煙化爐是向液態爐渣中鼓入空氣和粉煤的混合物,使渣中的某些有價金屬以金屬、氧化物或硫化物的形態揮發出來的設備。煙化爐原是處理鉛鼓風爐渣的設備。。
基本介紹
- 中文名:煙化爐
- 外文名:fuming furnace
- 簡介:向液態爐渣中鼓入空氣粉煤混合物
- 作用:煉錫爐渣
- 用途:處理爐渣的設備
- 問題:容易產生危險氣體
概述,粉煤燃燒機理,危險氣體,種類,產生原因,安全措施,節能分析,節能途徑,節能管理,
概述
向液態爐渣中鼓入空氣和粉煤的混合物,使渣中的某些有價金屬以金屬、氧化物或硫化物的形態揮發出來的設備。煙化爐原是處理鉛鼓風爐渣的設備。
有色冶金企業中各種爐渣(尤其是鉛鋅渣、錫渣)的處理均廣泛採用煙化爐。傳統煙化爐為間斷作業,用粉煤作還原劑,粉煤和風一起通過風嘴鼓入爐內。這樣做帶來的弊端有:風嘴受粉煤高速顆粒流的沖刷,磨損嚴重,壽命短;由於間斷作業產生的高溫煙氣經餘熱利用裝置所產的蒸汽不連續且波動很大不利於利用,尤其是不利於發電;需複雜的粉煤製備系統。
粉煤燃燒機理
煙化爐熔煉是一個周期性的工作,可以進行加料、 升溫、 還原吹煉、放渣四步。 粉煤在熔煉過程中具有還原和供熱雙重作用。 粉煤氣流燃盡的過程比較漫長。 讓煙氣過快離開爐膛會造成機械燃燒不完全而造成燃料損失。 在升溫階段, 應該根據粉煤氣流的燃盡時間來確定氣流操作速度。 選取合適的氣流速度, 保證粉煤燃燒發揮完全。
危險氣體
種類
(1)煙粉煤氣粉混合物,即空氣和煙粉煤的混合物。煙粉煤的爆炸濃度範圍與煤的成分、粒度、引火源的種類及環境條件有關,一般認為煤塵爆炸濃度極限為30~2000 g/m3;煙粉煤與空氣混合物著火溫度為350~500℃,這種溫度條件,幾乎一切火源均可達到,如爆破火焰、電氣火花、機械摩擦火花、 瓦斯燃燒或爆炸等。煤粉揚塵時也會形成氣粉混合物,甚至會發生燃爆現象。
煙化爐
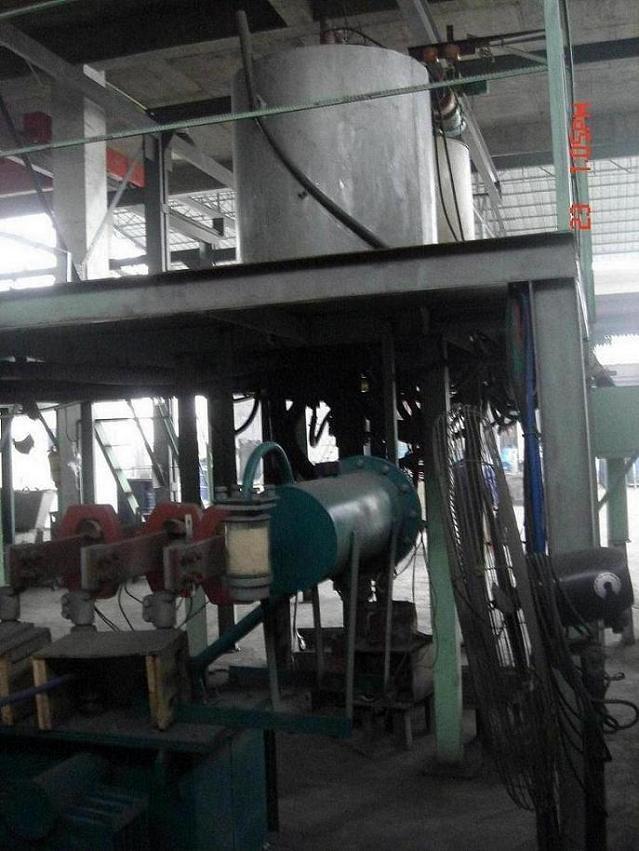
(2)CO:CO在空氣中的爆炸濃度極限為12~74.5%。在空氣中的自燃點為609℃,CO與空氣 混合物遇明火、熾熱會引起燃燒爆炸;CO通過呼吸道進人人體後,立即與血液中的血紅蛋白結合,從而使人體組織缺氧而中毒。
(3)水蒸氣。水受熱汽化時,體積增大1700多倍,瞬間汽化,輕則會燙傷人,如果在密閉容器內發生瞬時汽化,則會發生爆炸。
煙化爐生產中出現的安全事故,絕大部分是沒有控制好已形成的危險氣體造成的。
產生原因
煙化爐生產中,煙煤既作燃料又作還原劑,是形成煙粉煤氣粉混合物和CO危險氣體的根源。煙化爐為水(汽)冷水套或煙化爐——餘熱鍋爐——體化結構,生產崗位間斷操作,通常冷卻水強行冷卻、爐體水套漏水或冷卻水套浸沒人熔渣等都會使水蒸氣成為危險氣體。
一、粉煤製備和輸送過程危險氣體形成的原因:
粉煤製備過程中,煙煤經過熱風乾燥——球磨機磨煤——粉煤風機抽風——布袋室過濾將粉煤捕集,在粉煤風機抽風過程中,形成的氣粉混合物可能在爆炸濃度極限範圍內。
煤粉如遇熱空氣或明火極易產生自燃,若在煤倉儲存時間過長,由於其表面積大,碳與空氣中的氧緩慢發生化學反應,放出的熱量如果不能及時釋放而積聚,導致局部溫度越來越高,可能達到粉煤燃點而產生明火,著火的煤粉遇到揚塵或通風時,有可能形成達到爆炸濃度極限的氣粉混合物而產生爆炸。
二、爐內CO形成危險氣體的原因:
正常生產時,在中間粉煤倉不出現操作失誤的情況下可以使氣粉混合物受控燃燒,煙化爐內CO濃度處於工藝受控狀態,生產過程不會出現危險。 但是,煙化爐放完渣停煤時間不長,一次風管和混合箱內殘存粉煤噴到爐膛內因停止鼓風而發生不完全燃燒,此時如果停止抽風,產生的CO不能被及時抽 走,空氣和CO比重很接近,CO難以快速擴散到爐膛上部空氣中而導致局部積聚,CO在爐膛局部濃度可能達到12%以上,從而形成危險氣體,遇到明火便產生爆炸。
三、冷卻水產生水蒸氣形成危險氣體的原因:
煙化爐爐膛熔渣溫度達1150~1250℃,通常是間斷性生產,崗位操作也具有間斷性,如進料——放渣——清理進料溜槽——清理放渣孔和渣槽——轉入下一爐進料吹煉,其中清理進料溜槽、清理放渣孔和渣槽均要採用強行發水冷卻方式,水量控制不當可能流入爐膛導致出現明火或水蒸氣直接傷人;生產過程中發現爐體水冷水套缺水發紅,如果立即通水,最先進入的冷卻水可能快速轉化為水蒸氣,體積迅速膨脹,輕則導致水套變形,重則產生爆炸;如果水套浸沒入高溫熔渣內,水套內冷卻水瞬時轉化為水蒸氣, 體積急劇膨脹將產生爆炸。
安全措施
一、加強安全技術培訓
建立動火審批制度 粉煤製備系統、粉煤輸送管道、粉煤儲存倉等設備設施檢修不能擅自動火,否則可能引起嚴重後果; 必須確認動火部位無氣粉混合物、無殘煤,對焊渣實行隔離控制,保持在微負壓狀態下作業,消除可能存在的安全隱患,否則必須將粉煤清理乾淨,或採取必要的安全措施。
煙化爐
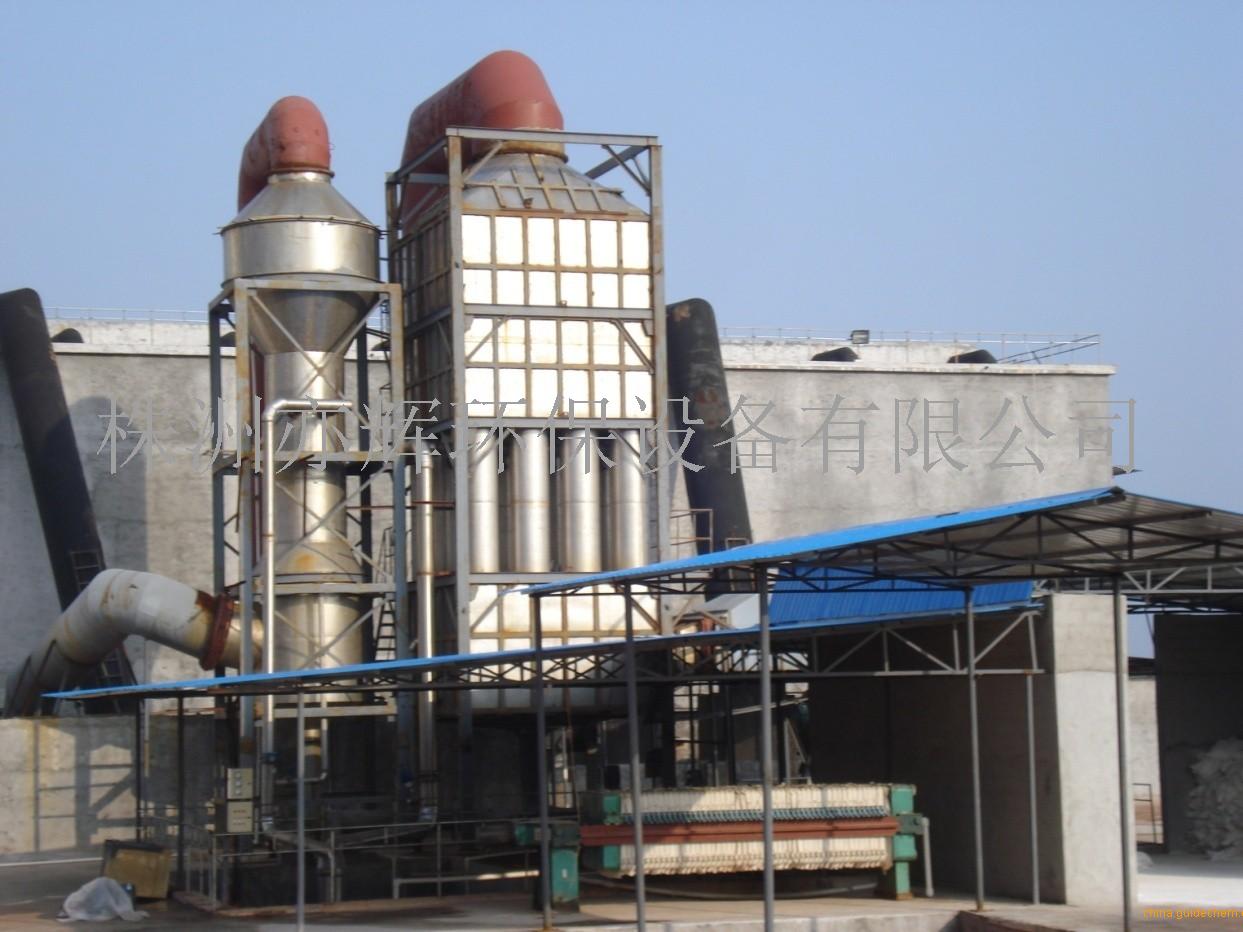
二、保證爐體內外通風暢通,防止CO積聚:
保證煙化爐收塵風機正常運轉、使爐內吸風,是 防止CO積聚最有效的手段。經調查,煙化爐出現的安全事故大多是收塵風機停止運轉引發的,如果停爐時間不長,在煙化爐爐體內外作業均要開啟收塵抽風機,防止CO積聚。
三、控制粉煤質量和貯存時間:
粉煤質量控制在:揮發份16%一21%、固定碳>40%、一200目以下不少於80%。儘管優質煙煤可以提高吹煉效果,但是在粉煤製備、輸送、儲存過 程中更容易發生摩擦自燃,嚴重時甚至引起爆炸,所以中等質量煙煤即可。粉煤倉中的粉煤不宜儲存超過半個月,原煤儲存倉中的原煤要及時使用、更新, 堆煤過多、過久應採取篾筒通風等措施。
四、加強崗位操作,保證冷卻操作及設備設施安全:
煙化爐通常採用渣包吊運熔渣經溜槽人爐的進料方式,溜槽內結有一層渣殼,下一爐進料前必須先用水冷卻清理渣殼,該操作存在安全隱患,宜採用噴淋水冷卻,儘量避免水流人爐膛;放渣完成後,及時用水冷卻清理渣口和渣槽,且儘量避免水流入爐膛; 考慮到放渣的安全性,儘量減少冰銅入爐吹煉,避免硫化物氧化不徹底導致放渣沖炮;生產過程中出現爐體水冷套缺水發紅時,嚴禁立即通水冷卻,應緊急放渣待水套冷卻後再供冷卻水;加固爐體水套連線, 防止水套掉入爐膛或浸沒入熔池內。
五、設定可燃氣體濃度報警器:
在爐體周圍操作場所設定煙粉煤氣粉混合物、 CO等可燃氣體濃度報警器,這也是企業安全標準化和HSE管理體系創建要求。
六、杜絕人為操作失誤:
中間粉煤倉操作失誤,會導致瞬間大量粉煤湧入爐內,造成噴火甚至爆炸事故。因此,必須對從事中間粉煤倉進煤、給煤操作的工人素質嚴格把關,加強培訓,建立操作資質準入制度。
節能分析
節能途徑
一、工藝冶煉節能:
煙化爐中鉛的揮發速率因為含氧率的增大而提高, 因為吹煉時間會縮短, 所以節能效果更加明顯。 但是很多煉鉛廠欠缺很多制氧工藝設備, 氧吹的成本很高, 沒有進行廣泛套用。
二、煙化爐餘熱利用:
(1) 汽化冷卻法。 如果在煉鉛廠安裝汽化冷卻裝置, 既能節約用水又能夠回收熱量, 保證煙化爐能夠正常運行。 然而使用汽化冷卻水會降低煙化爐使用壽命, 需要對煙化爐進行改進才可以使用。
(2) 安裝餘熱鍋爐回收餘熱。 在煙化爐中安裝餘熱鍋爐裝置, 通過生產證明得出這種強制循環和自然循環的方法是切實可行的。 通過在煙化爐內安裝餘熱鍋爐, 能夠有效利用高溫煙氣餘熱, 回收煙氣中的二氧化硫, 對環境起到保護作用。
節能管理
一、提高管理水平:
煙化爐
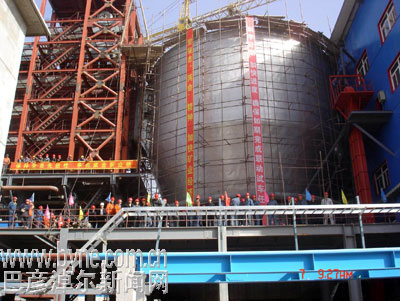
(1) 建立煉渣流程管理系統。 建立煉渣流程管理信息系統, 用計算機代替人為操作統計, 及時分析煙化爐能源損耗, 能夠提高管理水平。
(2) 強化人工和工序管理。 不僅建立人員技能培訓, 還要樹立節能意識。 發揮人員積極性, 儘量避免煙化爐能源損耗。 在生產經驗總結基礎上, 能夠制定完善的煙化爐生產工序, 克服生產過程的盲目。
(3) 發揮能源管理機構作用。 制定節能規劃, 保障能源機構措施積極落到實處。
二、 實現煙化爐控制節能:
為了達到節能的目的應該完善節能控制方法措施, 必須控制好下列條件, 即溫度、 燃料、 送風量、 和爐渣成分。
(1) 煙化爐燃燒溫度控制。煙化溫度和時間對鉛鋅揮發速度的影響, 在其它條件一定時, 鉛鋅的揮發速度隨著溫度的升高而增大。但溫度過高(如超過1350℃) , 可能會形成積鐵或Zn—Fe、 Sn—Fe合金, 有害於煙化作業的進行。 溫度過低, 金屬氧化物的還原速度變慢, 揮發速度降低, 爐渣流動性變壞, 甚至有結爐的危險, 所以煙化實踐中的溫度保持在1150~1300℃的範圍。
(2) 燃料控制。 燃料中含H 愈多, 則煙化過程的效率愈好。 所以煤以揮發分高者為宜, 一般為21~25%, 其消耗因質量而異。
(3) 送風量。 影響煙化過程揮發速度最活躍的因素是送風量。 因為爐內的溫度、一氧化碳比二氧化碳的比例、氣體量以及金屬的蒸汽壓力等都與送風的數量有關。 送風量的大小決定於粉煤消耗和空氣利用係數 , 空氣利用係數愈大, 則燃料的熱效應愈高,二氧化碳的分壓也愈大, 爐內溫度亦愈高; 空氣利用係數小時,熱效應降低,一氧化碳分壓變大, 還原能力增強。
(4) 爐渣成分。 爐渣含鋅率越高, 則回收率越大, 現實含鋅量以>6%為宜, 低於4% 的爐渣, 煙化處理量是不經濟的。 廢渣含鋅也不應降至2%以下。
三、熱風助燃:
我國的煙化爐空氣助燃一般為冷風。 冷風既不利於煙氣餘熱回收,又不利於燃燒和冶煉工藝的發展, 而國外已經選擇熱風助燃。採用熱風, 能夠增加氣態金屬氧化過程, 小顆粒粉煤也能燃燒透徹。 產品純度將會大大提高, 煙道高溫區也相對集中, 更加有利於餘熱回收。