噴氣雷射切割是一種利用雷射束照射到鋼板表面時釋放的能量來使不鏽鋼熔化並蒸發的技術。
基本介紹
- 中文名:噴氣雷射切割
- 原理:使不鏽鋼熔化並蒸發的技術
- 技術:二氧化碳雷射束
- 費用:150美元以上
雷射切割,噴氣雷射切割,噴氣雷射切割的主要技術,結語,相關搜尋,
雷射切割
雷射切割該技術採用雷射束照射到鋼板表面時釋放的能量來使不鏽鋼熔化並蒸發。雷射源一般用二氧化碳雷射束,工作功
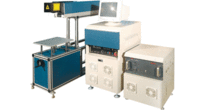
率為500~2500瓦。該功率的水平比許多家用電暖氣所需要的功率還低,但是,通祝廈過透鏡和反射鏡,雷射束聚集在很小的區域。能量的高度集中能夠進行迅速局部加熱,使不鏽鋼蒸發。此外,由於能量非常集中,所以,僅有少量熱傳到鋼材的其它部分,所造成的變形很小或沒有變形。利用雷射可以非常準確地切割複雜形狀的坯料,所切割的坯料不必再作進一步的處理。利用雷射切割設備可切割4mm以下的不鏽鋼,在雷射束中加氧氣可切割8~10mm厚的不鏽鋼,但加氧切割後會在切割面形成薄薄的悼重您晚氧化膜。切割的最屑晚祝大厚度可增加到16mm,但切割部件的尺寸誤差較大。
雷射切割設備的價格相當貴,約150美元以上。但是,由於降低了後續工藝處理的成本,所以,在大生產中採用這種設備還是可行的。由於沒有刀具加工成本,所以雷射切割設備也適用生產小批量的原先不能加工的各種尺寸的部件。目前,雷射切割設備通常採用計算機化數字控制技術(CNC)裝置,採用該裝置後,就可以利用電話線從計算機輔助設計(CAD)工作站來接受切割數據。
噴氣雷射切割
即汽化切割,在高功率密度雷射束的加熱下,材料表面溫度升至沸點溫度的速度是如此之快,足以避免熱傳導造成的熔化,於是部分材料汽化成蒸汽消失,部分材料作為噴出物從切縫底部被輔助氣體流吹走。一些照敬請不能熔化的材料,如木材、碳素材料和某些塑膠就是通過這種汽化切割方法切割成形的。
汽化切割過程中,蒸汽隨身帶走熔化質點和沖刷碎屑,形成孔洞。汽化過程中,大約40%的材料化作蒸汽消失,而有60%的材料是以熔滴的形式被氣流驅除的。
噴氣雷射切割的主要技術
雷射束的參數、機器與數控系統的性能和精度都直接影響雷射切割的效率和質量。特別是對於切割精度較高或厚度較大的零件,必須掌握和解決以下幾項關鍵技術:1、焦點位置控制技術:雷射切割的優點之一是光束的能量密度高,一般10W/cm2。由於能量密度與4/πd2成正比,所以焦點光斑直徑儘可能的小,以便產生一窄的切縫;同時焦點光斑直徑還和透鏡的焦深成正比。聚焦透鏡焦深越小,焦點光斑直徑就越小。但切割有飛濺,透鏡離工件太近容易將透鏡損壞,因此一般大功率CO2雷射切割工業套用中廣泛採用5〃~7.5〃〞(127~190mm)的焦距。實際焦點光斑直徑在0.1~0.4mm之間。對於高質量的切割,有效焦深還和透鏡直徑及被切材料有關。例如用5〃的透鏡切碳鋼,焦深為焦距的+2%範圍內,即5mm左右。因此控制焦點相對於被切材料表面的位置十分重要。顧慮到切割質量、切割速度等因素,原則上6mm的金屬材料,焦點在表面上;6mm的碳鋼,焦點在表面之上;6mm的不鏽鋼,焦點在表面之下。具體尺寸由實驗確定。
在工業生產中確定焦點位置的簡便方法有三種:(1)列印法:使切割頭從上往下運動,在塑膠板上進行雷射束列印,列印直徑最小處為焦點。(2)斜板法:用和垂直軸成一角度斜放的塑膠板使其水平拉動,尋找雷射束的最小處為焦點。(3)藍色火花法:去掉噴嘴,吹空氣,將脈衝雷射打在不鏽鋼板上,使切割頭從上往下運動,直至藍色火花最大處為焦點。對於飛行光路的切割機,由於光束髮散角,切割近端和遠端時光程長短不同,聚焦前的光束尺寸有一定差別。入射晚凳促光束的直徑越大,焦點光斑的直徑越小。為了減少因聚焦前光束尺寸變化帶來的焦點光斑尺寸的變化,國內外雷射切割系統的製造商提供了一些專用的裝置供用戶選用:
(2)在切割頭上增加一獨立的移動透鏡的下軸,它與控制噴嘴到材料表面距離(standoff)的Z軸照端櫃是兩個相互獨立的部分。當工具機工作檯移動或光軸移動時,光束從近端到遠端F軸也同時移動,使光束聚焦後光斑直徑在整個加工區域內保持一致。
(3)控制聚焦鏡(一般為金屬反射聚焦系統)的水壓。請禁組台若聚焦前光束尺寸變小而使焦點光斑直徑變大時,自動控制水壓改變聚焦曲率使焦點光斑直徑變小。
(4)飛行光路切割機上增加x、y方向的補償光路系統。即當切割遠端光程增加時使補償光路縮短;反之當切割近端光程減小時,使補償光路增加,以保持光程長度一致。
2.切割穿孔技術:任何一種熱切割技術,除少數情況可以從板邊緣開始外,一般都必須在板上穿一小孔。早先在雷射衝壓複合機上是用沖頭先衝出一孔,然後再用雷射從小孔處開始進行切割。對於沒有衝壓裝置的雷射切割機有兩種穿孔的基本方法:
(1)爆破穿孔:(Blastdrilling),材料經連續雷射的照射後在中心形成一凹坑,然後由與雷射束同軸的氧流很快將熔融材料去除形成一孔。一般孔的大小與板厚有關,爆破穿孔平均直徑為板厚的一半,因此對較厚的板爆破穿孔孔徑較大,且不圓,不宜在要求較高的零件上使用(如石油篩縫管),只能用於廢料上。此外由於穿孔所用的氧氣壓力與切割時相同,飛濺較大。
(2)脈衝穿孔:(Pulsedrilling)採用高峰值功率的脈衝雷射使少量材料熔化或汽化,常用空氣或氮氣作為輔助氣體,以減少因放熱氧化使孔擴展,氣體壓力較切割時的氧氣壓力小。每個脈衝雷射只產生小的微粒噴射,逐步深入,因此厚板穿孔時間需要幾秒鐘。一旦穿孔完成,立即將輔助氣體換成氧氣進行切割。這樣穿孔直徑較小,其穿孔質量優於爆破穿孔。為此所使用的雷射器不但應具有較高的輸出功率;更重要的時光束的時間和空間特性,因此一般橫流CO2雷射器不能適應雷射切割的要求。此外脈衝穿孔還須要有較可靠的氣路控制系統,以實現氣體種類、氣體壓力的切換及穿孔時間的控制。在採用脈衝穿孔的情況下,為了獲得高質量的切口,從工件靜止時的脈衝穿孔到工件等速連續切割的過渡技術應以重視。從理論上講通常可改變加速段的切割條件:如焦距、噴嘴位置、氣體壓力等,但實際上由於時間太短改變以上條件的可能性不大。在工業生產中主要採用改變雷射平均功率的辦法比較現實,具體方法有以下三種:(1)改變脈衝寬度;(2)改變脈衝頻率;(3)同時改變脈衝寬度和頻率。實際結果表明,第(3)種效果最好。
3.噴嘴設計及氣流控制技術:雷射切割鋼材時,氧氣和聚焦的雷射束是通過噴嘴射到被切材料處,從而形成一個氣流束。對氣流的基本要求是進入切口的氣流量要大,速度要高,以便足夠的氧化使切口材料充分進行放熱反應;同時又有足夠的動量將熔融材料噴射吹出。因此除光束的質量及其控制直接影響切割質量外,噴嘴的設計及氣流的控制(如噴嘴壓力、工件在氣流中的位置等)也是十分重要的因素。目前雷射切割用的噴嘴採用簡單的結構,即一錐形孔帶端部小圓孔。通常用實驗和誤差方法進行設計。由於噴嘴一般用紫銅製造,體積較小,是易損零件,需經常更換,因此不進行流體力學計算與分析。在使用時從噴嘴側面通入一定壓力Pn(表壓為Pg)的氣體,稱噴嘴壓力,從噴嘴出口噴出,經一定距離到達工件表面,其壓力稱切割壓力Pc,最後氣體膨脹到大氣壓力Pa。研究工作表明隨著Pn的增加,氣流流速增加,Pc也不斷增加。可用下列公式計算:V=8.2d2(Pg+1)V-氣體流速L/min(d-噴嘴直徑mm,Pg-噴嘴壓力(表壓)bar).
對於不同的氣體有不同的壓力閾值,當噴嘴壓力超過此值時,氣流為正常斜激波,氣流速從亞音速向超音速過渡。此閾值與Pn、Pa比值及氣體分子的自由度(n)兩因素有關:如氧氣、空氣的n=5,因此其閾值Pn=1bar×(1.2)3.5=1.89bar。當噴嘴壓力更高Pn/Pa=(1+1/n)1+n/2時(Pn;4bar),氣流正常斜激波封變為正激波,切割壓力Pc下降,氣流速度減低,並在工件表面形成渦流,削弱了氣流去除熔融材料的作用,影響了切割速度。因此採用錐孔帶端部小圓孔的噴嘴,其氧氣的噴嘴壓力常在3bar以下。
為進一步提高雷射切割速度,可根據空氣動力學原理,在提高噴嘴壓力的前提下不產生正激波,設計製造一種縮放型噴嘴,即拉伐爾(Laval)噴嘴。德國漢諾瓦大學雷射中心使用500WCO2雷射器,透鏡焦距2.5〃,採用小孔噴嘴和拉伐爾噴嘴分別作了試驗。試驗結果:分別表示NO2、NO4、NO5噴嘴在不同的氧氣壓力下,切口表面粗糙度Rz與切割速度Vc的函式關係。可以看出NO2小孔噴嘴在Pn為400Kpa(或4bar)時切割速度只能達到2.75m/min(碳鋼板厚為2mm)。NO4、NO5二種拉伐爾噴嘴在Pn為500Kpa到600Kpa時切割速度可達到3.5m/min和5.5m/min。應指出的是切割壓力Pc還是工件與噴嘴距離的函式。由於斜激波在氣流的邊界多次反射,使切割壓力呈周期性的變化。
第一高切割壓力區緊鄰噴嘴出口,工件表面至噴嘴出口的距離約為0.5~1.5mm,切割壓力Pc大而穩定,是目前工業生產中切割手扳常用的工藝參數。第二高切割壓力區約為噴嘴出口的3~3.5mm,切割壓力Pc也較大,同樣可以取得好的效果,並有利於保護透鏡,提高其使用壽命。曲線上的其他高切割壓力區由於距噴嘴出口太遠,與聚焦光束難以匹配而無法採用。
結語
綜上所述,噴氣雷射切割技術正在我國工業生產中得到越來越多的套用,國外正研究開發更高切割速度和更厚鋼板的切割技術與裝置。為了滿足工業生產對質量和生產效率越來越高的要求,必須重視解決各種關鍵技術及執行質量標準,以使這一新技術在我國獲得更廣泛的套用。
相關搜尋
雷射切割機 雷射切割
雷射切割加工 數控雷射切割機
金屬雷射切割機 雷射切割原理
(2)在切割頭上增加一獨立的移動透鏡的下軸,它與控制噴嘴到材料表面距離(standoff)的Z軸是兩個相互獨立的部分。當工具機工作檯移動或光軸移動時,光束從近端到遠端F軸也同時移動,使光束聚焦後光斑直徑在整個加工區域內保持一致。
(3)控制聚焦鏡(一般為金屬反射聚焦系統)的水壓。若聚焦前光束尺寸變小而使焦點光斑直徑變大時,自動控制水壓改變聚焦曲率使焦點光斑直徑變小。
(4)飛行光路切割機上增加x、y方向的補償光路系統。即當切割遠端光程增加時使補償光路縮短;反之當切割近端光程減小時,使補償光路增加,以保持光程長度一致。
2.切割穿孔技術:任何一種熱切割技術,除少數情況可以從板邊緣開始外,一般都必須在板上穿一小孔。早先在雷射衝壓複合機上是用沖頭先衝出一孔,然後再用雷射從小孔處開始進行切割。對於沒有衝壓裝置的雷射切割機有兩種穿孔的基本方法:
(1)爆破穿孔:(Blastdrilling),材料經連續雷射的照射後在中心形成一凹坑,然後由與雷射束同軸的氧流很快將熔融材料去除形成一孔。一般孔的大小與板厚有關,爆破穿孔平均直徑為板厚的一半,因此對較厚的板爆破穿孔孔徑較大,且不圓,不宜在要求較高的零件上使用(如石油篩縫管),只能用於廢料上。此外由於穿孔所用的氧氣壓力與切割時相同,飛濺較大。
(2)脈衝穿孔:(Pulsedrilling)採用高峰值功率的脈衝雷射使少量材料熔化或汽化,常用空氣或氮氣作為輔助氣體,以減少因放熱氧化使孔擴展,氣體壓力較切割時的氧氣壓力小。每個脈衝雷射只產生小的微粒噴射,逐步深入,因此厚板穿孔時間需要幾秒鐘。一旦穿孔完成,立即將輔助氣體換成氧氣進行切割。這樣穿孔直徑較小,其穿孔質量優於爆破穿孔。為此所使用的雷射器不但應具有較高的輸出功率;更重要的時光束的時間和空間特性,因此一般橫流CO2雷射器不能適應雷射切割的要求。此外脈衝穿孔還須要有較可靠的氣路控制系統,以實現氣體種類、氣體壓力的切換及穿孔時間的控制。在採用脈衝穿孔的情況下,為了獲得高質量的切口,從工件靜止時的脈衝穿孔到工件等速連續切割的過渡技術應以重視。從理論上講通常可改變加速段的切割條件:如焦距、噴嘴位置、氣體壓力等,但實際上由於時間太短改變以上條件的可能性不大。在工業生產中主要採用改變雷射平均功率的辦法比較現實,具體方法有以下三種:(1)改變脈衝寬度;(2)改變脈衝頻率;(3)同時改變脈衝寬度和頻率。實際結果表明,第(3)種效果最好。
3.噴嘴設計及氣流控制技術:雷射切割鋼材時,氧氣和聚焦的雷射束是通過噴嘴射到被切材料處,從而形成一個氣流束。對氣流的基本要求是進入切口的氣流量要大,速度要高,以便足夠的氧化使切口材料充分進行放熱反應;同時又有足夠的動量將熔融材料噴射吹出。因此除光束的質量及其控制直接影響切割質量外,噴嘴的設計及氣流的控制(如噴嘴壓力、工件在氣流中的位置等)也是十分重要的因素。目前雷射切割用的噴嘴採用簡單的結構,即一錐形孔帶端部小圓孔。通常用實驗和誤差方法進行設計。由於噴嘴一般用紫銅製造,體積較小,是易損零件,需經常更換,因此不進行流體力學計算與分析。在使用時從噴嘴側面通入一定壓力Pn(表壓為Pg)的氣體,稱噴嘴壓力,從噴嘴出口噴出,經一定距離到達工件表面,其壓力稱切割壓力Pc,最後氣體膨脹到大氣壓力Pa。研究工作表明隨著Pn的增加,氣流流速增加,Pc也不斷增加。可用下列公式計算:V=8.2d2(Pg+1)V-氣體流速L/min(d-噴嘴直徑mm,Pg-噴嘴壓力(表壓)bar).
對於不同的氣體有不同的壓力閾值,當噴嘴壓力超過此值時,氣流為正常斜激波,氣流速從亞音速向超音速過渡。此閾值與Pn、Pa比值及氣體分子的自由度(n)兩因素有關:如氧氣、空氣的n=5,因此其閾值Pn=1bar×(1.2)3.5=1.89bar。當噴嘴壓力更高Pn/Pa=(1+1/n)1+n/2時(Pn;4bar),氣流正常斜激波封變為正激波,切割壓力Pc下降,氣流速度減低,並在工件表面形成渦流,削弱了氣流去除熔融材料的作用,影響了切割速度。因此採用錐孔帶端部小圓孔的噴嘴,其氧氣的噴嘴壓力常在3bar以下。
為進一步提高雷射切割速度,可根據空氣動力學原理,在提高噴嘴壓力的前提下不產生正激波,設計製造一種縮放型噴嘴,即拉伐爾(Laval)噴嘴。德國漢諾瓦大學雷射中心使用500WCO2雷射器,透鏡焦距2.5〃,採用小孔噴嘴和拉伐爾噴嘴分別作了試驗。試驗結果:分別表示NO2、NO4、NO5噴嘴在不同的氧氣壓力下,切口表面粗糙度Rz與切割速度Vc的函式關係。可以看出NO2小孔噴嘴在Pn為400Kpa(或4bar)時切割速度只能達到2.75m/min(碳鋼板厚為2mm)。NO4、NO5二種拉伐爾噴嘴在Pn為500Kpa到600Kpa時切割速度可達到3.5m/min和5.5m/min。應指出的是切割壓力Pc還是工件與噴嘴距離的函式。由於斜激波在氣流的邊界多次反射,使切割壓力呈周期性的變化。
第一高切割壓力區緊鄰噴嘴出口,工件表面至噴嘴出口的距離約為0.5~1.5mm,切割壓力Pc大而穩定,是目前工業生產中切割手扳常用的工藝參數。第二高切割壓力區約為噴嘴出口的3~3.5mm,切割壓力Pc也較大,同樣可以取得好的效果,並有利於保護透鏡,提高其使用壽命。曲線上的其他高切割壓力區由於距噴嘴出口太遠,與聚焦光束難以匹配而無法採用。
結語
綜上所述,噴氣雷射切割技術正在我國工業生產中得到越來越多的套用,國外正研究開發更高切割速度和更厚鋼板的切割技術與裝置。為了滿足工業生產對質量和生產效率越來越高的要求,必須重視解決各種關鍵技術及執行質量標準,以使這一新技術在我國獲得更廣泛的套用。
相關搜尋
雷射切割機 雷射切割
雷射切割加工 數控雷射切割機
金屬雷射切割機 雷射切割原理