了清灰。
脈衝噴吹袋式除塵器(見圖6—35)的濾塵過程大致為:含塵氣體由下錐體引入脈衝噴吹袋式除塵器,粉塵阻留在
濾袋外表面上,透過濾袋的淨氣經文丘里管進入上箱體,從
出氣管排出。清灰過程是:由控制儀定期順序觸發各
排氣閥,使
脈衝閥背壓室與大氣相通(泄氣),脈衝閥開啟,則氣包中的
壓縮空氣通過脈衝閥經噴吹管上的小孔噴出(一次風),通過
文丘里管誘導數倍(約一次風的5~7倍)周圍空氣(
二次風)吹進濾袋,造成濾袋急劇膨脹振動,加之氣流的反方向作用,使積附在
濾袋外表面上的粉塵層脫落。這種清灰方法具有脈衝的特徵,因此叫做脈衝式
除塵器。壓縮空氣的噴吹壓力為500~700kPa,脈衝時間(或噴吹時間)為0.1~0.2s,
脈衝周期(噴吹周期)一般為60~180s。
脈衝噴吹系統由控制儀、控制閥、脈衝閥、噴吹管及壓縮空氣包等組成。
脈衝閥是控制系統的執行機構,其結構如圖6—36所示。脈衝閥的A室接氣包,B室接噴吹管,C室(
背壓室)接
控制閥。由
波紋膜片3將A、B、C室隔開,A、C室由節流孔5溝通,彈簧4壓著波紋膜片擋住噴吹口6。脈衝閥的工作原理是:當控制儀無信號發來時,控制閥和脈衝閥皆處於封閉狀態,A、C兩室氣壓相等。由於波紋膜片3在C室的受壓面積大於在A室的受壓面積,加上復位彈簧4的壓力,使波紋膜片封住噴吹口6。當控制儀發來信號時,控制閥和C室與大氣相通而迅速泄壓,A室壓力大於C室壓力,波紋膜片3移向C室,打開噴吹口,
壓縮空氣從氣包經A室和B室通過噴吹管噴向
濾袋。信號消失後,控制閥關閉,C室停止排氣,重新充氣並回升至氣源的壓力,膜片重新封閉噴吹口,
脈衝閥關閉,噴吹即行停止。每個脈衝閥接一根噴吹管,其上有六個對準
文丘里管軸線的噴吹孔,同時噴吹六隻濾袋。
脈衝控制儀是向
控制閥發出
脈衝信號的裝置。通過脈衝控制儀可以調節噴吹周期和噴吹時間,因此控制儀是
脈衝噴吹袋式除塵器的關鍵設備,它直接影響著
除塵器的清灰效果和正常工作。脈衝控制儀主要有無觸點電動脈衝控制儀(即電控)、氣動脈衝控制儀(即氣控)和機械脈衝控制儀(即機控)三種。從使用情況看,以無觸點電動脈衝控制儀居多。
以上三種控制儀都是採用定時控制清灰方式,即固定噴吹周期,定時噴吹清灰。這種方式雖比人工控制清灰方式優越,但由於在實際運行中除塵器進口含塵濃度、過濾風速、噴吹壓力等因素都會隨時間而產生波動,因此當採用定時控制時,除塵器的實際阻力往往不同於設計的阻力(即預定的阻力)。實際阻力高於設計阻力時,除塵系統的風量會因此而降低,不但影響除塵效果,而且還會影響吸塵罩的吸塵效果;實際阻力低於設計阻力時,會造成
除塵器阻力尚未達到設計阻力就過早地進行噴吹清灰。噴吹清灰次數過多不但使
壓縮空氣消耗量增加,而且會使除塵效率下降,影響
濾袋和
波紋膜片的壽命。
為了克服這種現象,採用定阻力控制的清灰方式,如AL-3型電控儀,即把除塵器的設計阻力作為控制儀的工作點,使噴吹周期隨除塵器阻力的變化而改變。定阻力控制清灰方式能避免定時控制清灰方式存在的缺點,因而這種方式更為合理。
脈衝噴吹袋式除塵器噴吹清灰用的壓縮空氣消耗量主要取決於噴吹壓力、噴吹周期、噴吹時間以及脈衝閥數量等因素,因此,壓縮空氣消耗量可按下式計算:
(6—31)
T——噴吹周期,min;
a——附加係數(包括管道漏氣損失),一般取1.2;
q——每個脈衝閥噴吹一次的耗氣量,m3。當噴吹壓力為(5—7)×105Pa、噴吹時間為0.1~0.2s時,每個脈衝閥噴吹一次的耗氣量為0.01~0.034m3,計算耗氣量時可取0.022m3。
在通常的
脈衝袋式除塵器中,為了達到必需的清灰效果,噴吹壓力要求達到(5~7)×105Pa,這樣不僅需要消耗過多的能量,同時一般工廠企業的壓縮空氣管網往往達不到這么高的壓力,配置專門的
空壓機,又會增加設備投資和維護工作量。因此對降低噴吹壓力進行了研究,提出以下兩種方法。
(1)用直通
脈衝閥代替直角脈衝閥(見圖6—37) 它與直角形(壓氣進口和出口成90°角)單膜片或雙膜片脈衝閥相比,阻力大大減小,噴吹壓力可降低約50kPa,在高壓力時
過濾速度可提高約10%。
(2)採用低壓噴吹系統 主要採取以下措施來降低噴吹壓力:採用直通脈衝閥;適當加大噴吹管直徑;用特製的噴嘴代替噴吹孔。試驗結果表明,在同一噴吹時間下,噴吹壓力為3×105Pa時的
壓縮空氣噴吹量,與採用直角脈衝閥的
脈衝噴吹袋式除塵器在6×105Pa時的噴吹量相同,即噴吹壓力可降低1/2。由於噴吹壓力降低,膜片的壽命可延長,維修的工作量可減少。
20世紀70年代末我國從德國引進一種環隙噴吹
脈衝袋式除塵器,它採用環隙式引射管進行脈衝噴吹清灰,如圖6—38所示,由帶有連線套管及環形通道的上體和起噴射管作用的下體組成。上下體之間有一狹窄的環形縫隙。各引射管之間藉助於快速拆卸的插接管與壓縮空氣分配管相連線,
濾袋及其套框共同嵌吊在環隙式引射管上。這種環隙噴吹結構,安裝和維護簡單、方便、可靠,與普通的噴孔——
文丘里管式脈衝袋式除塵器相比,噴吹清灰效果好,可提高過濾風速66%以上。但
壓縮空氣多耗25%左右。此外,
脈衝閥採用雙膜片結構,提高了可靠性和抗干擾能力。
另外,脈衝袋式除塵器還有順噴、對噴等結構形式,在此不一一列舉。
扁袋除塵器除了圖6—38所示的楔形扁袋形式外,還有迴轉反吹扁袋除塵器,如圖6—39所示。這種除塵器外殼為圓筒形,扁袋呈輻射形布置在圓筒內,根據所需的過濾面積,
濾袋可以布置成1圈、2圈甚至4圈。濾袋斷面呈梯形,長邊為320mm,兩短邊分別為40mm和80mm,袋長為3~6m。
含塵氣體沿簡體切向引入,靠離心力作用使粗塵分離,然後進入濾袋過濾(為外濾式的),淨氣由上箱體引出。濾袋清灰採用迴轉臂反吹風方式,反吹風量約占過濾風量的15%左右,反
吹風機風壓約為5kPa左右,迴轉臂靠裝在除塵器頂蓋上的電動機和減速器帶動。這種除塵器具有以下特點。
(2)除塵器自帶反吹風機,不受使用場合壓縮空氣源限制,易損部件少,反吹風作用距離大,可採用長濾袋,充分利用空間,占地面積小。
(3)採用梯形濾袋在圓筒內布置,結構緊湊。據計算,在同一簡體空間內,採用梯形扁袋比圓袋多32%的過濾面積。
(4)除塵器上蓋上設有迴轉揭蓋及換袋人孔,換袋時不必揭上蓋。
(5)圓筒形外殼受力均勻,用在易爆的煙氣(如
電弧爐煙氣)淨化中,可以防止變形。
存在的主要問題是,內、外圈濾袋的反吹時間不同,濾袋易損傷,各
濾袋的阻力和負荷皆有差別。
在袋式除塵器的濾袋上添加預塗層(
助濾劑)來捕集污染物的
除塵器稱為預塗層袋式除塵器。
袋式除塵器是一種高效除塵器,但傳統的袋式除塵器難於處理粘著性、固著性強的粉塵,不能同時脫除含塵氣體中的焦油成分、油成分、
硫酸霧等污染物,否則濾袋上就會出現硬殼般的結塊,導致濾袋堵塞,使袋式除塵器失效。用它來處理低濃度含塵氣體時,除塵效率也不高。1962年美國一家公司在玻璃纖維上添加預塗層(助濾劑為
煅燒白雲石)來捕集鍋爐煙氣中冷凝的SO3液滴(
H2SO4)獲得成功,1973年吉路德又提出在鋁工業中用加預塗層的
濾料來捕集油霧的報告。這充分說明,在
袋式除塵器的
濾袋上添加恰當的
助濾劑作預塗層能夠同時除脫氣體中的固、液、氣三相污染物,為袋式除塵器的套用開創了新的途徑。
預塗層袋式除塵器的
除塵系統如圖6—40所示,它由預
除塵器、助濾劑自動給料裝置、預塗層袋式除塵器(濾袋為圓筒開放型,安裝在上部和下部花板上)、排風機和消聲裝置等組成。預除塵器內裝有
金屬纖維狀
填充層,用以除去粗粉塵,並起阻火器作用。在起始含塵濃度較低和沒有火星進入預塗層袋式除塵器的情況下,可以不設定預除塵器。
過濾時,帶有氣、液相污染物的含塵氣體先進入預除塵器,除去粗粉塵,未被捕集的粉塵(包括氣、液相污染物)隨氣流從預塗層
袋式除塵器頂部進入
濾袋室,形成筒形濾袋時,粉塵被阻留在濾袋內表面的預塗層上,淨化後的氣體經風機排入大氣中。隨著粉塵在濾袋上的積聚,粉塵
附著層逐漸增厚,
除塵器阻力也相應增加。當阻力達到規定數值時,反吹風機構和
振動器(圖中未示出)同時動作,對濾袋進行反吹清灰,將粉塵附著層和阻濾劑過濾層一起清落下來。清灰後,
助濾劑自動給料裝置重新進行添加作業,添加時間可由
定時器控制。由於除塵器是多室結構,所以各室可按確定的程式進行添加作業和實現過濾與清灰過程。
用於預塗層袋式除塵器的助濾劑尚未定型,仍處於研製階段。一般說來,
比表面積大,塗於濾袋後不致使過濾阻力增加過多,並能吸附、吸收或中和氣、液相污染物的微細粉料適合作助濾劑。選擇恰當的助濾劑是提高預塗層
袋式除塵器捕集效果的關鍵。例如用比表面積大於45m2/g的
氧化鋁粉末,在袋式除塵器前的反應器中吸收從鋁電解爐產生的帶有氟化合物的氣體時,淨化效率可達99%以上。
預塗層袋式除塵器有以下幾個特點。
(1)由於
助濾劑的作用,預塗層袋式除塵器能淨化傳統的袋式除塵器所不能淨化的含有焦油成分、油成分、
硫酸霧、
氟化物和露點以下的含塵氣體,對粘著性、固著性強的粉塵也比較容易處理。
(2)由於助濾劑起著保護
濾料表面的作用,故
濾袋的使用壽命可以延長。
(3)可以作為空氣過濾器,用於淨化精密機器裝配車間、電氣室、製藥廠、淨化室,大型
空壓機進口的低濃度含塵空氣。
雖然預塗層
袋式除塵器和助濾劑在捕集某些氣、液相污染物上已確認有效,但都是對特定的污染物和特定的工藝過程中取得的實踐經驗,對其他污染物和工藝過程是否適用還有待進一步研究和探討。
套用
袋式除塵器作為一種高效
除塵器,廣泛用於各種
工業廢氣除塵中,如輕工、機械製造、建材、化工、有色冶煉及鋼鐵企業等。它比
電除塵器的結構簡單,投資省,運行穩定,還可以回收因比電阻高而難於回收的粉塵;它與
文丘里管洗滌器相比,動力消耗小,回收的乾粉塵便於綜合利用,不存在
泥漿處理的問題。因此,對於細而乾燥的粉塵,採用袋式除塵器淨化是適宜的。
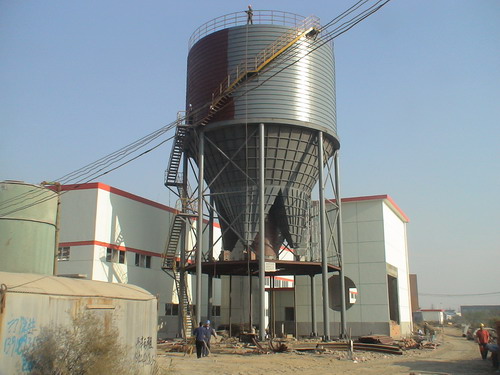
袋式除塵器不適用於淨化含有油霧、
凝結水及黏結性粉塵的氣體,一般也不耐高溫。儘管採用某些耐高溫的合成纖維和玻璃纖維等濾料,套用範圍有所改善,但在一般情況下,氣體溫度宜低於100℃。因此,在處理高溫煙氣時存在著煙氣的冷卻降溫問題。常採用的冷卻方式有三種:①噴霧塔(直接蒸發冷卻);②表面換熱器(用水或空氣
間接冷卻);③混入室外冷空氣。三種冷卻方式各有優缺點,冷卻後氣體流量按③→①→②順序減小,方式②能使
除塵器體積達到最小,但設備費卻順著②→①→③次序降低。採用噴霧蒸發冷卻方式,會導致氣體露點升高,粉塵容易黏結在濾料上,且存在腐蝕和水污染問題。所以除非需要
急冷外,不能大量採用這種方式。一般多採用換熱器冷卻,特別是採用
餘熱鍋爐時,可以做到能量的回收。
作為氣體溫度的最後調節,可以考慮採用混入少量室外冷空氣。採用何種煙氣冷卻方式,要依具體條件而定。此外,
袋式除塵器占地面積大,
濾袋更換和檢修較麻煩,工作環境也較差。