NUMMI(新聯合汽車製造公司)是1984年豐田與通用兩大汽車巨頭在美國加利福尼亞州共同成立的一家合資公司,也是美國第一家合資汽車公司。該公司已生產了豐田卡羅拉、Matrix、Tacoma車型,以及龐蒂克Vibe等,堪稱是日、美汽車合作的經典性公司。
基本介紹
- 公司名稱:新聯合汽車製造公司
- 總部地點:美國
- 成立時間:1984年
- 公司性質:合資公司
簡介,歷史影響,供應商,成功背景,領導團隊,製造團隊,
簡介
新聯合汽車製造公司(New United Motor Manufacturing, Inc.,簡稱NUMMI)是一家在美國費利蒙市的汽車製造工廠 。以前是通用汽車在1962年所設的工廠,現時為豐田及通用汽車的合資公司。通用汽車藉此了解日本汽車的設計技術,而豐田則以此為進軍北美市場的基地。在不少企業教科書多以此合資公司為例。
工廠占地約88個足球場,現時擁有五千五百名員工。
歷史影響
新聯合汽車製造公司合資經營20年
2004年,位於美國加利福尼亞福瑞蒙特的新聯合汽車製造公司迎來了自己成立20周年的慶典。在一百多年的汽車製造史上,這家製造廠無論從規模還是時間上來說,都只能算小字輩。然而它對於改寫世界汽車工業格局所起到的重要作用,無疑是影響深遠的。
NUMMI(新聯合汽車製造公司)
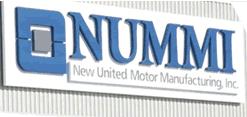
新聯合汽車製造公司的特殊之處就在於它是兩個競爭對手之間的合作,合資雙方是當時汽車界裡的兩個巨頭———通用和豐田。雖然父母大有來頭,但新聯合汽車製造公司卻是個先天不足的苦孩子。通用拿出了自己兩年前就關門歇業的最差的廠房設備,豐田則投入了一億美元,招回因原廠關門而失業的工人,一班老兵破槍就從1984年開始了生產。由於擔心反托拉斯和反不正當競爭,這次特殊的合資還引來了美國聯邦貿易委員會的調查,而美國另外兩個汽車巨頭福特和克萊斯勒甚至不惜抗訴來阻止它。後來美國聯邦貿易委員會終於批准了這次合資,不過限定了產量不超過25萬輛、合資期限最多為12年,一直到1993年才取消這些限制。
通用和豐田共創了一個雙贏的結果
通用和豐田的這次合資可以說各有目的。豐田當時在美國市場上屢屢難以打開進口車的局面,急於把自己的生產方式拿到美國試一試,看看能不能進入這塊世界上最大的汽車市場。而通用受困於激烈的市場競爭和低下的生產效率,急於從日本人的“精益生產方式”中汲取新鮮血液。雙方一拍即合,兩個競爭對手的合作成就了當今世界上最大的兩個汽車巨頭。正如豐田社長張富士夫所言:“沒有與通用在20年前的合作,豐田就沒有今天,而現在我們幹得很棒。”通過在新聯合汽車製造公司積累的生產和銷售經驗,豐田隨後投入了超過163億美元在美國多處建廠,雇用超過了35000個員工,投入150億美元在北美發展零配件,並在服務方面投入42億美元,如今豐田在北美獲取的盈利與在日本一樣多,成了世界上最賺錢的汽車公司。而輪流供職於新聯合汽車製造公司的通用官員們紛紛把豐田的精益生產方式帶回了這家古老的美國企業。要讓一個傳統觀念根深蒂固的老牌企業接受另一種文化主導下的工作方式真不是一件容易事,儘管抱怨、衝突、抵制不斷,好在通用終於為自己更換了一部分新鮮血液。正如新聯合汽車製造公司首任生產和勞工關係總經理甘瑞·康威斯所說,通用和豐田都學到了各自想學的,都成功了,甚至推動著整個市場的競爭。
合資教會了中國進行現代化轎車工業生產
幾乎與新聯合汽車製造公司誕生的同一時期,在大洋彼岸的中國也開始了自己的汽車工業合資道路。中國當時幾乎沒有轎車生產能力,完全靠進口轎車根本無法滿足國內市場需要。為了滿足需求,更是為了發展自己的轎車工業,中國決定尋找合資夥伴。1985年,中德合資的上海大眾汽車有限公司開始生產桑塔納,這次合資同樣在汽車工業史上產生了深遠的影響。在後來的近20年裡,中國的轎車工業從無到有,從弱到強。從早期的上海大眾、廣州標緻、神龍、一汽大眾、長安鈴木等,到後來的天津夏利、廣州本田、上海通用,中國的轎車工業形成了一批以合資公司為主的生產力量,同時也培養出了一個較有實力的零配件產業。不可否認,這種循序漸進的合資規模為中國轎車工業打下了堅實的基礎。
中方合作夥伴必須為合資工廠增加價值
中國不僅僅通過合資的方式讓自己從數量上學會了造車和享受車,更在一年多的時間裡,開始從質量上改變自己的汽車工業格局。自去年以來,新雅閣、馬自達6、伊蘭特等最新國際同步車型,以及寶馬、賓士、凱迪拉克等豪華品牌,紛紛在中國實現或即將實現本土製造,中國的轎車工業正在從技術、品牌、管理、理念等全方位經歷著徹底的洗禮。不久前,在一次關於汽車話題的中央電視台《對話》節目中,當主持人問到經營合資公司最大的感受時,中國最大的汽車工業集團———中國第一汽車集團的總經理竺延風回答:“讓我們逐漸懂得了造汽車。”
通過合資學習技術是中國汽車界的願望,這也是當年中國汽車產業政策“以市場換技術”的初衷。南京大學商學院教授、東方智業管理顧問公司首席顧問成志明認為,由於企業的戰略目標和資源是不斷變化的,因此很少有合資公司能夠長久存在。而作為一種過渡性的安排,汽車業的合資主要是為企業創造一個學習的機會———任何一個現代企業都需要學習,以追趕商業環境的變化。
在談到如何看待合資公司的問題時,竺延風坦言不是為了某一天能打倒對方,而是為了長期共贏。但是合作必然需要符合雙方利益的基礎和目標。竺延風以合資公司的利益分配作為例子,外方認為投入了技術和品牌,中方覺得拿出了市場和廉價勞動力,各自都希望更多地獲得回報。
去年,《亞洲華爾街日報》援引日產公司CEO卡洛斯·戈恩的話說,外國汽車廠商提供的技術在為合資工廠“添加價值”。而與此相對比,當前他們的中國合作夥伴除了提供低成本的勞動力和銷售渠道外,對實際經營和管理的貢獻幾乎為零。他說,中國合作夥伴在與外國汽車製造商成立的合資公司通常持有50%的股份,這是日產汽車這樣的外國公司進入中國蓬勃發展的汽車市場所付出的代價。這一結構在短期內不會改變,但將不會長期維持,中國合作夥伴必須開始為合資工廠增加價值。
合資之路創造了一個學習的機會
時值新聯合汽車製造公司成立20周年之際,我們不妨思索一下這家合資公司走過的道路。以它的規模來看,年產量不超過40萬輛,累計產量500多萬輛,估計再過幾年就可能被中國的幾個合資公司超過。但是它作為在北美地區最先進的整車組裝工廠之一,曾經贏得過多個行業獎項,並且受到通用和豐田雙方領導的重視,其業界地位和作用不是中國目前眾多合資公司能夠比擬的。南京大學成志明認為,這個合資企業之所以保持了長久的生命力,關鍵就在於雙方通過這家合資企業在不斷相互學習———在合資企業內部,雙方都在學習對方的優勢資源,從某種意義上說,形成了雙方學習的競賽。如果一方在學習中失敗,失去對方需要的資源,那么合資就沒有意義了。
中國汽車業的合資公司是在“以市場換技術”的背景下產生,經過多年臥薪嘗膽,不但拿來了產品,引入了資金,還帶動了相關產業,培養了大批人才。可以說過去的20年合資在中國汽車工業史上是很輝煌的。但是,事物的發展都是階段性的,當我們在第一階段成功以後,現在是不是應該考慮進入第二個階段了呢?從目前的經營狀況來看,合資公司對於中國的汽車集團來說,大多屬於賺錢機器,而在學習這方面略顯不足。
東風汽車公司總經理苗圩說:“過去我們在轎車的自主產品研發方面幾乎都是空白的。我們沒有一款東風品牌的轎車產品,我們想通過合資,把日產的經驗積累在轎車研發方面。將來我們的公司在乘用車上可能採取聯合開發。”或許,一種學習型的合資公司才是今後中外雙方都願意繼續共事的長久之地。
供應商
讓我們先來看一個案例,這是NUMMI同事花了整整三個月的時間,幫助一個NUMMI的供應商INJEX公司提高產品質量和生產力改變的案例。它已被哈佛商學院選入案例課本給MBA學生學習。
案例分析CASE STUDY:
Injex工業公司( INJEX INDUSTRIAL)
公司地址:美國加利福尼亞州Hayward
主營業務:汽車門軟膠製造
地 位:只為NUMMI生產,NUMMI是它唯一的客戶
問題所在:在 NUMMI每四年一度的汽車車型改變中,INJEX出現很大的問
題,跟不上NUMMI車型改變的節奏。
解決辦法:及早向NUMMI求救,NUMMI派的四位日本部專家和美國本部的
數位精英免費為該公司提供改善生產流水線、標準作業、存貨管
理、準時生產方式等等,幫助INJEX度過了難關。
由於汽車行業是一個需要大量供應商的行業,我們的直接供貨商有近四百家,間接的供貨商要達到2,300家。供應商團隊其實是整個汽車企業不可分割的一部分。如果一家關鍵的供應商發生了很大的問題,其實對汽車企業的生產和質量控制有很大的影響。
我們是和供應商建立長期的戰略夥伴關係,和供應商一起進步,共負盈虧。同時,我們不斷地培訓供應商,讓他們有能力開發新的產品,並保證現有產品的質量。這樣,在從供應商那兒進貨的時候,我們就獲得了最好的質量的產品,儘量減少庫存,努力達到零庫存。
對於象INJEX這樣能力比較淡薄的企業,為了保證質量,我們會免費協助他們改善。比如說,我們幫助他們建立豐田模式的標準作業,通過攝像機觀察到所有工藝的過程,工人做完份內的工作後不許幫助別人做。這樣,主管人員就很明白對每個員工的工作是否分配合理。經過調整,為該公司節省了1/4的人力資源,平衡了每個員工的工作量。廠房的使用率也大大提高,按豐田模式是以空間來計算,充分利用了每一立方米的空間。最後,成本大大節省。NUMMI採購該產品的價錢也降低了,而質量上升了。體現出了NUMMI和供應商分享利潤的最後宗旨。
在採購價格上,NUMMI按照豐田模式,是採用合理的價格引進最好品質的產品,並不是採購最便宜的產品。這種做法是有各種根據的。和豐田合資的GM就曾經吃過這樣的虧。GM在80年代末的時候,請了一個採購總裁,採用不規範的方式對付供應商。他邀請7個供應商來競標,選最低的三家中再次競標,為公司找到了最低的採購價。到了年底,的確為GM節省了很多採購費用,得到了很大的嘉獎。但這種方式,使很多供應商為了生存,都在虧本邊緣生產,壓得喘不過氣來,根本沒有其他經費和精力去研究和開發新的產品。最後,因為GM的競爭對手在車型的細節上,有符合時尚的新的開發,令GM某一款車的銷售量大大下降,這種捨本逐末的做法,最終導致了採購總裁被迫下台;而GM在這件事情上所受的打擊使它在內部設計上晚了3年。
同時,NUMMI按照豐田模式對採購員的要求是非常高的。採購員必須對NUMMI需要採購什麼樣的產品非常了解,從技術層面到原料層面的。這樣和供應商談判才達到共贏的目的。
NUMMI就是這樣嚴格要求供應商保證提供產品的質量,把住了生產線的第一關,也就是把生產線延伸到供應商處。
以上所有的採購模式,我們都可以在戴明的“第三要點,不要以價格為採購的單一標準。”中找到它的發源點。
NUMMI是成功了,靠著一個強有力的生產製造團隊,他們互相配合,互相支持。當我再來回顧一下NUMMI成功的背景,我想:我們的民族汽車業應該會更有啟發 ……
成功背景
70年代,日本產品在美國的銷量已經占了美國市場的50%。到了80年代後,美國不得不對日本進行貿易遏制,以保護美國的本土產品。美國在沒有辦法的前提下,只有通過和日本公司的合資來改變原來的團隊。於是,類似豐田-通用合資的NUMMI等日美合資企業就這樣一個個誕生了。顯然,NUMMI最後的成功也是由於“通用汽車”全面引進了當初導致豐田成功的以戴明的質量管理為精髓的豐田生產系統。
如果說20世紀80年代,美國汽車界為形勢所迫,不得不引入戴明思想和豐田生產方式的話,那么再上溯三、四十年,豐田的成功,在二戰後日本經濟蕭條的大前提下,是靠著戴明的質量管理的精髓,迅速發展起來的。在豐田公司的東京總部,至今在大廳里還懸掛著三幅畫像。一幅是公司的創始人,第二幅是現任主席,第三幅就是戴明畫像。由此可見戴明對豐田的影響之大,難以言表。是戴明的思想,促使了日本經濟繼明治維新後的又一次騰飛。日本人視美國管理學家戴明為日本工業之父,把其管理哲學奉為圭臬。所以1951年,日本就有了“戴明獎”。而豐田是最先貫徹戴明思想,並受益無窮的日本企業。豐田依靠著從戴明思想衍生而來的豐田生產管理思想(TPS),到現在為止,還是日本最賺錢的企業。
日本汽車靠著戴明思想成功至今,美國汽車靠著戴明思想仍然稱霸著世界,那么中國汽車要發展,就必須借鑑國家行為,吸取外國汽車巨人的成功經驗。
從以上的數據和陳述中,我們可以清楚地看清戴明思想對日本和美國的影響,其實,中國民族汽車工業的現狀和當初日本戴明帶著他的理論去日本時有很相似的地方,如果我們能完全引進戴明的這套管理思想,並從豐田生產管理系統中吸取精華,融合中國民族汽車工業的特點,然後制定出適合中國民族汽車的生產系統,堅定不移地去執行,最後,我相信中國的民族汽車工業也會象日本和美國一樣有質的飛躍!
領導團隊
記得在NUMMI的時候,領導不是坐在辦公室里指手畫腳,而是經常在生產現場。我們不斷地觀察員工的工作。觀察的時候,領導會反覆地思考:為什麼這個工人要這樣工作呢?可不可以有更好的改進方案呢?我們會協助員工更好地改善自己的崗位工作。同時,領導努力去發現員工的才能,把最合適的人放在合適的工作崗位上。我們為員工創造好的條件,讓他們在工作崗位上能夠充分發揮出他們的才能來。一旦員工遇到了問題,我們就和員工一起想辦法去解決問題。
比如在焊接部門,日本豐田來的領導,會和焊接工程師一起商討如何解決焊接存在的不足,更快更好地提高工作效率。他不一定是焊接方面的專家,但和員工一起在現場久了,對現場的了解使該領導能提出一些實際的解決辦法。這樣的領導帶領的團隊能夠在第一時間解決問題,容易追究問題點的責任人,容易改善現有的不經濟現象。
這些領導團隊的風格正是在在戴明的十四條要點的第七條“實施領導”中都有體現。這樣,建立出來的領導團隊是能擔當起伯樂和領航人角色的團隊,把合適的人放在合適的工作崗位上;當下屬出現問題的時候,就協助下屬去解決問題。當每個下屬都做得成功的時候,自然也展現領導的成功。所以,一個成功的團隊,必定有一個成功的領導。
製造團隊
舉一個很簡單的例子:NUMMI剛合資的時候,在裝汽車前玻璃的生產線上,總是有種種問題發生。這些安裝好的玻璃在接受防漏檢查的時候,總是漏水。當問題不斷發生時,GM就說派人想辦法解決。一問現場工人A,A說是跟B學的,而B又是跟C學的……
這種現象,戴明很早就在他的論述中闡述過。他說:“有位女士無法認清自己的工作是什麼?我問她:‘你怎么知道?’她說她是靠同事幫忙的;他們教她哪些是對的,哪些是錯的。然而,這些同事除了知道本身正在採用的工作方式外,還能教她什麼?對錯老師自己都不知道,學生自然也不會知道……就好像大家所熟悉的遊戲一般:大家坐成一圈,一個人向旁邊的人耳語,再依序傳話給下一個人,等到繞了一圈回來,原來的意思已經被傳到完全走樣、認不出來了。”
這些問題在汽車製造業中是很常見的。這實際上是個很小的事情,但卻會影響很大。首先,人教人的方式,如果沒有規範的話,有很多潛在的違反安全設計的操作,是很危險。第二,一個工人的一個小小的誤操作,就把存貨給弄得亂七八糟,某種存貨就莫名其妙地少了。如果存貨有多,還有彌補的可能。但如果按照豐田的零庫存原則,小小的一個動作,就會導致整個生產線的停滯,損失是無法估量的。
要解決這樣的問題,豐田的解決辦法是從戴明思想“第二要點:品質的提升才是關鍵。”中延伸出來的“標準作業”。一旦經過科學的研究,把工人的經驗都綜合起來,制定出每個崗位的高效“標準作業規範”,所有的員工都必須按照標準作業工作,結果做出的產品都是同一質量的。然後,更多的精力可以放在改善上,這樣就會越來越好。
所以,標準作業是建立一個高效製造團隊的關鍵。只要每個員工都有自己的標準作業,在工作中都能戰戰兢兢地把每個步驟做得十全十美,那產品就是十全十美的產品,公司就是十全十美的公司了。所以在豐田的系統中,是鮮有檢驗員的,每個員工就是自己生產的產品檢驗員。
其次,建立一個有效的製造團隊,需要不斷地培訓員工,使他們都成為多面手。按照美國大多數公司的方式,傾向於把工種分得很細,一個工人可能畢生就從事其中某項工作。按照豐田從戴明的“訓練實效”中延伸的理念,不斷地讓員工到不同的工作崗位上去鍛鍊。一個工人可以勝任很多種工作。比如一個噴漆工,如果他幹得出色,我們就讓他帶著成就感和新意去從事組裝或者焊接等其他工作。我們把工人看做能不斷學習和進步的人。這樣,至少有四個層次的優點。第一,提高了他們的工作興趣,工作對他們來說不是一種枯燥的機械工作,而是時不時地有挑戰,有新的變化。第二,當有突發事情有人缺席的時候,隨時有人可以頂替那個崗位。第三,員工在不同部門之間互相熟悉不同的工作,會把原來工作部門好的工作方法帶到新的部門中,又會學習新的部門中的好方法。第四,因為多面手有多崗位工作的經驗,他就能提出很多有價值的合理化建議,節省工序和成本。他又能體會到每一個工作的重要性,感受前一道工序的高品質會給後幾道工序帶來什麼樣的優勢,就會在每個工序上更兢兢業業地工作。
綜上所述,一個高效的製造團隊是必須達到標準作業、不斷培訓和不斷改善的。有了這三點,一個成功的製造團隊也就近在眼前了。