基本介紹
- 中文名:鍛造用鋼
- 外文名:forging quality steel
- 學科:冶金工程
- 分類:鋼錠與鋼坯
- 套用:鋼鐵冶煉
- 定義:鍛造用鋼材
介紹,分類,鋼錠,鋼坯,鍛造用鋼技術發展,易切削化結構鋼的選用與關鍵技術,非調質鋼及其晶粒細化技術,其它鍛造用鋼的技術發展,
介紹
鍛造用鋼是指可以通過鍛造成型的毛坯或零件用鋼。高硫、高銅含量或純淨度過低的結構鋼熱鍛工藝性能差。連續性遭到破壞的易切削化回硫鋼因塑性差,高碳、高合金鋼因變形抗力大,不適用於冷鍛或溫鍛。鍛造用鋼的研究除分析變形能力和變形抗力等工藝性能外,更要滿足鍛件的性能和成本要求。隨著零件高強韌化、輕量化的發展趨勢,鍛造行業追求高材料利用率、高精度、高效率、低能耗、低成本等目標。鍛造用鋼的發展,離不開評價和套用技術的開發。熱鍛用鋼的易切削化、非調質化,冷鍛用鋼的簡化熱處理是降低零件工藝成本、提高生產效率和節能降耗的主要材料技術;微合金化是改善零件強韌性和工藝性能,獲得高性能、低成本鍛件的有效手段。
分類
鍛造用鋼料有兩種: (1)鋼錠,將熔化 的鋼液澆入鋼錠模內,待冷卻凝固後便從鋼 錠模內取出的稱為鋼錠,鋼錠由冒口、中部、 底部三部分組成,由於組織粗糙,缺陷較 多,它僅適合自由鍛造各種大型鍛件之用, 且只取用中間部分,冒口和底部應予切除。 (2)鋼材 (鋼坯),是鋼錠經過軋制或鍛造 而成的坯料,沿著軋制或鍛造方向形成明顯 的流線,鋼材的缺陷比鋼錠少,可鍛性顯著 提高,因此適合於各種模鍛生產。鋼材套用 最廣的是熱軋圓鋼或方鋼,也有少數精密模 鍛件 (小型的) 採用冷拉棒材。
鋼錠
將煉成的鋼水澆注到鑄鐵製成的鋼錠模內,凝固後形成的錠子稱為鋼錠。鋼錠經軋制或鍛壓成為鋼材後方能使用,所以鋼錠是半成品。根據澆注方法的不同有上注鋼錠和下注鋼錠之分。上注法一次澆注一根鋼錠,下注法可以同時澆注許多根鋼錠。下注錠的表面質量優於上注錠。根據脫氧程度的不同又有沸騰鋼鋼錠、半鎮靜鋼鋼錠和鎮靜鋼鋼錠三種,此外還有外沸內鎮鋼錠。沸騰鋼是脫氧不完全的鋼,鎮靜鋼是脫氧完全的鋼,半鎮靜鋼的脫氧程度介乎前兩者之間,接近於鎮靜鋼。鋼錠的質量有表面質量和內部質量之分。表面質量以鋼錠表面是否有結疤和裂紋及表皮的純淨度和緻密度來衡量。內部質量則以鋼錠內部的純淨度、緻密度、低倍非金屬夾雜物數量和巨觀偏析的程度來衡量。沸騰鋼的表面質量好,但由於錠心偏析大,內部質量不如鎮靜鋼。
鋼坯
鋼坯是鋼錠經初軋或開坯得到的半成品,是各類鋼材軋機的原料。鋼坯斷面有方、圓、扁、矩形和異形等數種,主要與軋制產品形狀有關。軋制簡單斷面鋼材時,選用與成品斷面相近的方鋼坯或矩形鋼坯。軋制扁鋼、角鋼等扁形產品時,選用矩形坯或扁坯。生產工字鋼、槽鋼時最好用異形鋼坯,以利軋制過程的進行和提高成材率。圓形坯是生產無縫管的原料。鋼坯的生產方法見鋼坯生產。
鋼坯斷面尺寸應滿足軋制變形量和成品質量的要求,還要考慮軋輥強度和咬入條件的限制。一般鋼坯斷面高度H與軋輥輥徑D之比 (即H/D) 應小於或等於0.5。鋼坯長度受終軋溫度、軋制時間和產品的定尺或倍尺的限制。加熱時鋼坯過長容易產生撞爐牆事故,過短則爐底利用率不高,影響加熱爐產量。為生產各種鋼材而選用鋼坯時,應儘量考慮鋼坯的共用性,以提高開坯機的生產力,簡化車間的坯料管理。
鍛造用鋼技術發展
易切削化結構鋼的選用與關鍵技術
在鋼中添加S或S-Ca是改善結構鋼切削性能的最常用合金化手段。轉爐煉鋼使用80%以上的鐵水,即使是電弧爐也可以使用超過60%的鐵水,冷軋鋼板或高純淨鋼要求的鐵水預脫硫技術以及其它高純淨鋼冶煉技術被用於鍛造熱軋棒、線材或鑄錠的生產,此時,如果不在鋼包精煉或真空脫氣後實施回硫工藝,鋼中硫含量降到0.010%以下,材料的切削性能將大幅降低。根據切削性能和零件性能的綜合要求,回硫鋼中硫含量分為0.015%~0.035%、0.040%~0.065%、0.050%~0.070%等區間,硫含量越高,鋼的切削性能越好。
實踐證明,如果滲碳齒輪鋼20Cr Mn Ti H的硫含量由0.008%提高到0.015%,齒輪高速乾切刀具的耐用度可提高1.67倍;如果將曲軸用非調質鋼48Mn V的硫含量由0.015%提高到0.045%,則曲軸內銑(乾銑)刀片的耐用度將提高49%~66%。硫含量越高,鋼或鍛件的鍛造流線越嚴重,橫向性能下降越明顯。以半軸用40Mn BH為例,淬火和低溫回火狀態下,硫含量為0.0057%和0.064%的40Mn BH的扭轉強度和拉伸強度比值分別為0.82和0.74,前者的扭轉斷口斷面與軸線垂直,為切應力斷口,而後者則出現縱向開裂。因此,承受扭轉載荷的零件,如汽車驅動橋半軸、傳動軸叉等不宜採用回硫鋼。在熱模鍛件分模面對應部位,如果金屬產生激烈的橫向流動,將導致絲線狀、棒狀硫化物的扁平化,加劇硫化物分割基體的作用,使零件在該部位的橫向性能進一步惡化,增加零件淬火開裂和磨削開裂的傾向。圖1、圖2為含硫0.025%的42Cr Mo H感應淬火曲軸分模面磨削裂紋及其斷口上的硫化物形貌,可見分模面處硫化物的最大寬度達到12~20 μm,遠遠超出非分模面處檢出的4.5~6 μm。
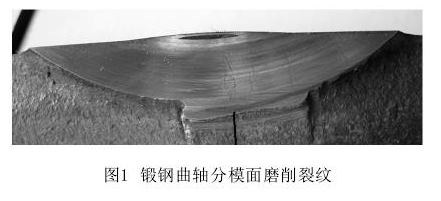
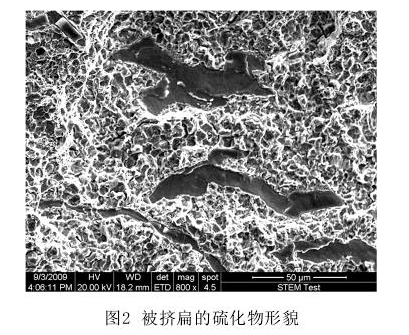
為防止回硫鋼模鍛分模面產生缺陷,減輕硫易切削化對鋼材或鍛件橫向性能的影響,可從工藝和材料兩個方面採取措施。其一是採用楔橫軋、閉式鍛模等鍛造工藝,代替模鍛工藝,因為前二者不產生分模面;其二是通過控制夾雜物形態,防止鋼中硫偏聚和硫化物的過分粗化,是降低硫化物對回硫鋼及其鍛件上述危害的有效措施。硫化物變質處理技術、連鑄工藝的末端攪拌或輕壓下技術,是冶煉此類鋼必要的關鍵技術。採用大截面鑄坯,增加棒材軋制比,減小硫化物的橫向尺寸,也有益於改善回硫鋼的橫向性能。
非調質鋼及其晶粒細化技術
非調質鋼因節能、降成本、生產周期短和不存在調質工藝缺陷等優點,在汽車零件和工程機械上得到廣泛套用。高強韌化一直是非調質鋼的發展趨勢。從第1代49Mn VS3牌號非調質鋼開始,按照增加鐵素體含量和強化鐵素體的技術構想,發展了低碳、高錳的40Mn VS、38Mn VS、30Mn VS以及高矽的更高強度的38Si Mn VS和30Si Mn VS等典型鋼種,稱為高強韌性“珠光體-鐵素體”非調質鋼;低碳和中碳貝氏體非調質鋼以中溫轉變的粒狀貝氏體和粒狀組織為基體組織,相對 “珠光體-鐵素體”非調質鋼具有更好的強韌性配合。
相對於相同強度等級的調質鋼零件,非調質鋼零件、尤其是熱鍛非調質鋼零件的塑韌性較低。除上述組織因素影響外,熱鍛(熱軋)控冷工藝狀態下的非調質鋼及其製品,因為比調質鋼製品少一次820 ~880 ℃的低溫奧氏體重結晶工藝,其晶粒比調質鋼的粗大,是導致其韌性較低的另一重要原因。常用調質鋼零件在調質狀態下的原奧氏體晶粒度可以穩定在5~10級,而非調質鋼製品,尤其是鍛後控冷狀態的非調質鋼熱鍛件的原奧氏體晶粒度則較少達到7級,大部分在5級以下,如果控鍛控冷工藝不當,甚至粗至00級。
其它鍛造用鋼的技術發展
利用Ti、Nb、V、Al、N、B微合金化對傳統鍛造用鋼進行適應性改造,控制其不同溫度區間析出物的數量和大小,達到析出強化、細晶強化或控制晶粒長大的作用,提高其力學性能和工藝性能。作為典型的微合金化非調質鋼,鋁鎮靜鋼中Al N晶粒細化的作用為眾人熟知。此外,齒輪鋼、彈簧鋼、冷鐓鋼等常用鋼種的微合金化改造又有新的進展。
1、滲碳齒輪鋼的微合金化
1、滲碳齒輪鋼的微合金化
對傳統滲碳齒輪鋼進行微合金化,最佳化了高溫滲碳齒輪鋼、冷鍛齒輪鋼、細晶強化高強韌性齒輪鋼等先進齒輪鋼品種。
1.1、高溫滲碳齒輪鋼
常用滲碳齒輪鋼利用殘餘的0.01%~0.05% Al,使其930 ℃奧氏體晶粒度細於5級,如果將Al含量穩定在0.02%~0.05%,提高N含量至0.010%~0.020%,控制Al/N比,則可以將Al N的溶解溫度即滲碳鋼的奧氏體晶粒粗化溫度提高至950 ℃,從而為高溫氣體滲碳工藝的套用提供材料支持。950 ℃氣體滲碳材料工藝技術均可在傳統的井式滲碳爐、多用滲碳爐和連續式無罐爐上實施,具有良好的套用前景。為減小或防止內氧化對齒輪滲層強韌性的影響,更高溫度的滲碳需要採用低壓真空滲碳技術,高溫低壓真空滲碳齒輪鋼的滲碳溫度高達970~1 050 ℃,此時單純利用Al、N的微合金化不能阻止奧氏體晶粒粗化,需要添加固溶溫度更高的氮化物如Ti、Nb等元素。Ti、Al、N複合微合金化齒輪鋼20Cr Mn Ti H在保溫時間為6 h情況下,其970 ℃和1 050 ℃加熱奧氏體晶粒度可分別達到8.0級和6.5級。在其中添加0.02% Nb,其1 000 ℃晶粒度可達到9.0級。
1.2 冷鍛齒輪鋼
冷鍛齒輪鋼同時融合了微合金化和熱機械軋制技術,添加Ti、Al、N或Ti、Nb、Al、N微合金化,以細化熱軋態晶粒,阻止冷鍛齒輪在後續加熱過程中的晶粒異常長大。熱機械軋制的目的在於細化熱軋交貨狀態晶粒度,通過應變誘發鐵素體析出,增加鐵素體含量,降低交貨狀態硬度。以上兩種技術的複合,使冷鍛齒輪鋼的塑性增強,臨界壓縮率達到80%,無需球化退火就能滿足冷鍛工藝要求;冷鍛成型後,可以省略再結晶退火,直接進行滲碳;滲碳後無需二次加熱淬火,就能達到晶粒度要求,達到節能降耗、簡化工藝、提高效率的目的
1.3 細晶強化高強韌性齒輪鋼
齒 輪 鋼 疲 勞 強 度 與 奧 氏 體 晶 粒 尺 寸 近 似 存在Hall-Petch關係,細化奧氏體晶粒可提高疲勞強度。細化奧氏體晶粒度的方法包括低溫滲碳、滲碳後二次淬火以及添加Nb、Ti、V微合金化。20Cr Mo H和經過Ti、Nb複合微合金化的20Cr Mo H,經歷930 ℃氣體滲碳7 h,擴散0.5 h後,有效硬化層深度分別為1.0 mm、1.2 mm,滲層晶粒度分別為7.2級和10.5級,而旋轉彎曲疲勞強度分別為995 MPa和1 230 MPa,Ti、Nb微合金細晶強化使得20Cr Mo H疲勞強度提高了23.6%。
2、高性能彈簧鋼的微合金化
彈簧鋼的使用主要參照材料的彎曲疲勞極限、鬆弛穩定性、腐蝕疲勞敏感性、延遲斷裂傾向等因素。此外,表面完整性、脫碳層深度、純淨度、晶粒度等因素對彎曲疲勞強度有顯著影響,需要據此對彈簧鋼進行質量分等。彈簧鋼的高強度化和高品質化是提高彈簧的設計應力水平,實現輕量化的必要條件。目前,汽車懸架系統螺旋懸架彈簧的扭轉疲勞設計應力水平最高達1 200~1 300 MPa,使用狀態硬度達51~53 HRC;變截面鋼板彈簧的彎曲疲勞設計極限應力水平也從之前的850~950 MPa向1 000~1 100 MPa範圍提升,從而使彈簧質量減輕25%以上。幾乎所有強度等級高於1 650 MPa的高性能彈簧鋼都經過微合金化,乘用車螺旋彈簧常用的1 650 MPa級51Cr V4牌號鋼需要添加0.2%以下的V來細化晶粒,提高回火穩定性和降低脫碳傾向。如日本神戶鋼鐵的UHS1900、UHS2000,大同制鋼的ND120S和ND250S等鋼種,都進行了V、Ti、Nb、Mo、B的微合金化,彌補了因碳含量降低至0.40%帶來的鬆弛穩定性不足,以及解決了晶界強度低於晶內強度導致的韌性下降等問題;尤其B的微合金化對彈簧鋼韌性和Ti微合金化對彈簧鋼的耐蝕性和延遲斷裂抗力的貢獻 。
3、高強度冷鐓鋼的微合金化冷鐓鋼的微合金化改造出於兩個目的:① 改善材料的冷鍛工藝性能,開發簡化退火或免退火冷鐓鋼;② 提高材料的延遲斷裂抗力,開發13.9級或更高強度等級螺栓用鋼。
3.1 高強度免退火冷鐓鋼
碳含量低於0.22%的碳素冷鐓鋼,如ML20、ML15等,在冷拔冷鐓前,不需要軟化退火或球化退火,已經屬於免退火冷鐓鋼,然而這些低碳冷鐓鋼淬透性和回火穩定性均較低,只能滿足6.8級以下緊固件的生產。普通高強度冷鐓鋼一般要經歷“退火—酸洗(剝殼)—磷化—皂化—冷拔—冷鐓—調質”等工序,退火工序的目的在於通過珠光體球化,降低材料硬度,提高材料塑性。但此工序同時也帶來較大的能量消耗和材料氧化脫碳損耗。高強度免退火冷鐓鋼得以開發套用,取得了良好的經濟和環境效益。目 前有兩類高強度免退火冷鐓鋼。一類為低碳B鋼,此類鋼的典型鋼號為SAE 10B21(SAE J403),其化學成分為0.21%C-0.08%Si-0.85%Mn-0.1%Cr-0.0025%B,通過低碳、低矽獲得較低的珠光體含量和鐵素體硬度以提高塑性,添加微量B以提高材料淬透性,控制Mn、Cr含量保證回火穩定性。此類鋼熱軋狀態的交貨狀態硬度低於85HRB,斷面收縮率達到55%,滿足冷拔和冷鐓工藝要求。該鋼種適用於8.8級螺栓,適當增加C、Mn、Cr含量可以滿足9.8級和10.9級螺栓性能要求。另一類高強度免退火冷鐓鋼是以普通的ML35、ML40Cr為基礎鋼,降低Mn、Cr含量,增加微量B以彌補淬透性不足,增加微量Ti含量,高Al/N比,以細化晶粒,運用控軋控冷(熱機械軋制)技術生產。
免退火的ML35或簡化退火的ML40Cr、ML42Cr Mo A通過雙相區(奧氏體-鐵素體)大變形量軋制,獲得
了更細的原奧氏體晶粒,更多、更細的鐵素體含量和退化的碳化物層片,因而具有更低的交貨狀態硬度和冷變形塑性。免退火冷鐓鋼ML35的熱軋交貨狀態鐵素體含量可以達到49%(退火態為42%),鐵素體晶粒度細於11級,對應的硬度為88 HB,延伸率大於26%,斷面收縮率大於55%;冷拔減面率15.7%時,冷拔後硬度為91.5 HRB,滿足冷鐓成型用料硬度低於92 HRB的要求。
了更細的原奧氏體晶粒,更多、更細的鐵素體含量和退化的碳化物層片,因而具有更低的交貨狀態硬度和冷變形塑性。免退火冷鐓鋼ML35的熱軋交貨狀態鐵素體含量可以達到49%(退火態為42%),鐵素體晶粒度細於11級,對應的硬度為88 HB,延伸率大於26%,斷面收縮率大於55%;冷拔減面率15.7%時,冷拔後硬度為91.5 HRB,滿足冷鐓成型用料硬度低於92 HRB的要求。
3.2 14.9級螺栓用鋼
強度等級達到或超過10.9級的螺栓製件,存在氫致延遲斷裂傾向,並且隨著強度等級增加,延遲斷裂傾向越明顯。冷鐓用SCM435、SCM440線材用於12.9級螺栓製件時,晶粒度達到8級,滿足抗鬆弛、抗疲勞、抗延遲斷裂要求,如果降低回火溫度容易使其強度等級達到1 400~1 500 MPa,延遲斷裂傾向明顯增加而使其無法實際套用。圖3為SCM435螺栓降低回火溫度使其強度達到1 450 MPa,運用缺口試樣慢拉伸獲得的延遲斷裂斷口形貌,裂紋起源呈現明顯的沿晶斷裂特徵,晶面有大量的氫脆特徵。
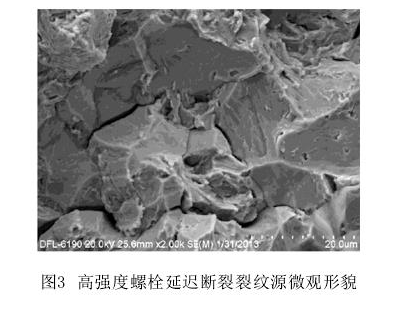