發火合金亦稱為引火合金或打火石合金。以粉末狀存在與空氣接觸後可以自燃的合金,包括一些稀土合金和鋯合金等,鐵、鈷、鎳、釩、鈦、錳等金屬的粉末也具有這種發火性質,稱為發火金屬,在一定角度受到金屬(如鋼)的撞擊和摩擦能產生強烈火花的合金。
基本介紹
- 中文名:發火合金
- 外文名:pyrophoric alloys
- 又稱:引火合金
- 別稱:打火石合金
- 分類:非稀土系和稀土系
- 含有元素:鐵、鎂、銅等
簡介,發火合金的物理性能和用途,化學成分和技術條件,打火石合金中各元素的作用,發火合金生產工藝,
簡介
發火合金按成分可分為非稀土系和稀土系兩類。非稀土發火合金是用鋯、鈦、錫、鉛、銻製成的合金,這類合金大都含有鋯,或者含有鈦和鋯,為早期使用的發火合金。自從1903年奧地利人韋爾斯巴赫(A.von Welsbach)研製出由混合稀土金屬和鐵構成的稀土發火合金以後,稀土發火合金便在發火合金中占有主導地位。這種合金主要用作打火機的打火石,並且廣泛套用於曳光彈、子彈和炮彈的引信、點火裝置和其他軍事設施上。工業上生產的稀土發火合金一般含有20~30%左右的鐵,有的含有2~3%左右的鎂。
稀土發火合金主要採用熔煉-擠壓工藝生產,也採用粉末冶金和鑄造工藝生產。熔煉-擠壓工藝是將發火合金熔化鑄造成錠,在400~600℃下擠壓成直徑為2.5毫米左右的細條,切斷後,在表面上噴塗防蝕劑即成。此法生產效率高、成本低。近年將發火合金製成粉末,用於製造發火武器以及其他裝置中的引火材料。稀土發火合金粉末中含矽20%,鋅25~40%或碳8~10%。
發火合金的物理性能和用途
一般製造發火合金廣泛套用混合稀土金屬,其中以鈰為主。含有鑭、鐠、釹等輕稀土金屬元素。利用稀土金屬的化學性質活潑,對氧的親和力強,而鈰組金屬的燃點很低(鈰為165℃,鐠為190℃,釹為270℃)並且燃燒時放出大量的熱。例如,燃燒1g金屬鈰放出4.4411KJ熱量。當這些金屬(特別是鈰)在不平的表面摩擦時,其細粉就自燃,但質地軟而不宜作打火石原料。打火石製造是採用以鈰為主的混合稀土金屬鐵合金,其中還配入適量的鎂、鋅、銅等,以增強打火石的發火性、耐磨性及耐腐蝕性能。
發火合金的密度約為6.7~6.89/cm3,熔點670~700℃,維氏硬度130~170HV。燃點很低,發火性能優良,因此廣泛套用於打火機、發火玩具、工業火炬點火器等發火合金中,在軍事工業上用於製造子彈或炮彈的引信及引燃裝置。
化學成分和技術條件
打火石的化學成分與火石的組織結構、發火性能等有很大關係,必須選擇最佳配方,打火石常見的化學成分見下表:

1、打火石的技術條件(GB 4383—84)如下:
發火率≥95%;
耐磨次數600次以上/粒;
硬度值130~170HV。
2、規格按外形長度劃分見下表:

打火石合金中各元素的作用
1、稀土金屬
稀土金屬是打火合金的基體,是主要成分,它與氧的親和力大,反應時放出大量的熱量。
2、鐵元素
鐵是合金中的主要填料,可提高合金硬度,與稀土鈰作用,生成CeFe5,CeFe2等金屬間化合物,含Fe在12%以下時,加工性能良好,發火性能差,但含Fe量高於25%時,則硬度高、擠壓力大、成型不良。
3、鎂元素
鎂能與稀土鈰生成Ce-Mg中間化合物,燃點很低,增強發火性能。含鎂量高於5%,發火性能雖好,但擠壓成型壓力高;含鎂量太低,則發光性能差,合金中晶粒細化,使合金帶有韌性,摩擦時不能粉化,打出的火不是火花而是焰。
4、鋅元素
合金中的鋅,無助於發火性,但可增加合金的密度和防腐蝕性能,因此,鋅的含量不宜高。
5、銅元素
在合金中加入少量的銅對打火石的發火性能、耐磨性能和儲存穩定性無不良影響,而對降低壓力有效,但銅成分不宜太高(對擠壓不利)。
發火合金生產工藝
用混合稀土金屬及鐵為原料,加入鎂、鋅、銅等少量元素,用石墨坩堝在中頻電爐內加熱熔煉、燒鑄成錠,經熱擠壓成型單孔連續出條再切粒、選粒、噴漆等一系列加工處理,成為打石產品。其工藝流程如下圖:
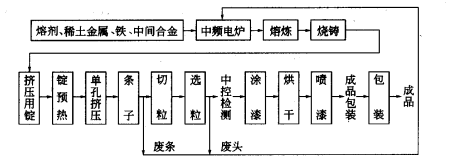
爐料組成包括金屬原料、回爐料、中間合金及熔劑四類成分。
1、金屬料包括混合稀土金(以鈰為主的鑭、鈰、鐠、釹、輕稀土金屬)、鎂、鋅、銅、鐵。
2、回爐料是指廢錠、澆口、切粒、選粒等廢料。
3、中間合金
其熔點只有約600℃,在通常的熔煉溫度下通過合金化能很快地熔化(純銅熔點高達1063℃,故須先製成有鎂、鋅、銅元素的中間合金使用)。
4、熔劑
通常使用KCl、CaCl2、Nacl、MgCl2等為熔劑,主要是造渣、稀釋熔渣,使液渣利於分離。
整個工藝過程中的主要工序有熔煉、澆鑄(模鑄法或管鑄法)以及成形(擠壓成形法和粉末成形法)。