胎面膠,輪胎最外層與路面接觸而表面印有花紋的一層膠料。能使輪胎具有牽引力,緩衝行駛時的衝擊和搖擺,防止簾線層的割破和刺穿等。
基本介紹
- 中文名:胎面膠
- 外文名:tread stock;(rubber) tread compound;tyre tread;green tread
- 要求:具有高度的耐磨性
- 表面印有:花紋的一層膠料
基本信息,判斷要點,質量標準,存放方法,性能介紹,
基本信息
品 名:胎面膠 拼音:taimianjiao
英文名稱:tread stock;(rubber) tread compound;tyre tread;green tread
說明:要求具有高度的耐磨性、耐疲勞性能,良好的耐老化性能,較高的拉伸強度、彈性和強韌性,以及行駛時低的生熱性。可用天然橡膠、丁苯橡膠、順式異戊橡膠和順丁橡膠等生膠製造。膠料中常加入大量炭黑,以提高其物理機械性能。可將膠料用螺桿壓出機壓出或用壓延機壓延經冷卻而成。前法所制的胎面膠,質量較優,生產能力也較大。修補外胎所用的補胎膠,也常稱胎面膠。
判斷要點
1、看胎面膠的光澤度:色澤黝黑鮮亮,用原子筆尖輕壓花紋塊突然放開能慢慢彈得起來,恢復原狀。 2、看胎面的橫截面:細密光澤柔和,無小顆粒狀。
3、看胎面花紋:花紋稜角清晰無圓角,花紋溝底無裂口。
4、看胎面地面:無裂口、無氣泡。
5、胎面硬度不低於60度(邵氏硬度)。
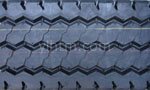
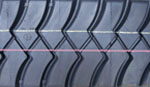
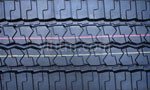
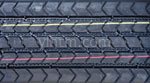
一、
質量標準
(1)壓出胎面膠斷面尺寸應符合施工標準。因為施工標準是根據成品的設計要求確定的,如達不到要求,將影響產品質量和原材料消耗定額等。
(2)胎面膠表面應平整、無疤痕、無裂縫、無氣泡、無水濕、無雜質、無焦燒和噴霜等現象。否則表面容易黏附雜物,灰塵。同時在硫化過程中,將影響膠料的流動性,產生外觀缺陷,如氣泡、水濕,降低了胎面膠與舊胎體的附著力,甚至胎面串空、脫層。
(3)胎肩兩側對稱,不得有凹凸不平,不得有斷邊等缺陷。
(4)存放時間不小於4h,不大於60h,先壓出先用。
存放方法
壓出胎面膠經冷卻打毛,裁斷後存放於活頁車或架子上,再運到胎面存放室。室內應具有一定的採光、通風 、空氣流通、防風沙和灰塵裝置。室內應保持一定的溫度,冬季25℃以上,夏季25℃以下,這對丁苯橡膠含量高的胎面膠尤其重要,這是由於丁苯橡膠收縮率大。
性能介紹
膠料(硫化膠)的主要物理機械性能指標,從輪胎整體來看,無論是新胎或翻修輪胎所用的膠料,都是組成輪胎的結構材料,結構材料性能的優劣,必然決定著輪胎的性能及使用壽命。那么用什麼來衡量及鑑定膠料的性能或質量呢?目前是將膠料(硫化膠)用專門的試驗儀試驗後所測得的數據,通過各種性能表示出來的。表示膠料物理機械性能的指標有拉伸強度、扯斷伸長率、定伸應力、永久變形、硬度、耐撕裂性、耐疲勞性、耐熱性、耐磨耗、耐老化等。
拉伸強度:扯斷單位斷面膠料時所需的外力為拉伸強度,它說明膠料抵抗損壞能力的大小。即拉伸強度越大的膠料越不易損壞,
扯斷伸長率:膠料被扯斷時的伸長與原長的比值為扯斷伸長率。它說明膠料被損壞時允許的最大變形範圍。伸長率大的膠料較伸長率小的膠料不易被外力的作用所損壞
定伸應力:使膠料產生一定的伸長變形時所需的外力為定伸應力。根據對膠料試驗時所採取的伸長變形不同,有100%、200%、300%、500%等。它說明膠料抵抗使之變形的能力,即在一定外力作用下,定伸應力大的膠料伸長變形必小。
永久變形:膠料扯斷時經停放一定時間(3min)後,所增值加部分的長度
硬度:膠料表面受一定壓力時的變形程度。有邵爾硬度、肖氏硬度等,常用邵爾硬度,它說明膠料抵抗外力使之變形的能力。
耐磨性:膠料受一定摩擦力作用後,膠料失去多少可用來表示膠料的耐磨性能。常用的有阿克隆磨耗,是以試樣轉動1.61km後,膠料被磨去的體積來表示。它說明膠料經受連續磨損的能力。
彈性:膠料反衝擊作用時,擺錘彈起高度與原高度之比,以%表示。它說明膠料彈性瞬間恢復能力的大小。即彈性越大,膠料受衝擊時接受外力越小,受衝擊本身的變形也越小。
耐撕裂性:撕裂已經切口的單位厚度膠料所需的力,稱為撕裂強度,單位為KN/m。它說明膠料抵抗外力撕裂能力的大小。
耐疲勞性:膠料在周期性外力迅速交換的作用下所產生的損壞程度、性能下降程度或開始損壞周期數和時間。它說明膠料本身保持原性能(即性能持久性)的能力
耐熱性:膠料在保持一定的恆溫後,進行物理機械性能試驗,以青示膠料在高溫條件下保持膠料原性能的能力。
耐老化性:膠料在經一定溫度和一定時間作用後,其性能與原性能之比。它說明膠料受一定溫度作用後,性能下降的程度。
四、胎面膠硫化三個要點:
胎面硫化溫度
一般以天然橡膠及順丁橡膠制的預硫化胎面,其硫化溫度最好在150℃以下,這是因為高溫硫化多硫鍵斷裂,交聯密度低,使胎面膠的物理機械性能較低,同時易發生硫化返原現象,質量難以控制,且在裝模時易產生焦燒或因流動性下降而不得不摻用抗返原劑及抗焦燒劑。
預硫化胎面硫化深度
預硫化胎面硫化的濃度很重要,胎面硫化時厚製品用流變儀測得的t90或用試片測得的正硫化點均需加以調整,以防胎面中間層次欠硫。因欠硫的胎面耐磨性急劇下降,反之,稍過硫對耐磨性的影響很小。因此預硫化胎面的硫化深度應保證胎面中部達到正硫化點,翻新兩次硫化時因硫化溫度低對胎面的性能影響不大。
預硫化胎面的硫化壓力
預硫化胎面硫化的壓力對胎面膠的物理機械性能是有一定的影響的,特別是對膠的耐磨性及抗刺扎性。將硫化壓力為5.0-7.0Mpa的環形及條形預硫化胎面翻新胎,與硫化壓力為1.5Mpa的模型法翻新的輪胎大規模地進行里程對比試驗(胎面配方相同)。結果是提高預硫化胎面的硫化壓力可提高胎面的耐磨性,硫化壓力為5.0Mpa的預硫化胎面翻新胎比模型法翻新的輪胎里程提高7.7%。