液壓壓磚機是通過液壓傳動從液壓缸直接產生的壓力來壓制磚坯的成型設備。壓制耐火製品的液壓壓磚機性能日趨完善,從泥料定量填模到磚坯移送的全過程實現了機組可控程式連續自動操作和多種成型工藝預選以及成型質量監測顯示。成型質量穩定,操作安全可靠,是高級耐火製品成型的主要設備。
基本介紹
- 中文名:液壓壓磚機
- 外文名:hydraulic pr-ess
- 學科:土木工程
- 作用:壓制磚坯
- 優點:成型質量穩定、操作安全可靠
- 出現時間:20世紀60年代
簡史,分類,設備組成,特點,產品介紹,
簡史
液壓機的發展已有一百多年的歷史,早在1859~1861年在歐洲維也納的機械製造部門製造了用於金屬加工的10000kN水壓機。在1884年英國曼徹斯特首先使用了鍛造鋼錠用的鍛造水壓機。到20世紀40年代德國已製造出30000kN的模鍛水壓機。同時期,一些小型水壓機也在陶瓷、耐火材料工業中得到套用。水壓機的液壓系統是以水為工作介質,但由於水有許多缺點(如粘度太低、潤滑性差、鏽蝕金屬、容易蒸發等)而逐漸被液壓油代替。到20世紀60年代,工業已開發國家在耐火材料工業中發展了專用的液壓壓磚機,並且逐步形成系列產品。隨著耐火製品向大型化、高密度、多品種發展的需要,液壓壓磚機噸位達到30000kN~50000kN,出現了帶有多功能輔助系統的全自動液壓壓磚機。中國於20世紀70年代初研製成8000kN~12000kN的全自動液壓壓磚機,在耐火材料工業中得到普遍套用。
分類
液壓壓磚機根據加壓方式的不同分為液壓靜壓式和液壓振動式兩種。
液壓振動式壓磚機因加壓方式為振動加壓,壓力小,磚的密實度不夠,現已基本淘汰,這裡就不再詳述。
液壓靜壓式液壓壓磚機因加壓平穩,故障率低,而且可以設定多次排氣,所以壓制的成品具有外形尺寸標準,密實度高等優點。
設備組成
液壓壓磚機機組一般由主機(包括脫模裝置)、液壓傳動裝置、泥料加料裝置與取磚裝置、磚坯檢測與填料量自動調節裝置、磚坯移送裝置等裝置組成。(圖1)
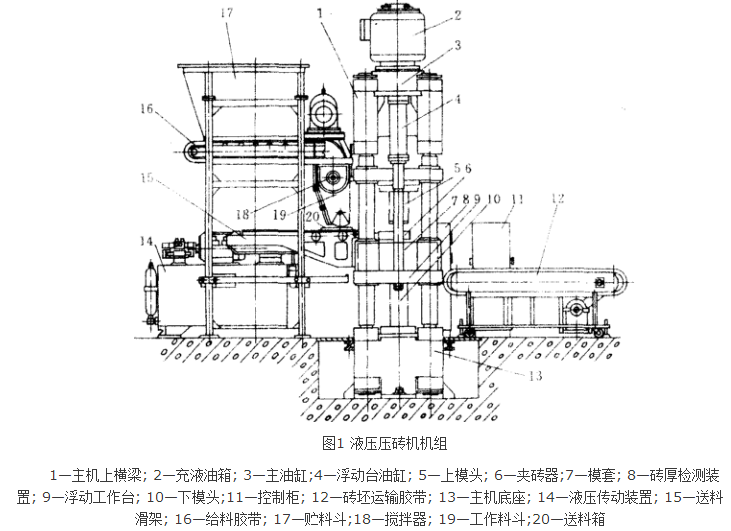
主機
有多種類型,按成型模具工作方式可分為固定模式和移動模式兩類。移動模式又有轉盤模台和往復移動模台兩種。轉盤模台帶有3個或4個模套,交替經過填料、壓制、脫模、清理和塗布防粘劑等工位周期工作,轉盤模台有較高工作效率,但模具多,裝模對位複雜,工作面大,只用於小型磚成型。往復移動模台分雙模與單模兩種。雙模裝於同一台車上,交替進入主機中心壓制磚坯,出磚、清模、填料都由設在主機前後的相應裝置來完成,與磚坯壓制同時工作,可提高工效,但需設兩套加料出磚裝置。為節省設施,少占地面空間,有的大型壓磚機寧願採用單移動模式。移動工作檯不在主機中心出磚填料,可縮短主缸工作行程,降低主機高度;複雜的輔助設施配置分散,工作維修方便,模具更換便利。固定模式液壓壓磚機模具固定在機架中心工作,結構緊湊,造價較低,為提高換模工作效率,新型壓磚機在模具固定方法及換模設施方面有了較完善的改進。這類壓磚機仍被普遍採用。
主機結構按施壓方式分上壓式和下壓式兩種。上壓式主油缸裝於上橫樑,柱塞與主滑塊聯接,上模頭固定於主滑塊上,主油缸活塞面產生液壓壓力向下施壓,底模頭固定於主機底座工作檯上,泥料在剛性模套內施壓緻密。支承模套的浮動工作檯由兩個對稱配置的油缸來控制其位移,在施壓時自動控制液壓傳動,使浮動台下降速度等於主活塞施壓速度的二分之一時,上下模頭是以相同的相對速度對泥料上下兩面施壓的,可使磚坯上下密度均勻。當磚坯脫模時,控制浮動台下降,至磚坯完全露出台面,上模頭一般處於上懸位置,亦可控制上模頭保持在一定壓力下脫模,亦稱有載脫模。
下壓式主機主油缸固定於機座上,柱塞與主滑塊相聯,下模頭支承於主滑塊上,上模頭固定於上橫樑上,在模套浮動工作檯上對稱配置一對驅動油缸,控制浮動台與主滑塊間的距離和相對移動速度,完成壓磚時浮動台動作並最後脫出磚模。
液壓傳動裝置
按照壓磚工藝和各項輔助動作的需要,壓磚機都有各自不同的液壓傳動系統。液壓壓磚機以液壓油為傳動介質,主油缸一般都採用近似恆功率變數柱塞泵直接傳動,空載採用重力充液或低壓充液迴路,合模升壓時壓力與速度呈近似直線關係變化,施壓速度隨壓力升高而遞減,適應壓磚工藝泥料緻密過程及排氣要求。液壓控制迴路能實現壓力速度靈活變換、快速卸荷、多次施壓、保壓和排氣調節。各輔助動作油缸的速度調節範圍較寬,能準確完成所要求的各項動作。套用壓力、位移、溫度、流量等感測技術達到安全限載、限位、液壓油恆溫控制。液壓系統封閉防塵,液壓油加熱冷卻和過濾設施完備。液壓系統各控制閥組更趨向閥板集成化,極少外部聯繫管道,元件更換、檢修方便,外觀整齊緊湊。
泥料加料裝置和取磚裝置
成型泥料的定量方式有兩種:容積定量與質量定量。後一方法可使成型磚坯外形尺寸更為精確。
(1)容積定量加料裝置和取磚裝置。容積定量加料方式見圖1左側所示。泥料經貯料斗由給料膠帶輸送,經一中間攪拌器進行疏鬆後落入工作料斗中。由工作料斗內的料位器和排料閥,再將粗定量的泥料排入送料箱內。為均勻排放泥料,在送料箱內裝有多個不同格板。送料箱由液壓缸驅動,在填模過程中帶動泥料箱在模孔上方作多次往復運動,使泥料填模均勻,邊角不出現疏鬆。回程時箱的底邊將泥料沿模面刮平。為使泥料填模均勻,送料箱到位後再降落底模板或升起模套形成填料空間的吸入式填料。取磚用裝在送料箱前端的夾磚器,夾磚器系由彈簧復位的氣動或液壓單向薄膜缸組成。當磚坯脫出後從側面雙向夾持磚坯。壓磚模頭的清掃刷子或噴塗防粘劑用的噴嘴裝在夾磚器與送料箱之間。送料箱行進時依次進行夾送磚坯、清刷或噴塗模具和將泥料送到模孔等動作。
(2)質量定量加料裝置和取磚裝置。質量定量加料裝置見圖2。貯料斗中的泥料經膠帶機輸送到稱量料斗中,由重力感測器電子秤計量。為使稱量準確,在輸送膠帶上裝有料層調節閘板,在稱量接近預定值時,閘板控制機構立即操縱閘板轉入薄層微量給料,當達到定量時膠帶機停止給料,同時截止閥截止料流。稱量與放料均在密封罩內進行,稱量斗底部設有氣動雙扇形閥。稱好的泥料再放入帶有移送和升降機構的送料斗中,送料斗內裝有電動攪拌器和氣動雙扇形閥,從受料到放料過程中攪拌泥料,使泥料均勻加入模內。送料斗前端裝有噴嘴,行進時往加料前面模孔噴塗防粘劑。當需要時亦可在送料斗前方裝設夾磚器,按程式夾持和移送磚坯。
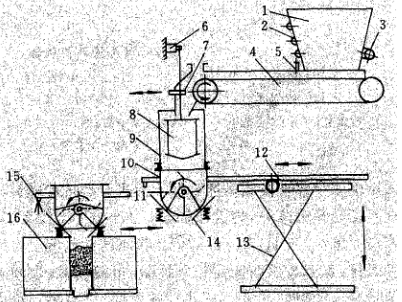
1—貯料斗;2—料位器;3—振動器;4—膠帶機;5—料層調節閘門;6—重力感測器;7—料流截止閥;8—稱量料斗;9—稱量密封罩;10—送料斗;11—攪拌器;12—移送機構;13—升降機構;14—密封套; 15—防粘劑噴嘴; 16—移動式磚模
磚坯移送裝置
壓磚機按壓制磚坯品種外形及碼磚要求設有各自的移送機構。圖1所示的機組是比較典型的配置形式。裝於送料滑架前端的氣動夾磚器從兩側夾持磚坯移送放置到磚坯運輸膠帶上,運坯機在接受信號後向前移送一個間距,在機前感測器作用下,前面磚坯未被取走時不繼續動作。大型磚坯一般採用真空吸取或機械手夾持從模上將磚坯直接碼放於台車上或指定位置。
特點
①液壓壓磚機容易實現壓磚機的大型化和系列化。通過提高油壓或增大油缸有效面積,即可得到大噸位的系列壓機。
②容易實現壓制力、壓制速度、動作時間、動作轉換的自動控制和調節。
③對坯料適應性強,能獲得高質量的坯體。
④布料均勻,工作平穩,對坯體施加的壓力近似靜壓力,有利於磚坯的成型和自動操作。
⑤易於實現牆地磚的自動化連續生產。
產品介紹
帶真空脫氣裝置的液壓壓磚機是20世紀80年代發展的設備,能適應排氣異常困難的泥料成型。真空脫氣磚模壓磚見圖5,模套、上下模頭都在真空罩內工作,真空罩由剛性金屬套和橡膠密封罩組成,與模具面接觸處填有軟密封圈,真空罩用油缸帶動升降,工作時與模面壓緊。模頭觸及泥料前真空閥開啟真空罩與真空源接通,罩內迅速形成真空,達到預定真空壓力時開始壓制磚坯,真空度可達 -80kPa,直至壓制終了,控制閥將真空源截斷密封罩轉與大氣相通。真空源由大功率水環真空泵和大容積真空罐組成,通過控制閥組自動操縱。真空系統要特別維護好密封裝置和過濾器,密封泄漏或失效時不僅達不到必要的負壓還將大量細粉泥料吸走而堵塞過濾器。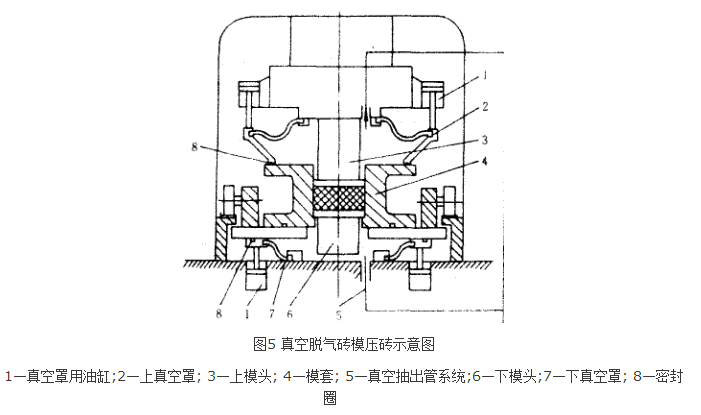
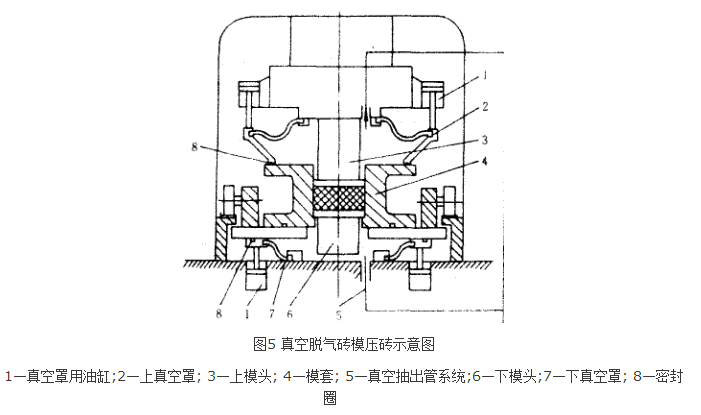
真空壓磚對於壓制微粒含量多排氣比較困難的泥料可以減少成型初期輕壓次數縮短壓制周期,並能避免磚坯成型時因泥料中氣體滯留而形成的層裂缺陷。
磚坯檢測與填料量自動調節裝置 液壓壓磚機為確保製品密度和磚坯厚度誤差的嚴格控制,一般都具備這些裝置,最常用的方法是測量壓制終了時合模尺寸,即模頭相對位移量。用機械位移放大,位移電感,光柵位移放大發出模頭最終位移信號及顯示,與設定標準位移相比較,納入程式控制輸出誤差調節量信號。填料自動調節系統按所測磚坯實際誤差值相當的填料量調節下一塊磚坯的填料深度(對容積定量制)。在原料與壓制工藝穩定時,這些自動裝置能精確控制磚坯密度和厚度。對於質量定量制的壓磚機則採用稱量單塊磚坯的質量誤差信號來調節填料秤量。