基本介紹
- 中文名:廢氣渦輪增壓
- 外文名:Exhaust turbocharging
- 定義:利用內燃機排氣能量驅動廢氣渦輪增壓器實現內燃機增壓的方法
- 技術障礙:爆燃、混合氣控制、熱負荷和增壓器的特殊要求等
發展歷史
工作原理
分類
利用
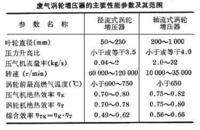
廢氣渦輪增壓是利用內燃機排氣能量驅動廢氣渦輪增壓器實現內燃機增壓的方法。廢氣渦輪增壓器(簡稱渦輪增壓器)由渦輪機(見透平)和壓氣機(見壓縮機)兩主要部件,以及軸...
廢氣渦輪增壓器主要由渦輪機和壓氣機等構成。將發動機排出的廢氣引入渦輪機,利用廢氣的能量推動渦輪機旋轉,由此驅動與渦輪同軸的壓氣機實現增壓。渦輪機進氣口與...
廢氣渦輪增壓系統由廢氣渦輪增壓器、內燃機進和排氣系統組成。...... 根據排氣管中壓力狀況和排氣能量的利用方式,廢氣渦輪增壓系統一般分為定壓增壓系統和脈衝增壓系統...
廢氣渦輪增壓是利用發動機排氣能量驅動壓氣機。廢氣渦輪增壓時,可充分利用自然吸收發動機在給定膨脹比下曲柄連桿機構沒充分利用的排氣能量,但另一方面,為了保證得到必要...
利用發動機排氣過程所排出廢氣的剩餘能量驅動廢氣渦輪高速旋轉實現增壓。增壓就是利用專用的裝置(增壓器)在進氣過程中採用強制的方法將新鮮充量送入氣缸,使其進氣量大...
渦輪增壓技術(Turbo)是一種提高發動機的進氣能力的技術。一般來說,如果我們在轎車尾部看到Turbo或者T,即表明該車採用的發動機是渦輪增壓發動機了。譬如奧迪A6的1.8T,...
渦輪增壓器實際上是一種空氣壓縮機,通過壓縮空氣來增加進氣量。它是利用發動機排出的廢氣慣性衝力來推動渦輪室內的渦輪,渦輪又帶動同軸的葉輪,葉輪壓送由空氣濾清器...
機車柴油機廢氣渦輪增壓系統是指利用柴油機排出氣體中的能量、驅動廢氣渦輪增壓器,使進人柴油機氣缸空氣壓力增加的系統。由排氣管、廢氣渦輪增壓器、進氣管以及空氣...
渦輪增壓是一種車用內燃機或航空用發動機用來增加進氣量的技術。與機械增壓器相比,兩者都可增加進入發動機的進氣量,從而提高其效率。...
增壓器應指發動機進氣增壓器,包括三種形式:廢氣渦輪增壓器、機械渦輪增壓器、電輔助渦輪增壓器。通過增壓器壓縮空氣,提高發動機的進氣密度,從而可以提高發動機的升功率...
渦輪增壓發動機指的是配備渦輪增壓器的發動機。渦輪增壓器實際上是一種空氣壓縮機,通過壓縮空氣來增加進氣量。它是利用發動機排出的廢氣慣性衝力來推動渦輪室內的渦輪,...
雙渦輪增壓是渦輪增壓的方式之一。針對廢氣渦輪增壓的渦輪遲滯現象,串聯一大一小兩隻渦輪或並聯兩隻同樣的渦輪,在發動機低轉速的時候,較少的排氣即可驅動渦輪高速旋轉...
按所用增壓器的不同可分為慣性增壓、機械增壓、廢氣渦輪增壓、複合增壓和氣波增壓(見圖)。慣性增壓內燃機裝有特殊設計的進排氣管(主要是進氣管),利用其中氣體運動...
渦輪(Turbo),是在汽車或飛機的引擎中的風扇,通過利用廢氣(exhaust gases)把燃料蒸汽(fuel vapour )吹入引擎,以提高引擎的性能。渦輪是一種將流動工質的能量轉換...
柴油機的增壓控制主要是由ECU根據柴油機轉速信號、負荷信號、增壓壓力信號等,通過控制廢氣旁通閥的開度或廢氣噴射器的噴射角度、增壓器渦輪廢氣進口截面大小等措施,...
渦輪增壓器是利用發動機排出的廢氣驅動渦輪,它再怎么先進還是一套機械裝置,由於它工作的環境經常處於高速、高溫下工作,增壓器廢氣渦輪端的溫度在600度以上,增壓器的...
幾何渦輪利用航空技術開發了電控變幾何廢氣渦輪增壓器(VGT),它可利用汽車、貨車和工程車的柴油發動機。...
(3)作為柴油機廢氣渦輪增壓器的軸承潤滑油。(4)作為閉式蒸汽機的潤滑油。(5)作為一些對粘度指數和極壓性要求不高的液壓系統用油。...
“大眾EA888發動機”是大眾全新設計的一款發動機,發動機集合缸內直噴、渦輪增壓、可變氣門正時等一系列先進技術於一身,實現了動力與經濟環保。...