鋼鐵廠能源中心採用計算機網路構成的集中管理和遠程遙控遙測的能源管理系統(簡稱MES系統),分析了系統的軟硬體結構、數據的採集和監控理念,並對該系統主要功能的實現進行了描述.
基本介紹
- 中文名:鋼鐵廠能源
- 採用:EMS系統
- 描述:系統主要功能的實現
- 主要有:煤
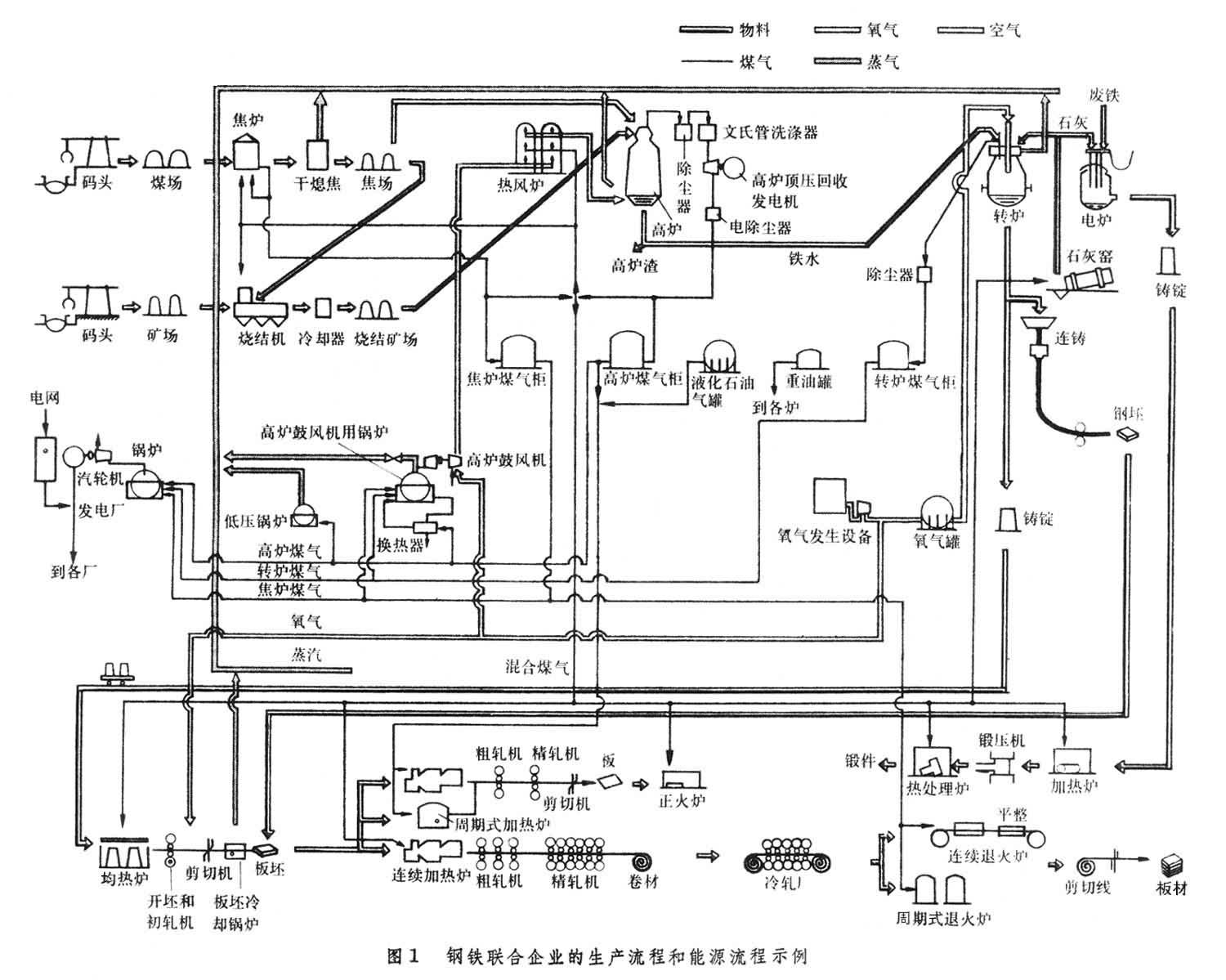
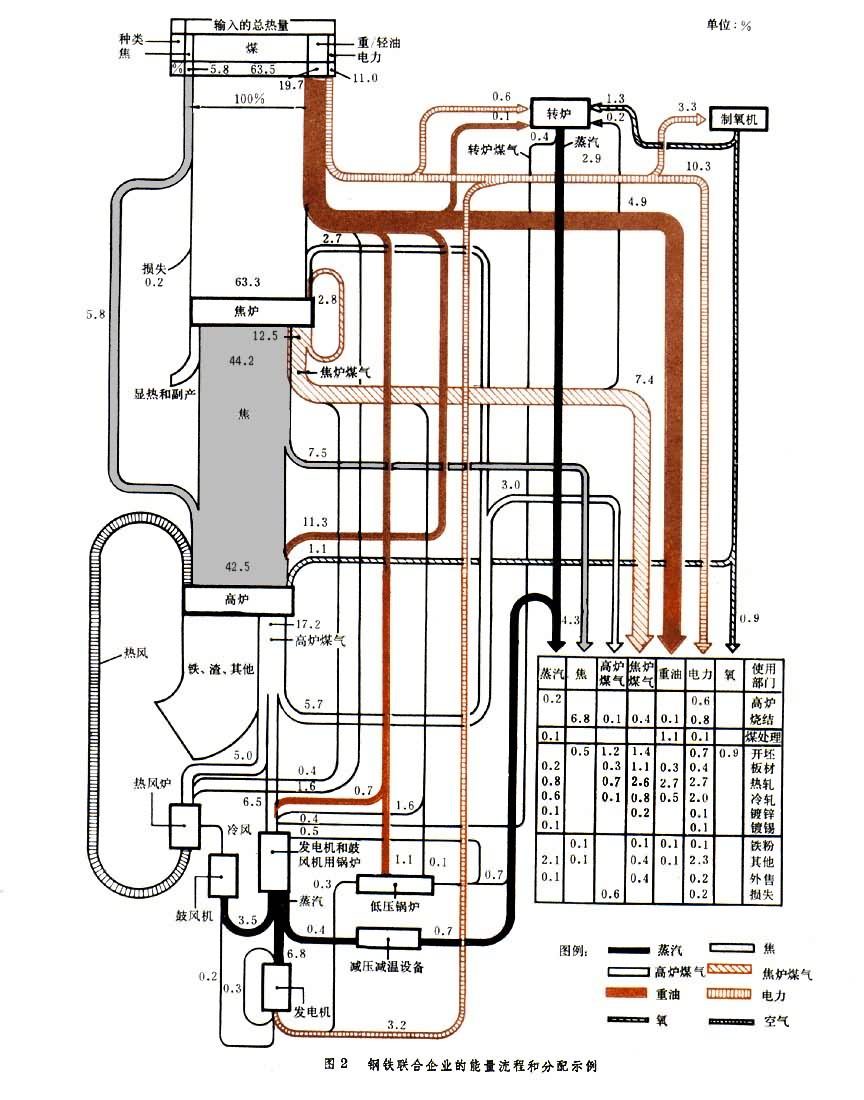
鋼鐵廠能源中心採用計算機網路構成的集中管理和遠程遙控遙測的能源管理系統(簡稱MES系統),分析了系統的軟硬體結構、數據的採集和監控理念,並對該系統主要功能的實現進行了描述.
鋼鐵廠能源中心採用計算機網路構成的集中管理和遠程遙控遙測的能源管理系統(簡稱MES系統),分析了系統的軟硬體結構、數據的採集和監控理念,並對該系統主要功能的實現...
《鋼鐵企業能源規劃與節能技術》內容簡介:《鋼鐵企業能源規劃與節能技術》還輔以模板使得規劃的執行具體化,同時匯集了行業節能技術,在實施過程中,依據企業實際情況,...
聯合企業噸鋼可比能耗的含義是指鋼鐵企業以鋼為代表產品前後工序能力配套生產所需要的能源消耗。是指企業每生產1t鋼從煉焦、燒結、煉鐵、煉鋼直到成品鋼材配套生產所...
《鋼鐵企業能源管理體系審核》力圖在有限的篇幅內,按照GB/T23331《能源管理體系要求》國家標準的條款主線,從能源的設計、採購、儲存、加工轉換、輸送分配、使用和...
鋼鐵廠的能源消耗約占鋼鐵成本的20%~40%。不同的裝備水平,工藝流程,產品結構和能源管理水平對能源消耗都會產生不同的影響。實用經濟的節能技術、數位化的平衡輸配...
採用信息技術作為平台,綜合新技術、新工藝、配套技術和管理措施,減少消耗,形成安全、穩定、經濟和高效的能源供給系統,對於降低鋼鐵生產成本,改善環境質量,提高產品的...
鋼鐵企業節能減排關鍵技術與裝備,拼音題名,gang tie qi ye jie neng jian pai guan jian ji shu yu zhuang bei,其它題名,能源與動力工程專業實習教程...
地理和資源稟賦,使太鋼具有資源、能源和區位優勢。太鋼是集鐵礦山採掘、鋼鐵生產、加工、配送和貿易為一體的特大型鋼鐵聯合企業和全球最大、技術裝備水平最高、品種...
在國家出台的《節能技術改造財政獎勵資金管理辦法》等配套政策措施的引導下,鋼鐵企業持續增加在節能環保領域方面的投資,推廣套用了餘熱余壓利用、能源管控中心、乾法...
強化環保執法約束作用,全面調查鋼鐵行業環保情況,嚴格依法處置環保不達標的鋼鐵企業,進一步完善鋼鐵行業主要污染物線上監控體系,覆蓋所有鋼鐵企業。加大能源消耗執法檢查...
通過鋼鐵產業布局調整,到2010年,布局不合理的局面得到改善;到2020年,形成與資源和能源供應、交通運輸配置、市場供需、環境容量相適應的比較合理的產業布局。...
北京大學工學院能源與資源工程系和天津鋼鐵有限公司共建“過程節能與資源再利用”聯合研發基地,雙方以鋼鐵冶金工藝中的節能、環保與生態技術為核心開展全面合作。以北京...
致力於研究、套用和推廣先進的鋼鐵工藝技術和冶金成套設備輸出,服務領域從鋼鐵業延伸至有色、輕工、化工、機械、交通、能源、環保等多種行業。擁有十餘家具備一流...
和歸宿,是河北鋼鐵集團對國家、對社會、對員工、對出資人、投資人和股東自覺擔當...來適應企業現代化管理創新這一基礎性管理工作,湧現出了《科學管理能源向節能減排...
秉承“商德唯信,利末義本”的山西高義鋼鐵公司於2003年創立於“關公故里”——山西運城,境內煤、鐵、鋁礬土等礦產資源居全國前列,是中國重要的能源和原材料工業...
霸州市新利鋼鐵有限公司始建於2002年,是一家以煉鐵、煉鋼為主體的鋼鐵企業。地...新利鋼鐵重視能源環保,以節能、節材、清潔生產和發展循環經濟為重點,不斷完善...
所必需的耗能量及企業燃料加工與運輸、機車運輸能耗及企業能源虧損所分攤在每噸粗...噸鋼可比能耗是在生產結構不同的各企業之間以及我國鋼鐵工業和國外鋼鐵工業之間...
為鋼鐵主業的發展提供有力支撐,2007年底寶鋼發展對原寶鋼集團企業開發總公司的...從寶鋼工程上海寶鋼節能技術有限公司首次試水契約能源管理商業模式,到如今首批契約...
工藝和熱工操作及自動化的要求;③根據燃料資源、燃料加工工業的發展水平,以及聯合企業的燃料平衡情況,綜合分析各類因素,確定選用燃料品種的最優方案(見鋼鐵廠能源)。...
鋼鐵企業是資源和能源的消耗大戶,大量使用鐵礦、煤炭、水、電等資源,鋼鐵企業用能占全國總用能的10%。中國鐵礦資源緊缺,50%以上的鐵礦需要進口,已經引起全球礦價...