空管反應器一般用於氣相反應,但是也適用於某些液相反應。如果傳熱速率要求較高,就採用直徑小的管,以增加表面與體積之比。多管並行排列,用集流管連線或以列管式換熱器同樣的排列方式安裝於管板上。對於高溫反應而言,反應管可以排列於爐中。
基本介紹
- 中文名:空管反應器
- 外文名:Air tube reactor
- 套用:氣相反應
- 優點:容積小、比表面大
- 套用領域:化工生產
- 模型:活塞流模型
簡介,空管反應器結構與特點,活塞流模型,空管反應器設計流程,
簡介
空管反應器是一種呈管狀、長徑比很大的連續操作反應器。這種反應器可以很長,如丙烯二聚的反應器管長以千米計。反應器的結構可以是單管,也可以是多管並聯;可以是空管,如管式裂解爐,也可以是在管內填充顆粒狀催化劑的填充管,以進行多相催化反應,如列管式固定床反應器。通常,反應物流處於湍流狀態時,空管的長徑比大於50;填充段長與粒徑之比大於100(氣體)或200(液體)。
在化工生產中,連續操作的空管反應器可以近似看成是理想活塞流,又稱平推流或置換流(PFR)反應器。它既適用於液相反應,也適用於氣相反應。當用於液相反應和反應前後無物質的量變化的氣相反應時,可視為恆容過程;當用於反應前後有物質的量變化的氣相反應時,為變容過程。如果在反應過程中利用適當的調節手段使溫度基本維持不變,則為恆溫過程,否則就為非恆溫過程。管式流動反應器內非恆溫操作可分為絕熱式和換熱式兩種。空管反應器多數採用連續操作,少數採用半間歇操作,很少使用間歇操作。
空管反應器結構與特點
空管反應器主要用於氣相、液相、氣一液相連續反應過程,由單根(直管或盤管)連續或多根平行排列的管子組成,一般設有套管或殼管式換熱裝置。操作時,物料自一端連續加入,在管中連續反應,從另一端連續流出,便達到了要求的轉化率。由於空管反應器能承受較高的壓力,故用於加壓反應尤為合適,例如,油脂或脂肪酸加氫生產高碳醇、裂解反套用的管式爐便是空管反應器。
此種反應器具有容積小、比表面大、返混少、反應混合物連續性變化、易於控制等優點。但若反應速率較慢,則有所需管子長、壓降較大等不足。隨著化工生產越來越趨於大型化、連續化、自動化,連續操作的空管反應器在生產中使用越來越多,某些傳統上一直使用間歇攪拌釜的高分子聚合反應,目前也開始改用連續操作的空管反應器。
空管反應器的長徑比較大,與釜式反應器相比在結構上差異較大,有直管式、盤管式、多管式等,如下圖所示。
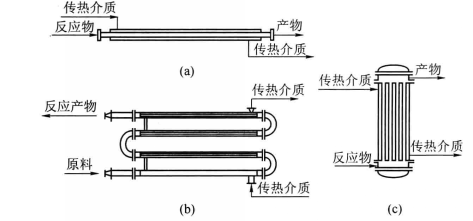
活塞流模型
流體在管內流動時存在流速分布,同一橫截面上,中間處的流速最大,越靠近器壁流速越小;當流體呈層流時,其徑向流速分布為拋物面狀,如下圖中a所示,呈湍流時則隨湍動的程度不同流速分布變得扁平,如下圖中b所示。
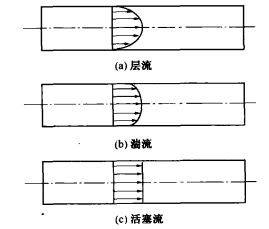
可以看出,中心部分的流體停留時間短,而靠近管壁處的流體停留時間長。停留時間不同影響化學反應進行的速率和程度。另外,由於反應器內的流體混合的形式和程度直接影響到反應器內各處流體的濃度和溫度,而它們又是決定反應速率的因素,因此反應器內流體混合也是一個重要的影響因素。根據實際流動狀況,對其進行合理簡化,建立流動模型。
活塞流是一種極端的理想流動狀況,即徑向流速分布均勻,如上圖中c所示。所謂活塞流是指反應物料以一致的方向、相同的速度從反應器進口向出口運動,像活塞一樣均勻地向前移動。其特點是連續定態操作,在反應器的各處截面上物料濃度均勻、溫度均勻,且物料參數不隨時間變化,屬於穩態操作;物系參數隨軸向位置變化,故反應速率隨軸向位置變化;所有物料在反應器內停留時間相同,不存在返混。
所謂返混是指具有不同停留時間的流體粒子之間的混合。對活塞流反應器而言,同一時刻進入反應器的流體粒子必然在同一時刻離開反應器,即所有物料在反應器內停留時間相同。因此,活塞流反應器與間歇操作釜式反應器具有相同的效果,即當物料在反應器內的停留時間相同時,兩者所達到的最終轉化率及最終收率相同。
對於連續操作釜式反應器,假設剛進入反應器的新鮮物料與已經存留在反應器中的物料能達到瞬間的完全混合,以致在整個反應器內各處物料的濃度和溫度完全相同,且等於反應器出口處物料的濃度和溫度,在這種情況下,物料的返混程度達到最大,這就是所謂的全混流模型,又稱完全混合流模型(CSTR),是另一種極端的理想流動狀況。
活塞流和全混流都屬於理想化了的流動,因此這兩種模型又稱為理想流動模型。兩者最大的區別在於活塞流無返混存在,而全混流返混程度達到最大。
空管反應器設計流程
反應器設計的一般流程如下:
1、收集與所需反應和副反應的所有熱力學和動力學數據。大多數有用的信息不可能都從文獻檢索中收集,因為關於商業上頗具吸引力的過程只有極少的信息在公開發行的文獻上出版。反應器設計所需的動力學數據一般是從實驗室和中試現場研究獲得。對於反應速率來說,反應操作條件:壓力、溫度、流速和催化劑濃度範圍值都是需要知道的。
2、收集設計所需的物理性質數據,要么通過估計從文獻查閱,如果必要,要么就通過實驗進行測定。
3、確定優勢速控機理:動力學,傳質或傳熱。基於類似反應的經驗,或根據實驗室和現場試驗工作,選擇合適的反應器類型。
4、初步選擇獲得所需轉化率和產率的反應器條件。
5、篩選反應器形狀並估計其性能。精確分析求解設計關係式幾乎是不可能的,一般不得不採用基於理想化反應器分析的半經驗方法。
6、選擇合適的結構建材。
7、對反應器作初步的機械設計:容器設計,傳熱表面,內部構件和總布局圖。
8、對計畫的設計、投資和運營進行成本核算,如果必要,重複4~8步,最佳化設計。在選擇反應器條件時,特別是轉化率以及最佳化設計時的反應器設計與其他過程操作的相互關係是不能忽視的。反應器中原料轉化率將會決定反應器的大小和成本,包括任何設備需要分離和再循環未反應原料的成本。在這些情況下,反應器及其相關設備必須最佳化成一個單元。