旋塗是旋轉塗抹法的簡稱,是有機發光二極體中常用的製備方法,主要有設備為勻膠機。旋塗法包括:配料,高速旋轉,揮發成膜三個步驟,通過控制勻膠的時間,轉速,滴液量以及所用溶液的濃度、粘度來控制成膜的厚度。電子工業中,基片垂直於自身表面的軸旋轉,同時把液態塗覆材料塗覆在基片上的工藝。
基本介紹
- 中文名:旋塗
- 外文名:spin coating
- 全稱:旋轉塗抹法
- 別稱:旋轉塗覆
- 釋義:依靠工件旋轉時產生的離心力作用
- 優點:易於獲得密度較大的塗層
簡介
塗料
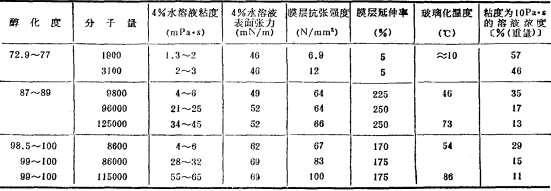

旋塗塗膜厚度
旋塗玻璃法
概況
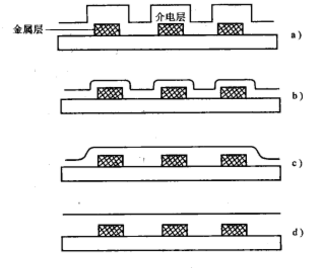
旋塗是旋轉塗抹法的簡稱,是有機發光二極體中常用的製備方法,主要有設備為勻膠機。旋塗法包括:配料,高速旋轉,揮發成膜三個步驟,通過控制勻膠的時間,轉速,滴液量以及所用溶液的濃度、粘度來控制成膜的厚度。電子工業中,基片垂直於自身表面的軸旋轉,同時把液態塗覆材料塗覆在基片上的工藝。
旋塗是旋轉塗抹法的簡稱,是有機發光二極體中常用的製備方法,主要有設備為勻膠機。旋塗法包括:配料,高速旋轉,揮發成膜三個步驟,通過控制勻膠的時間,轉速,滴液量...
勻膠機又稱旋塗機、甩膠機、旋轉塗膠機、旋轉塗膜機、旋轉塗層機、旋轉塗布機、真空鍍膜機,其總體由在國際上SOL-GEI技術領先的美國凱美特技術公司(CHEMAT ...
光刻膠旋塗單元包括一個可以旋轉的樣品台(spin table)和幾個噴嘴(nozzle),負責對晶圓表面做光刻膠塗覆,實現指定的厚度和均勻性。...
近十年來,各種石墨烯基膜相繼被開發並用於膜分離領域,目前石墨烯基膜的製備方法主要包括真空抽濾法、噴/旋塗法、層層自組裝法以及共混法。1真空抽濾法...
為此,研發了含Si的光刻膠,這種含Si光刻膠被旋塗在一層較厚的聚合物材料(常被稱作Underlayer),其對光是不敏感的。曝光顯影后,利用氧電漿刻蝕,把光刻膠上...
而常見的製備高分子薄膜的方法有旋塗法、絲網印刷法、浸塗法、噴墨列印法及噴霧熱解法等。高分子薄膜製備製備方法介紹 編輯 高分子薄膜製備旋塗法 ...
簡介電腦控制,可預置並記憶轉速,控制轉盤均勻加速;旋轉時間預置,到時,控制轉盤均勻減速。勻膠機spincoater旋塗儀(司樂機器) 轉速高:300–8000轉/分.(100轉/步,...
在製備過程(熱蒸發-沉積,或者溶液旋塗法)兩層膜總會形成一種互穿的結構,從而界面有較大的面積。在給體材料的體相中產生的激子,通過擴散可以較容易地到達兩種材料...
聚合物大多由小的有機分子以鏈狀方式結合在一起,以旋塗法形成高分子有機發光二極體。它與AMOLED相對應。中文名 高分子發光二極體 外文名 PLED ...
抗反射塗層(Anti-Reflection Coating, ARC)是旋塗於光刻膠與Si襯底界面處以吸收光刻反射光的物質。...
所採用的膠液常常是易揮發的,同時也有可能被蒸發掉,因此,旋塗速度越高,所得到的薄膜越薄,當然薄膜的厚度也取決於這種膠液和其比兌的試劑混合後的粘度和濃度等...
MLD相對於傳統的有機聚合物薄膜沉積工藝(旋塗,熱蒸發)而言,薄膜厚度精確可控(控制循環數),厚度更均勻、階梯覆蓋率和保型性更好、重複性更可靠。...
coating 在基片表面蓋上一層材料,如用浸漬、噴塗或旋塗等方法在基片表面覆蓋一層光致抗蝕劑。 具體說來, 塗覆就是在PC表面塗覆一層物質,用來增強抗腐蝕能力、...
1、 旋轉速度:轉速的快慢和控制精度直接關係到旋塗層的厚度控制和膜層均勻性。如果標示的轉速和電機 的實際轉速誤差很大,對於要求精密塗覆的科研人員來說是無法獲得...
◆勻膠機旋塗儀系統該設備是科研製備理想的勻膠機旋塗儀,由天然聚丙烯或特氟龍材質構造有216毫米,318毫米和370毫米三種腔體大小可選,可選擇用於濕法刻蝕或者手套箱...
三防漆噴塗機又稱三防漆塗膠機、三防漆噴膠機、三防漆噴油機,三防漆塗覆機等,是專門對流體進行控制,在PCB表面蓋上一層三防漆,如用浸漬、噴塗或旋塗等方法在PCB...