氧化期,是冶煉過程的一個反應階段。電弧爐冶煉鑄鋼工藝除不氧化法冶煉外,熔化期結束後就應轉入氧化期。
通常氧化期是指爐料熔清取樣分析後到扒完氧化渣這一工藝階段。氧化期的作業是充分利用鋼液全熔時溫度低的有利條件,迅速地造好流動性良好的泡沫氧化渣;利用加礦石或吹氧脫碳為手段,做到高溫氧化,均勻激烈沸騰,自動流渣,達到去磷、去氣體、去夾雜純潔鋼液的目的,同時要控制好氧化末期的鋼液溫度和終點碳,為還原期創造有利條件。
基本介紹
- 中文名:氧化期
- 外文名:Oxidation stage
- 解釋:爐料全部熔清取樣進入氧化階段
- 方法分為:不氧化法、返回吹氧法
- 一級學科:工程技術
- 二級學科:冶金工程
電爐煉鋼,定義,作業程式,氧化前的測溫,氧化期造渣,氧化控制技術,強化脫磷,
電爐煉鋼
簡介
以廢鋼為原料的電爐煉鋼,比之高爐轉爐法基建投資少,同時由於直接還原的發展,為電爐提供金屬化球團代替大部分廢鋼,因此就大大地推動了電爐煉鋼。世界上現有較大型的電爐約1400座,電爐正在向大型、超高功率以及電子計算機自動控制等方面發展,最大電爐容量為400噸。
常用方法
(1)氧化法。氧化法冶煉的特點是有氧化期,在冶煉過程中採用氧化劑用來氧化鋼液中的Si、Mn、P等超規格的元素及其他雜質。因此,該法雖是採用粗料卻能冶煉出高級優質鋼,所以套用極為廣泛。缺點是冶煉時間長,易氧化元素燒損大。
(2)不氧化法。不氧化法冶煉的特點是沒有氧化期,一般全用精料,如本鋼種或類似本鋼種返回廢鋼以及軟鋼等,要求磷及其他雜質含量越低越好,配入的合金元素含量應進入或接近於成品鋼規格的中限或下限。不氧化法冶煉可回收大量貴重合金元素和縮短冶煉時間。在缺少本鋼種或類似本鋼種返回廢鋼時,爐料中可配入鐵合金,這種冶煉方法又叫做裝入法,用“入”字表示,多用於冶煉高合金鋼等鋼種上。
(3)返回吹氧法。返回吹氧法簡稱返吹法,用“返”字表示。該法主要使用返回廢鋼並在冶煉過程中用氧氣進行稍許的氧化沸騰,既可有利於回收貴重的合金元素,又能降低鋼中氫、氮及其他雜質的含量。因此,該法多用於冶煉鉻鎳鎢或鉻鎳不鏽鋼等鋼種。
(4)氬氧混吹法。爐料全熔後,按比例將混合好的氬、氧氣體從爐門或從爐底吹入,即相當於一台電爐又帶一台AOD精煉爐。該法主要用於不鏽鋼的冶煉上,特點是鉻的回收率高,成本低,操作靈活簡便,且鋼的質量好。
定義
弧爐冶煉鑄鋼工藝除不氧化法冶煉外,熔化期結束後就應轉入氧化期。氧化期(Oxidation stage)是指當爐料全部熔清後取樣分析進入的一個氧化的階段叫做氧化期。
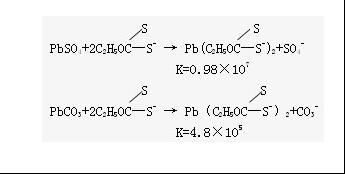
作業程式
氧化期的作業是充分利用鋼液全熔時溫度低的有利條件,迅速地造好流動性良好的泡沫氧化渣;利用加礦石或吹氧脫碳為手段,做到高溫氧化,均勻激烈沸騰,自動流渣,達到去磷、去氣體、去夾雜純潔鋼液的目的,同時要控制好氧化末期的鋼液溫度和終點碳,為還原期創造有利條件。
氧化前的測溫
全熔後,經充分攪拌取樣測溫。樣勺測溫法以鋼液結膜時間秒數為準:結膜秒數大於等於30秒時,方準氧化;採取熱電偶測溫時,應根據全熔鋼液含碳量決定開始氧化溫度:即低碳(C<0.25%) 大於等於1550攝氏度;中碳(C=0.25%~0.6%)大於等於1550攝氏度;高碳(C >0.60% )大於等於1530攝氏度。全熔測溫符合上述條件,方可進入氧化期,如果經測溫達不到規定要求溫度,應繼續升溫,直到符合規定溫度條件後,才能進入氧化期操作。
氧化期造渣
全熔測溫結束後,首先調整爐渣,向爐中補加一定量的石灰、螢石,使氧化期爐渣量達爐料重的3-4%,爐渣鹼度控制在2.0~2.5範圍內,經吹氧化渣渣料全熔後,加入氧化鐵皮或者小塊礦石,爐中立即發生碳氧反應,生成CO氣泡,這時爐渣應成為流動性良好的泡沫渣,然後要不斷加入礦石,保持爐渣Fe0的含量在12 % ~25%,使爐渣具有較強的氧化性。冶煉操作中無論是流渣或扒渣處理磷操作,補充新渣料時都應使爐渣保持大渣量、高鹼度、氧化性和良好的流動性。氧化渣的流動性。可用改變供電電流大小,吹氧節奏和加
渣等方法進行調整。為快速去磷,氧化前期保持特大渣量,後期為加速脫碳,可進行自動流渣量減少,滿足脫碳操作要求。

氧化控制技術
根據熔清試樣分析結果,測溫符合要求,渣調整良好後,即可加礦石開始氧化,礦石應分批加入,大於10t的爐子每批礦石不大於50kg,小於10t爐子每批礦石不大於30kg,每批間隔時間2~3min,加入後及時攪拌,觀察爐內反映情況,正常則繼續加礦石。為避免熔池出現大沸騰現象,加礦石時每鍬礦石不宜過多,而且要均勻地加入熔池中,不能集中在爐門口。否則熔池不能均勻沸騰,並會造成爐門口爐襯的損壞。在氧化操作過程中,要避免低溫加礦,或加礦過量。在有氧氣的條件下,氧化期可以進行礦石,氧氣交叉聯合氧化。加完礦石進行吹氧,吹氧時不斷移動氧管位置,用氧氣流攪拌熔池,使熔池各處供養均勻,達到高溫氧化,激烈沸騰自動流渣。在渣量較大的情況下,可先傾爐體,自動流出部分爐渣,自動流渣要防止鋼液流出,傾斜爐體時要緩慢而平穩。通常流渣操作是在通電的情況下進行的。流渣後根據爐中磷的情況,可以適當補加一定量的石灰和少量的螢石,保持爐渣在吹氧脫碳時仍然具備脫磷能力。氧化作業應是“先礦後氧”,使脫磷和脫碳都能順利進行,溫度控制也較方便,同時氧化末期鋼中過剩氧量少,也利於還原作業,礦石使用時間是根據鋼液含磷的情況而定,當氧化前期磷己大部分去除後,便可採用吹氧氧化。
氧化後期主要是吹氧脫碳,渣量要少,流動性要好,渣量控制在2~3%,即吹氧脫碳時能聽到電弧響聲為宜。一般鋼種要求脫碳量大於等於0.3%,關鍵品種脫碳量大於等於0.4 %,脫碳速度為 0.01~0.02%/min。吹氧時吹氧管插入角度應掌握在30度,插入深度約在鋼液面以下200mm以內,吹氧時要不停地移動氧管位置,以利於鋼液升溫和成分均勻。
強化脫磷
電爐煉鋼過程去磷操作主要是在氧化期通過強化傳質擴散到鋼一渣界面處進行氧化反應來完成的。因為在鋼液內新相的形核較困難,並且在有碳元素存在時,氧含量常低於與磷含量相平衡的數值,使鋼液中的磷難於氧化。所以,脫磷操作是電爐煉鋼過程的一個重要環節。
電爐氧化期最優脫磷操作工藝的熱力學條件是:熔池溫度控制在1550~1 600℃,最優是為1560~1580℃範圍內;控制爐渣量為鋼水量的3.5%~4.0%;脫磷渣鹼度大於3.5 、 (Fe0)含量為15%-25%範圍內;並保證足夠的供氧量。氧化期要保證一定的脫碳量和合適的脫碳速度,通過碳氧反應加強鋼液攪拌,增大鋼一渣間接觸界面,加速脫磷反應。