周期式軋管機(又稱為皮爾格軋機)是具有變斷面圓孔型,毛管一段一段送進,實行周期式軋制的熱軋管機。周期式軋管機多用來生產石油鋼管。新的周期式軋管機每個機架由一台直流電機單獨驅動,或者每個軋輥由一台直流電機直接驅動,並採用快速餵料器和進一步增加軋輥速度的辦法來提高軋機的生產力。
基本介紹
- 中文名:周期式軋管機
- 外文名:rotary forging mill
- 套用:生產石油鋼管
- 學科:冶金工程
- 效果:節約銅材
- 別稱:皮爾格軋機
簡史
工作原理
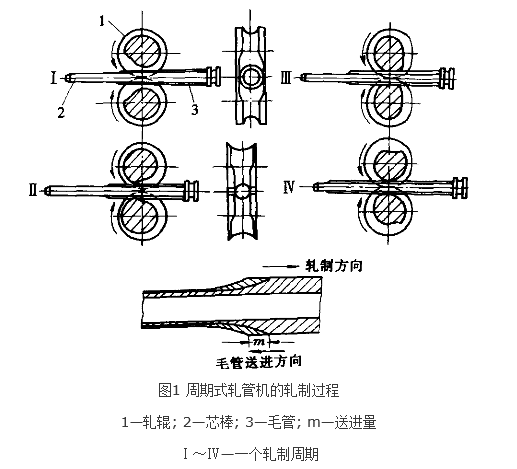
周期式軋管的變形過程
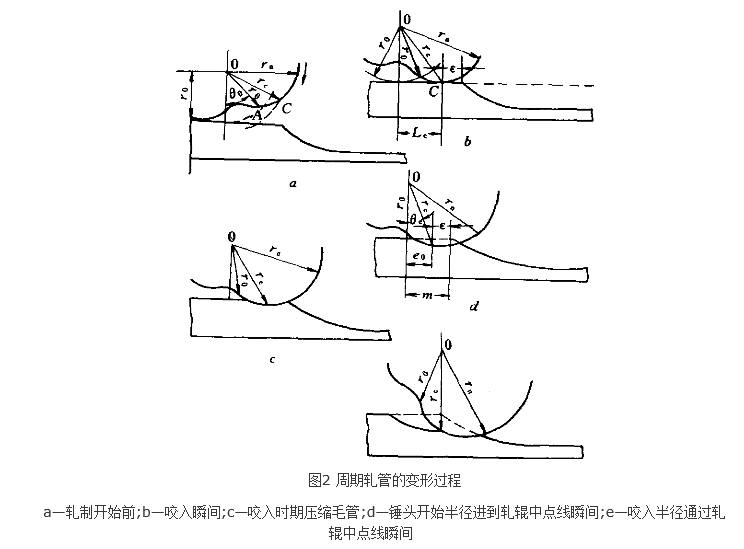
周期式軋管機(又稱為皮爾格軋機)是具有變斷面圓孔型,毛管一段一段送進,實行周期式軋制的熱軋管機。周期式軋管機多用來生產石油鋼管。新的周期式軋管機每個機架由一台直流電機單獨驅動,或者每個軋輥由一台直流電機直接驅動,並採用快速餵料器和進一步增加軋輥速度的辦法來提高軋機的生產力。
周期式軋管機(又稱為皮爾格軋機)是具有變斷面圓孔型,毛管一段一段送進,實行周期式軋制的熱軋管機。周期式軋管機多用來生產石油鋼管。新的周期式軋管機每個機架...
5 周期式軋管機通過技術改造後仍被保留並得到了發展周期式軋管機又稱Pilger mill ,適用於生產中、厚壁大中口徑鋼管,是世界上最古老的機型之一。這種軋機由於生產...
擴大, 但受齒鏈式無級變速器變速器傳遞功率的限制, 不能運用到大型軋管機上...周期式冷軋管機的發展[J]. 鋼管, 2002, 31(4):1-8. 3. 閻雪峰, ...
用熱軋的方法生產無縫管的軋機。軋機名稱自動軋管機 編輯 帶有圓孔型和快速回送輥的熱軋管機。軋機名稱周期式軋管機 編輯 具有變斷面圓孔型,毛管一段一段送進,...
芯棒(mandrel)生產無縫管時插進管體內部 同乳輻等構成環形孔型使管材成形用的工具。連續札 管機軋管、管材針軋延伸、周期式軋管機乳管、頂管和 管材冷乳冷拔時...
目前冷軋管生產多用周期式冷軋管機。周期式冷軋管機的工作特點是鋼管和芯棒不動,由機架往復運動帶動軋碾往復碾軋鋼管,採用變斷面孔型壓縮軋件,以達到減徑和減壁...
壓力穿孔是指用沖擠方法將實心坯穿孔成毛管的工序。穿孔後的毛管有帶杯底的和穿透的兩種,做為頂管、周期式軋管機軋管以及管材擠壓的坯料。...
14、龔景安、韓曉娟:用kane方法進行二輥周期式冷軋管機的動力分析; 《東重學報》1996年4期;15、韓曉娟:齒輪傳動系統剛度的確定方法;《力學與實踐》1998年4期;...
2.2.4最小可軋厚度2.3軋制壓力2.3.1軋制壓力的概念2.3.2軋制壓力的通常...3.3.2周期式冷軋管機軋制的變形原理和工具設計第4章有色金屬線材加工...
本書主要內容包括斜軋穿孔和軋管、縱軋軋管、周期式軋管等生產方法的實際套用,現代無縫鋼管生產工藝和設備進展,無縫鋼管的精整工藝(定減徑、拔制、酸洗和潤滑等...
11.2 有色金屬軋材的種類11.3 有色金屬軋制產品標準11.4 軋制技術的現狀與...15.4 周期式冷軋管機15.5 管材軋制的質量控制複習思考題鍛造16 鍛造...