鐵浴法是在鐵水熔池中完成氧化物還原的工藝。在反應器中原料礦石融入爐渣熔池與鐵水發生還原反應。流態化的煤粉由氧氣吹人鐵水熔池為還原反應提供還原劑;煤粉的氧化燃燒為熔池提供反應所需的熱能。鐵水中的碳始終處於飽和狀態,具有較高的活度。
基本介紹
- 中文名:鐵浴法
- 外文名:Iron-Bath Process
- 定位:鋼鐵工業的前沿技術之一
- 分類:工業
鐵浴熔融還原反應,過程概述,還原反應過程,鐵浴一步法流程,鐵浴二步法流程,COIN流程,HISMELT流程,AISI流程,DIOS流程,
鐵浴熔融還原反應
過程概述
現採用的鐵浴熔融還原法是在轉爐型的反應器內進行的,如圖所示。
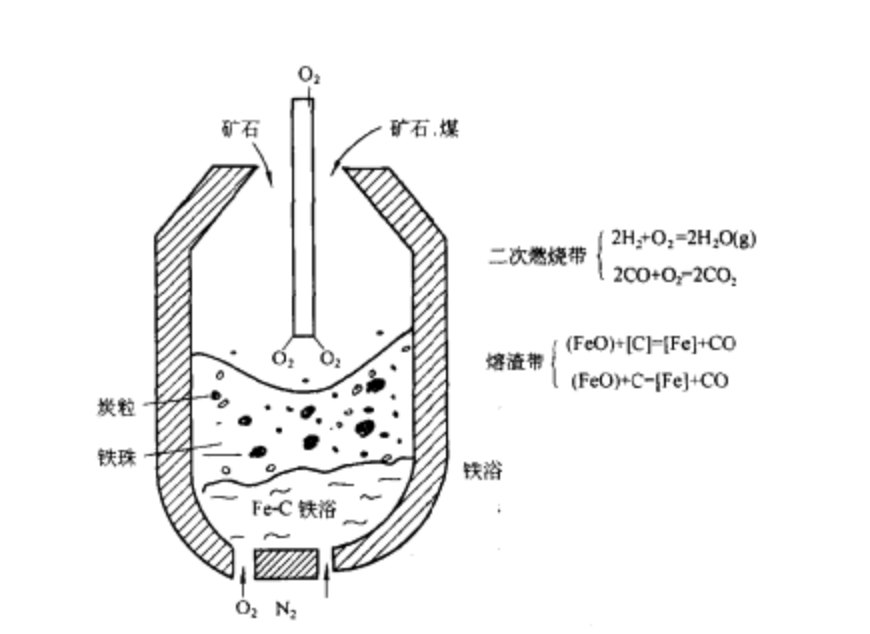
類似於轉爐煉鋼的反應器有垂直式和水平式兩種,經爐外加熱及預還原的礦石和煤加入或噴射送入爐內熔渣帶內。礦石在熔渣中溶解成(FeO),而後被渣中的煤粒及含碳飽和的鐵珠狀液滴的碳所還原的鐵則進人鐵浴內。還原生成的CO及煤放出的揮發物(主要是H)在熔渣帶上空被噴入的氧或空氣二次燃燒。放出的熱能用以加熱熔池及反應所需的熱能。
二次燃燒的產物包含有CO、CO2、H2、H2O等,經清洗後,送入另一反應器內預熱及預還原鐵礦石。
還原反應過程
熔融還原法的主要反應是氧化鐵(FexO)的熔態還原。經部分預還原的礦石溶解於熔渣中,為其內的固體炭粒及碳飽和的鐵珠的碳所還原。這種鐵珠是由爐底噴氣入鐵浴內,使含碳飽和的鐵液分散成鐵珠,進入熔渣內形成的。兩種還原反應的作用大約是相等的,即兩者並行,總反應的速率為此二還原反應速率之和。由於炭粒和鐵珠與熔渣的接觸面積很大,遠大於金屬液-熔渣間的平面接觸,所以總還原反應的速率很高,遠高於高爐內氣-固逆流相間反應的速率,特別是渣中炭粒和鐵珠的量很大時。
1.溶解於熔渣的(FeO)與鐵珠內(C)的反應:


鐵浴一步法流程
鐵浴一步法工藝生產鐵水,主要用於處理鋼鐵廠粉塵。開發者是莫斯科鋼鐵學院和鋼鐵設計院。1990年在新列別茨克建成一座設計能力為每年30萬噸的工業試驗裝置,原理如圖所示。
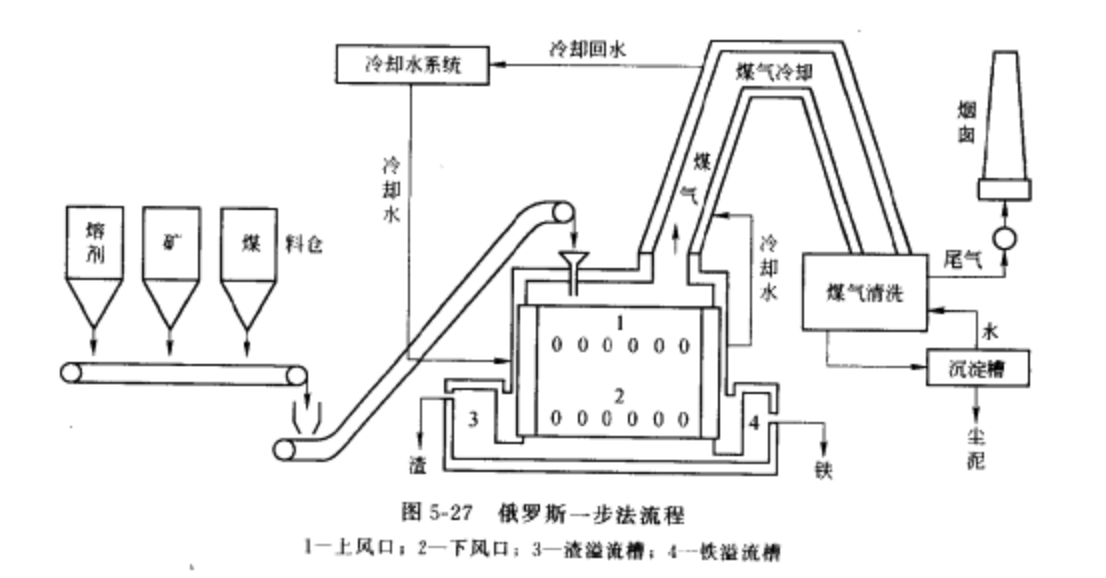
工業試驗裝置呈矩形,長度為8m,氣相空間部分較寬,熔池部分較窄。熔池面積為20m2(2.5m×8m)。爐頂和爐牆全部採用水冷掛渣爐壁。兩側爐牆在兩個不同高度上對稱設定兩排風口。較低的一排稱為下風口,較高的一排稱為上風口。在爐體兩端分別設有熔渣溢流槽和鐵水溢流槽。爐頂設有加料斗和用於煤氣餘熱回收及冷卻的餘熱鍋爐。
未經還原的含鐵料與煤和熔劑一起通過爐頂料斗加入熔煉爐。下風口位於渣層,吹人含氧55%~60%的富氧空氣,強烈攪拌渣層,使熔渣形成泡沫狀。穿過渣層的高溫富氧空氣與煤產生劇烈的燃燒反應,生成大量還原性氣體,進人氣相空間。上風口位於氣相空間,吹入氧氣,支持二次燃燒。二次燃燒率控制在50%左右。二次燃燒產生的熱量一部分傳遞給爐料,一部分傳遞給熔池,其餘的由煤氣攜帶排出爐外。高溫煤氣出爐後,首先進入一個餘熱鍋爐煤氣冷卻器,進行問接水冷。再經清洗後排放。鐵水溢流槽的內部開口位置在渣線以下,僅容鐵水通過。出鐵口位於鐵水溢流槽外壁。爐渣通過熔渣溢流槽內部開口通人溢流槽內,然後通過渣口排出爐外。
鐵浴二步法流程
COIN流程
COIN(Coal Oxygen Injection)是德國Krupp開發的熔融還原流程。開發工作是在一個3t試驗轉爐上進行的。研究工作自20世紀70年代中期已經開始,原目的是利用煤氧噴吹放出的熱量熔煉廢鋼或其他金屬鐵料。後來,為了利用熔煉過程發生的高溫強還原性煤氣,計畫在熔煉爐的基礎上配置一台還原豎爐或者還原流化床,形成一個使用廣譜煤種,適應小規模生產的二步法熔融還原技術,以備Krupp對外進行技術出售。從文獻資料看,開發者準備以豎爐型還原器作為該流程第一代的配置,以流化床型還原單元作為最終開發目標。COIN流程(豎爐還原)原理如圖所示。
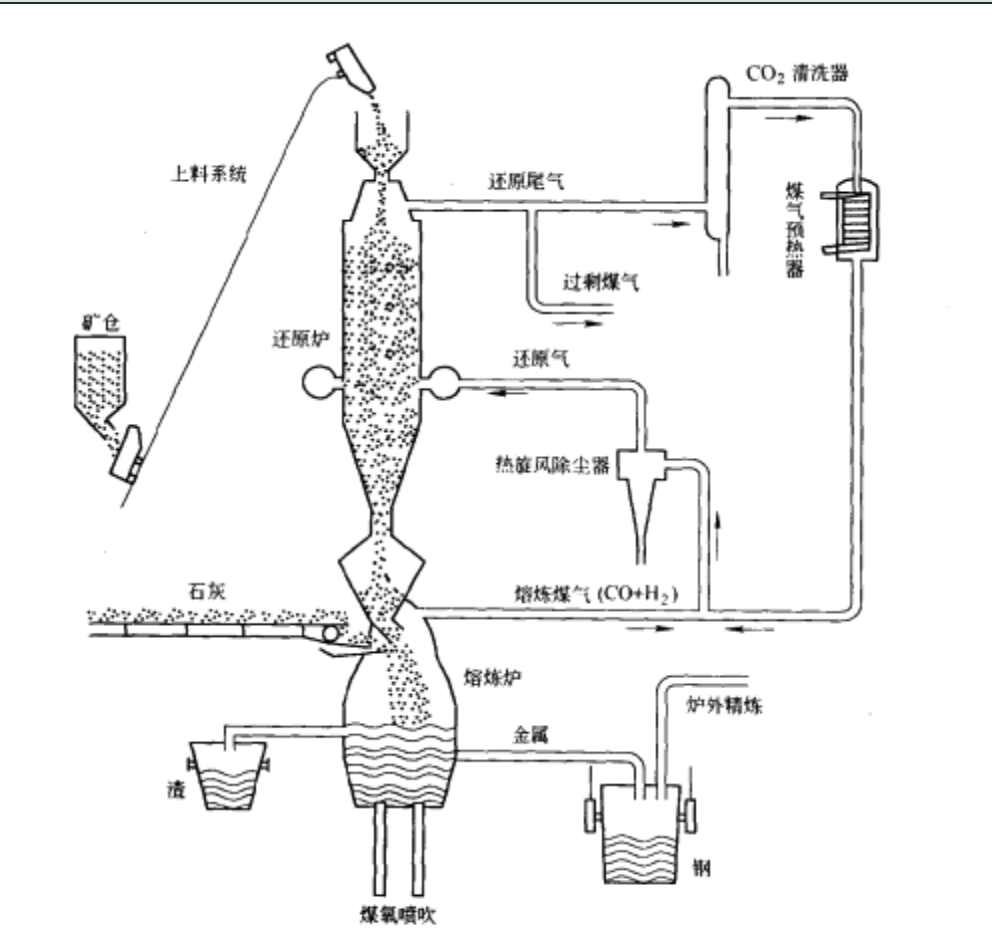
此外,開發者還制定了兩套流程方案,分別稱為COIN1和COIN2,流程模式如下圖所示。
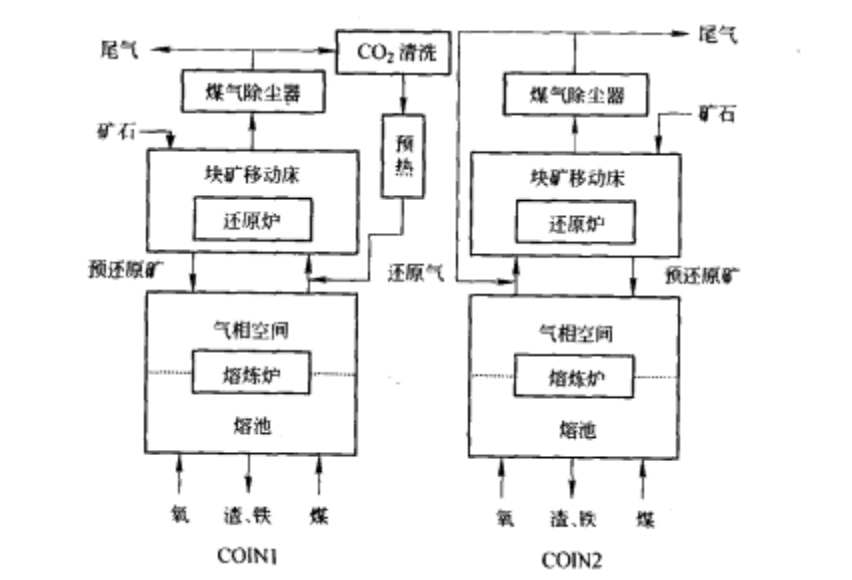
COIN法使用粉煤做燃料。工業試驗中使用的煤粉粒度不大於200μm,預計在大型工業裝置中可放寬至1mm。COIN對熔煉煤的適應性很強,從高揮發分煤至焦炭都在試驗中得到驗證。
煤粉和助燃氧氣通過套管式噴槍直接從爐底吹入熔池。噴槍的中心管用於吹氧,外套管用於噴吹煤粉。煤粉造成的局部冷卻效果起到對噴槍的保護作用。試驗轉爐裝有3根這樣的噴槍。試驗中,爐渣內FeO含量低於1%,硫在渣鐵問的分配基本達到平衡。典型的鐵水溫度為1500℃,含碳1%~4%,矽含量很低。鐵水含硫受熔煉煤含硫量的影響,一般在0.15%左右。
煤氣中的氧化性氣氛很低,含塵量在30g·m-3左右。煤氣中約帶走人爐硫量的10%左右。這部分硫在600℃以下時大部分被粉塵中的金屬顆粒脫除。因此,除塵後的低溫淨煤氣含硫極低。
套用熔煉爐尾氣的流化床還原試驗是單獨進行的,產品也未在熔煉試驗中使用。使用含塵煤氣的豎爐還原試驗也限於實驗室規模。
HISMELT流程
HISMELT(High Intensity Smelting)技術是德國Klockner和CRA公司(一家澳大利亞的資源公司)聯合開發的。該流程採用臥式鐵浴爐作為熔煉造氣爐,循環流化床作為還原爐,可直接使用粉礦進行全煤冶煉。流程概況如下圖所示。
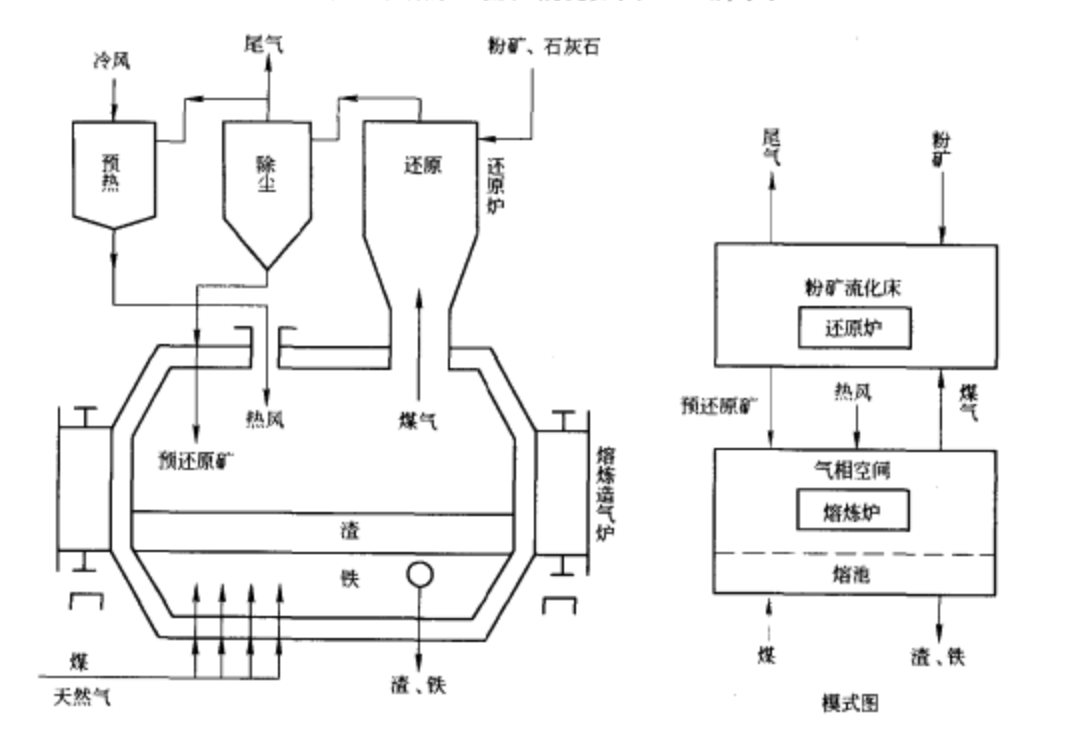
1984年末,一座在連續生產條件下年產3萬噸規模的工業試驗轉爐投入運轉。試驗的目的之一是確定實現高二次燃燒率和高熱效率的操作條件。試驗中使用了不同品級的熔煉煤,研究了各類重要冶金反應。
同時,粉礦還原的實驗室工作也在進行。研究結果表明,在不出現金屬鐵的情況下,粉礦可在流化狀態下迅速還原成浮氏體,同時可成功地避開粘結失流問題。因此,開發者選擇可直接使用粉礦的流化床作為還原反應器。為了避免出現金屬鐵,預還原率則控制在30%以下的水平。較低的預還原率使熔煉負荷加重,但也具有不可忽視的優點。首先,還原單元對還原氣質量的要求降低,可使用氧化程度和溫度較高的熔煉煤氣,不需設定還原氣改質單元。其次,不必擔心預還原礦進入熔煉爐後發生再氧化反應。這些為提高熔煉二次燃燒率創造了有利條件。
二次燃燒率的提高是鐵浴熔煉爐開發中的重要問題。HISMELT工業試驗中,二次燃燒率已達到50%~60%的高水平。
AISI流程
AISI(American Iron and Steel Institute)法是美國鋼鐵學會在美國能源部的財政支持下開發的。美國在熔融還原研究開發工作中起步較晚。自1987年夏季AISI撥款資助起,才開始了正式的研究工作。第一個步驟是成立了一個由大學教授和公司代表組成的所謂"Task A”10人委員會。該委員會的任務是確定世界範圍內熔融還原技術的發展方向和現狀。首先進行了詳細的文獻檢索,並訪問了歐洲和日本22家在熔融還原領域處於先導地位的公司和科研單位。最後確定了美國發展熔融還原的技術方案,即AISI方案:
- 使用北美鋼鐵工業大量生產的球團礦;
- 採用不小於50%的二次燃燒率。
- 使用單段還原裝置將球團礦還原成浮氏體,還原劑是熔煉尾氣。
- 有能力熔煉相當比例的廢鋼,使產品含碳量降低到實際能夠達到的最低水平。
由此可見,AISI的目標是採用鐵浴熔融還原法直接煉鋼。1989年起,利用一座現有15噸轉爐進行了熔煉單元試驗研究。該階段未配置還原設施,採用Hylsa提供的預還原球團礦作為熔煉原料。至1991年初,進行了26次試驗,產率達到每小時4.2t。1991年末,將原來的立式熔煉爐改為水平圓筒狀的逆流雙熔煉區臥式熔煉爐。熔煉能力可達10t·h-1。經過第一階段的研究,確定以HYL型豎爐作為還原單元的主體設備,流程概況如圖所示。
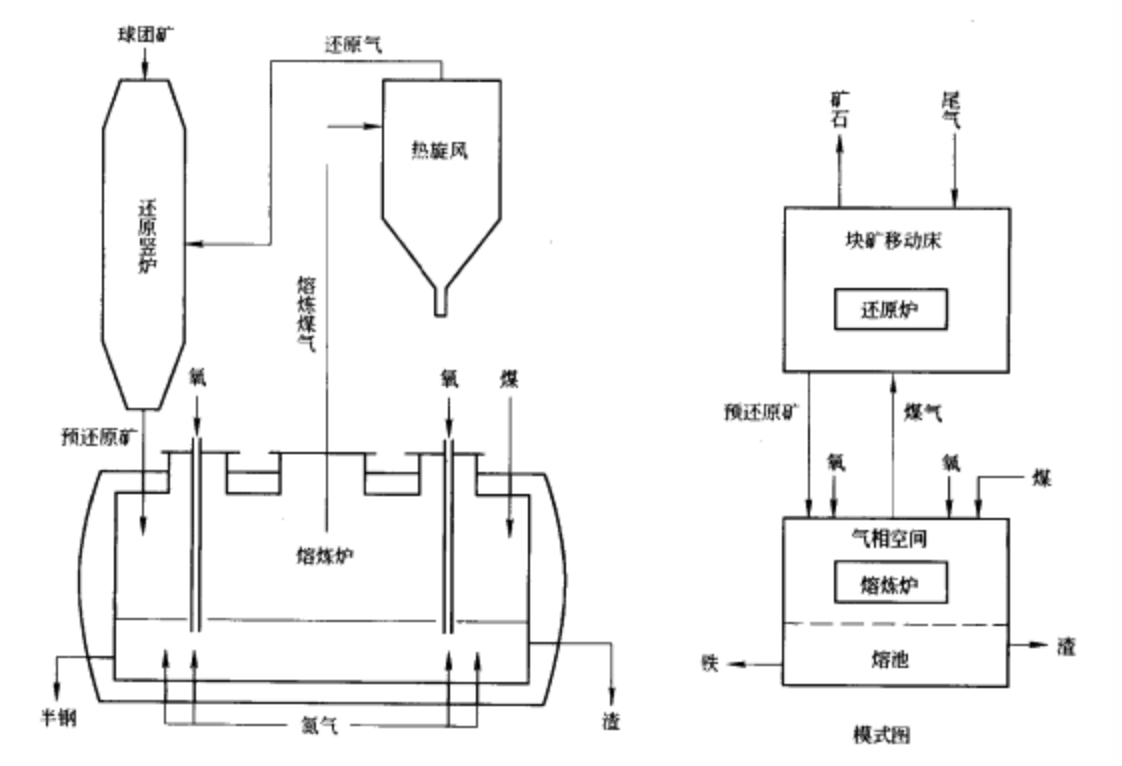
AISI熔煉爐採用兩個氧槍,分別位於左右兩側,用於吹入工業純氧。形成兩個高溫熔煉區。在兩個熔煉區的底部分別設有氮氣噴嘴,吹人氮氣,攪拌熔池。預還原礦加入左熔煉區。因此,左熔煉區氧化勢較高,氣相二次燃燒率也較高。煤則加入右熔煉區。因此,右熔煉區的還原勢較高,而二次燃燒率則較低。
預還原礦人爐後迅速熔化,形成高FeO爐渣。渣口設於右側,高FeO渣流向右熔煉區,在高還原勢的氣氛中,FeO迅速還原、滲碳,形成鐵水和低FeO爐渣。爐渣定時自渣口排放。鐵1:1設於左側,高碳鐵水自右熔煉區流向左熔煉區,在高氧化性氣氛中完成部分脫碳過程,形成半鋼。半鋼自鐵口定時排放。這樣的半鋼經鋼包處理,繼續脫除其中的C、S等雜質,成為最終產品鋼水。
來自兩個熔煉區的煤氣具有不同的二次燃燒率。這兩部分煤氣相向流動,在中間區混合,並排出熔煉爐。熔煉煤氣出爐後經熱除塵,再通入還原豎爐,將氧化球團礦中的高價鐵氧化物還原成FeO。
DIOS流程
在川崎、住友、神戶等大量前期工作的基礎上,日本鋼鐵聯盟組織八大鋼鐵公司制定了一個熔融還原7年(1988~1994年)開發規劃。開發工作得到日本政府
的財政資助。研究目的是開發一種鐵浴法熔融還原技術,定名為DIOS。熔煉單元採用立式轉爐型鐵浴熔煉造氣爐。還原單元採用流化床,以壓低還原度的措施避免還原過程的粘結失流問題。流化床形式可能為傳統鼓泡流化床,高速循環流化床或二者結合。熔煉爐採用較高的二次燃燒率,高溫高氧化度的尾氣通過一個煤氣改質爐利用粉煤改造成中溫高還原性的還原氣。

整個計畫分為三步進行:
1.單元試驗,計畫於1990年完成。
2.500t·d-1級中試廠建設,計畫於1990~1993年間進行。
3.中間試驗,計畫於1994年完成。
