煤制炭素材料是以煤為主要原料製取的高碳材料。主要包括活性炭、炭分子篩、炭素耐火材料和炭素電極材料。
基本介紹
- 中文名:煤制炭素材料
- 外文名:coal base carbon materials
- 學科:煤化工
- 材料:活性炭、炭分子篩等
- 原料:煤
- 類型:炭素材料
活性炭,炭分子篩,炭素耐火材料,炭素電極材料,煤基橡膠填料,
活性炭
煤或其他含碳物質經過炭化和活化得到的具有多孔結構的炭質材料,是具有一定形狀、不溶於水和有機溶劑的黑色固體,有很強的吸附性能。
種類按製造活性炭的原料可分為植物性原料活性炭,如木質炭、果殼炭等;礦產性原料活性炭,如煤質炭、石油質炭等;動物性原料活性炭,如骨炭、血炭等;有機合成原料活性炭,如合成樹脂炭、有機廢料炭等。市場上常見的活性炭主要是煤質炭、木質炭和果殼炭。按製造方法不同可分為氣體活化炭和化學活化炭。按用途可分為脫色炭、糖用炭、藥用炭、淨化炭、黃金炭、空氣淨化炭、溶劑回收炭、脫硫炭、催化劑載體炭等。按外觀形態可分為顆粒炭(定型炭和破碎炭)和粉狀炭。按活性炭處理的對象是液相還是氣相,又可分別概括為液相用活性炭和氣相用活性炭。
生產工藝主要有氣體活化法和化學活化法2種。化學活化法是將含碳材料用化學藥品浸漬後在適當的溫度下,經過炭化、活化製取活性炭的一種方法,它適用於泥炭、木屑等植物性原料製成粉狀炭。常用的化學藥品是氯化鋅、磷酸、硫酸鉀和硫化鉀,其中氯化鋅套用最廣。化學活化法具有產品收率高、活化溫度低、能製得具有獨特性能(過渡孔發達)的活性炭的特點,但對環境污染和對設備的腐蝕比氣體活化法嚴重。
氣體活化法是將煤等含碳材料炭化後用水蒸氣、二氧化碳氣等氣體或它們的混合物進行高溫活化製取活性炭的一種方法。它主要適宜用煤、果殼等硬質含碳材料製取顆粒炭。氣體活化法生產工藝的基本內容包括原料的製備、炭化、活化和產品的後序處理。一般工藝流程如圖1所示。
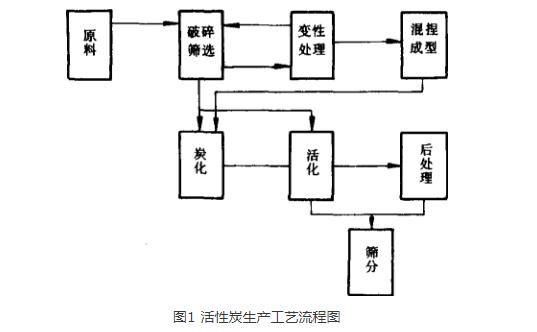
原料製備包括原料的破碎、篩選和變性處理,對於無煙煤或弱粘結性的煙煤,只須破碎、篩選出合適粒度的顆粒,經炭化、活化即可。若生產定型顆粒活性炭,破碎之後還要將煤磨至180目以下,再加粘結劑混捏成型;若用粘結性煙煤制定型顆粒活性炭,就須對原料進行變性處理,目的是降低煤的粘結性,避免炭化時原料膨脹變形,影響產品質量。通常可採用:①低溫空氣氧化;②加破粘劑破粘;③低溫乾餾成半焦進行變性處理。
混捏成型將製備好的煤粉加入適當比例的粘結劑和水混捏成稠度均勻的膏料,用成型設備加工成所需要的形狀和尺寸。中國、日本和原蘇聯國家多採用液壓和螺壓式成型機,生產直徑在1.5~5.0mm的圓柱狀活性炭; 美國採用無粘結劑高壓成型技術,將1~150μm的粉煤在1400kg/cm壓力下擠壓成直徑20cm的壓塊,然後將壓塊破碎成尺寸合適的不定型顆粒,再炭化、活化生產破碎炭。
炭化生料在隔絕空氣的低溫條件下的乾餾過程。目的是趕出生料中的部分揮發物,以形成具有初步孔隙度、緻密度和足夠強度的炭化料(半成品)。炭化速度和炭化最終溫度須根據原料煤的性質選擇,一般無煙煤可採用較快的炭化速度和較低的炭化終溫(550~600℃),高揮發分煙煤宜慢速炭化,炭化終溫在600~700℃。炭化設備可選用迴轉爐、流動爐或多段炭化爐等。
活化活化的目的是使炭化料的孔隙進一步發展、擴大,以獲得具有發達孔隙結構和一定強度要求的活性炭產品。活化的實質是水蒸氣和二氧化碳氣同碳的氧化反應。
後處理是對活化後的產品進行再加工過程。包括活性炭的脫灰、浸漬及再破碎、篩分。脫灰通常採用酸洗或鹼洗方法,一般可脫除原灰分的30%~50%。浸漬是將活性炭表面均勻地浸漬上一定重量的金屬鹽類,以改變活性炭的表面化學性質,提高去除或分離某種物質的能力。
結構與性質活性炭屬微晶質碳,根據X射線的研究,賴利 (Riley)提出兩種活性炭結構類型。第一種結構類型是由類似石墨的基本微晶構成,這些基本微晶多數是由六角形排列的碳原子的平行層片組成,各層片的排列是不規則的、紊亂的,有人把這種排列稱為“亂層結構”。第二種結構類型為不規則的交聯碳六角形空間格子,這是由類石墨層片扭曲造成的。
炭分子篩
以煤或有機化合物為原料加工製成孔徑為分子級的多孔含碳物質。一般要求原料煤的灰分和硫分愈低愈好。
炭分子篩製造工藝有熱分解法、氣體活化法、熱收縮法和堵孔法。
(1) 熱分解法。將煤等含碳物質在惰性氣氛中進行適宜的炭化。
(2) 氣體活化法。將煤等炭化物進行有控制的活化。
(3) 熱收縮法。將活性炭、焦炭等含有細孔結構的含炭材料在惰性氣氛中於1200~1800℃的溫度下煅燒,使孔隙收縮。
(4) 堵孔法。將活性炭、煤的炭化物浸漬於含有樹脂或焦油之類的高分子物質中,然後加熱處理;或是將多孔性炭質材料先加熱至400~900℃,並使其與含有苯、乙烯等碳氫化合物的惰性氣體接觸一定時間,使熱解炭沉積在孔壁或孔口上以減小孔隙直徑。
這幾種方法既可單獨使用也可配合使用。例如熱分解法同堵孔法相結合通常比單獨熱解法效果更好。圖3是德國B. F公司以煙煤為原料製取炭分子篩的工藝圖。
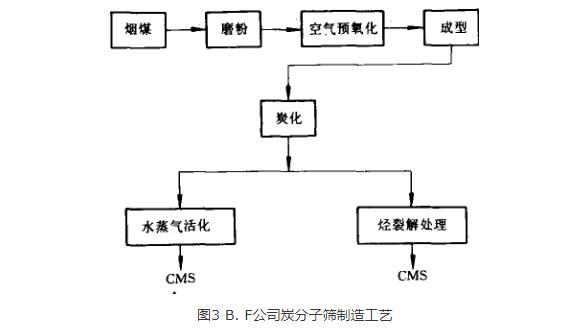
中國多使用非粘結性煤磨粉加粘結劑成型、炭化和堵孔的方法生產炭分子篩。由於各種煤的煤階性質不同,製得的分子篩孔徑大小及篩分效果也不相同,應根據原料性質通過實驗選擇合適的製造工藝。
炭分子篩的結構和性質與活性炭基本相似,同屬多孔性碳質吸附劑,有很強的吸附性能、良好的化學穩定性和較高的抗碎強度。不同之處是炭分子篩的微孔孔徑分布在一個狹窄的範圍內,且微孔孔徑的大小與被分離的氣體分子直徑相當,通常在0.3~0.7nm,孔隙形狀為狹縫形。沸石分子篩的孔隙形狀為墨水瓶形。由於炭分子篩含有分子大小的均一微孔結構,只有較小分子氣體可以進入,而較大分子的氣體則進不去,因而可用於某些氣體的分離。工業用粒狀吸附劑的一般特性見下頁表。炭分子篩分離氣體的有效性取決於對某一組分的選擇性吸附和被分離組分的吸附速度比2個因素。
炭分子篩是20世紀60年代發展起來的一種新型吸附劑,主要用於各種氣體的分離和濃縮,已工業化的是以炭分子篩為吸附劑的變壓吸附工藝分離空氣中的氮和氧。
炭素耐火材料
以無煙煤或焦炭為原料經特殊加工獲得能夠滿足高溫條件下使用要求的炭質材料。其製品主要包括各種炭磚(磚製品)、炭塊和各種炭糊類製品。
工業用粒狀吸附劑的一般特性
特 性 | 炭分子篩 | 活性炭 | 沸石分子篩 | 矽 膠 | 鋁凝膠 |
平均孔徑(nm) | 0.4~0.7 | 1.2~2.0 | — | 2.0~12 | 4.0~15 |
真密度(g/cm3) 裝填密度(g/cm3) | 1.7~2.0 0.55~0.65 | 2.0~2.2 0.35~0.6 | 2.0~2.5 0.6~0.75 | 2.2~2.3 — | 3.0~3.3 0.5~1.0 |
空隙容積(cm3/g) 比表面積(m2/g) | 0.5~0.6 450~550 | 0.5~1.1 700~1500 | 0.4~0.6 400~750 | 0.3~0.8 200~600 | 0.3~0.8 150~350 |
生產工藝炭素耐火材料的製造方法與一般炭素製品基本相同,其生產工藝流程如圖4。
(1)煅燒。目的是排除原料中的揮發分,提高原料的密度、強度和熱穩定性,降低比電阻。
(2)破碎與篩分。煅燒後的原料應破碎成適當粒度再篩分成不同的粒級,以實現正確的配料。
(3)配料。顆粒與粉末的配比須以混合料的視密度達到最大值為宜。
(4)混捏。將配合好的原料和預先準備好的粘結劑一起放在混捏機里加熱到120~160℃進行混捏,以使各種不同骨料均勻混合提高糊料的密實程度。
(5)成型。將混捏好的糊料用加壓設備壓製成所需要的形狀和尺寸。炭磚、炭塊類製品一般採用振動成型。
(6)焙燒。除糊類產品外,為使炭素製品具備使用時所需要的一系列物理化學性能,必須將生製品按一定的工藝條件進行焙燒,最高溫度為1200~1750℃,通常在倒焰式焙燒爐、隧道式焙燒爐、環式焙燒爐中焙燒。生製品周圍用焦粉或石英砂等材料作為保護介質,在隔絕空氣的條件下按一定的升溫速度進行間接加熱。
(7)加工。焙燒後的一些炭素製品,根據使用要求再機械加工成必要的形狀,尺寸。
(8)套用。炭素耐火材料能耐高溫,在化學性質上是穩定的,耐酸鹼浸蝕,熱導率高,熱膨脹係數小,而且熱變形少,在高溫下抗碎強度大,廣泛用於砌築各種冶金爐的內襯。例如用炭塊砌築高爐的爐底、爐缸及爐腹等。
炭素電極材料
以無煙煤和冶金焦為主要原料製成的炭質導電材料。其製品有用於電弧冶金爐的石墨化電極,用於鋁電解槽的炭塊,用於中、小型電爐及鐵合金爐冶煉一些普通電爐鋼及鐵合金的炭素電極。炭素電極比電阻要比石墨化電極大一些,但導熱性及抗氧化性均不如石墨化電極。炭素電極的生產工藝與炭素耐火材料基本相同,成型採用擠壓成型,此外還有屬自熔電極的電極糊等。
中國寧夏汝箕溝無煙煤是優質炭素電極材料的原料。
煤基橡膠填料
將煤磨細並加入適量的化學添加劑製取的橡膠補強填充材料。它可以代替半補強炭黑、通用炭黑、碳酸鈣、陶土、立德粉等,用於橡膠製品的生產。
製取橡膠填料用煤以較高可磨性的貧煤、貧瘦煤和瘦煤為宜。煤經磨細後其比表面積增加,加入的化學添加劑與煤發生作用;進一步提高了煤的表面活性,使其與橡膠分子的親合能力增加,從而具有增容、填充和補強作用。煤基橡膠填料與炭黑相比、經橡膠樣片測試具有密度小、彈性好、永久變形小、抗衝擊、耐低溫、電絕緣性能優良等特點,而且在橡膠混煉和壓延過程中工藝性能良好,可用於輸水膠管、非機動車胎、密封墊圈、電纜、膠鞋和蓄電池外殼等的生產。
生產工藝:原料煤經乾燥、破碎、篩選、研磨至一定程度後,加入化學添加劑並混合均勻,再進行超細粉碎,直到粒度、碘吸附值、pH值等符合要求。