基本介紹
- 中文名:煙塵率
- 外文名:soot rate
- 描述對象:錫精礦還原熔煉過程的關鍵指標
- 作用:衡量整個熔煉過程好壞
- 影響因素:操作管理制度 設備構造
- 描述領域:錫精礦還原熔煉 冶金
簡介,煙塵產生,產生過程,產生原理,煙塵率高的原因,閃速爐煙塵率,還原熔煉,
簡介
煙塵率是錫精礦還原熔煉過程中的一個關鍵指標,同時也是衡量整個熔煉過程好壞的一個依據,煙塵率上升,將使金屬Sn入煙塵量增加,Sn直收率下降,從而增加了返回品煙塵的處理量及生產作業成本,降低了經濟效益,並且造成爐子煙塵處理系統超負荷運行,發生堵塞,爐子抽風差,影響了整個流程的暢通。它不僅使餘熱鍋爐清灰更為複雜,從而能響閃速爐作業效率、而且還增加了收塵設備和洗滌系統的負荷、使能耗增加,對設備維護也非常不利。此外由於煙塵反覆循環,使得閃速爐制精礦淨投人量減少,使r產量最受到影響、降低冶煉直收率。
煙塵產生
產生過程
原熔煉技術的特點是由一支經特殊設計的噴槍插入爐內熔融渣池進行強烈攪拌而進行的強化還原熔煉過程。因此,它的整個熔煉過程是連續動態進行的,與傳統反射爐相比,煙塵量明顯高於反射爐。爐內的整個還原熔煉過程是典型的氣(煙氣)一固(爐料)—液(爐渣)多相反應過程。噴槍對熔體的直接噴射和攪動更有助於促進氣一固、固一液和液一氣之間的相間反應。在這種反應條件下,煙塵的產生存在以下途徑:
(1)機械夾帶
爐料從加料口進入爐內約有10m距離,因此在下落過程中將不可避免地有部分含Sn物料直接被煙氣夾帶抽入煙氣處理系統而成為煙塵,但從實際生產中精礦與煙塵的化學分析來看,能形成揮發性產物的Sn、Zn、Pb、等元素在煙塵中品位高於在錫精礦的品位,而難揮發的脈石成分Si02、CaO和Fe品位明顯低於精礦。這說明煙塵的主要組成不是物料的機械夾帶,而是高溫揮發產物,而且煙塵的顏色和粒度也明顯不同於錫精礦。因此,可以認為機械夾帶不是煙塵產生的主要原因。
(2)以SnO 形態揮發



重新被氧化
成進入煙塵。


(3)以SnS形態揮發
SnS是一種極易揮發的物質.其沸點約
,在熔煉過程溫度下有很高的蒸氣壓。在精礦和其它爐料(如返回的煙塵等)以及還原煤和燃煤中都含有大量的S,在熔煉過程中不可避免地產生SnS揮發進入煙氣。

綜上所述,SnO和SnS的揮發是錫還原熔煉過程中產生煙塵的主要原因。
產生原理













煙塵率高的原因
閃速爐煙塵率
影響閃速爐煙塵率的原因是多方面的,總歸起來有兩個主要因素:一是操作管理制度,二是設備構造。如精礦噴嘴和反應塔重油噴槍的結構不盡合理,即設備本身存在的缺陷。
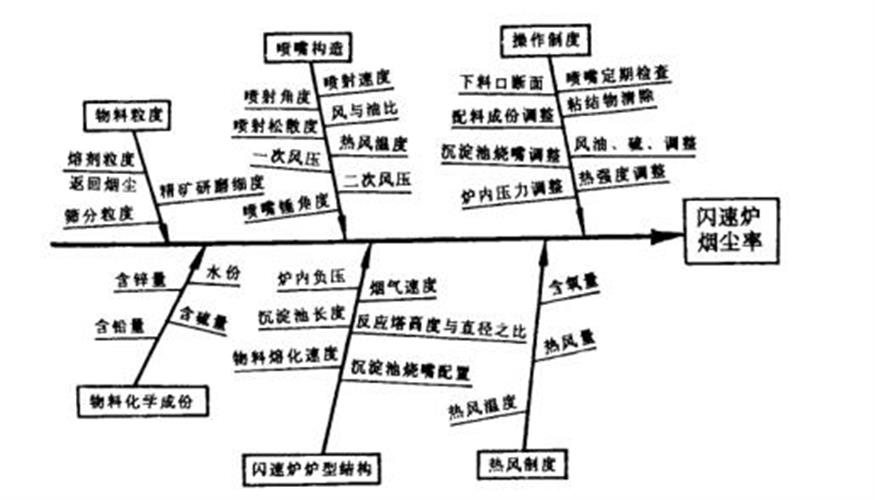
還原熔煉
(1)入爐物料的影響
由於錫精礦價格上漲、原料短缺,但同時為保證爐的正常生產,部分高S精礦在沒有經過煉前處理沸騰爐焙燒脫硫的情況下直接進入熔煉生產,同時化驗結果的滯後,增加了配料難度,降低了配料的準確性,使得在生產過程中產生大量SnS揮發進入煙塵,煙塵量上升,Sn直收率下降。
(2)入爐物料的影響
由於錫精礦價格上漲、原料短缺,但同時為保證正常生產,部份高S精礦在沒有經過煉前處理沸騰爐焙燒脫硫的情況下直接進入熔煉生產,同時化驗結果的滯後,增加了配料難度,降低了配料的準確性,使得在Ausmelt爐的生產過程中產生大量SnS揮發進入煙塵,煙塵量上升,Sn直收率下降。
(3)渣型的影響
渣型合理與否直接決定了0還原熔煉過程的好壞。在熔煉過程中主要通過矽酸度K值的調整來達到所需要的合理渣型。渣中含量的增加會增大渣中SnO的活度,更有利於SnO的揮發進入煙氣而增大煙塵量。隨著精礦含AS、S、Fe等雜質含量的升高,以及還原煤、燃煤質量下降,含固定炭降低、灰份增加,灰份中主要成分SiO、CaO、MgO等的大量帶入,造成熔煉過程中渣型發生較大轉變。妒渣熔點上升粘度增大,流動性差,加大了熔煉難度,煤耗進一步上升,其入爐煤量中帶入的CaO在渣中含量的增加增大了渣中SnO的活度,更有利於SnO的揮發,從而增大了煙塵量。
(4)返回品搭配率的影響
由於精礦的量少,在熔煉過程中配入較多的返回品,如煙塵、淋洗塵、析渣等含錫物料,返回品的搭配率有時達到45%左右,而返回品由於含AS、S等有害雜質高,導致AS、S等有害雜質在熔煉過程中的惡性循環,Sn使煙塵率增加,產生大量煙塵。
(5)熔煉溫度的影響
因精礦含Sn品位下降,隨著耗煤量的增加,灰份的帶入量增多,將增大爐渣的產出量,同時大量的爐渣在熔煉過程中,隨渣型轉變,矽酸度K值上升,熔點升高,粘度增大,流動性差,必將提高整個熔煉過程的控制溫度。因此,過高的溫度將使SnO的揮發量增大,煙塵量增加。
(6)噴槍操作槍位的影響
(6)噴槍操作槍位的影響
噴槍操作槍位的控制是還原熔煉過程中的關鍵,槍位的高低直接決定了攪拌強度的強弱,也在一定程度上決定了煙塵率的大小。槍位過高,熔池溫度下降,還原效果降低,增加燃煤及還原煤單耗,也就增加了煤中帶入的S量,Sn入煙塵率增加;槍位過低,加大了噴槍對熔池的攪拌強度,溫度上升過快,煙塵產出量增大。