產生背景
作為企業質量管理行業領先行業的汽車行業,在質量管理領域最早就已經形成了標準的質量管理五大工具(APQP、PPAP、FMEA、MSA、SPC),汽車行業在產品研發管理、生產工藝水平、質量管理等方面都在製造業起著帶頭作用。隨著汽車行業PLM、CAPP、ERP、DMS、OA等系統的導入,大幅度提升了企業產品研發創新能力及成本管控等能力。相比之下無處不在的質量管理層面依然停留在紙面、手工作業的模式,嚴重阻礙企業業務過程管控及產品質量管理能力的提升。自2007年開始以海馬汽車、長豐汽車等企業開始嘗試展開研發質量管理、供應商質量管理、裝配過程質量管理、售後質量管理、產品質量追溯管理、計量器具管理、試驗管理、目標管理的信息化套用,並取得了實際的管理效益,QIS質量管理信息系統繼而誕生。
設計理論
基於ISO9001/TS16949 PDCA持續改進機制:
QIS質量管理信息系統基於ISO9001/TS16949體系要求展開功能梳理,將質量體系的PDCA模型持續改進機制融合到系統業務邏輯中,實現ISO體系持續改進機制的系統固化。實現了嵌入了TS五大手冊及QC七大手法等成熟的質量工具和方法。
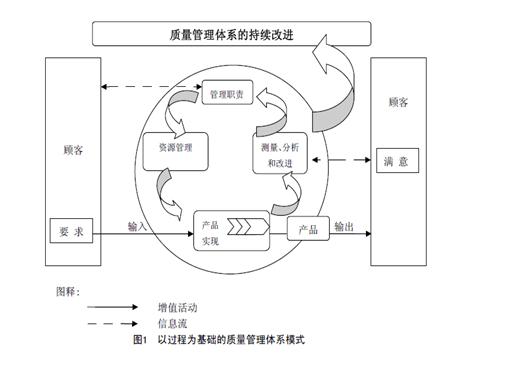
功能介紹
以汽車行業為代表的QIS質量管理信息化建設,在研發質量管理、供應商管理、整車裝配過程質量管理、售後質量管理、整車追溯、計量器具管理、試驗管理、目標管理及五大工具(APQP、PPAP、FMEA、MSA、SPC)套用方面都展開了實際信息化推廣套用。QIS質量管理信息系統繼承了汽車行業先進的管理理念、管理模型、方法及實施經驗。汽車行業QIS質量管理信息系統套用水平代表當今市場QIS質量管理信息系統的最高水平。以下以安必興汽車行業QIS質量管理信息系統為例展開系統功能模組介紹:
系統功能架構
⑴ 管理決策層包含: 企業管理看板、 管理KPI月度考評、 過程能力考評、 質量監控 計畫監控
⑵ 過程管理層包含:
過程管理是基於PDCA改進模型展開的功能設計:
P:計畫管理、 目標管理
D:產品先期質量策劃(APQP)、 進貨檢驗管理、 供應商管理、 製程質量管理、 售後質
量管理、 統計過程控制(SPC)
C:產品試驗管理、 產品評價管理、 顧客滿意度管理、 質量成本管理、 內部審核管理、
管理評審
A:質量改進管理
⑶ 資源管理層包含:
培訓管理、人員資質管理、 計量器具管理、 設備/設施管理、 追溯管理、 異常履歷、 體系
檔案管理
⑷ 平台支撐層包含:
管理技術支撐:統計過程控制(SPC)、 測量系統分析(MSA)、 產品先期質量策劃(APQP)、 生產件核准(PPAP)、 產品時效模式分析(FMEA)、 QC七大手法、 質量管理模型庫(供應商評價模型、抽樣標準、判異準則、質量成本構成表、顧客滿意度調查模型等)、 質量算法包:CPK值等30多個統計量算法、 基礎維護及自定義:計畫模板自定義、採集內容自定義、供應商評價模型自定義等
IT技術支撐:單點登錄、 許可權管理、 工作流管理、 任務管理、 表單管理、 報表管理、 委託管理、 數據字典管理
⑸ 系統集成層:
1:OA集成:待辦、郵件、組織機構及用戶等
2:ERP集成:產品BOM、物料BOM、工序等
3:供應商管理系統:供應商名稱等
主要業務功能
(1)管理儀錶盤系統主要包括功能:
建設質量目標看板,展開公司級、公司級質量目標項目月推移圖趨勢呈現自動生成公司月度質量目標達成情況考核表展開質量目標監控展開進貨檢驗、製造過程、售後過程等過程質量監控展開公司級重大計畫項目進度監控(後期拓展)展開公司級質量改進項目過程進度監控管理儀錶盤套用模型示例如下:
(2)進貨檢驗管理系統主要包括功能:
通過與SAP集成,實現檢驗任務的通知實現檢驗員與物流關係維護,展開檢驗員任務管理。展開物流、零部件檢驗標準維護。展開抽樣計畫維護展開抽樣方案加嚴、正常、放寬及免檢的維護及人工干預基於來料信息,自動觸發檢驗任務,並動態獲取物流、零部件檢驗項目、方法、檢驗數量等信息。展開進貨檢驗記錄信息錄入,並自動判標。支持進貨檢驗不合格處理進貨檢驗合格、不合格狀態回寫SAP,實現入庫流程的真正閉環。展開任意供應商、物流進貨檢驗合格率動態統計展開供應商來料不合格信息查詢展開供應商來料不良監控。進貨檢驗管理套用模型示例如下:
(3)供應商管理子系統
供應商管理系統主要包括功能:
展開供應商檔案信息,聯繫人信息、三證信息、提供產品信息等維護展開供應商準入流程的控制,基於物料重要的展開準入管控根據準入階段變化動態更新物料準入狀態支持展開準入現場審核標準維護現場審核報告自動評分及是否“通過”的自判定支持展開樣件鑑定、小批鑑定業務,以及樣件鑑定、小批鑑定次數控制展開供應商業績評價模型維護,供應商評價時支持根據物料類型或物料重要的或具體物料展開供應商評價。展開供應商評價評分評級標準維護,並根據評分自動展開評級及排名支持供應商評分紅黃牌規則維護,並自動實現供應商評分結果紅黃牌監控展開供應商年度監察計畫制定、監察報告、監察計畫跟蹤、計畫達成率統計等功能。支持展開供應商開發進展、評價紅黃牌等供應商綜合信息查詢。供應商管理套用模型示例如下:
製造質量管理系統主要包括功能:
支持整機各塗裝檢驗、調試檢驗、入庫檢驗、發貨檢驗、整機評價等不良BOM維護,並支持不良嚴重度、扣分值維護,並基於業務邏輯實現整車一次合格率的自動統計。考慮到車間檢驗人員的便捷性和效率,檢驗信息錄入採集將採用無線PDA方式採集。展開關鍵檢驗工序檢驗信息線上採集,基於系統集成、條碼、離線PDA等技術實現現場整機檢驗信息的高效採集。實現檢驗不良項目的返工控制,實現不良原因、措施等返修信息的記錄,並形成返修經驗庫。同時與SAP系統展開集成,實現返工過程控制,確保整機所以不良返工合格方可以辦理入庫或發貨。展開塗裝檢驗、調試檢驗、入庫檢驗、發貨檢驗過程檢驗不合格TOP 10、不合格柏拉圖分析支持製造不合格品處理流程管理,並支持返工、讓步使用、報廢子流程展開。支持整機製造過程狀態查詢,在哪個工序?檢驗發現不良項目?不良返工進展情況?再檢是否通過? 支持展開各車間檢驗發現不良數、嚴重度分布等統計分析製造質量管理套用模型如下:
售後質量管理系統主要包括功能:
支持導入或系統錄入售後理賠單,並形成理賠單台賬查詢展開售後舊件返回返回跟蹤管理,實現舊件返回過程管控。展開舊件返回後的責任鑑定工作,並支持對責任鑑定未完成舊件展開過濾查詢。索賠舊件返回後,完成索賠鑑定後可自動生成對應的索賠通知單。展開索賠鑑定及並生成二次索賠。展開理賠信息損失分析、整機型號分布分析、零部件分布分析、早期故障率分析等質量統計分析,為整機質量可靠性改進提高有效輸入。展開抱怨客戶分布、產品分布及問題點等分析展開零部件售後不良PPM動態統計及排名售後質量管理模型示例如下:
改進管理系統主要包括功能:
支持展開質量進貨檢驗、製造過程、售後過程等業務過程的質量監控,並基於質量監控預警規則展開線上預警,也可以直接觸發糾正預防措施或預警訊息通知支持糾正預防措施單工作流過程審批,展開過程審批任務管理,並展開任務通知。也支撐根據企業改進模式,如8D、DMAIC、QCC等改進模式展開對應表單及業務流程開發。支持質量改進過程跟蹤管理,隨時展開當前單據狀態查詢及流程審批進度查詢基於質量異常處理過程,實現改進經驗庫的固化,對典型異常問題點的原因、糾正措施、預防措施展開固化和查詢。展開改進按時完成率統計,支持按責任部分展開統計展開異常來源分析、發生工序、產品分布、責任單位分布、問題分布分析等。支持基於系統展開改進效果驗證質量改進管理套用模型示例如下:
追溯管理子系統主要包括功能:
通過與MES系統的集成,實現整機裝配零部件信息的導入和採集。並與QIS系統質量信息一併,實現整機產品質量檔案的系統構建。產品質量檔案信息主要包括功能:
支持展開產品零部件配置信息的集成展開整機檢驗信息、不合格信息及零部件批次等信息的整合,並支持展開整機信息的聯查。支持依據整機號展開整機檔案信息的正向查詢支持展開異常零部件批次(或唯一號)查詢對應整機號明細查詢。
套用價值
業務過程管控能力提升:
產品質量管理前延到新產品研發過程,實現研發項目階段、輸入輸出標準化固化及研發問題點管理規範化,進而促進研發過程質量管理能力提升;
通過嚴謹的供應商準入流程、供應商評價紅黃牌機制及進貨檢驗合格率監控等,實現供應商管理水平全面提升,促進供應商質量及物料質量提升,
通過與ERP系統集成,實現產品不良返工過程控制,杜絕不良未經返工再檢合格即入庫的失控情況發生。
製造過程合格率及CPK能力監控,實現製造過程質量管理能力的提升。從合格控制轉向過程能力管控;
通過對售後零部件PPM排名、監控,第一時間展開零部件售後產品可靠性監控;
通過監控預警機制,支持“質量閥”及“拉燈系統”管理理念落地。
將SPC統計學技術真正運用與產品質量控制過程中,實現產品質量控制從合格控制邁向過程能力控制
促進管理效率提升
通過與ERP系統集成,實現物料入庫流程最佳化。入庫周期縮短0.5天以上;
通過產品質量信息的系統採集和整合,實現追溯、跟蹤效率提升90%以上;
基於改進過程線上互動,實現供應商改進周期縮短3天以上。內部質量改進周期縮短1天以上;
通過系統實現核心質量管理數據的自動匯總、統計,實現月管理例會數據統計提前5-10天;
基於靈活的自定義數據統計分析體系,實現柏拉圖、直方圖、控制圖等QC分析方法的全面套用,打造穿透的數據體系,數據統計及驗證效率提升90%以上。
效益提升
新產品研發質量保障能力提升,批量生產時不良率降低、市場故障率減低,失敗成本減少;
供應商管理能力提升,促進來料質量提升,減少停工待料損失;
製造過程合格率及CPK能力指數提升,實現不良率降低減少失敗成本損失;
通過對來料檢驗、製造過程及售後質量展開預警規則及監控,實現異常後第一時間展開管理干預,避免異常損失擴大。
通過對內外部損失責任單位分布、不良項目分布、產品型號分布、工序分布等有效分析和責任量化,確保責任明確、波動監控,進而促進損失遞減;
產品質量異常時通過精準追溯,確保異常物料、產品精準鎖定,避免擔心不良流程而擴大返工產品數量,
隱形問題顯性化
研發項目階段進展、評審問題點及改進進展隨時查詢
實現任一供應商、物料合格率動態統計,來料不良及業績評分扣分隨時查詢
實現製造過程任一產品型號、車間、生產線、工序合格率動態統計,及不良柏拉圖分析
實現售後不良項目及零部件PPM排名之禍首分析
內外部損失成本之損失來源產品分布、責任部門分布、不良項目分布隨時分析,
各部門目標狀況狀況動態掌控,隨時了解各目標達成率及未達成項目
實現全面提升標準化水平
1:實現產品不良描述標準化
2:實現業務過程之管理模型、業務表單、業務流程、統計報表標準化
3:基於業務過程及目標管理要求,展開預警監控機制等管理機制的標準化固化
4:基於業務過程管理需要建立目標體系、過程業績統計方法標準化、分析方法標準化
5:質量目標、異常監控實現自動預警,並展開跟蹤管理,實現PDCA模型的有效固化