多功能鋼包處理站是指在鋼包內完成多種爐外精煉功能的專用工藝與設備的組合。現代鋼包處理站配備有進行鋼液真空處理、鋼包吹氬處理、鋼液合成渣處理、噴射冶金處理、餵線法處理、鋼包頂渣控制等多種工藝所需設備系統。
基本介紹
- 中文名:多功能鋼包處理站
- 工藝布置:需遵循3個原則
- 配備有:進行鋼液真空處理鋼包吹氬處理等
- 加熱設備包括:電弧加熱、餵鋁線吹氧加熱
簡介,多功能鋼包處理站設備,多功能銅包處理的工藝技術,處理站的工藝布置原則,處理效果及其分析,總結,
簡介
多功能鋼包處理站是指在鋼包內完成多種爐外精煉功能的專用工藝與設備的組合。現代鋼包處理站配備有進行鋼液真空處理、鋼包吹氬處理、鋼液合成渣處理、噴射冶金處理、餵線法處理、鋼包頂渣控制等多種工藝所需設備系統。它們包括:真空系統,吹氬系統,餵線機,噴吹設備,加熱設備(電弧加熱、餵鋁線吹氧加熱、等離子弧加熱等)以及加渣料和添加合金設備(運送、貯存、稱量等)。
“多功能爐外處理設備及技術研究”是“七·五”國家重點科技攻關項目,公司組織科研、設計翻造與生產部門聯合進行了攻關。1985年轉爐車間建成吹氳噴粉系統,1988年增建了塊狀材料加料系統,1990年引進裝備了DV41000型直讀光譜分析儀、DEs一3型單線餵線機和氣動擋渣器等設備,聯合組成了先進的爐後多功能鋼包處理站。各項功能可單一,可多項配合,都是線上使用。經生產試驗,現已實現對鋼水測溫、取樣、吹氬、噴粉、廢鋼調溫,合成渣渣洗、覆蓋保溫、成分微調、餵線等處理的多項功能。它是冶煉手段的延續,可簡化爐前工藝、縮短冶煉時間、理順生產流程,是保證鋼質、淨化鋼液的手段,特別是提供合格鋼水對穩定連鑄生產、提高拉成率和連鑄連連比已成為不可缺少的手段。
多功能鋼包處理站設備
1.加料系統
該套裝備設在2號、3號轉爐出鋼線後方,兩座轉爐共用。
2.Des-3型單線餵線機
由導管、主機和附機(包括線盤)組成。安裝在3號轉爐爐後距鋼包上口3.1m的上方專用小平台上。
3.吹氬噴粉系統設備
組成如圖2所示,主要技術參數見表2。
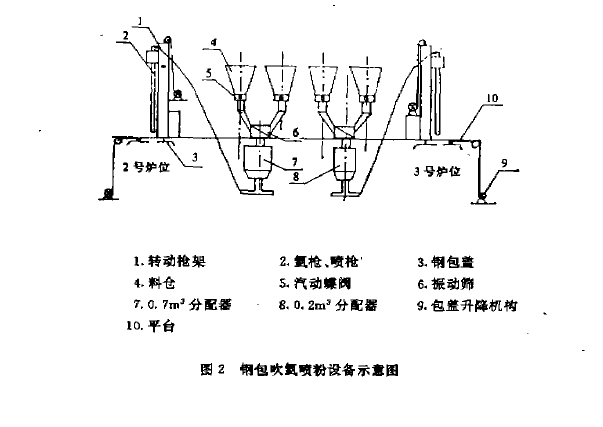

4.快速分析顯示系統
DV41000型直讀光譜分析儀安裝在轉爐車間 完成爐前及處理過程中的成分分析,分析結果快速傳送,可顯示於多功能處理站電視螢幕上。
5.控制系統
加料(成分徽調台金、保溫荊、小廢鋼、合成渣等)、吹氬、噴粉、餵線等各硬處理功能的操作控翻身成俸系,互不干擾。加料系統為按鈕操作,整個加料過程的運轉狀況可通過模擬顯示盤進行顯示和觀察。吹氬系統分室內和室外兩地操作。由切換開關控制。噴粉系統可實現身動操作。其它控制,諸如吹氳槍、噴耪槍、鋼包蓋升降,鋼包車行走,槍架旋轉蕁均為手動或點動操作。
多功能銅包處理的工藝技術
1.工藝流程(見圖3)
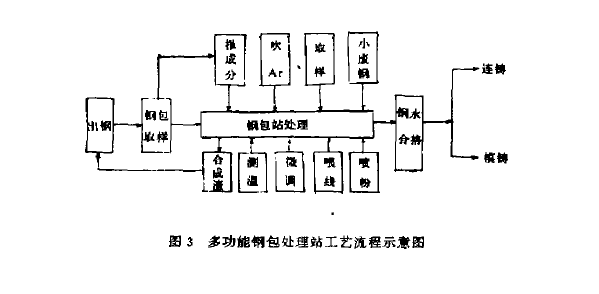
2.原材料(見表3)
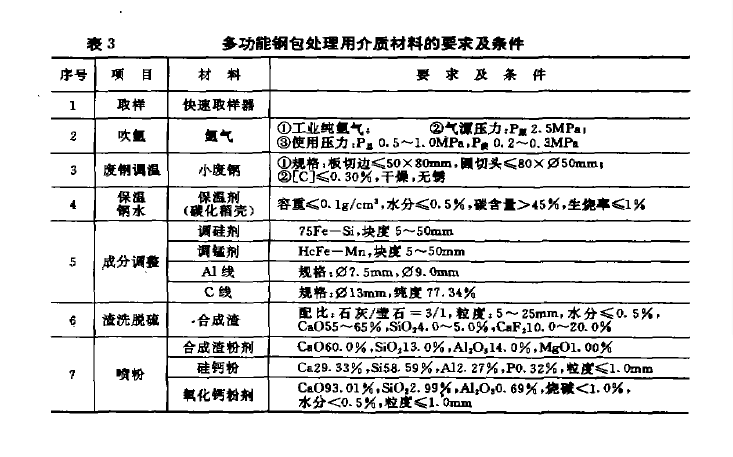
3.工藝要點(見表4)
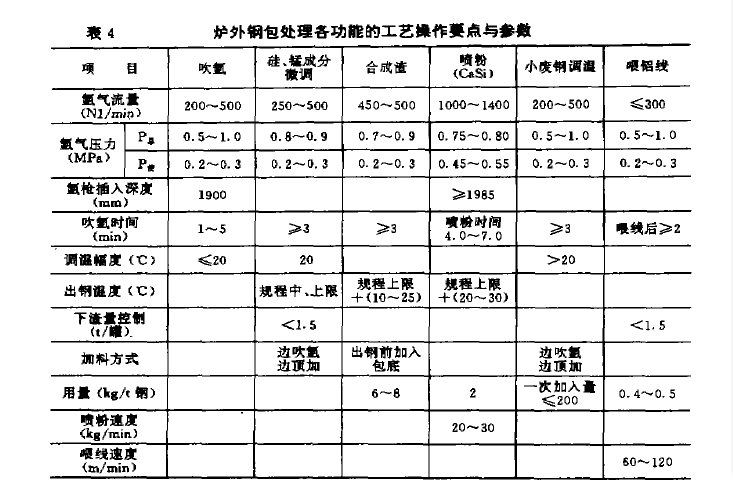
處理站的工藝布置原則
(1)保證整個工藝流程通暢,各工序的設備順序布置,避免鋼包的往返運送;
(2)儘量縮短各工序間的距離,兼顧操作和維修的方便;
(3)真空設備的噴射泵、管道、閥門等是個龐大體系,為節省投資一般不設在主廠房內,而是安裝在緊挨著主廠房的副跨內的10m高平台上,真空系統管道的安裝必須便於維修和清理。多功能處理站通常為三層高架結構,地面部分放鋼包車或設放置鋼包車的大坑;二層為操作平台,與煉鋼操作平台相接或在煉鋼爐斜對面,平台上有操作控制室,各種控制、檢測和顯示儀表、顯示屏等均設於此;最高一層平台設定加料系統(包括真空加料倉)。
處理效果及其分析
1.測溫、取樣
多功能處理站接收鋼水後,吹氬一分鐘再測溫、取樣。以連測兩次溫度的差值≤5℃時作為爐後溫度。採用快速取樣器取鋼樣--是決定連鑄是否開包,以保證連鑄鋼成分合格和穩定;二是配合科研工作。溫度測成率和取樣成功率均已穩定在98% 以上。爐後吹氬及其它處理結束後測得的溫度作為鑄鋼溫度,同時測量渣層厚度。渣樣按不同要求勺取。
2.吹氬
鋼包吹氬的主要作用是均勻鋼水成分和溫度,去除鋼中夾雜物以及氫、氧、碳。經1990年對矽鋼調查,吹氬去除夾雜率達76.32% ,平均夾雜含量為63ppm。同時,吹氬是實麓鋼包處理站各項處理功能的必需配合手段,吹氬技術直接影響各項功能的處理效果。1991年吹氬率達98.35% ,其中連鑄為100%。平均每爐吹氬時間為3.15min。
3.溫度調整
鋼水溫度調整採用兩種方式,即調溫幅度<20℃時採用吹氧調溫;而>20℃時採用加小廢鋼吹氬攪拌複合調溫。
4.鋼水保溫
爐外處理結束,把保溫劑(炭化稻殼)散加在鋼包內,正常加入量為0.4kg/t鋼,當鋼水溫度偏低或等澆鑄線路時加入量為0.6kg/t鋼,以減少鋼水熱損失,穩定過程溫度,保持頂渣流動性,減少低溫廢品和回爐。
5.鋼水矽、錳成分微調
該工藝對準確控制鋼中矽 錳含量,減少廢品及改判品,簡化爐前台金化操作,節約鐵合金有重要作用。當調si劑(75Fe—Si)、調錳劑(高碳Fe—Mn)加入量為0.50~ 2.00kg/t鋼時,可使鋼水分別增矽、增錳0.01~0.13% 和0.01~0.12%,經常使用的調整範圍為si≤0.06% ,Mn≤0.08% ,要求吹氬站鋼樣[Si]、[Mn]含量低於規格下限加0.04% 的爐次須進行調矽和/或調錳處理。
6.餵線工藝
餵線工藝的主要冶金特點之一是合金元素在鋼液內部進行化學反應和熔化,而使其有較高的和穩定的利用率和回收率。
餵鋁線處理鋼種以鋁靜鋼為主。可節鋁0.65kg/t·鋼,除矽銅不進行餵鋁線處理外,其餘鋼種餵Al在0.01~0.O4%內可調。可完全取代出鋼加鋁,並可節鋁0.5kg/t鋼。
7.吹氬噴粉脫硫
使用矽鈣粉和石灰粉對矽鋼、GCr15、20g等鋼種進行了噴粉脫硫處理。重點對矽鋼進行了加覆蓋合成渣吹氬噴粉處理,達到了脫氧、脫硫的目的,脫硫率最高可達76.47% ,平均為66.84% ,成品磕含量最低達到0.004% ,平均為0.0063% 從而提高了矽鋼的潔淨度和電磁性能。
8.合成渣渣洗
鋼包加固體粒狀鈣基合成渣吹氬工藝的優點是成本低,工藝簡單,具有較好的脫硫效果。鋼水原始磽含量[So]、鋼水溫度及吹氬時間、合成渣加入量及覆蓋渣渣量和組成是影響脫硫效果的主要工藝因素。
總結
1.轉爐爐後多功能鋼包處理站的優點是設備簡單、布置緊湊、操作方便、運轉穩定.集多功能與一體。保證了現代化煉鋼技術發展的需要。
2.各項功能可單一、可多項配合,都是線上使用,工藝技術實用性強。可對轉爐目前生產的優質碳結鋼和低台金鋼進行多種功能的線上處理。包括測溫、取樣、吹氬、廢鋼調溫和鋼水保溫等項處理技術已納入大生產,成為轉爐煉鋼生產流程中不可缺少的工序環節。
3.多功能鋼包處理的吹氬噴粉脫硫率平均為66.84% ,鋼水Si、Mn的在0.10%內可調,Si和Mn的回收率平均為52.2O% 和78.2O% ,餵鋁線在0.01~ 0.04%內可調.鋁的回收率為52.20% ,比包內加, 鋁提高一倍i餵碳線在0.01~0.05% 內可調,碳的回收率平均為86.80% ,廢鋼吹氬調溫在30℃範圍內可調;合成渣脫硫率平均為40.13% 。
4.運用多功能鋼包處理站工藝技術有利於簡化爐前工藝、縮短冶煉時間 充分發揮轉爐大量生產優質鋼的設備能力。並能提高鋼水質量、減少成分不合格品、提高內控率、擴大品種、降低消耗.為後部工序提供台格鋼水、配台連鑄生產,具有一定的直接經濟效益和社會效益。