燒結鋼是粉末冶金工業中產量最大、套用面最廣的一類重要鐵基零件材料,每年需求量已超數10萬噸。燒結是在高溫加熱情況下,通過擴散使一個粉末聚集體產生顆粒聚結的過程。燒結鋼零件的製造是粉末冶金學做出的一個貢獻。
基本介紹
介紹,組織特點,合金元素作用,熱處理工藝,淬火-回火,感應淬火,滲碳碳氮共滲,氮碳共滲,燒結硬化,材料選擇,工藝因素,硬度特點,零件密度分布,
介紹
生產燒結鋼產品最常使用的方法就是金屬注射成型,即將非常細小的鋼粉末與一定比例的塑膠粘結劑混合,然後注入模具中,成為具有任何形狀的半製成品,例如齒輪、軸承或表殼。這一過程與塑膠的注射成型相似,但是注射溫度稍高,不過仍低於200°C。然後將半製成品放入溫度超過1000°C的高溫爐中,這樣可將塑膠粘接劑燒掉而鋼則留下。
燒結鋼的性能與一般鋼鐵材料類似,主要取決於材料的密度、化合碳含量、合金元素的種類與數量、組織狀態。燒結鋼與鋼鐵材料的最大區別在於前者組織中存在著孔隙,其密度在一定範圍內可任意調節,因此材料密度是影響燒結鋼性能的重要參數之一。在選擇燒結鋼牌號時,首先要確定材料密度,用粉末冶金法可以根據使用要求製造從低密度到完全緻密的具有各種性能的燒結鋼。燒結鋼熱處理的特點
組織特點
(1)孔隙度對材料性能的影響
粉末冶金零件在壓制、燒結至最終形狀時,其內部含有大約10%的殘餘孔隙。溫壓的零件的殘餘孔隙可低至5%。一般鑄鍛鋼的硬化取決化學成分與晶粒尺寸,而粉末冶金的硬化更大程度上受其連通孔隙的影響。
由於粉末冶金工藝能夠提供最終形狀的產品,其硬化過程就更為關鍵。粉末冶金產品的尺寸變化一般是發生在淬火和回火過程中。對於形狀簡單的製品,其收縮是可以預測的,能通過壓制模具的設計予以調節。
對於形狀複雜的粉末冶金零件,像典型的多台階面零件,不同台階面中的孔隙的變化,會引起明顯的熱處理變形,影響工件在裝配中的功能和配合。發生這種現象時,需要進行精加工,但這將減少粉末冶金在成本上的優勢。
孔隙也影響材料的硬化。連通孔隙起到了絕熱的作用,減少了材料的導熱能力,當零件從奧氏體相區迅速淬火時,孔隙延緩了冷卻速率,造成了混合型顯微組織,以及不均勻的硬度。零件形狀越複雜,這種現象越明顯。
由於上述原因,鐵基粉末冶金材料的硬度障孔隙度增加而降低。圖5.1-1為燒結碳鋼和類似成分鑄鍛鋼的距表面不同距離的硬度對比。該圖表明:不僅因孔隙對材料熱傳導性造成的影響而致使硬度下降,而且孔隙本身也減少材料的硬度測量值。在某些情況下,由於孔隙的影響,有可能出現材料表觀硬度低,但實際上顯微硬度並不低,因此應選用低載荷的硬度測量方法。此外,淬火介質水或液態鹽能浸入孔隙造成腐蝕,使用真空淬火,可避免這類問題。
圖5.1-1
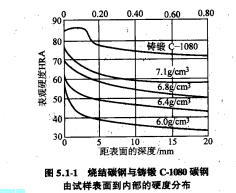
(2)孔隙對硬化層深度的影響
具有連通孔隙的燒結鋼零件的表面硬化工藝,如滲碳、碳氮共滲和氮碳共滲,由於氣氛氣體的快速滲入,對工藝的控制十分敏感。這些高碳勢氣氛由零件外表面通過孔隙表面擴散進入內部,造成在外表面下迅速滲碳至有效深度,以及表層/心部過渡區的消失。燒結低碳鋼滲層深度與密度的關係曲線見圖5.1-2。燒結鋼滲碳層的深度隨密度增大而下降。低密度燒結鋼滲碳時,滲碳氣體通過連通孔隙以分子擴散方式向零件心部滲透,而通過碳原子擴散的作用不大;高密度燒結鋼的連通孔隙很少,當密度達到7.2 g/cm3後,連通孔隙幾乎都已封閉,阻止滲碳氣體的直接滲入,滲碳方式主要是通過碳原子擴散的形式進行。當對密度小於6.8 g/cm3的燒結鋼進行滲碳時,由於滲碳性氣氛通過零件內部的連通孔隙而使整個零件變脆,故一般要求滲碳的燒結鋼零件密度不低於7.0 g/cm3。圖5.1-2表明適於表面硬化工藝的密度應控制在大於或等於7.2 g/cm3範圍。為提高零件表面密度,可用表面滾壓、精整、整形、噴砂、切削加工等方式,或採用氧化處理和硫化處理來封閉孔隙,從而得到薄而明顯的滲碳層。
燒結低碳鋼表面硬化的主要目的是提高硬度、耐磨性,維持心部的韌性和彈性。這樣,便可給予齒輪和其他高強度零件的綜合力學性能。但當碳勢失控時,這類零件可能非常脆,還會出現淬火後的變形。
(3)燒結鋼組織不均勻性的影響
燒結鋼是以幾種純元素粉末或予合金粉末為原料進行混合後而製成時,由於未經熔煉,而燒結過程以固相燒結為主,粉末顆粒之間進行擴散均勻化,使得燒結鋼在微觀結構上存著化學成分和顯微組織不均勻的特點。這種特點以及孔隙的存在,使燒結鋼與鑄鍛鋼相比,其過冷奧氏體穩定性較低,淬硬性較差。在熱處理過程中,燒結鋼的組織變化規律,基本遵循鐵.碳相圖,以及三元或多元相圖。但顯微組織不均勻造成材料組織不是完全按相圖中對應成分點的直線改變,而是按成分點附近區域的成分改變,呈多種組織共存的非平衡狀態。
合金元素作用
燒結鋼的化學成分、組織與性能在燒結鋼中添加合金元素,能改善材料的金相組織及孔隙形態。燒結鋼的組織變化規律,基本遵循鐵-碳相圖,以及鐵的其他三元或多元相圖。但與熔煉材料相比,由於孔隙的存在,以及未經熔煉過程,合金化充分程度有差異。隨著溫度的變化,材料組織不是完全按相圖中成分點對應的直線改變,而是按成分點附近的區域成分改變,呈多種組織共存的非平衡狀態。
合金元素在燒結鋼中的作用大致可歸納為:
1)活化燒結,即在燒結時,合金元素與基體形成低熔點共晶,或加速擴散過程:
2)球化孔隙,即在燒結時提高擴散係數,通過鐵原子擴散,使孔隙由多邊形趨於球形;
碳、銅、鎳和鉬對燒結鋼的組織、性能影響規律與對緻密鋼的影響相同。此外,銅還有活化燒結和調節燒結收縮的作用。
硫、磷在緻密的鋼材中是有害元素,但在燒結鋼中,加入適量的硫或磷,卻會產生有益的作用。燒結鋼結構零件,除熱鍛件外,一般不進行熱壓加工,故無熱脆性問題。硫的質量分數為0.4%以下時,加硫可提高材料的斷後伸長率;硫的質量分數為0.2%以下時,加硫可提高材料的抗彎強度;此外,加硫可改善材料的被切削性能,提高減摩性能。
磷溶於鐵素體中,固溶強化的同時使鐵素體的塑性降低,故在緻密鋼材中要儘量減少磷含量。對於燒結鋼來說,孔隙是影響材料韌性和塑性的主要因素。磷的存在,可於1050°C與鐵、953°C與鐵和碳分別形成共晶,產生液相,活化燒結,提高材料密度(即減少孔隙),並使殘留孔隙呈球狀,從而提高材料的韌性和強度。燒結鋼中磷的加入量ωp不得高於0.8%(一般控制在0.6%),否則Fe3P沿晶界析出,會降低材料的韌性。
鉻、錳、釩合金元素對燒結鋼性能的影響與對緻密鋼相同。這三種元素均與氧有很強的親合力,因而對燒結時的保護氣氛要求很高,通常用預合金粉的方式加入,也可以鉻或釩的碳化物形式加入,經熱處理後,獲得高強度燒結合金鋼。
熱處理工藝
燒結鋼的熱處理、化學熱處理、蒸氣處理和電鍍 燒結鋼製品,進行整體熱處理(在奧氏體化溫度淬火,於200~280°C回火)。燒結鋼的熱處理與熔煉的緻密鋼的基本相同,但由於孔隙的存在和合金化的特殊性,鐵基結構材料的熱處理有以下特點:
1)密度對熱處理後的材料性能影響很大,密度越高,熱處理效果越好,性能越穩定。
2)由於孔隙的影響。材料表觀硬度偏低。但其組織的顯微硬度並不低。為了反映材質本身的硬度,應選用載荷1.96N以下的維氏硬度(HV)。
3)孔隙降低材料的導熱性,造成過熱敏感性差,以及淬透性差。為此,淬火溫度應比緻密鋼高500°C左右,加熱時間相應延長。
4)熱處理過程應防止有害物質由表面孔隙進入材料內部,低密度件不宜用鹽浴加熱;不宜在水中淬火,而應選機油作為介質;加熱時需用保護氣氛等。
5)對於密度低於7.0g/cm3的製品,在化學熱處理時,滲透速度快,滲層過厚。為防止此現象,可用封孔措施,如液相燒結或滲硫。燒結鋼常用的化學熱處理有滲碳、碳氮共滲、滲氮、氮碳共滲以及滲合金元素等。
淬火-回火
燒結鋼零件的整體熱處理主要是淬火一回火。這種熱處理工藝主要為了提高零件的耐磨性和改善心部強度。燒結鋼零件一般含碳0.5%~0.8%,密度通常超過6.8g/cm3。大多數燒結鋼零件常用周期密封淬火爐(而不是連續網帶爐)進行熱處理。因為產品具有最終形狀,所以在加熱過程中不能相互接觸或碰撞,否則會引起變形和軟點。廣泛用於熱處理的氣氛,用甲烷和空氣燃燒而成並控制碳勢的吸熱性氣氛。由於氣氛快速滲透到零件內部連通孔隙,在工藝溫度相當低及處理周期相當短時,碳的擴散也非常快。
對中等到高密度(6.8~7.2 g/cm3)零件,更宜選擇周期密封淬火爐,以便於控制爐溫曲線。使用這種設備,零件能擺放在專門工裝中,使加熱淬火時零件變形最小,而且碳勢的控制也很精確。很多新型爐設計都有內部自動升降操作設備以改變淬火的熱負荷。
當零件需要較深的淬硬層深度時,可使用攪拌油冷。攪拌油冷的冷卻速率較快。負載大小也是獲得零件硬度均勻的限制性因素。大多數密封淬火爐的設計能力是每4 L淬火油處理0.5kg鋼件,對於燒結鋼,使用11.5~15 L淬火油來冷卻0.5 kg零件。為獲得均勻的熱處理性能,應儘量避免過載。
回火用於減少零件內因快速淬火和馬氏體相變產生的熱應力與組織應力,這種應力如不去除,會增加燒結鋼零件的脆性和缺口敏感性,使之較易斷裂。這種應力隨零件密度增大而增加。所有密度大於6.7 g/cm3的零件淬火後,都應回火。建議燒結鋼的回火溫度範圍為150~200℃。在200℃以上回火,會改善淬火零件的韌性和斷裂性能,提高抗拉強度和衝擊強度。但在這一溫度範圍內回火爐應該對淬火油揮發所引起的大量的煙霧有專門措施,以減少對大氣的污染。回火也用於減少燒結合金鋼快速淬火時產生的奧氏體。這種奧氏體的影響表現於材料的尺寸變化和硬度變化。通過低溫冷凍處理(低於-100℃)數小時,可使殘餘奧氏體轉變成馬氏體。通常要在200℃進行二次回火,以消除新形成的馬氏體內應力。圖5.1-8表示了在淬火後回火溫度對FLA205燒結合金抗衝擊性的影響。
圖5-18
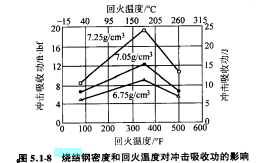
感應淬火
直齒圓柱齒輪、錐齒輪、帶花鍵槽輪轂以及凸輪都是套用粉末冶金技術製造的典型零件。這些零件的某些部位需要具有堅硬、耐磨的表面,同時保留燒結基體的延展性。感應淬火一般可滿足這類需求的。可採用自動生產線,以減少操作程式。由於孔隙的存在,影響了粉末冶金材料的感應加熱,所以與同樣成分的鑄鍛材料相比,燒結鋼一般需要較高的功率或較長的加熱時間,才能達到給定的淬火深度。與鑄鍛鋼相似,感應淬火主要受化合碳含量、合金元素含量和表面脫碳的影響。粉末冶金零件則主要受表面脫碳的影響。傳統的帶式燒結爐,可能使零件在離開保溫帶,從1100℃緩慢冷卻到800℃的過程中發生脫碳。新近的燒結爐設計有能夠通過控制進入這一轉變區冷卻的裝置,補償脫碳問題。
多數情況下燒結鋼零件的感應淬火是用水基冷卻劑,其中含有一些種類的防鏽劑,以防止零件內部腐蝕。零件密度大於90%才能進行感應加熱。隨著密度減低,材料的電阻率增加,磁導率減小。基於這一原因,粉末冶金件的表面硬化常使用帶高速噴液淬火的整體淬火線圈。
滲碳碳氮共滲
燒結鋼的滲碳和碳氮共滲這兩種表面處理工藝最常用於那些承受頻繁循環負載和表面黏著磨損的零件。這些零件需要表面硬度高與心部具有韌性、延展性相結合。大多數高負載的齒輪都需要進行這些處理。
滲碳和碳氮共滲處理可用於高密度預合金化或部分合金化燒結鋼零件,這些零件的碳含量低於0.5%。孔隙度高於10%的零件不宜於進行這些處理,這是由於大量連通孔隙會使碳迅速滲透零件,增加了零件的脆性。
在鍛造鋼中,表面處理後零件表面硬度均勻,有效滲層深度通常是用測量50HRC(513HV)的深度來確定的。顯微硬度能精確地表明鍛造鋼橫截面剖面上的硬度分布,但對於燒結鋼則可能產生誤差。燒結鋼中表面下的孔隙能影響硬度讀數。對表面下的每個滲層深度,至少取3個讀數,取平均值確定實際滲層深度。圖5.1-9表明,對於3種不同密度的Fe-Cu合金,真空滲碳過程中,孔隙對實際滲層深度的影響。
圖5-19
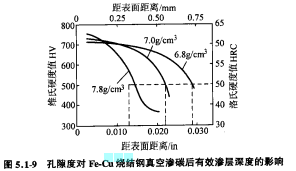
碳氮共滲一般是採用具有一定碳勢的氣氛,並在其中加入氨氣以分解出活性氮原子。氮與碳同時擴散到燒結鋼中,可延緩淬火的臨界冷卻速率,提高淬硬性。這有利於產生較為一致的表面硬度曲線,改善粉末冶金材料的耐磨性。碳氮共滲的工藝溫度通常低於滲碳溫度。與滲碳相比,碳氮共滲改善了零件的尺寸控制,減小了零件變形。加入氨時要小心,因為過量的氮擴散進內部孔隙,會引起脆化和強度減低。
碳氮共滲是淺滲層處理。滲層深度一般不大於0.5mm。基於這一原因,處理時間相當短,通常僅需30-45 min,主要決定於工藝溫度、所需滲層深度以及密度。滲碳是工藝的第一步,隨之加入氨。處理溫度取決於燒結鋼的成分和密度,通常為870℃。
在上述處理中,控制碳勢是關鍵。為維持零件中碳的分布,一般規定碳勢為1.0%-1.2%。為減少可能產生的混合相和殘餘奧氏體,通常的辦法是保持碳勢0.85%-0.95%。然而在燒結鋼零件中,由於氣體通過孔隙的快速滲入,在零件表面很難保持均勻的碳含量。
氮碳共滲
氮碳共滲作為粉末冶金零件的硬化處理工藝,正在越來越多地替代其他處理方式而得到廣泛套用。氣態氮碳共滲是一種表面處理工藝,在一定條件下,氮、碳可以擴散進入低碳燒結鋼的表面,這點與碳氮共滲有些類似,但在較低的處理溫度(570~630℃)以及氣氛成分方面,該工藝與前述工藝不同。碳氮共滲(780~870%)是用吸熱性氣氛為基體,添加NH3作為氮源,而氮碳共滲是用NH3作為基體氣氛,加入各種碳氫化合物作為碳源。這種工藝可以使用各種類型的設備,如周期式箱式淬火爐、井式爐以及真空離子滲氮爐等。在氮碳共滲溫度範圍內,不發生奧氏體轉變,因此關鍵是減少零件在油淬時可能發生的變形。氮和碳以一定的濃度擴散進零件表面,並在其表面形成氮化鐵薄層,在金相觀察時顯示出白亮層。該白亮層提供的高硬度和潤滑性改善了零件耐磨性。這種工藝的套用,能使鋼表層的摩擦係數與未處理前相比降低一半。氮化層改善了零件表面耐黏著磨損性能。隨後的氧化過程也能夠提供耐蝕性和耐磨性。
由於氣態氮碳共滲依靠擴散過程,所以套用於粉末冶金零件時,密度影響很大。如果氮從孔隙表面滲入並形成氮化物,會發生體積膨脹和脆化。基於這一原因,粉末冶金零件的密度應為理論密度的92%。只有採用溫壓或復壓工藝,才能達到這一密度水平,也可使用價格較低的蒸汽處理作共滲前的封孔處彈,來解決這一問題。
離子氮碳共滲能夠使零件保持良好的精度。在處理過程中零件被置於真空室中由離子轟擊直接或間接加熱。這種工藝常常用於象同步齒轂、凸輪翼等零件的生產中。套用輝光離子,將離子轟擊到零件表面,並且使表面的氮、碳離子濃度和氮的擴散更為均勻。其內部孔隙表面的氮化很少,因此發生在氣體氮碳共滲中的體積膨脹和脆化,在離子氮碳共滲中不明顯。
氮碳共滲工藝可用於燒結密度超過6.9 g/cm3的鐵及預合金粉製取的零件。低於這一密度,零件中孔隙的變化會導致不均勻的尺寸變化,燒結鐵橫向斷裂試樣在各種氮碳共滲工藝處理後的尺寸變化見圖5.1-10。
對鐵素體進行氣體氮碳共滲工藝最適於用在要經受滑動摩擦磨損的零件上。因為堅硬的氮化物層相當薄,這種工藝不套用在高壓應力或抗衝擊負載的零件上。
經氮碳共滲的零件表面會形成ε相,該相具有相當於銼刀的硬度(大於60HRC),硬度值的高低還取決於鋼中的合金元素含量。由於氮碳共滲處理溫度較低不會發生相變,因此零件可以空冷而不降低硬度。氮碳共滲還改善了燒結鋼零件的強度對缺口的敏感性,而且不會因孔隙吸收油造成污染。圖5.1-11是兩種低碳燒結鋼在氮碳共滲後的疲勞強度。
燒結硬化
使燒結鋼由燒結溫度冷卻而發生馬氏體相變的工藝稱為燒結硬化。這樣:零件在燒結後便可獲得所需的高強度和高硬度礦,這種工藝對於大批量生產的零件成本是最低的,因為燒結後不需要熱處理。
這種工藝需要用預合金化粉末。為獲得燒結零件的組織和性能,最重要的影響因素是冷卻過程中合金轉變為馬氏體或貝氏體的能力。
各種商用鋼材中常加入0.25%-1.0%Mn,以增加普通碳鋼的強度和硬度。Cr也是常見的強化元素,但幾乎不用於預合金化粉末中,因為很難除掉顆粒表面形成的氧化鉻,而氧化又會阻礙顆粒同的擴散。Mo和Ni常用於低合金燒結鋼,因為其氧化物易還原。這些元素在提高強度和韌性上證明是非常有效的。燒結硬化需要控制燒結後從奧氐體相區(1120-1290℃)的冷卻速率。決定合金燒結硬化能力的因素是,600℃和150℃之間的冷卻速率,這包含各種燒結鋼馬氏體相變的起始點(帆點)溫度、合金元素含量、混合料成分。最常用的合金粉是4600型粉末加入銅和碳。
燒結硬化鋼的顯微組織是表層韻馬氏體大於90%,而心部組織的馬氏體小於70%。這種組織結合了零件表面的硬度和心部的韌性,而沒有油淬後的高應力集中。
因此,了解冷卻速率和合金成分是非常重要的,這可以提供具有給定質量、密度的零件所需要的淬硬性。在標準網帶燒結爐中,對於給定的零件密度,為獲得淬硬性,需要採用4600合金中加入0.2%Cu和0.9%C的成分。對於有效提高冷卻能力的新型燒結爐,可以使具有較低的合金含量的燒結鋼獲得同樣水平的淬硬性。有一種簡單的試驗方法,能夠用於測定卻速率、密度、合金含量對燒結材料的硬度和組織的影響,把熱電偶埋在不同質量和密度的圓柱型試樣的表面和心部,另一個熱電偶被固定在網帶上,用於在已知溫度和帶速下測量爐內的環境冷卻速率。剖開這些試樣,確定在熱電偶定位處的組織和硬度,以構成圖5.1-12的曲線。該圖為4600型合金的結果。對於各種混合成分的不同密度的合金,根據給定的使用條件,能構造出相應的組織一硬度一冷卻速率圖,以便選擇最低成本的材料。除了成本最低以外,燒結硬化還有以下幾個優點:
1)能夠很好地控制顯微組織,提供較好的性能;
2)孔隙不含油.對環境無污染
3)與油淬相比,複雜形狀霉件的變形小。
4)改善尺寸穩定性,並能保證大批量生產的產量和質量的穩定。
燒結硬化的主要缺點是零件的成分需要高碳含量,才能獲得必要的淬硬牲。高碳含量降低了燒結鋼的力學性能。
材料選擇
工藝因素
當有多種不同成分和密度的材料都能滿足使用要求時,應儘量選擇密度低的材料。因為提高密度勢必增大壓制壓力,加快模具消耗和增加工序。一般密度小於6.59/cm3時,一次壓制即可達到。密度為6.5~6.99/cm3時,需選用壓縮性好的鐵粉。密度為6.9~7.49/cm3時,需增加復壓復燒、熱復壓、浸銅等工序或採用溫壓工藝。密度大於7.49/cm3時,需採用熱鍛工藝或注射成形工藝。需要採用熱處理工藝提高零件的強度和硬度時,應選擇6.69/cm3以上的材料密度以避免過多的孔隙降低導熱性影響材料的淬透性。
硬度特點
測定鐵基結構材料表觀硬度時,壓頭作用在材料的金屬基體與孔隙的複合體上,表觀硬度值低於相同成分及組織的緻密材料。但金屬基體的顯微硬度可能不低於緻密材料(同成分時),也可能高於緻密材料(不同成分時)。大多數有硬度要求的結構材料在使用中,局部壓應力並不很大,主要要求耐磨,故表觀硬度低的粉末冶金材料,其耐磨性往往優於表觀硬度高的緻密材料。應注意,選材時對材料硬度的要求,要區別於通常對緻密材料的要求,即相同使用效果時,允許粉末冶金材料有較低的表觀硬度。另外,選用較小負荷的HV硬度,較之HRC硬度更能反映材料的表層狀況。再者,密度分布的不均勻性及合金化效果各部位不平衡的特點,使粉末冶金材料表觀硬度的波動範圍增大,在制定硬度要求時,要允許有一個比緻密材料更寬的硬度波動範圍。
零件密度分布
粉末冶金結構零件在成形時,因模壁摩擦和粉末流動性差的因素,造成製品的密度不均勻性,並使零件不同部位的物理一力學性能有差異。對性能要求嚴格的零件,必須規定零件不同部位分段密度允許的差值,並對零件主要工作部位,如最大應力處、摩擦處、導磁部位等,規定密度允許的最小值。