側吹轉爐煉鋼是從轉爐的爐牆側面吹入空氣或氧氣把鐵水煉製成鋼的轉爐煉鋼方法。空氣酸性側吹轉爐按發明者姓氏也稱特羅佩納(Tropenas)爐。 50年代中國唐山鋼廠試驗成功了鹼性爐襯的側吹轉爐煉鋼,1958年後在中國各地使用。
基本介紹
- 中文名:側吹轉爐煉鋼
- 外文名:sideblown converter steelmaking
- 別稱:特羅佩納爐煉鋼
- 類屬:轉爐煉鋼
- 方法:從轉爐的爐牆側面吹入空氣
- 學科:冶金工程
介紹
小型貝塞麥法
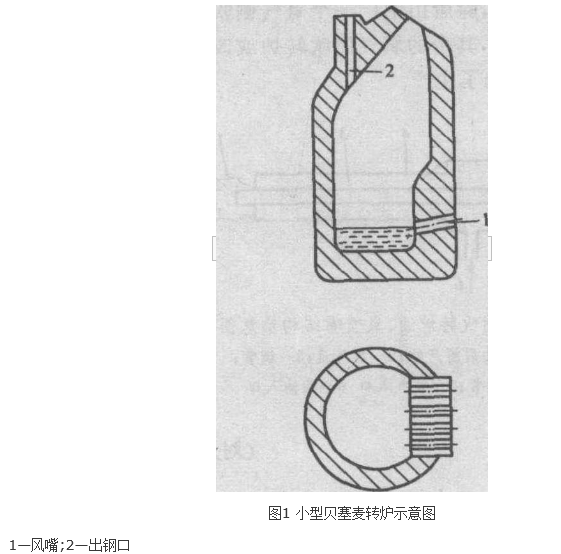
側吹鹼性轉爐煉鋼
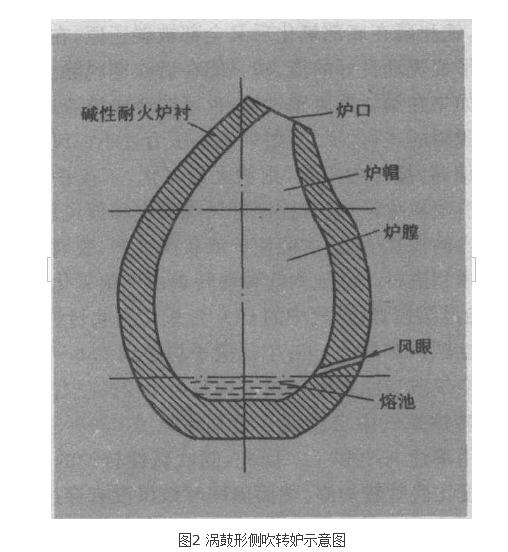
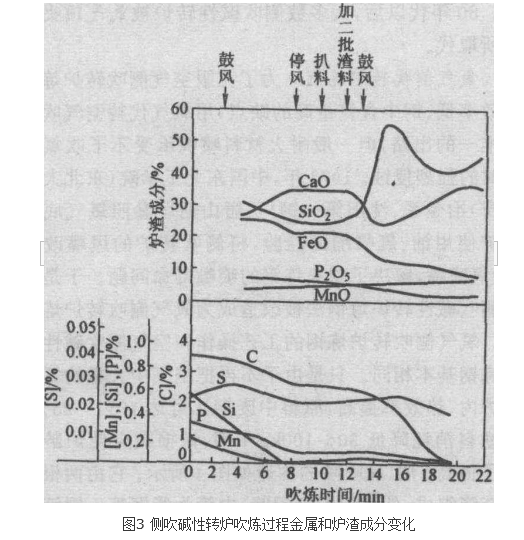
氧氣側吹轉爐煉鋼
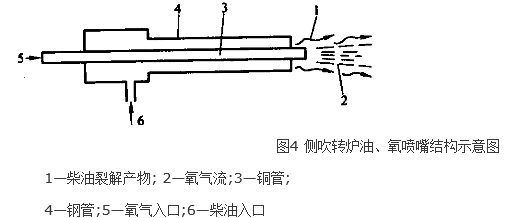
側吹轉爐煉鋼是從轉爐的爐牆側面吹入空氣或氧氣把鐵水煉製成鋼的轉爐煉鋼方法。空氣酸性側吹轉爐按發明者姓氏也稱特羅佩納(Tropenas)爐。 50年代中國唐山鋼廠試驗成功了鹼性爐襯的側吹轉爐煉鋼,1958年後在中國各地使用。
側吹轉爐煉鋼是從轉爐的爐牆側面吹入空氣或氧氣把鐵水煉製成鋼的轉爐煉鋼方法。空氣酸性側吹轉爐按發明者姓氏也稱特羅佩納(Tropenas)爐。 50年代中國唐山鋼廠試驗...
側吹轉爐側吹轉爐煉鋼(sicle blown converter steel making)是指從轉爐爐身側面吹入空氣或氧氣以氧化去除鐵水中的雜質元素並提供熱量而獲得鋼水的轉爐煉鋼方法。...
氧氣側吹轉爐煉鋼是指從轉爐的爐牆側面吹入空氣或氧氣把鐵水煉製成鋼的轉爐煉鋼方法。在當代各種煉鋼方法紛紛採用氧氣強化冶煉的階段,我國各地空氣側吹轉爐也面臨了...
轉爐煉鋼(converter steelmaking)是以鐵水、廢鋼、鐵合金為主要原料,不藉助外加能源,靠鐵液本身的物理熱和鐵液組分間化學反應產生熱量而在轉爐中完成煉鋼過程。轉爐...
托馬斯轉爐煉鋼是把高磷生鐵吹煉成鋼的一種轉爐煉鋼法,由發明者的姓而得名。...... 中國於30~40年代曾在各地用側吹酸性轉爐煉鋼,總生產能力約10萬噸/年。50年...
早期的貝塞麥轉爐煉鋼法和托馬斯轉爐煉鋼法都用空氣通過底部風嘴鼓入鋼水進行吹煉。側吹轉爐容量一般較小,從爐牆側面吹入空氣。煉鋼轉爐按不同需要用酸性或鹼性耐火...
按氣體吹入爐內的部位可分為頂吹轉爐鋼、底吹轉爐鋼和側吹轉爐鋼,還有頂吹、...從上述分析可知, 精煉工序增氮為轉爐煉鋼全程增氮的限制性環節。而精煉工序增氮...
氧氣側吹轉爐煉鋼法氧氣煉鋼的三種方式 氧氣煉鋼發展現狀 編輯 20世紀60年代中期,我國設計、科研、製造、生產人員共同協作,開展了大型氧氣頂吹轉爐煉鋼廠的設計,1971...
從轉爐爐頂吹氧的同時又向爐底吹入不同氣體進行吹煉的轉爐煉鋼方法。這是在氧氣頂吹轉爐煉鋼法和氧氣底吹轉爐煉鋼法兩種方法(簡稱頂吹法和底吹法)的基礎上發展...
轉爐煉鋼(converter steelmaking)是以鐵水、廢鋼、鐵合金為主要原料,不藉助外加能源,靠鐵液本身的物理熱和鐵液組分間化學反應產生熱量而在轉爐中完成煉鋼過程。轉爐...
酸性底吹轉爐煉鋼法是指將空氣由酸性爐襯的轉爐爐底吹入鐵水以氧化其中的雜質元素並發生大量的熱,藉以煉成鋼水的轉爐煉鋼方法。又稱為貝賽麥法。在19世紀中葉,...
20世紀50年代,中國在側吹轉爐煉鋼中發現除了進入渣中的硫和留在鋼中的硫以外,還有一部分硫轉入氣相。而且隨著終渣氧化鐵的增高,進入氣相的硫的比例增大。王國忱...
肖來潮,冶金工程專家。積極參與領導了我國第一座空氣側吹鹼性轉爐的試驗,是主要創始人之一,解決了酸性轉爐只能用低磷生鐵煉鋼的難題。領導的“直立複合吹煉雙排氧槍...
會後,該經驗在全國範圍內推廣,對指導我國轉爐煉 鋼工業的發展作出了重要貢獻;1966年3月國家 科學技術委員會為唐鋼和八鋼頒發“側吹鹼性轉 爐煉鋼法”發明證書。...
後吹是指轉爐煉鋼時吹煉到鋼水含碳量≤0.08%、脫碳速率顯著減小後仍繼續吹氧冶煉的一種不當的操作。該詞來源於托馬斯煉鋼法的後吹期。這種操作使鋼中氧、氮...
轉爐冶煉原理簡介:轉爐煉鋼是在轉爐里進行。轉爐的外形就像個梨,內壁有耐火磚,爐側有許多小孔(風口),壓縮空氣從這些小孔里吹爐內,又叫做側吹轉爐。開始時,轉爐處於...
1962年,將上鋼一廠一座5噸側吹轉爐改為氧氣頂吹轉爐。 [5] ...20世紀30年代初,周志宏在上海煉鋼廠將15噸酸性平爐改為鹼性平爐,並利用江南造船...
酸性轉爐煉鋼生鐵礦石P≤0.03%鹼性平爐煉鋼生鐵礦石P≤0.03%~0.18%鹼性側吹轉爐煉鋼生鐵礦石P≤0.2%~0.8%托馬斯生鐵礦石P≤0.8%~1.2%...
將空氣由酸性爐襯的轉爐爐底吹入鐵水以氧化其中的雜質元素並發生大量的熱,藉以煉成鋼水的轉爐煉鋼方法。又稱為酸性底吹轉爐煉鋼法。在19世紀中葉,歐洲資本主義工業...
唐鋼始建於1943年,是我國鹼性側吹轉爐煉鋼的發祥地。"九五""十五"以來,唐鋼實施鐵、鋼、軋三大系統技術改造"三步走"發展戰略和完善老區、聯合周邊、加快開發...
LBE法即復吹煉鋼法,其名稱為Lane Bubbling Equilibrium。頂底復吹轉爐煉鋼從轉爐爐頂吹氧的同時又向爐底吹入不同氣體進行吹煉的轉爐煉鋼方法。這是在氧氣頂吹轉爐...
4冶金熔池中浸入式側吹技術及其工業套用4.1我國氧氣側吹轉爐煉鋼的發展4.2熔池頂吹、底吹和側吹吹氣攪拌效率對比的水模型研究4.3傾斜側吹氣液射流在熔池中的軌跡...