縮痕為製品表面的局部塌陷,又稱凹痕、縮坑、沉降斑。當塑件厚度不均時,在冷卻過程中有些部分就會因收縮過大而產生縮痕。但如果在冷卻過程中表面已足夠硬,發生在塑件內部的收縮則會使塑件產生結構缺陷。縮痕容易出現在遠離澆口位置以及製品厚壁、肋、凸台及內嵌件處。
基本介紹
- 中文名:縮痕
- 外文名:Shrink mark
- 別稱:凹痕、縮坑、沉降斑
- 原因:注塑件壁厚不均
- 出現位置:製品厚壁、肋、凸台及內嵌件處
- 消除措施:提高注射壓力等
基本信息,產生原因,
基本信息
注塑件表面上產生的不規則的凹陷稱為縮痕,也可稱為塌坑、凹痕、凹陷和下陷等,如下圖所示。
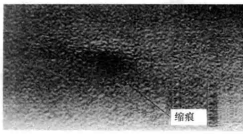
縮痕是由於保壓補塑不良,注塑件冷卻不均,壁厚不均而引起收縮量不一致或因塑膠收縮率過大等原因而產生的,可歸納為冷卻收縮影響類的缺陷。
產生原因
產生縮痕現象的原因及排除方法如下:
1、成型條件控制不當
可適當提高注射壓力,增加熔料的壓縮密度,延長注射和保壓時間,補償熔體的收縮,增加注射緩衝量。如果凹陷和縮痕發生在澆口附近,可以通過延長保壓時間來解決;當塑件在厚壁處產生凹陷時,應適當延長塑件在模內的冷卻時間;如果嵌件周圍由於熔體局部收縮引起凹陷及縮痕,這主要是由於嵌件的溫度太低而造成的,應設法提高嵌件的溫度;如果由於供料不足引起塑件表面凹陷,應增加供料量。此外,塑件在模內的冷卻必須充分。
2、模具缺陷
結合具體情況,可適當擴大澆口及流道截面尺寸,澆口位置儘量設定在對稱處,進料口應設定在塑件厚壁的部位。如果凹陷和縮痕發生在遠離澆口處,一般是由於模具結構中某一部位熔料流動不暢,阻礙壓力傳遞,應適當擴大模具澆注系統的結構尺寸,最好讓流道延伸到產生凹陷的部位。
3、原料不符合成型條件要求
對於表面要求比較高的塑件,應儘量採用低收縮率的樹脂。
4、塑件結構設計不合理
進行塑件結構設計時,壁厚應儘量一致。若塑件的壁厚差異較大,可通過調整澆注系統的結構參數或改變塑件壁厚分布來解決。
5、製品壁太厚或邊角處熱量集中,製品難以冷卻。一般製品壁厚不超過3.5mm(氣輔或發泡除外),若邊角處較厚,可使頂面壁厚漸變減薄,並使該區域充分冷卻,減少收縮。
6、工藝調整
①壓力調整。在達到滿射時注射壓力的基礎上,每次注射遞加0.5~1MPa,直至壓力增加至設備最大注射壓力。調整過程中注意觀察製品的脫模情況,若出現製品拉白、頂白等現象,應對拉白、頂白位置噴脫模劑,以防止肋斷造成試模失敗而影響裝配驗證。當注射壓力尚未增至設備最高壓力,而製品分型面已脹模時,則以當前壓力為最高壓力,而無須增至設備最大注射壓力,但必須作試模記錄,並保留脹模的樣件。找準最大注射壓力後,需進行時間調整。
②時間調整。觀察注射行程電子尺,將注射、保壓時間延長至注射行程電子尺無位移。若仍不能解決,進行模具溫度調整。
③模具溫度調整。降低產生縮痕處的模具溫度至30℃以下。
通過以上工藝調整,若仍不能去除製品的縮痕現象,可認為製品的縮痕無法通過調整注塑工藝來解決。