介紹
階梯式反應器硫酸法烷基化原理流程圖
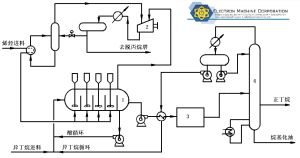
反應器各段均有一部分烴類蒸發,吸收反應所放出的熱量,維持較低的反應溫度。
所蒸發的烴類經壓縮冷凝液化後再脫除丙烷後回反應系統。
管殼式硫酸法烷基化反應器示意圖
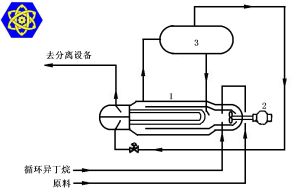
反應後的酸-烴乳狀液進入沉降器,分離出來的硫酸循環回反應器重複使用,而從沉積器分離出來的反應流出物則經過壓力控制閥流經反應器的取熱管,部分氣化吸收反應熱,以保持反處於較低的溫度。
主要影響因素
硫酸烷基化
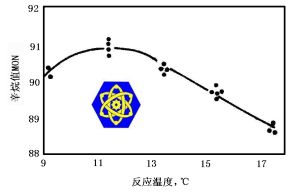
當硫酸的濃度高於99m%時,SO3將會與異丁烷直接反應,增加酸耗
當濃度低於85m%時,催化劑的活性大大降低,同時對設備的腐蝕也趨於嚴重。
因此適宜的硫酸濃度為95--96m%。
工業上通常加入反應器的新鮮硫酸濃度為98--99m%,由於原料中含水以及副反應生產的水的稀釋,以及硫酸酯和酸溶性聚合物的生成,都會使硫酸濃度在運轉過程中逐漸降低,為了保證硫酸烷基化油的質量,同時避免硫酸對設備的腐蝕,當酸濃度降低至88--90m%時,即需要作為廢酸排出。
硫酸的消耗在硫酸烷基化生產成本中占有相當的比重,因此應儘量減少酸耗。
原料中的雜質含量增加時會導致酸耗增加,原料中的烯烴中如含有丙烯和戊烯也會導致酸耗顯著增加,反應條件不當如溫度過高或過低、混合分散不均勻也同樣會導致酸耗的增加。
為此應避免導致酸耗增加的上述情況發生。
為了保護環境和降低成本,裝置所排出的廢酸絕對不能隨意排放,應將廢酸送往焚燒爐焚燒,在高溫下生成SO2,再將SO2進一步氧化成SO3,以回收硫酸。
工業上一般採用的酸烴比為1--1.5:1,以保證硫酸處於連續相。
由於硫酸的導熱係數比烴類要高得多,以硫酸為連續相能更有效地散去反應熱,避免因局部過熱反應溫度過高而加劇副反應的發生。
酸烴比也不能過大,否則會減少烴類的進料量,降低裝置的處理能力,同時硫酸增多後會使反應體系的粘度以及密度增加,導致攪拌所需的能耗增加。
鑒於提高烷烯比的目的是提高反應體系中的異丁烷的純度,在生產中常控制反應流出物中異丁烷的濃度不低於60--70v%。
如時間過短,反應不完全,影響烷基化油的收率。
如時間過長,不僅降低裝置的處理能力,會發生二次反應使產物的質量降低。