氧勢是指平衡體系中氧的相對化學勢。金屬氧化反應達到平衡時的氧分壓pO2 稱為化合物MexOy的分解壓,此值越低,表示金屬氧化物MexOy越穩定,它與氧化反應的氧勢(ΔG°)的關係是:
ΔG°=R T ln pO2
式中R為氣體常數,T為絕對溫度。
基本介紹
- 中文名:氧勢
- 外文名:Oxygen potential
- 釋義:平衡體系中氧的相對化學勢
- 套用:金屬冶煉
- 學科:化學
概念,攀鋼高爐渣鐵氧勢測定實驗研究,研究進展,測定原理和難點,現場渣鐵樣氧分壓的測定,測試過程的可靠性,低氧勢焙燒預處理難浸金礦,研究背景,工藝原理,實驗結果,
概念
氧勢是指反應體系中氧的相對化學勢,即標準平衡分壓,也表示氧化物中氧逸出的趨勢。例如,當氣相的氧分壓小於氧化物的平衡分壓時,此氧化物不穩定,將發生分解;反之,氧化物將穩定存在或單質將繼續被氧化成氧化物。
攀鋼高爐渣鐵氧勢測定實驗研究
研究進展
提高高爐含欽爐渣的城勢(氧分壓)是抑制渣中TiO2過還原的重要措施,是防止和消除泡沫渣生成,實現全釩欽礦冶煉的關鍵。為此,進行高爐高欽型爐渣氧勢的測定研究具有十分重要的意義。由於欽渣高溫還原變稠等特性,給測定工作帶來很多困難。
測定原理和難點
(1)測定原理
氧化物固體電解質濃度差電池通常可用於測定體系中的氧分壓或活度,其工作原理見圖1。
圖1 固體電解質氧電池工作原理示意圖
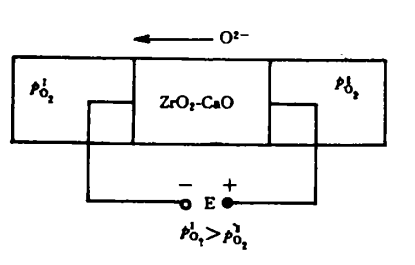
當把固體電解質置於不同氧分壓之間,並連線金屬電極時,在電解質與金屬電極的接界面處將發生電極反應,並建立不同的平衡電極電位。顯然它們構成的電池,其電動勢E與電解質兩側氧分壓直接有關。
(2)測定難點
以往,固體電解質濃差電池一般是用於測定氣相中氧的分壓及金屬液中氧的活度,測定渣相氧分壓的工作則很少見。這通常是由於渣相中電極反應及導電機制的複雜性,使得測童工作的穩定程度無論在理論及實踐上都較難把握的緣故。特別對測定攀鋼高爐渣的鐵氧分壓,又具有以下特殊難點。
①測量對象為高爐渣鐵樣,其氧分壓值較低。曾有人測定過煉鋼爐渣的氧分壓,其值大致在1.01325×10-2Pa,而普通高爐渣氧分壓遠低於該值,通常認為在1.01325×10-11Pa左右。攀鋼高爐由於採用特殊技術措施,其氧分壓可能有所提高,但仍會遠低於煉鋼爐渣。有關低氧分壓高爐渣鐵氧位的測定工作還未見報導。由於氧分壓越低,其值的微小變化對測量電勢(開路電壓)的影響就越顯著,因此,獲得穩定測量值的難度也就越大。所以,在低氧分壓條件下,要獲得穩定可靠的測量值,一定要穩定其測量環境,這樣必然加大實驗難度。
②攀鋼高爐渣含有大量的TiO2,與普通高爐渣有顯著不同的特點。它對所選固體電解質穩定性的影響尚有待進行研究,同時高欽渣本身穩定性對於電極反應及導電機制的影響,也少有人進行討論。
③因面臨的實驗溫度較高,約1500℃左右,這對定氧探頭的一些使用性能,如抗熱震性能的要求較高,同時在此高溫下,要保持實驗溫度的恆定並取得穩定的毫伏級實驗電位值的難度也很大。
④因實驗所測試樣為現場渣鐵,如何保持渣鐵在重熔過程中其氧分壓不變,及如何保持測量過程中測量環境的氧勢,對測量對象,即現場渣鐵不構成影響,是取得準確實驗數據的關鍵,要實現這一點也不易。
現場渣鐵樣氧分壓的測定
為了確定攀鋼高爐渣鐵的氧分壓,在實驗室用上述定載探頭進行部分典型現場渣鐵樣的側定工作。將攀鋼現場渣鐵選出成分差異較大的試樣作實驗,並取鞍鋼普通高爐渣作比較(表1)。
表 1 實驗用渣鐵樣成分及測試結果
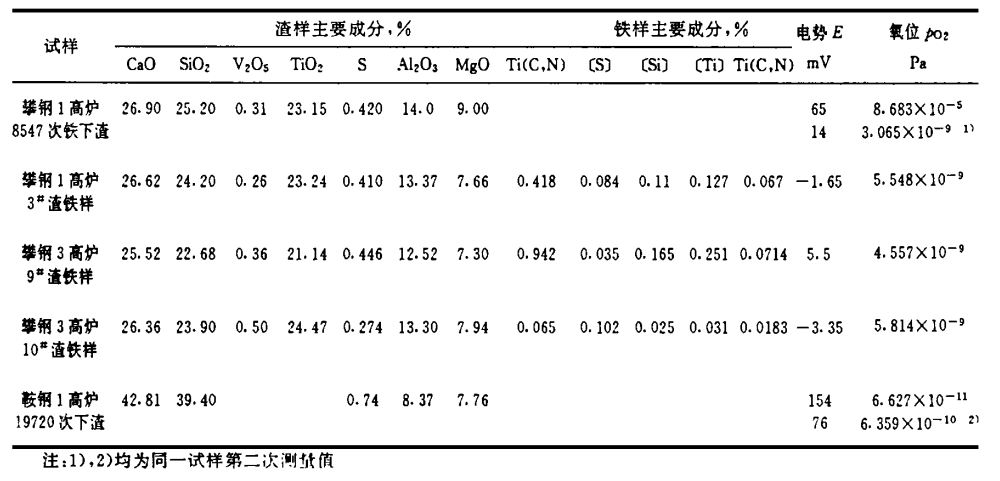
由於每次所取的現場渣鐵樣均來自同一爐次,如果考慮到爐缸中渣鐵反應已近似達到平衡,且攀鋼渣中帶鐵多,則可認為同一爐次的渣鐵樣具有相同的氧分壓,這樣將同一爐次的渣鐵樣放在一起進行測量。
測試過程的可靠性
本實驗的結果表明,用上述工藝組裝的定氧探頭測定攀鋼及鞍鋼高爐渣鐵的氧分壓,能夠獲得長時間穩定的電勢值(典型曲線如圖2所示),說明探頭的抗熱震性及穩定性較好。同時,構造的測量環境非常穩定,制定的實驗方法可行,因而使待測渣鐵的氧分壓可在測定過程中長時期(最長可持續20min不受環境影響而保持穩定,可真實反映攀鋼或鞍鋼渣鐵的氧勢值。
圖2典型定氧電勢位曲線
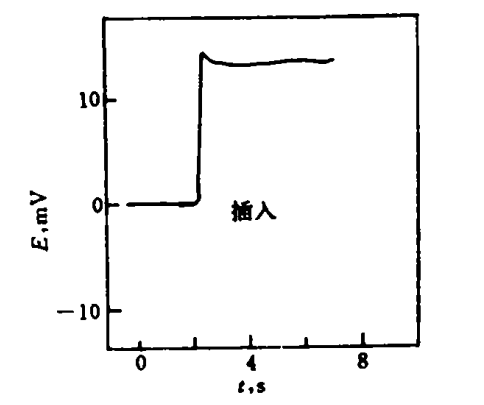
低氧勢焙燒預處理難浸金礦
研究背景
隨著世界上易浸金礦資源的日漸枯竭,難處理金礦中金的處理愈來愈受到重視。我國難處理金礦資源十分豐富,已探明的黃金儲量中,30%屬難處理金礦,各種難處理金礦金儲量1000多t,潛在經濟價值800餘億元,且仍在逐年增加。這類金礦直接浸出,金的回收率只有2%~40%,沒有經濟效益,大部分成為呆礦。越來越多的黃金生產企業隨著生產時間的延長,易處理礦石逐漸減少,必須轉向難處理礦石。因此對技術和經濟上都可行的難處理金礦回收新技術的需求非常迫切。
焙燒是難處理金礦的預處理方法之一,套用較廣泛。但是,通常的焙燒作業能耗高,勞動條件差,對環境污染大,投資和經營費用高,且金的提取率(我國平均80%~85%,國外平均89%)也不高。常規焙燒預處理難浸金礦石技術需要改進。
工藝原理
焙燒預處理的目的是使難浸金礦中的金與包裹體解離,使金在氰化時能直接與浸出劑作用,從而提高金的回收率。由固體材料界面性質可知,固體材料界面破壞分為力學破壞和熱力學破壞兩類,化學破壞屬熱力學破壞,機械應力和熱應力等破壞屬力學穩定性破壞。熱應力既能由界面相鄰兩相物理性能(膨脹係數、彈性模量)的差異引起,也能由非均勻溫度場產生,相變也能引起應力。熱力學穩定性的破壞,包括溶解、擴散、化學反應等多種類型,並受界面幾何形狀和環境條件的影響。
由斷裂力學可知,材料應力腐蝕或腐蝕疲勞破壞可在任何環境下發生,並且在溫度升高時,材料往往發生脆性斷裂。腐蝕首先從晶界開始,而不是在晶粒表面均勻地發生。滕布和霍夫曼的晶界管道模型表明,氧化分解從晶界深入到核心處所需氧化的元素結點少,如圖3所示,而且晶界、相界上位錯、扭折、台階、空穴等缺陷多,自由能高,反應活性大,有利於擴散,因而,受控的焙燒反應,就以晶界(相界)為反應前沿和通道,由(砷)硫顆粒外部向內部進行選擇性氧化。
圖3 計算機模擬得到的鋁[100]的三種傾轉晶界
![圖3 計算機模擬得到的鋁[100]的三種傾轉晶界 圖3 計算機模擬得到的鋁[100]的三種傾轉晶界](/img/7/202/nBnauQjZ2UGNkFGOzcTZyQWZ2QzNwIDN2ATZ1gTM2gTOxgjZxUDMiJWMyI2LtVGdp9yYpB3LltWahJ2Lt92YuUHZpFmYuMmczdWbp9yL6MHc0RHa.jpg)
包裹金的晶粒中的雜質比一般純材料更多,因此引起位錯塞積多,熱應力引起位錯反應產生斷裂核心也多。通過控制焙燒參數,產生適宜的熱應力,破壞礦物的熱力學穩定性條件,沿晶粒邊界誘發粒間裂紋和裂隙生成,使粒間裂紋和裂隙以及礦粒內部缺陷擴展,將金暴露,形成浸出劑與金髮生作用的條件。
實驗結果
焙燒溫度過高,會出現局部物料過燒,使已經解離的金又被焙燒形成的赤鐵礦包裹,生成的孔隙又被燒結封閉,形成“裂紋閉合”,造成金的“二次難浸”。硫酸化程度最高即氧化最好的試樣,金的浸出率僅為44.4%,比直接氰化金的浸出率還要低。在低溫成型焙燒條件下,金的包裹體形成裂紋和裂隙,破壞性的分解以及沿晶間和相界的腐蝕氧化起主要作用,硫的氧化率僅有9.85%~10.9%。低的硫氧化率,傳統焙燒方式獲得高的金浸出率是不可能的。在300℃以上FeS2分解發生相變,FeS2→FeS+1/2S2,FeS2晶體就會產生裂紋和裂隙。在熱應力的作用下,裂紋、裂隙會進一步的萌生和擴展,產生了浸出劑可與金髮生作用的反應通道,提高金的浸出率。
圖4 低溫成型焙燒與細磨處理在使金包裹體發生變化的比較
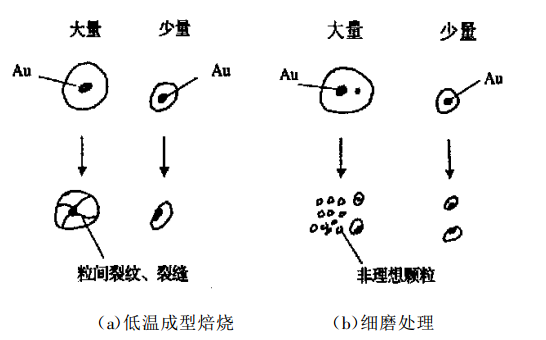
雖然FeS2在300℃~500℃會顯著氧化,但團礦降低了氧在料中的傳遞,形成局部的低氧勢,阻止了FeS2的氧化,減少SO2產生,降低了環境污染和物料隨煙氣損失。與細磨方法相比,金包裹體發生變化如圖4所示。
表2 焙燒前後的粒度變化
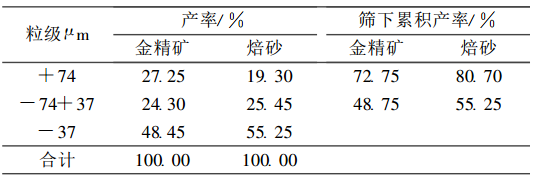
與原料金精礦相比,焙砂中-74μm粒級的含量僅增加約8%,達80.7%,如表2所示。說明預處理過程是以造成粒間裂紋、裂隙為主,晶粒的解離僅占很小的比重。