基本介紹
- 中文名:高溫氣冷堆燃料元件製造
- 外文名:fabrication of fuel element for HTGR
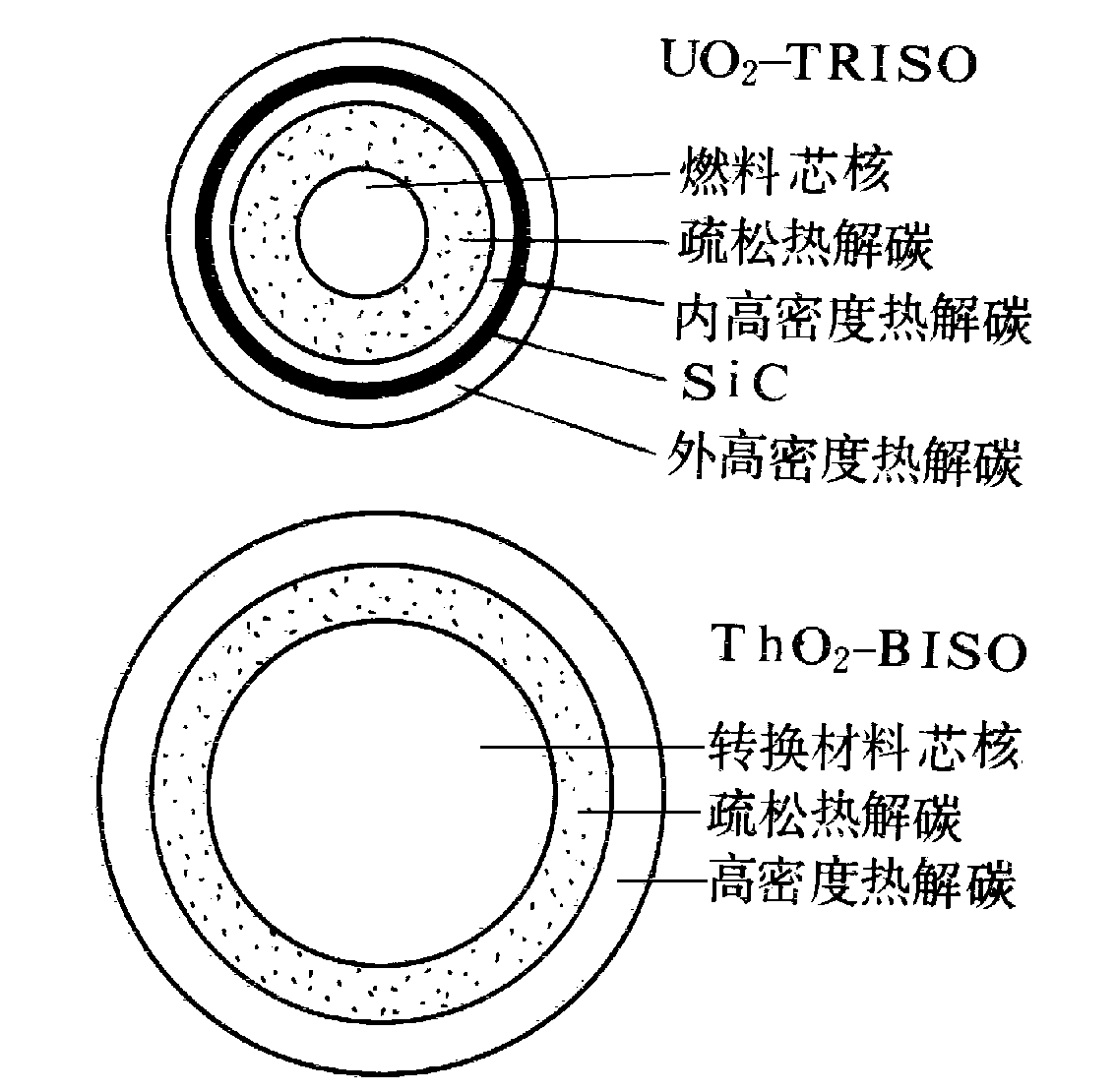
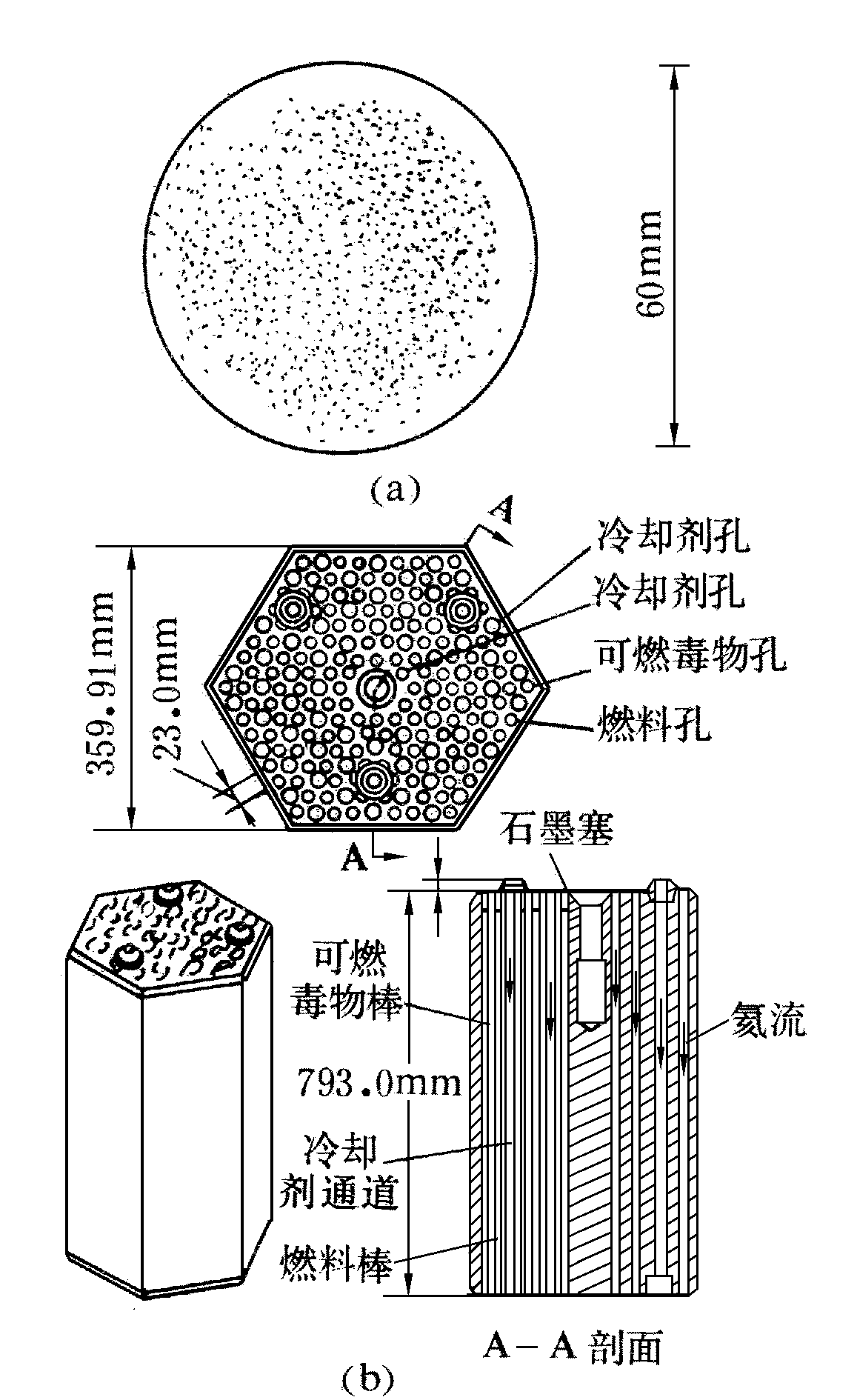
高溫氣冷堆燃料元件是包覆顆粒燃料彌散在石墨基體中的全陶瓷型元件,它的基本組成單元是包覆顆粒燃料(圖1)。高溫氣冷堆燃料元件有球形和稜柱狀兩種形式(圖2)。高溫...
《高溫氣冷堆燃料元件》是2007年化學工業出版社出版的圖書,作者是唐春和。...... 1.3.3球形燃料元件的製造1.3.4稜柱形元件的製造1.4高溫氣冷堆燃料元件主要性...
用作,出口溫度高的核反應堆。高溫氣冷堆採用塗敷顆粒燃料,以石墨作慢化劑。為,甚至更高。核燃料一般採用高濃二氧化鈾,亦有採用低濃二氧化鈾的。根據堆芯形狀,高溫...
核燃料元件是核燃料產業的最終產品,是核電站的能量源泉,核燃料元件的製造過程分...濃鈾燃料元件、100MW 高溫氣冷堆包覆顆粒球形燃料元件和脈衝堆鈾氫鋯燃料元件。...
是一種用氦氣作冷卻劑,出口溫度超高的核反應堆。高溫氣冷堆採用塗敷顆粒燃料,以石墨作慢化劑。堆芯出口溫度可達850~1000℃,甚至更高。核燃料一般採用高濃二氧化鈾,...
是建於北京市昌平區的一座用於驗證高溫氣冷堆的設計和性能的反應堆。...... 用於驗證高溫氣冷堆的設計和性能的反應堆...的基體中,製造成直徑為6cm的球形燃料元件...
上述兩種高溫氣冷堆的堆芯結構各有優缺點。高溫堆主要優點 編輯 球床堆芯的優點①球形燃料元件的設計和製造較為簡單;②堆芯內可方便地混合裝載適當比例的石墨元件...
球形元件是在球床高溫氣冷堆上使用的燃料元件。由德國研究和發展,其主要特點就是利用球的流動性,實現不必停堆就能完成裝卸料。球形燃料元件主要有注塑型元件、壁紙...
圖1(a)所示為高溫氣冷堆用的塗敷顆粒燃料,它是以直徑為200~400μm的氧化鈾...球床堆芯的優點是:①球形燃料元件的設計和製造較為簡單;②堆芯內可方便地混合...
高溫氣冷堆的燃料元件有兩種,一種是與壓水堆相似的稜柱形的,另一種是球形的...它的經濟性隨著模組式堆型的提出及核電設備製造經驗的成熟逐漸顯現出越來越強的...
用氦氣作冷卻劑,出口溫度高的核反應堆。高溫氣冷堆採用塗敷顆粒燃料,以石墨作慢化劑。堆芯出口溫度為850~1000℃,甚至更高。核燃料一般採用高濃二氧化鈾,亦有採用...
《先進核能系統和高溫氣冷堆》從燃料循環、安全性和經濟性等方面探討了先進核能系統——第4代核電技術的基本特點以及相關的技術工程問題。並且以模組式球床型高溫氣...
高溫氣冷堆燃料芯核高溫氣冷堆的燃料元件的核心部分二它是直徑為5f7n}c rn的二氧化油的燃料穎粒,也可以是一氧化牡,化鈾的混合氧化物或碳化物、氮化物顆粒,用...
10兆瓦高溫氣冷實驗反應堆就是由清華大學核研院建設的國家863高技術發展計畫項目.高溫氣冷堆是在以天然鈾為燃料、石墨為慢化劑、二氧化碳為冷卻劑的氣冷堆的基礎上...
水堆核電燃料元件生產線,正在建設第三代AP1000壓水堆核電燃料元件和第四代高溫氣冷堆核電燃料元件生產線,同時,為滿足國家大力發展核電的需要,即將對AFA3G壓水堆...
高溫氣冷堆按燃料元件和堆芯結構來分有兩種類型:球床堆和柱床堆。 球床堆由於堆芯內難以設定控制棒導向管,控制棒的插入難度大,通常控制棒插於設定在反射層的...
燃料球是高溫氣冷反應堆中使用的一種核燃料,屬於固體核燃料中得彌散型燃料。其主要優點是高燃耗、高傳熱效率和高強度、塑性和耐蝕性良好。...
高溫氣冷堆採用優異的包覆顆粒燃料是獲得其良好安全性的基礎。[2] 鈾燃料被...,包覆顆粒燃料均勻彌散在石墨慢化材料的基體中,製造成直徑為6cm的球形燃料元件。...
石墨高溫氣冷堆是一種用較高富集度鈾的包覆顆粒作核燃料、石墨作中子慢化劑、氦氣作為冷卻劑的先進熱堆。堆芯出口溫度為850~1000℃,甚至更高。根據堆芯形狀,...
的燃料;陶瓷與陶瓷,如(U,Th)O2[或(U,Th)C2]-石墨或碳化矽,是高溫氣冷堆...彌散燃料的製造方法隨不同類別而異。對第一類彌散體,可用常規冶金方法,並採用...
唐春和,1970年至1975年在清華大學核研院,從事液體金屬反應堆,熔鹽反應堆的材料和高溫氣冷堆材料研究。...
包覆顆粒全稱包覆顆粒燃料,彌散燃料的一種。包覆顆粒燃料也是一種彌散體系。在高溫氣冷堆中,採用鈾、釷的氧化物或碳化物作為核燃料,並把它彌散在石墨中。由於石墨...
通過高溫氣冷實驗堆(HTR-10)的設計、建造、臨界運行和併網發電,我國掌握了高溫氣冷堆燃料元件製造、燃料元件裝卸系統和數位化控制保護系統等核心技術,同時形成了...
1994年 中國核工業總公司部級科技進步獎三等獎:10MW高溫氣冷堆全尺寸模擬實驗裝置及球床流動特性研究,1994年 中國核工業總公司部級科技進步獎三等獎:燃料元件製造...
新加坡南洋理工大學材料工程學院、加拿大多倫多大學機械與工業工程系微孔塑膠製造實驗...“高溫氣冷堆球形燃料元件重要參數研究”(中國核工業總公司科技進步二等獎),...
2012年12月9日,中國自主研發的世界首座具有第四代核電特徵的高溫氣冷堆核電站在...蒸汽發生器等核島7項主設備製造供貨契約已簽訂完畢,燃料元件原型生產線試生產成功...
3.1 2燃料元件的製造913.1 2.1 輕水堆燃料元件933.1 2.2 壓力管式重水堆...3.1 2.5 高溫氣冷堆燃料元件963.1 3核燃料後處理973.1 3.1 磷酸鉍流程99...
第3章 高溫氣冷堆3.1 高溫氣冷堆發展概況3.2 高溫氣冷堆簡介3.2.1 球床高溫氣冷堆3.2.2 柱狀高溫氣冷堆3.3 高溫氣冷堆燃料元件...